在微机电系统(MEMS)工艺中,沉积金属作为掩模是目前较为常用的方法。金属掩模的制备一般采用溅射与电镀结合的方式,在衬底上先溅射用于电镀工艺所沉积金属的种子层,然后采用电镀的方式生长金属掩模。
据麦姆斯咨询报道,为了优化和控制电镀过程,近期,来自中北大学的研究人员于《传感器与微系统》期刊发表论文,对溅射剥离再电镀工艺的电镀铜(Cu)沉积过程进行了仿真模型的构建,研究了电镀过程中晶圆表面整体沉积情况以及背腔位置的金属纵向与横向生长情况,并探究了溶液电导率对金属掩模沉积的影响。最后将溶液电导率设置为15 s/m时,金属掩模的仿真计算结果与实际电镀沉积情况进行了对比,验证了仿真模型的可靠性。
电化学仿真
电镀三维仿真几何模型如图1(a)所示,阳极为一个溶解Cu板,阴极为通过溅射剥离方式含有Cu种子层的4英寸晶圆,其余部分为电解质溶液。为研究背腔边界Cu在电镀过程中向垂直与水平方向的生长情况,图1(b)为将实际的三维晶圆电镀模型简化在二维平面上,上边界为阳极表面,中间部分为电解质域,下表面的中间凸起表示溅射金属为阴极表面的3个部分。
图1 电镀仿真模型
溶液电导率为15 S/m时,阴极的电镀情况如图2所示。从图2(a)与图2(b)中可以看出,晶圆边界处其电解质电位高于中心器件区位置,17 min时边界电解质电位最大为0.1993 V,器件区电解质电位最小值为0.04845 V,相差4.11倍。电解质电位从晶圆边界向内呈指数衰减至0.05 V后趋于稳定,中间器件区位置由于靠近背腔的镀层侧壁存在局部电流集中导致其电解质电位升高,在晶圆中部呈现出波浪状的电解质电位分布。图2(c)与图2(d)为晶圆Cu镀层的沉积结果图,Cu镀层最大沉积厚度在晶圆边界,值为59.3132 μm,镀层最小厚度位于晶圆器件区中心位置,值为14.3953 μm。沿直径方向镀层厚度曲线变化与表面电解质电位分布曲线一致,晶圆边界处镀层厚度沉积厚度较大,但范围占比较小,晶圆器件区整体镀层厚度偏差在6.56%。
图2 电导率为15 S/m晶圆镀层电解质电位与厚度分布
接着,通过参数化扫描方式对比电解质电导率在5 S/m、10 S/m、15 S/m时电镀效果。从图3的仿真结果可以看出,随着溶液电导率的提高,电解质电位分布更加均匀,晶圆边界与中心处镀层厚度差减少,电导率为5 S/m、10 S/m、15 S/m时,晶圆镀层最大、最小厚度比值分别为7.30、5.07、4.12,整个晶圆表面镀层厚度过渡随着电导率的提高更加平缓,器件区整体镀层厚度提高。
图3不同电导率下晶圆镀层电解质电位与厚度分布
实验验证
如图4所示,将4英寸单抛硅(Si)片使用7133负性光刻胶进行喷涂,使用背腔尺寸为1000 μm × 1000 μm的5英寸掩模版进行光刻,显影去掉背腔位置之外的光刻胶。在MESP-3200磁控镀模设备先溅射20 nm的铬(Cr)作为黏附层,再溅射200 nm的Cu作为种子层,使用无水乙醇超声5 min进行剥离,只留下溅射在Si片表面的金属,镀件准备完成。
图4 待镀件工艺流程
随后使用磷质量分数为0.1%-0.3%的磷铜板以避免Cu板在硫酸盐镀液中以Cu+形式溶解。输出电流控制为4 A,电镀时间为17 min,使用鼓泡机进行空气搅拌,整个实验在超净间完成,避免外部环境对电镀液的污染。
接着,以背腔位置Si面为基准平面,测试镀层表面到Si面位置的相对高度来实现对镀层厚度的测量,镀层曲线形貌如图5所示。中心点位置镀层厚度为13.92 μm,与仿真计算结果偏差为3.41%,镀层曲线形貌与仿真结果一致,镀层厚度向背腔位置逐渐升高,且在侧壁位置有因为局部电流集中有明显凸起。
图5 中心位置镀层厚度台阶仪测试曲线
综上所述,该研究基于电化学理论,构建了晶圆电镀模型,模拟了溅射—剥离方式电镀金属掩模的生长过程,并通过实验验证了仿真模型的准确性。研究结果为采用溅射—剥离方式电镀金属掩模进行背腔深刻蚀的(碳化硅)SiC压阻式压力传感器芯片加工涉及的工艺补偿提供了仿真模型设计参考。
审核编辑:郭婷
-
传感器
+关注
关注
2551文章
51097浏览量
753556 -
mems
+关注
关注
129文章
3931浏览量
190625 -
仿真
+关注
关注
50文章
4082浏览量
133602
原文标题:MEMS电镀金属掩模工艺优化研究
文章出处:【微信号:MEMSensor,微信公众号:MEMS】欢迎添加关注!文章转载请注明出处。
发布评论请先 登录
相关推荐
仿真系统的性能优化技巧
Simulink模型仿真与分析技巧
PCBA线路板镀金与沉金:如何选择最适合的工艺?
电镀工艺流程详解 电镀技术在工业中的应用
韩国将开始量产用于第6代OLED制造工艺的精细金属掩模板
点亮创造力,一文详解pcb电镀金
在连接器电镀加工中镀金含量是多少?
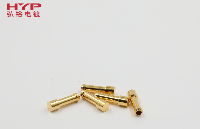
使用仿真模型进行拓扑分析

评论