近年来,随着智能汽车相关技术的迅速发展,在过去的五十年间,工业机器人就已经被广泛应用于车身制造车间,来更大的提升生产力。如今,市场经济的蓬勃发展推动了生产需求的提升,工业机器人技术已无法满足日益复杂的市场,因为机器人技术的高效仅仅展现在负责传送汽车底盘的传送系统上。对于许多汽车厂来说,效率低下的传送系统业已成为提升性能的主要障碍。
传统传送技术存在的问题
事实上,在车间的日常运用中,汽车制造业所用的传送技术还影响了产能和灵活性。现有的链条式传送带、辊道甚至滑板传送带都需要以定速、定节距运行。对于汽车装配厂来说,这意味着整个传送系统必须始终保持通电状态并以相同的速度运行才能正常运转。然而,传统的传送载体无法加速、减速,也无法根据工序步骤的完成情况精确定位特定的底盘。虽然某些传统系统支持变“节距”或改变传送器之间的距离,但在大多数情况下,即使距离改变,也难以兼容多种型号。
此外,传统传送带采用复杂的机械设计,配有传送链、传送带、辊轮和齿轮等,有时还需要使用数百种易磨损零部件。这些解决方案体量庞大、结构复杂,不仅难以调整,还需要频繁维护并可能导致计划外停机。但更重要的可能是,传统的摩擦式传送系统依靠的是旋转电机技术。从本质上来说,旋转电机会增加线性应用的惯性,并引入多个机械部件,这会影响速度和加速度的提升。
如何提高装配传送系统的性能?
目前,对于汽车制造商而言,提高车间装配传送系统的性能迫在眉睫。为了更好的适应市场需求,罗克韦尔自动化推出了独立小车技术,能够依托直线电机技术在实际生产中取得新进展,并推动性能效率的显著提升。
这是为什么呢?首先,借助线性电机技术,汽车制造商可对传送模块进行端到端配置,产生可驱动传送器的电磁力,让载体以远超传统系统的速度移动。其次,直线电机没有接触件,也没有易磨损零部件,能够更大限度地减少了维护作业。不过,直线电机只是一方面,真正提高生产力、灵活性和可持续性的则是智能运动控制系统。例如,全球知名汽车自动化系统供应商 Kuka Systems 推出的 PULSE 载体传送系统。该系统专为汽车车身装配流水线而设计,采用的是 MagneMotion 的直线同步电机技术。
此外,利用嵌入式位置传感器和控制软件可对轨道上的每个载体进行单独控制,并对加速度、减速度、移动速度和位置等参数进行编程。车身部分并不以固定的速度移动,而是可以随着一道又一道工艺步骤快速向前穿过机器人工作站。
那么结果如何呢?与传统的摩擦式传送系统相比,这样的“无节距”系统不仅更节能,速度也提升了 30%。而速度提升后,工业机器人和其他加工设备的价值也得到更充分地利用,并大大缩小了系统的整体占用空间(与传统系统相比)。另外,这一系统的可配置程度极高,经过改造后可兼容多个型号,而其模块化设计更是提高了扩展的成本效益。
罗克韦尔自动化独立小车系统在车间运用中还具有如下优势:
产量提高
机械部件和连杆数量有所减少。加速度提高 (>6g),速度亦有所提升 (>5m/s),且运动轨迹全面受控,产量得到提高
灵活性增强
每个移动的载体都支持独立控制,可灵活调整机械节距,让同一台机器得以同时处理多种包装/格式规格并全面控制产品的移动
包装追踪质量稳定
提供完整的追踪轨迹。载体由软件控制,用户无需使用外部传感器和复杂的追踪解决方案,即可确切了解载体位置
灵活性正常运行时间得到延长
淘汰机械连杆和机械部件,仅留极少移动部件,这样可以缩短整体停机时间、减少维护并降低能耗
占用空间明显减小
借助独立小车技术,可以在更小的空间内利用一种机器处理多种产品规格
小罗有话说
罗克韦尔自动化作为作为智能制造的引领者,未来将继续专注于技术创新,利用自动化、数字化和智能化技术,为汽车行业打造更安全、环保、节能、高效的超级车间,提升企业的全球竞争力,推动汽车制造业的数字化和智能制造转变。
审核编辑 :李倩
-
电机技术
+关注
关注
1文章
50浏览量
11168 -
运动控制
+关注
关注
4文章
593浏览量
33010 -
传送带
+关注
关注
0文章
22浏览量
8822
原文标题:独立小车技术 | 车间的“智胜法宝”,下一代运动控制
文章出处:【微信号:罗克韦尔自动化,微信公众号:罗克韦尔自动化】欢迎添加关注!文章转载请注明出处。
发布评论请先 登录
相关推荐
突破传统桎梏,富唯可重构柔性装配系统引领行业新变革
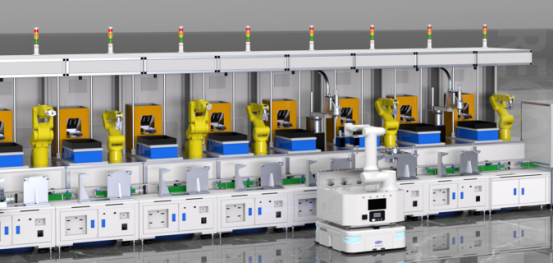
如何优化总线系统的性能
明达MR30 IO模块助力汽车座椅装配线升级

如何优化MEMS设计以提高性能
如何优化DCS系统的性能
如何提高GPU性能
如何提高云计算的性能和效率
提高系统的阻尼比对系统有何影响
能否建议通过内存映射提高aur性能?
美国硅谷站群服务器如何提高网站性能
装配行业如何通过MES系统实现生产管理数字化
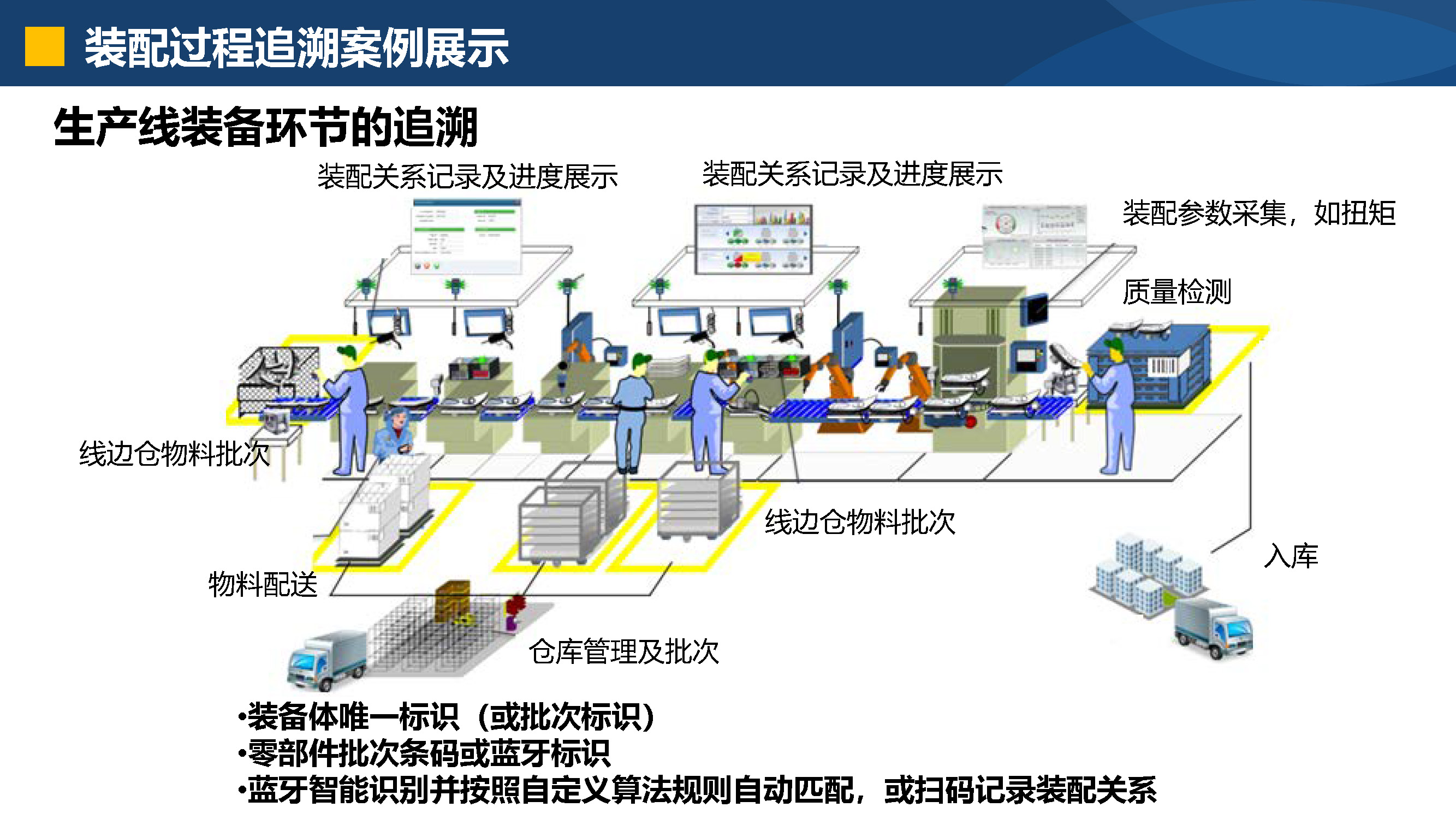
挖掘机生产装配线无线通讯应用
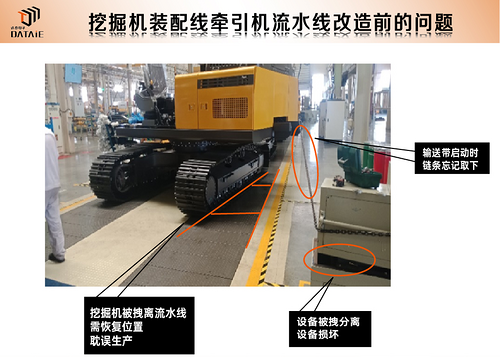
评论