数字成像技术的最新发展动态
该技术研发进展缓慢、孵化期较长,但最终可加速提高批量生产,改善其验收。
有人还认为,除了微通孔技术的发展之外,数字成像技术可能是在可接受的良率范围内实现高密度互连的最具创新性的技术。
值得一提的是,“直接成像”可能比“激光直接成像(laser direct imaging,简称LDI)”更适合指代这一技术,因为LDI虽然开创了成像技术,但它只是数字成像的方法之一。
设备和光致抗蚀剂供应商已详细介绍了形成电路的数字化方法所具备的优势。因为省去了制造和调节底片的过程,所以数字化方法具有交付时间更短的优势。因此,不需要额外成本就能定制小批量生产,如在产品上添加日期和批号等信息。激光光束的焦点在成像时会达到不同的深度,所以可以在共面性较差的表面上成像精细走线。可能最大的优势是缩放成像的能力,也就是可以调节每次曝光范围的尺寸,以最适合多层结构底层图形上的参考点。但早期的数字成像系统存在大量缺陷,例如Orbotech的DP100只能使用有限辐射功率的氩离子激光器,不仅功耗大,对冷却操作的要求也很高。
多年来,LDI都被作为数字成像技术的同义词。初期取得商业化成功的数字工艺会用到激光技术,而近期的工艺会用到发光二极管(light emitting diode,简称LED)等非激光光源,这类光源功耗低、持久性强且光源输出功率更高(图1)。
图1:新一代数字直接成像技术(digital direct imaging,简称DDI)使用不同光源和常见的TI DMD微机电系统(micro-electrical-mechanical system,简称MEMS)微镜来引导强烈的紫外线
各种各样的水银灯也利用了不只一种波长。有些公司还使用喷墨技术构建成像图形,例如标识打印文字、阻焊油墨或抗蚀油墨。这些技术都是逐像素地形成图形,而且是用数字“开/关键”来生成图形。开关可以充当光调制器(与激光直接成像技术中的一样)或液晶聚合物电池(liquid crystal polymer,简称LCP)阵列,可以用电脉冲将其变为半透明或不透明。开关可以是芯片上的微镜,例如 Texas Instruments生产的Digital Micromirror Device (DMD),利用电脉冲对微镜进行寻址,使微镜倾斜,将光导向基板或远离基板(图2)。
图2:使用同样的方式将UV光通过DLP/DMD直接射向面板表面
下文总结了数字成像系统的研发和商业化进程。
在2013年的productronica展会上,法国成像系统供应商Altix-Automata-Tech首次推出了ADIX系统。该系统基于先进的大功率LED辐射源(advanced high-power LED radiation source,简称ALDS)、两个多波长UV-LED和DMD,适用于刚性和挠性基板,并且有自动处理功能选项。早期使用DMD的系统包括:
ORC的DI-Impact(之前由Pentax生产)
Hitachi的DE成像设备DE-H、DE-S和DE-F系列
德国MIVA Technologies公司生产的Miva 2600X直接成像设备
Maskless Lithography公司研发的基于DMD的系统(美国),其中用到了水银电弧光源或LED
Aiscent Technologies(加拿大)
韩国公司Ajuhitek凭借EP数字成像系列设备打入市场,设备使用了波长为405 nm的激光二极管辐射源。
据我所知, HAN’s Laser Technology Group是中国知名的供应直接成像设备的制造商。
日本的直接成像设备供应商ADTEC、DNS、ORC和Via Mechanics还在不断推出改进系统。
瑞士供应商PrintProcess公司推出了Apollon DI-F10(前置式手动单面操作)和Apollon-DI-A11 (内部翻转自动化双面操作)。根据光致抗蚀剂类型的不同,线宽分辨率为30~20μm。上面有1~7个成像头(也可以选择8个)。光源选用UV-LED,多波长的长度范围在360~420 nm之间。这些设备可自动完成装载卸载,不仅能自动完成成像缩放,还能成功分辨1mil[25.4μm]的特征。
德国的KLEO Halbleitertechnik GmbH公司从2009年开始供应直接成像设备,生产厂分别在德国和瑞士。KLEO-LDI-System CB20HV-Twinstage使用了波长为405nm的激光二极管。亚洲地区的工厂主要使用405nm的辐射源。Hitachi、DuPont、Atotech、Eternal、Kolon和Elga Europe均可以提供适合在405 nm波长的光源下进行曝光的光致抗蚀剂(干膜和液态)。2015年,Manz公司收购了KELO。
德国Limata公司生产的UV-P100 UV-LED直接成像设备主要针对样品和快捷生产。该设备可使用传统干膜和阻焊油墨。光源使用寿命大于10000小时。能够加工的最大面板尺寸是650 mm × 540 mm,形成特征的分辨率可达50微米。该设备具备自动装载卸载功能,并通过摄像头和校准目标孔完成边与边校准。
Orbotech已经安装了1000多台直接成像设备。他们生产的Nuvogo DI System专门用于高阶HDI/挠性和刚挠结合应用的批量生产。Nuvogo 800几乎与早期所有抗蚀剂类型都兼容,可生成18μm的线宽和线距。Nuvogo利用了Orbotech久负盛名的大镜面扫描技术(large-scan-optics-technology,简称LSO)。
MultiWave Laser Technology使用了多波长高强度激光光束,因此,可以使用具有标准光敏水平但成本更低的抗蚀剂提高产量(每条生产线每天最多可以生产7000块面板),且具有最佳走线结构。
Manz是一家生产湿制程工艺化学设备供应商,该公司已经凭借其SpeedLight 2D系统打入了数字成像技术领域。该系统有2个操作台,在成像第1块面板的同时可以校准第2块面板。成像设备含有288个激光二极管光束,由9个多边形镜像模块调节形成。
德国激光直接成像系统供应商Limata GmbH公司在先进的UV-R 系列中应用了成熟的UV-P模型,应用于小批量PCB生产和光化学加工流程。该系统可以使用最新的多波长UV二极管激光器,具有很长的运行寿命。这两个模型都包含1~8个激光头,线宽线距分辨率可达25μm。预校准模块最多可以处理64个校准目标,可实现近乎完美的校准。使用3种波长用最大的光源强度完成阻焊层成像,以适应敏感度较低的光致抗蚀剂。该设备可以添加机器人装卸台来提高产量并优化与其他加工设备的接口。
加拿大供应商Aiscent Technology研发数字成像技术已经15年之久。他们生产的系统使用了基于DMDR的光刻技术和专有的大功率激光器。现有的双面模型可用于生产PCB、高分辨率光掩模和数字屏幕成像,以及其他定制工业用途。
知名的机械与激光钻孔设备供应商Schmoll Maschinen推出了数字直接成像(digital direct imaging,简称DDI)系统,可用于内层、外层和阻焊层成像的样品加工。该系统以半导体激光二极管和大型(宽)光学部件为基础,设备包含2~8个二极管激光器。Schmoll公司还推出了微镜数字成像(micromirror digital imaging,简称MDI)系统。花岗岩工作平台上安装了独特的“轻型发动机”成像头,形成了可精密定位的系统。这项新技术可以用200多万个高分辨率微镜片将紫外线光形成的图像转移到电路基板上。这些系统有单工作台单元或串联式工作台单元,最大加工尺寸为1371 x 914 mm单块面板的XXL模型。这些单元使用了大功率LED,以及365~405 nm多波长的DMDR。
瑞士公司First EIE SA生产光电绘图设备和喷墨打印机,其生产的直接成像设备EDI500非常适合小批量快板生产。其光源技术基于TI的DMDR设备,配备有高阶UV镜头和超高压水银弧光灯。通过外置的CCD摄像头或手动销钉对准完成面板的校准。最大面板尺寸是620 x 690 mm,但新款EDI700可以加工更大的面板。
Visitech是一家专为直接成像设备提供光调制器(光学子系统)的挪威公司。Luxbeam Rapid System(LRS)是以TI的DLPR(微镜)和多波长LED光源为基础,射出的波长范围在350~440 nm之间。该系统可以提供能够达到不同分辨率的5个模块,包括LLS2500 (2.5μm t/s)、 LLS04 (4μmt/s)、 LLS06 (6μmt/s)以及2个达30μmt/s的模块。光多路传输技术可以实现更精细的分辨率。
前后对准
理想的是能达到前后对准。实现这一目标的对准方法有很多,有些方法不需要在曝光前在面板上钻取靶位孔(“无孔对准”)。图3展示了4种使用机械钻孔和激光钻孔进行对准的方法。“无孔对准”利用了光致抗蚀剂可以“打印出图像”的特性,在曝光过程中,抗蚀剂的颜色会发生改变,使尚未显现的聚合结构显示了出来。不论使用哪种对准方法,都需要将面板放置在位于曝光顶部的操作台上。在真空环境下,操作台内放置的标识物开始在面板底部成像靶点或孔的位置。CCD摄像头随后将送入的面板和操作台对准,反转面板后,在面板顶部再重复一次同样的操作。将面板翻转后,CCD摄像头在底部定位靶点或孔标记,然后进行校准和成像。
图3:可以应用多种对准方法,图中展示了其中4种方法
另一种方法如图4所示。首先,校准DLP塔的记录头(步骤a),使用对准相机和对准类型(步骤b)检测是否需要校正位置,然后在快速运转的计算机上针对缩放、旋转、定位和放大操作进行补偿,从而保证成像可靠精确。自动聚焦功能会一直跟踪PCB并针对翘曲和线路板厚度做出补偿。
图4:在PCB上设置校准目标的方式有很大差异,本图展示了其中一种方式(来源:Dainippon Screen Mfg.Co.Ltd.)
总结
在应用DI技术生产新一代UHDI时,图5所示是在较大的面板(510 mm x 515 mm)上形成3 μm线宽/线距。本图展示的CCL/ABF基板使用了厚度为10 μm的干膜抗蚀剂,形成的走线纵横比刚刚超过1∶3。使用焦点曝光矩阵(focus exposure matrix,简称FEM)可以确定材料最佳用量和最佳焦距。最佳用量用于证实分辨率。
由图可知,当DOF是60μm时,CD值从-10 ~ -70 μm的偏离小于10%。使用FEM数据绘制出泊松分布图(图5a),其中X轴是焦距(μm),Y轴是CD(μm)。该图显示了60 μm的DOF。图5b展示了在放大倍数较低的情况下,3 μm、3.5 μm和4 μm密集线宽/线距阵列。3 μm走线的高分辨率横截面图(图5c)展示出了中线的宽高比为3.181∶9.873(高度为抗蚀剂厚度)。
图5:a)FEM数据生成的泊松分布显示60 μm DOF的偏离范围小于10%;b)3 μm、3.5 μm和4 μm的密集线宽/线距阵列的低分辨率图像;c)铜基板上10 μm厚干膜抗蚀剂上3 μm走线的横截面图像;在横截面图像中,走线的临界尺寸是3.181 μm,抗蚀剂厚度为9.873 μm。
审核编辑:汤梓红
-
led
+关注
关注
242文章
23235浏览量
660474 -
成像技术
+关注
关注
4文章
289浏览量
31452 -
数字成像
+关注
关注
0文章
15浏览量
8120
原文标题:你可能不了解的:直接成像技术发展史
文章出处:【微信号:actSMTC,微信公众号:actSMTC】欢迎添加关注!文章转载请注明出处。
发布评论请先 登录
相关推荐
恒压变压器的发展史
RFID发展史
美国力科示波器发展史
5G技术的发展与应用你了解多少
5G的发展史
通信技术发展史
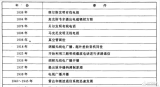
评论