系统性良率问题正在取代随机缺陷,成为最先进工艺节点半导体制造中的主要问题,需要更多的时间、努力和成本来实现足够的良率。
良率是半导体制造中的终极秘密话题,但它也是最关键的,因为它决定了有多少芯片可以有利可图地出售。PDF Solutions的首席技术官 Andrzej Strojwas 说:“在较旧的节点上,当您开始批量生产时,您唯一需要担心的良率问题就是随机缺陷。”“大多数系统学将被淘汰,参数问题将得到控制。”
情况不再如此。Strojwas 解释说,系统缺陷和参数变化现在出现在早期生产中,需要积极的良率管理策略才能将产品良率提高到可接受的水平。“有时特定的布局模式会出现问题,”他说。“例如,在互连层面,您可能会遇到金属岛问题,这些问题会导致灾难性故障,如短路或开路。不幸的是,尽管人们对光学邻近校正(OPC)给予了很多关注,以确保打印的结构非常接近设计意图,但这些情况仍在发生。”
图1:分析以解决良率上升的设计系统问题。资料来源:先进制造公司
GlobalFoundries 最近在其寿命为两到三年的 14 纳米 finFET 移动产品的量产期间实施了良率改进方法。该公司表示,工艺、设计和布局之间的系统性缺陷是早期良率损失的主要原因。该流程(见图 1)将客户 GDS 文件与经过调整的从设计到硅的流程相结合,该流程根据历史学习中的弱点或缺陷评估良率损失。设计特征为模式匹配提供输入,计算过程开发期间捕获的薄弱点 (WP) 或夹点的出现次数。设计示意图根据产量影响对 WP 进行排名,并将其反馈到 NPI 工艺设置中。最关键的是,在 NPI 设置期间使用在线 CD、明场检查、电子束扫描、自动图案检查和工艺窗口鉴定对系统进行全面的工艺表征。根据这些发现实施修复,然后在晶圆上进行验证。
在一个例子中,GlobalFoundries 的工程师发现了一个中间线接触接触短路的薄弱点,“这与一个 7.5T 标准电池有关,双图案接触 (CA) – CA1 和 CA2 之间的边缘空间很小,晶圆边缘芯片丢失(>5%)(见图 2)。基于设计布局分析和图案匹配,实施了光学邻近校正 (OPC) 修复解决方案以扩大工艺余量并提高良率,如图 2g 所示。“CD 检查确认了整个过程窗口。”
图 2:通过光学 (a)、布局 (b、e) 和电子束 (d) 确认的触点短路已使用 OPC 进行校正,并通过更大的间距 (f) 和晶圆边缘良率增益 (g) 进行了验证。资料来源:IEEE ASMC
3D 计量和良率学习
最近最重要的变化之一是 3D 检测和计量学习的增加。finFET 和纳米片晶体管的采用发生在前端,而高级封装则需要在后端进行 3D 计量。
“我们看到的主要挑战实际上是 3D 复杂性,” Nova的首席技术官 Shay Wolfling 说。“所以这始于具有数百层的 3D NAND——而且不是一层,而是两层和三层。客户不仅对 CD 感兴趣,还对顶部 CD、中间 CD 和底部 CD 感兴趣——配置文件中的多个参数。堆叠纳米片的逻辑也是如此。”
例如,纳米片晶体管的三维测量和过程控制产生了一种新工具,即垂直移动光谱仪,Wolfling 将其描述为在传统 OCD 功能(散射测量)之上添加了干涉测量法。这项新技术为反射率测量带来了额外的相位信息,例如,这显着提高了纳米片晶体管中腔体和间距测量的准确性。
在 FEOL 中,同时使用了光学和电子束技术。西门子 EDA 的Tessent Group产品管理总监 Matt Knowles 说:“在晶体管级别采用环栅技术,你会在前端缺陷中引入更多的复杂性。”“已经完成了光学检测并正在应用电子束检测,但浇口的三维特性带来了重大挑战。”
具体而言,Knowles 强调布局模式系统缺陷的影响越来越大。“这是人们多年来一直面临挑战的领域,但在高级节点,图案复杂度更高,这些缺陷可能占良率的百分之几。因此,我们将 YieldInsights YMS 的机器学习与 PDF Solutions 的模式引擎相结合,以解决其中的一些问题。”
模式签名
在生产过程中,工程团队寻找可用于快速提高产量或减少产量限制事件影响的可操作数据。工具和处理问题通常在晶圆级模式中捕获,软件程序可以对其进行建模和自动识别。
良率管理系统中的机器学习可以分析晶圆级空间模式。例如,Skywater Technology 和 Onto Innovation 的工程师实施了基于 ML 的空间模式识别 (SPR) 引擎,以根除由于工艺或工具边际性导致的系统产量问题。该引擎主动生成高影响步骤的 Paretos,以更有效地识别产量限制事件的原因。“半导体行业对采用 SPR 并不陌生,”SkyWater Technology 的 David Gross 说。“然而,有效利用 SPR 结果来加快确定根本原因和采取纠正措施仍然是一个挑战。”
图 3:三个月的未知模式学习结果。资料来源:IEEE ASMC
产量改进方法从基于 ML 的基于数月生产数据的模式自动发现开始(见图 3)。工程师将模式样本添加到库中,而库和配方设置组合用于改进跨多个产品和层的模式识别。在生产中,当晶圆检测、计量和探测数据被输入良率管理系统时,SPR 引擎会检测具有空间特征的晶圆并对其进行分类。根据工程师的监控标准,采取自动行动,例如电子邮件警报、自动报告等。
SPR 引擎识别出三种未知图案,包括光刻条纹、两个边缘带和一个中心簇。“光刻条纹可能是由于光罩污染或检查配方敏感性问题造成的。但是,执行 Repeater 和 Event Reports 等深入分析可以快速找出根本原因。”生产中的产量限制模式仪表板(见图 4)被发现可以提高工程生产力 (+25%),方法是突出显示有助于产量限制警报条件的工艺工具,从而实现快速反应和恢复。
图 4:通过将设备研究信息与 AOI 图像相结合,使用仪表板定期监测缺陷模式将工程生产力提高了约 25%。资料来源:IEEE ASMC
Skywater 的其他案例研究确定了受特定空间模式影响的所有晶圆,从而无需进行耗时的手动分类。SPR 引擎还可以在完全影响之前捕获已知的故障模式,例如晶圆上呈风车状的蚀刻薄片,其实时警报会通知工程师组件需要更换。该团队得出结论,SPR 引擎有助于勾勒出偏移范围并将内联签名与限制产量的缺陷相关联。
可操作的数据
更好的数据分析程序有助于更好地利用缺陷和故障数据。“我们看到的一个大趋势是,为了让缺陷数据更容易获得和操作,人们在生产中运行更多的批量诊断,”Knowles 说。“过去,只有几家大公司收集并分析了他们所有的故障数据。其他客户在新产品推出或某些良率问题的临时基础上这样做。但现在,所有客户都变得更加主动。他们必须这样做,因为他们不能忍受持续一周或更长时间的收益率波动。”
缺陷隔离是一项持续的挑战,尤其是当缺陷被隐藏时(见图 5)。“在前端,你有两种功能截然不同的工具,”诺尔斯说。“第一个检测工具非常快速地扫描整个晶圆,寻找所有污染物和缺陷。然后,审查工具会提供非常高分辨率的图像,很可能就是您要查找的缺陷。”他指出,审查分析已缩短到大约 10 分钟。
然而,陈指出,抽样程序正在发生变化。旧例程不足以捕获所有致命缺陷,尤其是在汽车和服务器芯片中,可接受的缺陷水平低于 ppm。因此,公司必须投资于工具以提高产量,例如使用 TSMC 的 CoWoS 的 HBM 内存堆栈。他指出了一种范式转变,从在少数芯片上产生 ppm 速率的旧采样率到具有数千个具有复合故障率的设备的现代汽车系统。“在服务器单元或高性能人工智能芯片中,投资回报率更具吸引力。但是对于外包制造,任何影响生产力的事情,比如额外的检查步骤,都需要一个整体的行业解决方案。”
图 5:100% X 射线缺陷检测(左排图像)之后是审查(中)和横截面验证(右),以隔离 HBM 中光学技术可能遗漏的隐藏缺陷。资料来源:Bruker
Bruker对芯片连接后的 X 射线检查和审查的采样率和自动反馈进行了研究,以确定最佳采样率、良率增益和偏移持续时间(见图 6)。“我们对 HBM 隐藏缺陷的分析表明,您可以通过进行 30% 的采样来显着减少偏移时间,这会产生大约 7 天的偏移时间。一直到 100% 采样可将产量提高 1.7%,并将偏移时间缩短至 2 天。”
快速计量过程反馈是将缺陷率提高到 100 ppb 水平的关键。“对于自动反馈,仅仅提高采样率是不够的,”Bruker 说。“实际上,您需要提供更多反馈才能在工艺窗口内进行自动更正,以将事情保持在工艺规范内。”
图 6:30% 的采样率将偏移时间减少到 7 天。最终,采样率达到收益递减点。资料来源:Bruker
工程师识别可操作数据的方法之一是通过故障缺陷分类 (FDC) 程序。FDC 使用过程工具上的传感器数据和监控数据来自动对故障进行分类。“我们在工艺工具和计量系统上做越来越多的 FDC,” Onto Innovation软件产品管理总监 Mike McIntyre 说。“例如,有一种最著名的方法是将 FDC 放在您的计量工具上,从而实现车队匹配,从而能够确保它们每天的行为始终如一。这样您就不必依赖校准标准来确保计量测量处于受控状态。因此,我们正在引入这种学习,我们可以开始研究工具上的固有信号。”
但越来越多的工具上的传感器数量在增加,因此维护和分析来自过程监视器的所有数据的成本也在增加。并且需要在整个产品生命周期中从一开始就跟踪缺陷。
数据分析和生命周期管理
晶圆厂、组装和测试设施的数据管理有两个方面——历史数据和日常运营产生的实时数据。Synopsys硅生命周期管理高级产品营销经理 Guy Cortez 表示:“在宏观层面上,随着先进节点的出现,需要分析的数据量确实发生了阶跃函数变化。”“这些工具必须能够很好地处理架构,以执行容量分析、跟踪实时和历史数据以了解产量问题,从而支持实时行动。”
半导体加工中的数据管理挑战可以简化,尤其是从真正重要的方面来看——半导体材料或芯片。“在 Onto,我们查看数据,我们基本上发现它都符合三个向量之一,”麦金泰尔说。“它要么是与正在生产的材料相关的矢量,要么是与在材料上执行功能的设备相关的矢量,要么是与应用于影响材料的工具的过程相关。所以所有数据都属于这三个桶之一。这有助于我们组织数据进行分析。”
从设计方面来看,内存设计和制造都得益于自我修复机制。现在,在某种程度上,类似的技术正在应用于逻辑器件。“在制造设计中,我们正在将 BiST 扩展到自我修复,就像我们对记忆所做的那样,然后是其他块。现在我们正在为接口 IP、重新配置、校准、流式传输等进行现场改进技术,”Synopsys 首席架构师兼研究员 Yervant Zorian 说。“但将工具相互链接是我们在 LCM 中所做的较新的事情,因为有了传感器监视器,芯片内部的修复系统可以一直延伸到云端的分析。因此,我们不会将分析与片上资源分开。我们正在将它们相互连接和关联,并进行优化。”
结论
系统性缺陷在最近的工艺节点中明显占主导地位,推动了对涉及空间模式识别、实时报告和缺陷识别以及工具问题自动建议的更复杂良率管理程序的需求。机器学习和数据分析程序正在帮助加快新节点和生产过程中产量上升的根本原因分析。
审核编辑:郭婷
-
芯片
+关注
关注
455文章
50771浏览量
423396 -
NAND
+关注
关注
16文章
1681浏览量
136148 -
晶体管
+关注
关注
77文章
9687浏览量
138130
原文标题:【半导光电】系统性良率,成为先进工艺芯片制造主要问题
文章出处:【微信号:今日光电,微信公众号:今日光电】欢迎添加关注!文章转载请注明出处。
发布评论请先 登录
相关推荐
【「大话芯片制造」阅读体验】+内容概述,适读人群
大话芯片制造之读后感超纯水制造
【「大话芯片制造」阅读体验】+芯片制造过程工艺面面观
台积电2nm芯片试产良率达60%以上,有望明年量产
晶圆制造良率限制因素简述(2)
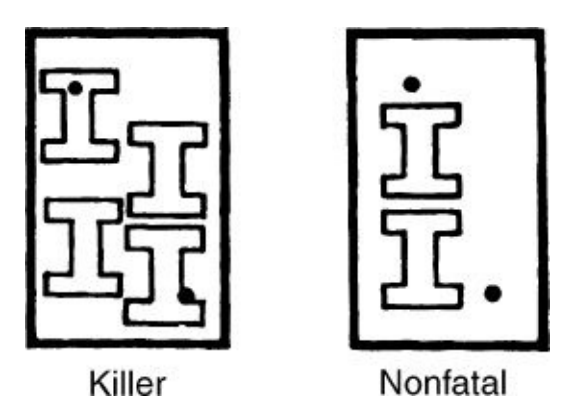
广立微INF-AI助力格科微产品良率提升
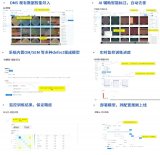
半导体工艺之生产力和工艺良率
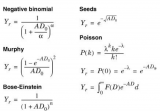
三星3nm芯片良率低迷,量产前景不明
三星3纳米良率不足60%
良品学习在高良率制造业中缺陷检测的应用
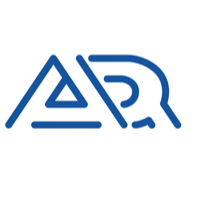
评论