一、引言
在我们平常的工作中,你有没有过这样的感触:
1,XX问题已经出现了好几天了,问题是什么原因引起的?
2,这个不良现象到底是什么,为什么现在查到的和当时得知的不一样呢?
3,都已经让XX部门全检了,怎么又发现不良了呢?
4,XX不良记得已经解决了呀,怎么还在发生呢?
5,原来XX 以前处理过这个问题,我们去看看他们怎么处理的。
6,XX问题这次解决了,后续还会发生吗?
相信大家都遇到过以上几种情况。同一问题持续发生,问题的原因是啥;该如何才能彻底找到根因,药到病除呢?那么,8D报告就是一个行之有效的良药,可以对问题进行拆解分析,找到根因,实施导入解决方案。
二、8D目标和应用流程简介
8D(8 Disciplines)即解决问题的8条基本准则或称8个工作步骤。最早是福特公司使用的经典质量问题分析手法,对于解决工厂中存在的问题是一个很有用的工具;尤其在面对重大不良时,它能建立一个体系,让整个团队共享信息,并引导团队提供解决问题的方法。
8D的目标
1、提高解决问题的效率,积累解决问题的经验;
2、提供找出现存的与质量相关的框架;
3、杜绝或尽量减少重复问题出现;
4、8D格式的原则上针对出现的问题,找出问题产生的根本原因,提出短期,中期和长期对策并采取相应行动措施;
5、8D法可跨部门建立小组来加强部门间的协调,推进问题有效解决,从而改进整个过程的质量,防止相同或类似问题的再发生,以保证产品质量。
8D方法应用流程:
三、8D报告的8个步骤
D1组建问题解决团队
8D原名就是叫团队导向问题解决步骤,8D小组需要由具备产品及制程知识,能支配时间且拥有职权及技能的人士组成,必须指定一名8D团队组长。不具备以上条件的8D是失败的8D,它没法在你需要资源解决问题时提供帮助。若一个体系出现了质量异常,绝非单一部门职能失效,否则整个体系需要重新进行完善。
关键要点:成员资格,具备工艺、产品的知识;成员目标 ,分工 ,程序,小组建设 。
8D负责人:作为8D项目支持者的身份参与8D项目。没有负责人的签字8D报告不能进行关闭。
8D组长:负责8D全过程的进行直至问题解决、8D项目关闭8D组员:在组长的协调下利用自身知识与技能参与8D问题的解决
确定团队成员应注意的问题:团队人数:4~10人组长的选择:部门经理指定本部门人员或亲自担任组员的选择原则:与问题相关且具备相关的资源、能力
工具:行动计划、时间管理、建立团队
8D团队的角色构成:
D1的常见性错误:选择的8D团队成员对涉及问题没有相关知识或认识;只有一两个人实施8D过程。
D2描述问题
目的:用量化的术语详细说明与该问题有关的内/外部顾客抱怨,如什么、地点、时间、程度、频率等。
如何进行问题描述:要找到问题的根源而不是表现症状的简单描述;要定义问题的边界(不要将问题范围扩大到不可控的范围之外)
关键要点:收集和组织所有有关数据以说明问题;问题说明是所描述问题的特别有用的数据的总结;审核现有数据,识别问题、确定范围;细分问题,将复杂问题细分为单个问题;问题定义,找到和顾客所确认问题一致的说明,“什么东西出了什么问题”,而原因有未知风险等级。以客户的角度和观点详细描述其所感受到的问题现象,将所遭遇的问题,以量化的方式,明确出所涉及的人、事、时、地、为何、如何、多少。
工具:质量风险评定,FMEA分析,5W2H(What/Why/When/Where/Who/How/How many)、折线图、直方图、排列图
D2的常见性错误:针对表象而不是针对真正的问题进行描述;对问题的根本原因做过早的假设。
D3 实施并验证临时措施
目的:保证在永久纠正措施实施前,要有临时措施将问题与内外部产品/顾客隔离。(原为唯一可选步骤,但发展至今都需要使用)
关键要点:评价紧急响应措施;找出和选择最佳“临时抑制措施”;决策;实施,并做好记录;验证(DOE、PPM分析、控制图等)
工具:方法:FMEA、DOE、PPM、SPC、检查表、记录表PDCA
开发ICA:保护问题可能的相关角色免受问题的影响~隔离问题-争取时间让8D团队找到问题的根本原因~在根本性解决措施出台之前防范问题的重复发生-ICA将执行到根本性解决措施(PCA) 采用为止
D4确定问题根本原因
目的:用统计工具列出可以用来解释问题起因的所有潜在原因,将问题说明中提到的造成偏差的一系列事件或环境或原因相互隔离测试并确定产生问题的根本原因。
关键要点:评估可能原因列表中的每一个原因;原因可否使问题排除;验证;控制计划
工具:FMEA、PPM、鱼骨图、头脑风暴&关联图、5why法、稳健设计
确定根本原因的主要工具:
5Why 反复提问(Five Why Method):
故障树(Fault Tree Analysis):
鱼骨图(Cause Effect Diagram):
D5 定义并验证根本性解决措施
目的:在生产前验证解决方案,并对方案进行评审以确定所选的校正措施能够解决客户问题,同时对其它过程不会有不良影响。
关键要点:重新审视小组成员资格;决策,选择最佳措施;重新评估临时措施,如必要重新选择;验证;管理层承诺执行永久纠正措施;控制计划 。当根本原因找出后,长期对策往往应运而生,但是如何针对性地制定最佳改善对策,以避免问题再发,仍需要整个团队讨论决议。值得注意的是,一个原因可能有几条措施,同步实施时需要保障解决最根本问题的措施务必被贯彻落实。
工具:FMEA、设计验证和报告(DVP&R)、因果图、稳健设计、检查表、记录表
D6确认与实施根本性解决措施
目的:制定一个实施永久措施的计划,确定过程控制方法并纳入文件,以确保根本原因的消除。在生产中应用该措施时应监督其长期效果。
关键要点:重新审视小组成员;执行永久纠正措施,废除临时措施;利用故障的可测量性确认故障已经排除;控制计划、工艺文件修改 。长期对策可以改善或监控不良现象,是亡羊补牢的纠正措施;而预防再发着重于消除潜在的不合格或者发生趋势变化的原因,属未雨绸缪的改善方法。
预防再发时,我们一般需要考虑几个方面:
平行展开(举一反三)针对相同的工艺、方法、材料或设备方面进行同等风险评估(FMEA)
流程完善从流程面管控,多道审核或趋势预警,在问题爆发前发现。
防呆措施自技术层面可彻底解除不良的防呆措施。
确定PCA计划- 怎样实施- 何时实施- 谁来实施- 何地实施- 如何管理
按计划执行PCA对计划执行进行监控以确认执行的有效性
证实PCA问题是否完全被消除?怎样证明?(设定证明的标志或标准)
不建议采用类似如下效果确认:
培训完成
纠正措施已完成
可疑问题产品全部检查完
工具::FMEA、防错、SPC、PPAP
D7预防类似问题的重复发生
目的:修改现有的管理系统、操作系统、工作惯例、设计与规程以防止这一问题与所有类似问题重复发生。
关键要点:选择预防措施;验证有效性;决策;组织、人员、设备、环境、材料、文件重新确定。改善措施定义完成后,应长期监控从员工反馈、数据分析、现场确认等方面查核措施执行力及有效性。最常用也最有效的方法即为改善前后不良率对比。一旦确认措施有效,必须进行文件标准化。标准化是把企业所积累的技术、经验,通过文件的方式进行规范。标准化的结案应为形成文件编号并上传系统,且对应岗位员工完成相关培训。
工具:FMEA、控制计划CP、过程流程图Flow-chart。什么是预防再发生?预防再发生是指防止当前问题、相似问题再次发生问题解决标准化
D88D过程总结
问题解决完成,对小组成员的努力予以肯定。
8D项目正式关闭
文件定案和存档
记录过程中学到的教训
提交8D问题分析报告
表达对成员的感谢
四、最后
本文对常用8D报告的应用,进行了基本的介绍,仅供大家学习交流,如有错误,敬请指正。
审核编辑:刘清
-
FMEA
+关注
关注
1文章
96浏览量
13607 -
PPM
+关注
关注
0文章
46浏览量
17003 -
DOE
+关注
关注
0文章
38浏览量
12976 -
PDCA
+关注
关注
0文章
15浏览量
3085
原文标题:8D报告该如何使用
文章出处:【微信号:海马硬件,微信公众号:海马硬件】欢迎添加关注!文章转载请注明出处。
发布评论请先 登录
相关推荐
汽车发电机降本引发的车灯模组故障剖析与应对策略
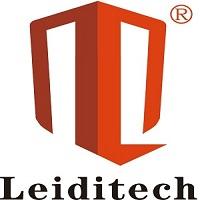
ADS131E08输入接地读数该为0,但是读出来的数一点不对,为什么?
光缆8d与8b区别
基于瑞萨电子RA系列的野火耀阳RA8D1开发板产品简介
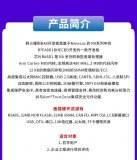
美行科技通过ISO26262:2018汽车功能安全ASIL D流程认证
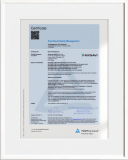
M8_8pin公头如何简化工作流程
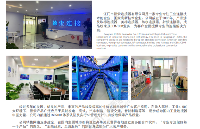
探索8D锁存器:工作原理、特性和应用领域详解
Nullmax提出多相机3D目标检测新方法QAF2D
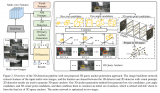
如何搞定自动驾驶3D目标检测!
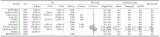
评论