微笔直写技术属于广泛应用的电子3D凹印技术,采用电子浆料为原料,用微细笔装置以气体为动力将电子浆料按照三维线路图形布线要求沉积于预先成型的基板表面,然后辅助采用激光烧结或炉体固化,即可形成所需要的导电图形,其成型原理如图1所示。
图1 微笔直写原理图及微笔直写微观形貌(100倍)
据麦姆斯咨询报道,近期,中国电子科技集团公司第三十研究所创新性地尝试采用微笔直写技术打印天线阵面,通过打印材料选择、打印参数优化实现天线阵面的打印,并通过专业测试,评估未来电子3D打印在天线阵面上制造应用的可行性。相关研究成果以论文形式发表于《电子工艺技术》期刊。
打印材料选取和打印参数优化
首先,研究人员根据材料黏度、介电性能、导电性能等因素,选取聚酰亚胺(PI)为介质基板打印材料,选取导电银浆作为辐射阵元图形打印材料,金属基体采用常用的5A06材料,由数铣加工而成。接着,根据打印的聚酰亚胺介质板的介电常数测试和分析结果,针对阵元及介质板厚度开展尺寸调整设计。经样件的测试,确定相应工作频段内聚酰亚胺的介电常数值,并根据驻波、波束范围、波束宽度等主要设计需求,综合聚酰亚胺介电常数测试值、测试误差等开展天线阵面单元设计以及容差设计,确保样件的打印工艺性。最终,经天线仿真和计算,确定介质层厚度为0.4 mm,贴片尺寸为4.04 mm × 3.69 mm,贴片加工误差为±0.0254 mm,孔位间距误差为0.05 mm。
图2 天线阵面打印样件优化设计图
天线阵面介质基板大面积打印
在微笔直写设备上选用0.31 mm的针头,分别采用“回”字形、“一”字形打印路径进行大面积(100 mm × 100 mm)聚酰亚胺溶液的直写打印(如图3所示),并观察打印效果。最终选定打印路径为“一”字型策略,并选取每打印三层,以150℃中间预固化、保温10 min的方案作为预固化参数,完成天线阵面介质基板的大面积打印。
图3 不同打印路径的效果图
天线阵元图形打印
首先采用已有的直写打印技术在铝合金天线基板上打印聚酰亚胺基板,再采用紫外激光对聚酰亚胺基板进行打孔加工。完成聚酰亚胺介质层打孔后,采用已有的直写工艺在聚酰亚胺介质层0.6 mm孔内逐层打印银浆以填充孔,且逐层激光烧结使孔内银浆固化成形。与此同时,采用相同的直写工艺及参数在聚酰亚胺介质层上继续打印完成阵元贴片的打印。表层阵元贴片经激光烧结固化后,再次采用与聚酰亚胺介质层打孔相同的紫外激光及参数打出0.6 mm的馈电孔,最后形成阵元图形。
图4 天线基板上介质层打印并打孔
天线阵面打印
所选样件阵面为非展开曲面,但整体曲率半径较大,整体高度差在10 μm以内。就微笔直写打印工艺特点而言,通过微笔直写形成线条,再通过路径形成整个面,可以从打印路径上进行分解简化,转换为二维平面进行加工,以满足打印成型需求。采用已经成熟应用的微笔直写工艺参数、聚酰亚胺多层固化工艺参数及电子浆料激光烧结工艺参数,进行了打印样件的制作(如图5所示)。
图5 天线阵面打印样件效果图
综上所述,该研究采用微笔直写3D打印技术打印微带天线阵面,并通过聚酰亚胺及导电银浆成功实现了微带天线阵面的3D打印制造。经测试,微带天线阵面孔精度、孔对位精度及电压驻波比均满足设计要求。因此,微笔直写3D打印技术具备的快速制备和快速验证,以及结构设计自由度大的特点,有效保证了电子产品研制的快速开发需求。但是,电子3D打印的后处理技术、成本及效率控制等方面均有待深入研究,以进一步促进电子3D打印技术的发展及在电子产品上的应用。
审核编辑:郭婷
-
天线
+关注
关注
68文章
3181浏览量
140707 -
3D打印
+关注
关注
26文章
3544浏览量
108865
原文标题:微笔直写3D打印天线阵面工艺研究
文章出处:【微信号:MEMSensor,微信公众号:MEMS】欢迎添加关注!文章转载请注明出处。
发布评论请先 登录
相关推荐
3D打印在珠宝行业的设计和制造应用-CASAIM
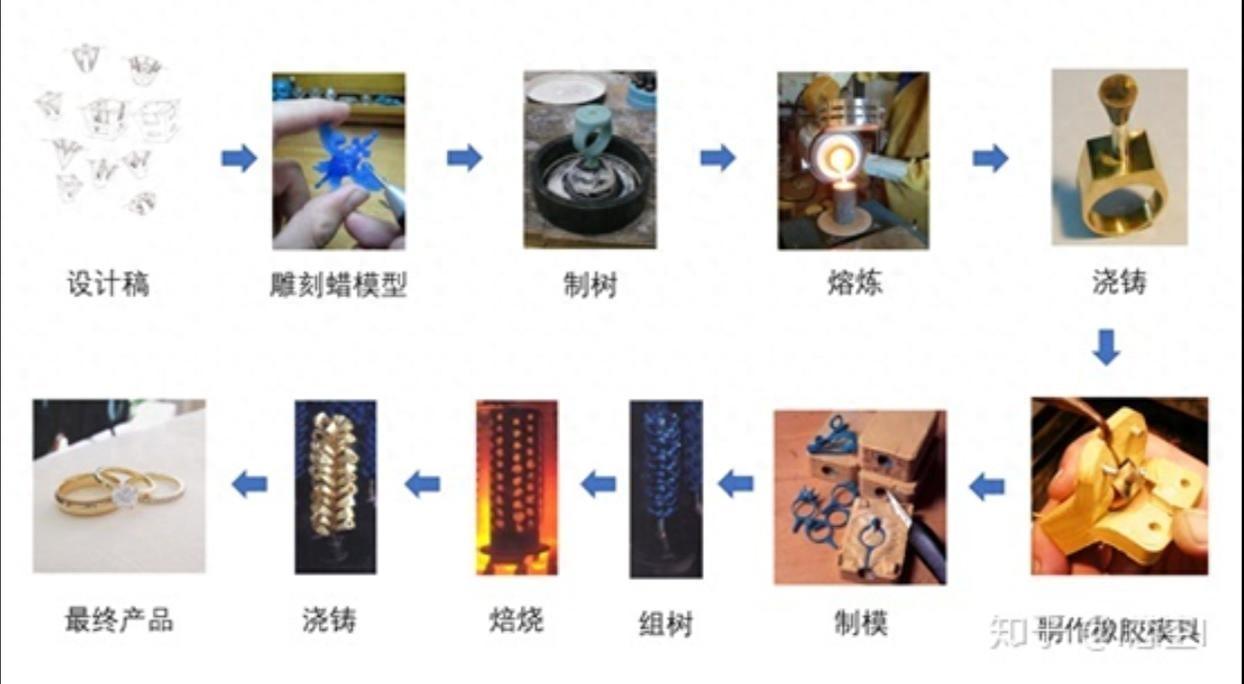
评论