介绍
位于高压、恶劣、嘈杂的工厂车间环境和复杂的低压可编程逻辑控制器 (PLC) 之间的边界是经常被忽视且不起眼的数字 I/O 模块。由于应用用途的多样性以及对电气隔离、小尺寸和低功耗的共同要求,这些模块的设计具有挑战性。在本设计解决方案中,我们将研究I/O模块数字输入(DI)组件的传统“分立”设计的局限性,这些设计集中在高功耗产生的热量上。然后,我们提出了一种替代方案,与传统方法相比,它具有几个独特的优势。
PLC 的 IEC 61131-2 标准规定了三种不同类型的数字输入接收器:类型 1、2 和 3。该标准规定,Type 3的理想实现方案在逻辑高电平状态下应尽可能接近2mA,电压转换门限在5V至11V之间。
3类接收器的典型分立式实现如图2所示。隔离利用光耦合器提供。接收到的输入信号阈值使用分压器R1和R2设置,然后使用具有迟滞的电压比较器解释为逻辑高电平或逻辑低电平(以提供抗扰度)。
数字输入设计
数字 I/O 模块通常由 16 或 32 个数字输入或数字输出 (DO) 通道组成。某些模块允许根据需要将通道配置为 DI 或 DO。数字输入与PLC和电机驱动器一起使用,以接收来自现场传感器和开关的数字信号。由于现场电压(24V或更高)远高于PLC逻辑电压(5V或更低),因此DI的一个关键要求是出于安全原因在两个域之间提供电气隔离。
图2.带基本限流的数字输入
这种电路配置效率低下,因为它仅使用电阻来限制电流消耗(这显然取决于电压)。对于 32V 输入,此配置可消耗超过 10mA 的电流。
在紧凑的多通道模块中,功耗(及其相关的散热)是一个关键问题。因此,必须实施更复杂的电流限制形式。可以构建定制设计的限流电路,但需要10多个分立元件:TVS、电阻、晶体管、基准电压源和比较器。该解决方案的电流消耗通常为5mA,是3类输入的理想电流2mA的两倍,并且这种设计消耗的电路板面积相对较大。这种方法的另一个缺点是,虽然限流比使用简单的电阻分压器更准确,但其工作的数字输入电压范围可能非常有限。
图3.具有离散电流限制功能的DI
减小功耗和尺寸
离散组件方法的一个更好的替代方案是使用集成解决方案。与分立式解决方案相比,这有几个优点。电流消耗降低到更接近Type 3输入的理想规格的水平,电流限制变得更加精确,这两者都有助于减少散热。与分立解决方案相比,集成器件还可以在更宽的输入电压范围内工作,并有可能减少电路板面积。
图4所示的寄生供电数字输入是符合IEC 61131-2标准的全集成数字输入,可将24V数字工业输入转换为2.6mA (最大值)电流,以驱动光隔离器。单个DI通道的功耗约为65mW (24V 2.6mA),与限流分立式方案的210mW (24V ×8.75mA典型值)相比,功耗降低了三倍以上。在整个电压输入范围内,电流消耗限制在2.1mA至2.6mA之间,变化仅为25%。与分立式解决方案相比,这是一个巨大的改进,在分立解决方案中,电流变化可能超过100%。与其他集成解决方案相比,这也是一个改进,这些解决方案的电流范围为每通道2.3mA至3.4mA,变化为35%。电压阈值和电流水平符合 1 类和 3 类输入。该器件兼容 48V 输入,并增加了外部电阻器。它提供 60V 的最大工作电压,而其他典型集成解决方案仅允许 45V。另一个吸引人的特点是工作电流来自输入信号,无需专用的现场侧电源,从而简化了电路板布局。
图4.MAX22191功能框图
小型 6 引脚 SOT23 封装尺寸为 2.8mm × 2.9mm,与分立元件方案相比,所需电路板面积减少了多达 40%。根据所需的应用,该器件可配置为拉电流或灌电流。它具有 250ns 的快速响应时间,支持高速 DI 器件,1kV 浪涌保护(使用外部 TVS)即使在最具挑战性的工业条件下也能确保鲁棒性。
图5中的热图像显示了与分立式DI方案相比,使用该IC时的有效散热效果。两种解决方案都在同一电路板上,在典型的实验室环境中,单个24V输入信号记录的温差》15°C。在多通道模块的密闭空间中减少热量的潜力是显而易见的。
图5.分立DI与MAX22191的热图像
结论
我们 回顾了 PLC 数字输入的典型分立元件实现的局限性,然后将其性能与几乎完全集成的方法进行了比较。我们 介绍 了 一种 寄生 供电 的 数字 输入 IC, 该 IC 提供 了 更小、 更 低功耗 的 解决 方案, 且 发热 少 得多。它适用于过程自动化、工业自动化、电机控制、单独隔离的输入和具有电流吸收/拉出输入的应用。
审核编辑:郭婷
-
光耦合器
+关注
关注
8文章
502浏览量
36422 -
接收器
+关注
关注
14文章
2486浏览量
72487 -
plc
+关注
关注
5021文章
13437浏览量
467017
发布评论请先 登录
相关推荐
I/O接口与I/O端口的区别
使用TPS2661x保护模拟输入和输出模块中的HART I/O
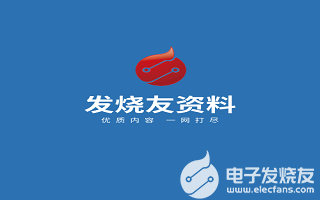
Pickering Interfaces扩展PXI数字I/O模块组合
品英Pickering扩展业界最大的 PXI 数字 I/O 模块组合
Pickering Interfaces 扩展了业界最大的 PXI 数字 I/O 模块组合
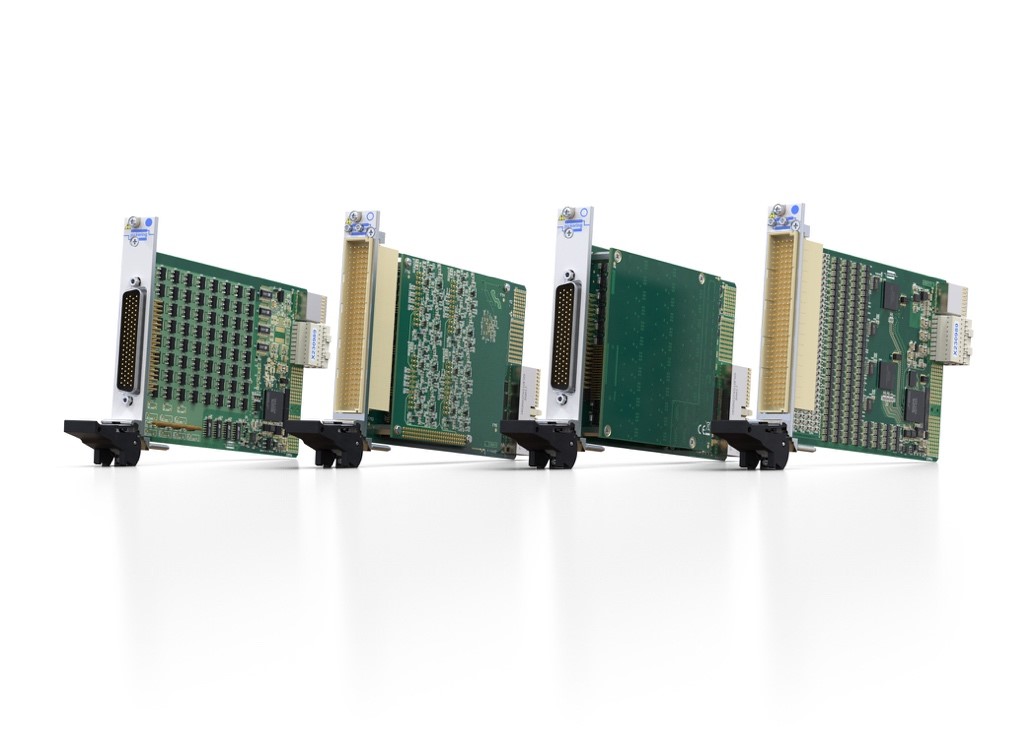
PLC的I/O模块的作用及其重要性
电子电气|T15系列I/O模块精选推荐
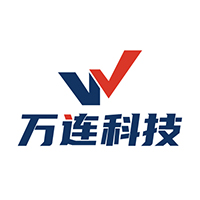
评论