功耗和散热是嵌入式电机控制系统开发人员面临的持续挑战,因为随着执行器在汽车中的部署越来越多、减少发动机二氧化碳排放的驱动力以及车辆重量的增加,集成度和性能密度不断提高。
本文以步进电机执行器IC为例,对电机控制软件和硬件环境提出了许多改进,旨在应对这些挑战。
在车辆中,电机和执行器的应用范围很广,从前格栅百叶窗和自适应大灯到车门后视镜调节器。电机控制IC顾名思义,控制电动机的性能。这些器件正在不断发展,以集成所有必要的功能,例如稳压器、振荡器、看门狗、闪存、EEPROM、ADC、相电流控制和电机驱动器。这种高集成度可在单个芯片内实现紧凑而智能的执行器设计。然而,缺点是集成度和性能密度的所有这些增加都会产生热量。在空间非常宝贵的嵌入式电机控制系统中,工程师在功耗和热管理方面正在达到极限。但这一挑战并非不可战胜;具体措施可以帮助解决电源散热问题。
建立热预算
为了确定热预算,我们研究了基于TDK-Micronas HVC 4xyzF SDB-I v4.1评估板的步进电机执行器,该评估板使用高度集成的电机控制IC(图1)。该板在结构和尺寸方面与现实生活中的应用相似。
图1:步进电机执行器框图
操作执行器的基本要求是:
最大可能环境温度 (TA) 由 IC 中的预期功耗 (PV_IC)、结和环境之间的热阻 (RthJA) 以及允许的最高结温 (TJ) 计算得出。在这里,应考虑IC在电路板上的环境温度,即没有任何外壳,尽管可能存在一个。作为最坏的情况,将应用最大值:
最大 T A =最大 TJ-PV_IC最大值xRth JA最大值
IC中转换的总功耗由电机驱动器(PMotorDriver)的功耗以及IC的CPU和外围模块(PDDP)的功耗组成。
PV_IC最大值=P电机驱动器最大值+P 最大 DDP
电机驱动器损耗由相电流 (IPhase_RMS) 和集成半桥的输出电阻计算得出。对于两个电机相位中的每一个,都要考虑高端(RDS(ON)hs)和低边晶体管(RDS(ON)ls)的电阻。一个PWM调制晶体管的开关损耗是近似值。
psw=1/2 x U x Ix(tr+t f)xfPWM
20 kHz PWM频率下的开关损耗、开关速度的标准设置和三个PWM调制晶体管由13%的附加功率损耗加法器表示。为简单起见,我们没有单独考虑随心所欲的损失。作为最坏情况的考虑,电机连续运行,即有效相电流连续流动。因此,电机驱动器损耗的计算公式为:
P电机驱动器最大值= 2 x(2 x(IPhase_rmsRDSONhs max.+RDSONls max.))x1.13
CPU和外设的损耗由IC的电流消耗(IDDP)和给定的工作电压(VBAT)决定。为简化起见,忽略可能存在的任何极性保护处的压降,这表示额外的安全裕度。
借助以下数据表最大参数,计算最大功耗:
P最大 DDP=IDDP最大值x 最大 V 蝙蝠
P最大 DDP=0.035Ax16V=0.56W
这使我们能够计算最大电机损耗:
P电机驱动器最大值= 2 x(2 x(IPhase_rmsRDSONhs max.+RDSONls max.))x1.13
P电机驱动器最大值= 2 x(0.25 2 A 2 x(2.8 Ω + 2.8 Ω))x 1.13 =0.791瓦
反过来,我们可以计算IC中转换的总功耗:
PV_IC最大值=P电机驱动器最大值+P 最大 DDP
PV_IC最大值=0.791 W+0.56W=1.351W
执行器的简化热模型(图2)表明,这仅限于初级热阻,这应该足以考虑稳态。
图 2:TDK HVC 4xyzF SDB-I v4.1 评估板的简化热模型
起点是类似于圆形评估板的电路板,由 FR4 材料制成;它厚1.6毫米,直径40毫米。它有两个信号层,一个 35 μm 铜层、一个 3 x 3 热通孔阵列和一个位于 ePad 下方底部的铜表面,其面积约为 0.75 cm2。
该电路板的最大RthJA约为32 K/W。因此, 我们可以计算电路板的最大可能环境温度。
最大 T A =最大 TJ-PV_IC最大值xRth JA最大值
最大 T A =150°C-(1.351瓦× 32K/瓦) =106.8°C
通常, 电路板和电机紧密地放置在外壳中。因此,要计算外壳内的温度,还必须考虑电机的功耗。我们使用的塑料外壳,测量的热阻(RthAH)为11 K/W。
电机损耗(PMotor)仅通过铜损来描述,铜损构成了大部分损耗,以保持简单。假设电机相位的电阻 RPhase 为 12 Ω。因此,我们可以计算电机的功耗。
PV_电机= 2x(IPhase_rms 2 xRPh酶)
PV_电机= 2 x(0.2502一个阿拉伯数字x12Ω)= 1.5 W
有了这些信息,我们就可以计算外壳中的总功耗(Ptot)。
Ptot=PV_ICmax.+PV_电机=1.351 W+1.5 W=2.851 W
因此,执行器外壳上的温度梯度(ΔT)由下式决定:
∆TAH=PtotWxRTHAHK/W
∆TAH= 2.851Wx11K/W=31,36千米
如果将此温度梯度添加到执行器的最大指定环境温度(85°C)中,则内部外壳温度为116.4°C。
之前计算的电路板的最高允许环境温度(106.8°C)与现在已确定的外壳内部温度(116.4°C)之间存在10 K的差距。因此,需要采取适当行动来弥合这一差距。
仅在需要时使用
降低功耗的最有效方法是完全不让它发生。因此,所有外设模块应仅在需要时处于活动状态。到目前为止,评估板中最重要的功耗是ADC(8 mA)、BEMF比较器(1.3 mA)和增强型PWM(1.1 mA)。
当电机运行时,即使在停留期间,BEMFC和EPWM也必须处于活动状态,以产生保持力。相比之下,ADC并不总是必需的,由于它是最大的功耗,因此可以通过“按需”操作实现显著的节省。
在我们的步进电机应用中,ADC测量反电动势电压,以识别过载和与之相关的步进损失。假设速度为每秒1000个完整步,则ADC每秒或每毫秒激活1000次。转换时间为1 μs,每个事件使用8次顺序转换,并考虑预热和同步时间,使ADC总活动时间为每整步20 μs。
因此,平均活动时间(TA)可以按如下方式计算。
T A=T开/T周期=20 μs/1000 μs= 0.02
由此,我们可以计算出ADC的平均电流消耗(IADC_av)。
IADCav.= 8 mA×0.02=0.16mA
因此,模块的电流消耗可以降低7.84 mA,相当于功耗降低7.84 mA×16 V = 125.4 mW。
优化时钟速度
在嵌入式执行器中,软件通常是事件控制的,其中动作由中断触发。CPU 主要参与后台任务和等待新事件。这些事件可以是内部事件(如定时器中断)或外部事件(如过压或欠压中断)。
在非时间关键型后台任务期间动态减慢 CPU 时钟速度可降低电流消耗。一旦出现中断,CPU可以自动切换到最大时钟速度,并且可以以最大速度处理中断服务例程。在中断服务例程结束时,软件切换回较低的时钟速度。
对于典型的步进电机软件,CPU 平均花费 40% 的时间执行中断服务例程。这意味着 60% 的时间都花在处理后台任务上;在此期间减慢时钟速度将显著降低电流消耗。
一个很好的折衷方案是为后台任务选择 5 MHz 的 CPU 时钟速度。最大时钟速度的四分之一(20 MHz)可节省38%的电流(图4)。因此,总电流消耗(不含电机驱动器)降低了60%,×38%=22.8%。
图 4:TDK HVC 4223F MCU 标准化为 20 MHz 的电流消耗。该行表示当前节省。
HVC 4223F MCU 在所有外围模块关闭的情况下(其中 fYS = fCPU = 20 MHz)的典型电流消耗为 15 mA。因此,可以节省15 mA×22.8% = 3.42 mA。这种节省相当于功耗降低3.42mA×16V = 54.72 mW。
降低开关损耗
电机驱动器中的开关损耗由电压、电流和开关时间引起。由于外部要求决定了电压和电流,因此只能改变开关时间。在这里,我们可以分三个阶段设置开关速度。在最快的设置下,与最慢的设置相比,切换时间可以减少一半以上。计算出将开关损耗加法器从电机驱动器损耗的13%降低到5%。
P电机驱动器最大值= 2 x(2 x(IPhase_rmsRDSONhs max.+RDSONls max.))x1.05
P电机驱动器最大值= 2 × (0.250²A²×(2.8 Ω + 2.8 Ω))×1.05 =0.735W
由于最初的功耗计算为0.791 W,这相当于功耗降低了56 mW。但是,请注意,必须仔细考虑电磁兼容性,因为这种分期技术可能会影响个别情况。
印刷电路板优化
QFN 封装底部的 ePad垂直获取主热流。热量必须从芯片下方传导, 通过电路板到 PCB 的底层。因此,必须使底层的铜表面尽可能大,以保证水平分布和有效散热。
由于标准过孔存在焊料流出的风险,我们建议用树脂填充并用铜覆盖它们。我们还建议通过数组使用 4×4 或 5×5。再多也只会导致热阻略有降低(图 6)。如果对机械稳定性的要求允许, 还可以减小电路板的厚度, 因为垂直方向的热阻与电路板厚度成正比。
图 6:通过 2×2 标准化过孔的 Rth
通过最大化连接到ePad的接地层,可以进一步改善散热。通过布局优化,铜表面可以翻倍至约1.5 cm²,从而将热阻降低2 K/W.与热阻为32 K/W的原始两层电路板相比,这些优化将其降低到26 K/W。
如果成本不是问题,您可以使用四层电路板,通过将 ePad 连接到额外的内层接地层,将热阻降低到 20 K/W。
将外层的铜层厚度加倍至 70 μm 也更便宜,但效果较差, 这使得该电路板上的铜层厚度减少了 1 到 2 K/W.但是,如果您决定采用此选项,请在早期阶段这样做,因为较厚的铜层会影响信号层的布局。这是因为当铜厚度加倍时,最小轨道宽度和距离必须几乎翻倍。
最大净空
通过优化软件,IC的功耗可降低238.1 mW。电路板上的优化措施将热阻 (RthJA) 降低了 6 K/W。有了这些新数字, 我们可以重新计算电路板允许的最高环境温度。
最大 T A =150°C-(1.351 W-0.2381W) ×(32-6)K/W=121.0°C
通过简单且具有成本效益的措施,与电路板最初允许的最高环境温度 106.8°C 相比,可以实现 14.2 K 的改进。
功耗降低后沿外壳的温度梯度的新计算结果为:
∆TAH=2.851宽-0.2381宽 x 11K/W=28.74千米
与初始温度梯度 31.36 K 相比,这相当于提高了 2.62 K。加上执行器所需的最高环境温度 (85°C),新的内部外壳温度为 113.7°C。 这缩小了差距,具有 7.3 K 的舒适动态余量。
结论
对软件和电路板进行经济高效的优化可以提高应用的热预算,并为嵌入式电机控制系统的开发人员提供充足的余量。重要的是,这些改进可以在任何嵌入式电机控制系统上实现。
TDK-Micronas HVC 柔性伺服驱动器系列能够以经济高效的方式开发高性能和紧凑型嵌入式电机控制系统。它们由 32 位 CPU (ARM Cortex-M3) 提供支持,解决了功耗散热挑战。除了我们在计算中使用的两相双极步进电机外,集成了所有必要功能的微控制器同样适用于最多三相的无刷直流 (BLDC) 电机和有刷直流 (BDC) 电机。
审核编辑:郭婷
-
嵌入式
+关注
关注
5082文章
19093浏览量
304613 -
控制系统
+关注
关注
41文章
6595浏览量
110569 -
电机
+关注
关注
142文章
8987浏览量
145314
发布评论请先 登录
相关推荐
LDO在嵌入式系统中的应用 常见LDO故障及解决方法
【「嵌入式Hypervisor:架构、原理与应用」阅读体验】+第7-8章学习心得
嵌入式系统的未来趋势有哪些?
嵌入式系统怎么学?
了解嵌入式驱动器中的电源模块
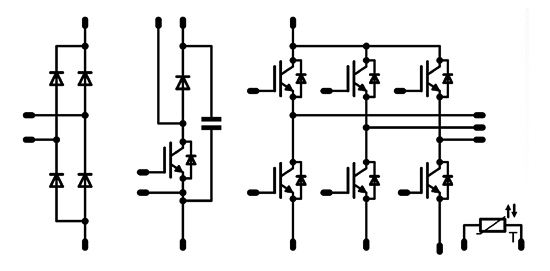
评论