专精特新企业开始大量涌现,从企业微观视角看,这是市场主体成功经营的结果,但是从中观行业和宏观经济视角看,这或许是中国制造业展开系统性重构的一种重要表现。
很多专精特新企业的能量是通过改变原先价值创造方式释放出来的,它们在适当的时间,基于合适的技术构建了一个更加高效的新型价值创造系统,在这个系统中,效率大幅提高,综合成本明显下降,供给柔性大幅扩张,供给质量也大幅提升。
在新一代技术革命和大国博弈等趋势性力量的驱动下,中国制造业走向了深层次的结构性调整,驱动产业发展的系统性逻辑发生改变。研究中国制造,专精特新企业是极其重要的着眼点,而研究专精特新企业,更需要理解制造业在宏观和中观层面的变革趋势。
宏观视角:产业系统性重构是前提条件
据世界银行数据,2010年我国制造业增加值首次超过美国,跃居世界第一。此后十多年持续扩张,2021年这一指标占全球比重近30%,相比2010年的19.6%提高了10个百分点以上。中国在原材料、零部件中间品、机械装备、消费品等各个赛道齐头并进,价值链条不断延伸、壮大。中国的产业配套能力实现了全球领先,机械装备制造规模占据全球超过三分之一,中间品制造规模占据全球超过20%。
中国制造业“量”的势已成,“质”的势正快速凝聚。
2010年后,中国制造业在规模优势的基础上开始叠加体系优势,局部和细分领域已经出现了明显的系统性重构特征。这种重构并非是市场单方面的变化,而是技术原理、制造方式、产业组织伴随着需求的同步革新甚至变革。大量的创新型企业尤其是专精特新企业是这种系统构建的微观基础,它们推动了制造业细分领域不断专业化分工,从而带来效率、质量的大幅跃升。专精特新企业既是重构力量的重要贡献者,也不断从重构产生的变化中汲取动能。
伴随着中国制造业的系统性重构,国家层面也敏锐地感受和引导促成专精特新企业这股“势”。2011年,工业和信息化部首次提出要大力推动中小企业向“专精特新”企业发展。在国家战略加持下,专精特新企业开始集体涌现。截至2022年9月,工业和信息化部评选了四批共计8997家专精特新“小巨人”企业,全国认定省级专精特新企业4万多家,入库培育11万多家。这些专精特新企业大部分处于价值链的中间环节,为行业提供关键技术、基础材料、核心零部件和先进装备,它们既是材料和零部件供应商,又是复杂产品的创造者。
许多专精特新企业的崛起和这种系统性重构高度呼应。例如国内工业机器人行业近年来呈现爆发式增长态势,产量在六年内增长了十倍,伴随着市场的扩张,原先以汽车、电子为重要方向的供给能力需要进行革新,国内企业开始挖掘新的场景,开发新的产品,满足新的需求,从而对此前国外力量主导的产业格局进行系统性重构,其背后是大量专精特新企业持续在细分领域开展创新。目前行业内已涌现100多家专精特新“小巨人”企业,覆盖了从传感器、控制系统、伺服电机、精密减速机到机器人本体、机器视觉、系统集成各个环节。它们从产业市场扩张过程中获取规模优势,而其壮大也帮助中国工业机器人行业构建了全产业链的系统型竞争力。
中观视角:构建新的价值创造系统是竞争力所在
调研近百家专精特新企业之后发现,这些企业成功的关键之处是顺势而为,它们规模不大,多数营收规模处于1亿~10亿元区间之内,但是掌握技术深度的优势,对于客户理解度更高,更善于感知行业重构的趋势,同时其处于价值链中间环节,是产业链中的“活跃分子”,更容易组织产业链供需部门和技术链产学研部门进行协同创新,并大胆开展制造方式变革、营销服务方式变革甚至是组织变革,从而提供更好的产品和服务。很多专精特新企业的能量是通过改变原先价值创造方式释放出来的,它们在适当的时间,基于合适的技术构建了一个更加高效的新型价值创造系统,在这个系统中,效率大幅提高,综合成本明显下降,供给柔性大幅扩张,供给质量也大幅提升。
这一价值创造新系统的形成路径有多种方式,但常见的有三种类型。
第一种是基于产业集群的价值创造系统构建。这种模式较多发生在机械和复杂零部件领域,在这些产业集群中,专精特新企业往往是创新能力最高、组织能力最强的企业。例如无锡的汽车零部件制造商毅合捷,它定位于以更低的成本、更快的速度来满足100多个国家超过10000家客户的需求,但仅仅壮大自身生产能力难以兼顾效率、质量和规模等目标,后来企业通过工业互联网平台连接当地集群100家精密制造供应商,在设计、制造和商务等领域开展高水平的数字化、网络化协同来提高制造系统的柔性化水平。新的系统反应更加灵敏,制造更为柔性,最终带来业务的的持续快速增长,这家企业近三年营业收入年均复合增长率超过50%,2022年1~8月同比增速超过25%。
第二种是基于创新生态的价值创造系统构建。在许多高复杂度产业,新技术的突破带来了技术原理、产品功能、制造方式和应用场景等方面的同步革新,在某些时候会形成一个上下游高度协同的创新体系。专精特新企业往往是各种创新要素汇集的关键枢纽,它们一端深入用户内部,挖掘独特场景;另一端整合优质技术,开发出新产品,甚至创造出新赛道。
例如宁波力劲公司在2019年抓住了特斯拉的压铸机订单机会,成功开发并向特斯拉全球四大超级工厂供应9000吨超大型压铸机,助推了汽车底盘的一体化制造。随着新能源汽车产销量的快速增长,单一产品开始变成了细分赛道,一体化压铸技术逐渐成为汽车轻量化的主流技术方向,并逐渐演化成一个技术创新生态。这一技术创新生态,从供给端来看,力劲、瑞立、汇川、恒立等专精特新企业整合上海交大、浙大等高校资源,开始向免热处理合金、PLC、5G智能压铸系统等基础材料和关键零部件延伸。从需求端来看,文灿、鸿图科技、蔚来、小鹏等用户持续为力劲提供应用场景,应用数据不断反馈到力劲公司,完善了超大型一体化压铸机的试验认证,不断提升一体化汽车底盘、车身的良率,形成了全产业链创新的闭环和新的价值创造系统的构建,并借助市场的壮大不断放大价值。
第三种是基于互联网平台的价值创造系统的构建。民生消费产品领域一般产品复杂度较低,技术成熟度较高,客户数量庞大,中小企业很难凭借一己之力撼动行业格局,但是借助消费互联网平台可以连接更多客户,高效分解客户的大规模个性化需求,利用数字化产品可以承载更多增值服务,同时利用工业互联网可以轻松调动更多制造资源,这本质上是构建了一个设计、制造、消费高度协同的价值创造体系。北京有一家峰米科技,此前企业采取多车间多产品的品类策略,因为在产品上市之前,很难猜准消费者需求,新产品开发风险巨大。此后,峰米科技选择和京东、小米等消费互联网平台合作,集合峰米科技先进的光电技术、小米生态链的快反供应链和京东的市场大数据等优势,建立了协同创新的产业链价值链网络,通过数字化的协同设计、智慧供应链生产和大数据营销,实现了对消费者需求的精准定位和快速响应,2022年推出的峰米S5激光投影仪新品,成为线上智能投影仪的销冠产品。
微观视角:基于不满足感的持续改进,是动力之源
专精特新企业的成功因素往往具有多样性,很多企业由于规模不大,在组织层面上很少开展体系化的规划和系统性的管理,因此,企业发展的构思、关键性的决策以及战略性关系的维护往往都由企业负责人推动。
在这种情况下,负责人的认知和愿景尤其重要,关键性的决策大多来源于负责人对于技术和市场的判断,例如在宁波力劲决定配合特斯拉开展超大型压铸设备研制的时候,企业已经判断这个市场具有极大潜力,并早早开展技术储备。
但仅仅选对方向未必能成功,在做出正确选择之后,持续改进是更为重要的成功因素。而持续改进来源于企业的不满足感,企业面对竞争不服输,面向客户希望做得更好,面向供应链希望联系更为紧密,然后持续投入来改变产品、技术和组织。
这种不满足主要来源于四个方面。
一是企业认识到了能力瓶颈。例如浙江一家童车制造企业,一直希望自己能够开发出市场价格在千元以上的产品,但做了多次尝试,只能停留在200~300元区间。企业发现,仅仅拥有制造能力还不足以让其成为真正的专精特新,对客户需求的准确认知、创新性设计和供应链的高水平整合,才能开展高水平的价值创造。
二是企业认识到了效率瓶颈。例如浙江的一家输送线制造企业,近年来发现自己跟不上需求变化,重点客户的订单交付周期从此前4个月缩短至2个月以内,设计制造的单位成本也需要每年压低10%左右,企业不仅需要提升自身效率,还要想办法使配套企业也具有更高的效率。
三是市场需求变化带来企业经营复杂度提高。例如河北的一家工程零部件企业,它已经能开发制造近4万种产品,但小批量多品种已经成为客户的主要需求,它需要在5天内生产2000种产品来满足全球高端客户。因此,企业开始持续推进智能制造以形成高水平的柔性供给能力。
四是和行业对手的“贴身肉搏”带来的压力。目前国内有一批企业在制造规模上接近甚至超越国外竞争对手,但随着双方的短兵相接,竞争压力快速扩张。例如江苏一家大型机械设备制造商,其在欧洲的竞争对手开始在国内扩大制造规模,限制核心零部件销售,并开展本土化设计,同时将产品价格下调30%,导致企业争取新客户的难度也大幅提升。
综上所述,我们可以把专精特新企业的涌现理解为中国制造业开展系统性重构所形成的强大势能。正所谓“激水之疾,至于漂石者,势也”,企业的成功,固然离不开自己的努力经营,但更主要的是有效利用了产业重构的力量。所以专精特新企业都是非常聪明的企业,它们选择在细分领域的关键价值链环节深耕细作,在积累力量之后又善于把握住那些转瞬即逝的机会,也即“鸷鸟之疾,至于毁折者,节也”。不过,我们也要清晰地认识到,企业的发展没有止境,专精特新企业只是在一定阶段实现了领先,它们在未来也会面临更加激烈的竞争,决策者需要持续进取,突破一道又一道难关,最终才能从本土的专精特新走向全球的专精特新。
审核编辑 :李倩
-
制造业
+关注
关注
9文章
2259浏览量
53757 -
信息化
+关注
关注
1文章
494浏览量
21223
原文标题:系统性重构中国制造业
文章出处:【微信号:CADCAM_beijing,微信公众号:智能制造IMS】欢迎添加关注!文章转载请注明出处。
发布评论请先 登录
相关推荐
设备管理系统对制造业的重要性体现在哪些方面?
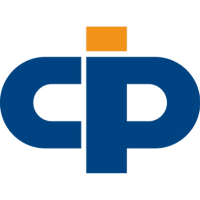
扬杰科技荣获2024中国制造业上市公司价值500强
制造业BOM应该如何管理?
华为UPS5000系列通关精密制造业UPS极限短路检测
计算机通信设备制造业、仪器仪表制造业等先进制造业发展向好
TPM邂逅机器人:智能工厂如何引领制造业革命性升级?
中国制造业企业总量突破600万家
欧时制造业产品及解决方案助力中国制造业企业工业数字化转型
深圳恒兴隆|制造业的新星:高光超精电主轴的崛起...
柔性制造单元:制造业的灵活利器
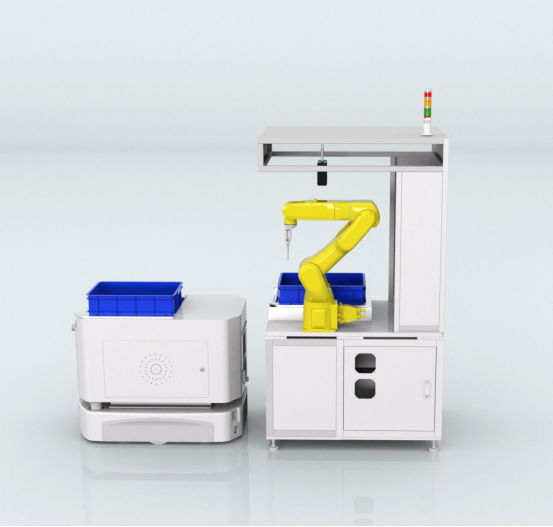
制造业应用TPM设备管理系统的重要性及价值
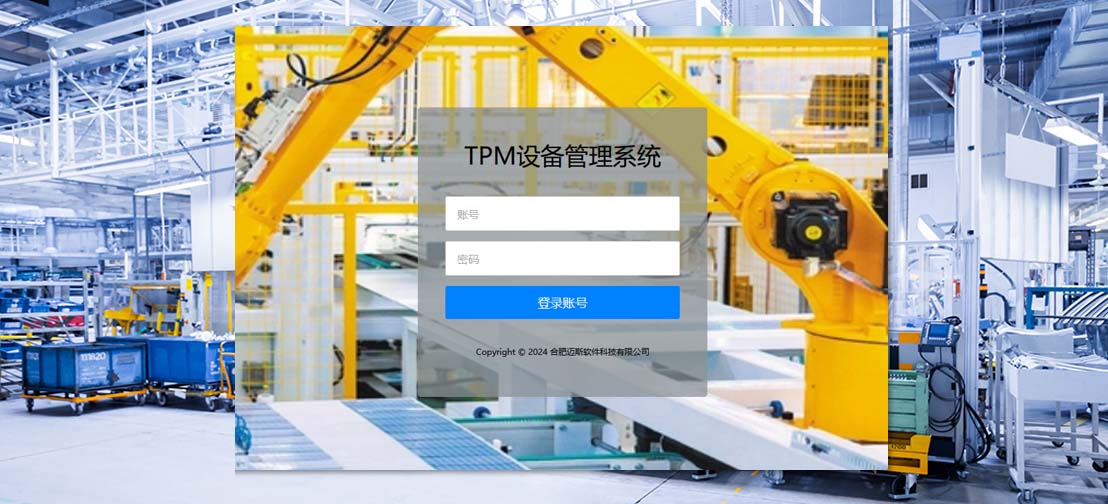
评论