卡扣连接器(也称为紧固件或机构)用于将一个部件直接连接到另一个部件,在空间受限的环境中,它们通常用于组装复杂的注塑成型零件。这种连接结构由于连接方便、加工容易、成本低,被广泛应用于电机外壳连接键的设计中。
众所周知,受挤压机构的弯曲特性会严重影响电机的性能。在研究这些特性时,直接使用目标样机进行验证是很耗费资源的,可能会对样机造成损坏并浪费大量资金。但是,随着计算机技术的发展,这些问题都可以通过 CAE 模拟的方法来解决[1]。有很多关于卡扣的设计研究,但是大部分的研究仍是针对传统卡扣,并且多数集中在塑料卡扣的设计中。一些研究表明,传统卡扣设计的工作原理独立于制造过程,并提出了增材制造卡扣设计指南,很多先前的方法需要适应新制造技术的制造方式[2-3]。
强度、约束、兼容性和稳健性已被确定为卡扣设计的关键要求,前三个在设计阶段是必不可少的。通过遵循一般设计指南,可以较容易地满足这些要求。稳定性高是指尺寸变化的容忍度。坚固性是不可预测的,尺寸会根据制造和材料特性的差异而变化。当我们模拟模型时,假设材料是各向同性的,但材料很难完全各向同性。最关键的尺寸变化是刀具和粘合面之间的匹配角度。过盈量决定了配合力和预紧力的质量。由于卡扣连接器的行为类似于悬臂,因此配合力会随着干扰的增加而增加。过少的干涉会导致装配松动,过多的干涉会导致组装困难或可能导致零件和连接器的永久变形,从而导致废品率高而影响效益。
与恒力机构一样,卡扣连接器是一种封闭结构,当受到一定的输入位移时,它会提供一定范围的恒定反作用力。本研究的卡扣连接器是用于连接电机金属部件,卡扣连接器的质量可以很大程度影响电机的生产以及质量。
大多数的研究主要集中在塑料材料上,很少有关于电机外壳金属卡扣的研究。本文研究了刀具的形状如何影响卡扣材料的变形,评估卡扣压型的整个过程以获得刀具的反作用力,从而调整模具进行冲压成型。
1 材料特性及典型的封装结构
1.1 材料特性
对于塑性材料,其变形过程有四个阶段:弹性阶段(O-a)、屈服阶段(a-d)、应变硬化阶段(d-e)和颈缩阶段(e-f),分别表示在图 1 中[14]。从O到a的阶段定义为载荷随应变线性增加,当载荷达到某个最大值a后,屈服阶段开始,应力增加很小,但应变增加很大。经过b后,应力减小,应变增大,直至稳定阶段,在应变增大过程中应力保持相对稳定,略有波动。试样一部分的直径开始减小,这种现象称为颈缩(e-f)。颈缩开始后,稍低的载荷足以使试样进一步伸长,直到它最终破裂。这意味着无论负载是否存在,材料都会发生永久变形。
图1 材料的拉伸曲线
为预测不同尺寸结构的性能,采用有限元分析方法评估性能。本文使用ANSYS Workbench 用于压缩模拟,而有些论文使用 Abaqus 进行压缩模拟,虽然软件不同,但都是基于有限元方法对模型进行离散化分析[15-17]。材料的力学性能如表1所示。多线性各向同性硬化参数如表2所示,本文使用表2数据进行分析。
表1 材料力学性能
表2 镀锌钢板多线性各向同性硬化模型
1.2 典型的封装结构
图 2 显示了典型的电机卡扣结构。四位槽对称分布在一个空心圆柱体上,相邻槽之间间隔90°。R1和R2分别是内半径和外半径,H1和h1分别是圆柱和孔的高度,b1是刀具的宽度。L1为凹槽宽度,L2为最大夹钳宽度,L3为刀具宽度,L4为夹钳高度,L5为最大凹槽宽度。α是内刀角,β是外刀角。四个孔对称分布在一个空心圆柱体上,相邻两个孔之间的间距为110°。
图2 电机外壳结构示意图
在刀具压缩卡扣结构过程中,压缩位移S可以表示:
(1)
式中:V0是压缩开始时压缩工具的速度;Fc是压缩过程中的压缩力;m是工具的质量;t是压缩时间。根据图1的材料特性,初始阶段不可避免地存在一个载荷阶段a-c,其中受力大于稳定阶段。本研究认为,当稳定阶段的持续时间占压缩持续时间的 70% 以上时,阶段(a-c)可以忽略不计[18]。在这个假设下,压缩力被认为是恒定的,并且接近于稳定阶段的平均力。然后,假设压缩结束时,速度下降到0,式(1)可简化:
(2)
式中:是压缩过程中的平均力;S是总位移;t是压缩过程的整个时间。通过推导可以得出,在压缩过程中,可以按照位移约束的方式进行载荷加载在ANSYS软件中。
1.3 刀具角度的不同参数
刀具的稳定位移是在压缩过程中表现出来的。在压缩过程中,变形主要发生在卡扣锁紧部分处,如图 3 所示。
图3 卡扣锁紧部分凸起筋条
压缩过程中铁壳的变形主要受刀具角度的影响。刀具角度α会影响图3中锁紧部分的变形,影响电机外壳的预紧力。本研究确定了锁紧部分和刀具的尺寸。本研究介绍了95°、100°、105°这三个不同的角度来寻找最合适的α角度,压缩过程中的最大压缩为1 mm,确保刀具能够刚好碰到L4的底部并且不会破坏电机外壳。整个过程耗时为 1 s,包含20 个子步。
枚举法通过枚举问题的所有可能答案,找到满足给定条件的合理解。它通常计算量大、效率低,但是,当用于小规模问题时,它无需复杂的计算和推导就能更快地达到解。本研究引入ANSYS Workbench 2021R1,比较不同刀具角度的性能。在 Mechanical Workbench 中,通过 User Defined Result 获取变形后的节点坐标:LOC_DEFX、LOC_DEFY、LOC_DEFZ。通过坐标计算,得到空间中两个端点(图3中红色星状标识)的距离。
刀具角度列于表3,唯一不同的是角度α,三个仿真模型的其他参数均相同。L1取值为5.2 mm,卡扣锁紧部位的宽度为2 mm。使用式(3)计算表4中的数据,得到卡扣锁紧后两个端点的空间距离,从而对比差异。
两个节点的空间距离公式:
(3)
通过对比如表4所示的结果,可以得到在刀具作用的过程中,卡扣向内变形,锁紧端盖,α=100°时变形后距离最小,变形效果最好。
表3 不同的刀具角度的模型参数
表4 不同刀具角度对应的变形值
1.4 网格无关性验证
过多的网格会导致计算量的增加,过少的网格也会导致计算精度的降低,本文对电机模型进行网格无关性验证,以保证在满足精度的前提下尽量缩小计算量。测试在DELL 工作站Precision 5820 Tower上测试,处理器Intel(R) Xeon(R) W-2275 CPU @ 3.30 GHz并带有256 GB内存,测试软件平台为Windows 10 专业工作站版,版本号20H2,测试仿真软件平台为ANSYS Workbench 2021R1 带有8核HPC, 最大算力可以调用12个CPU物理内核,所有软件皆在正版授权软件中进行测试。测试模型的刀具角度为95°,分别进行三种单元密度网格无关性验证[19-22],网格划分方法为全局网格,采用1.5 mm网格尺寸,在卡扣部分采用局部加密方式进行加密,加密网格尺寸及验证结果如表5所示。根据表5所示的数据,选择网格尺寸为0.5 mm时的单元尺寸进行计算。
表5 网格无关性验证
1.5 边界条件
为了获得整个压缩过程中壳体的变形情况,首先通过建模将刀具与电机壳体位置对应,刀具内侧与壳体卡扣凸起部分相接触,由于有润滑的存在,所以刀具与壳体部分的接触设置为无摩擦接触。在实际加工过程中,壳体固定在操作台上,将壳体下表面进行约束处理,约束6个方向自由度。刀具在下压过程中,电机端盖是盖在电机壳体上的,并且没有添加其他约束,端盖只与电机卡扣凹槽部分进行接触,在电机壳体周向移动,径向无法移动,设置好的边界条件如图4所示。端盖释放Z方向的自由度,约束X、Y两个方向的平动自由度,刀具运动方向如图5所示。
图4 电机壳体端盖约束
图5 刀具运动方向
1.6 不同刀具角度导致的壳体变形情况
刀具在下压过程中共耗时1 s,分20个载荷步进行施加,在进行锁紧工艺时,整体应力开始变大,材料产生塑性变形,图6~图14列出了100°刀具角度情况下壳体的塑性变形情况。本文的分析在满足壳体平面度要求以及总体变形要求的情况下,尽可能地锁紧端盖,以免端盖出现松动。通过仿真分析可以直观地看出,卡扣卡口部分已经有明显的变形,但是变形只在卡扣锁紧部位,并未传递到电机壳体的其他部位,这正是加工生产所要的效果,符合预期的设计。这样既可以保证卡扣卡位的精准锁紧,又不会影响电机壳体的其他部位的变形,从而影响电机的性能。
图6 100°刀具加工壳体变形情况
图7 100°刀具加工壳体局部变形情况
图8 100°刀具加工壳体端盖变形情况
图9 95°刀具加工壳体变形情况
图10 95°刀具加工壳体局部变形情况
图11 95°刀具加工壳体端盖变形情况
图12 105°刀具加工壳体变形情况
图13 105°刀具加工壳体局部变形情况
图14 105°刀具加工壳体端盖变形情况
1.7 不同刀具角度压缩卡扣结构的压力
通过软件计算,可以得到刀具在下压卡扣的过程中需要多大的下压力,才可以将卡扣锁紧,用于指导实际加工生产中,相关工艺的下压力完成装配。本文对刀具的三个角度的模型进行分析,并得出下压力的精确值,如表6所示。不同刀具角度的下压力是不同的,当刀具角度为105°时,下压力最大。较大的下压力并不是生产中最理想的状态,有可能导致壳体的其他部位变形。而较小的下压力会有压不到位的风险。100°的刀具角度是三种刀具中最优的。
表6 不同刀具角度的下压力
1.8 锁紧结构尺寸的影响
图2中,L1的尺寸与端盖配合,无法进行更改;L2的尺寸为加工后的凹槽,可以通过更改L2的尺寸来调整锁紧结构的变形,从而影响锁紧的效果。同时,调整L2的尺寸,也会影响刀具的压力,较大的压力会对整个结构的变形产生不稳定的作用,压力要尽可能控制在一个合理的范围内。在刀具角度为100°的情况下,L2的初始尺寸为9.2 mm,此时,L1的尺寸为5.2 mm,单个锁紧结构的宽度T为2 mm,宽度的计算公式如下:
T=(L2-L1)/2
(4)
不同的锁紧宽度对压力的影响如表7所示。通过整理表8数据,并根据式(4)计算得到在三种宽度分别为1.7 mm,2 mm,2.3 mm的情况下,相同的刀具角度,不同的宽度值T,卡扣锁紧部位表现的性质不同,当宽度为2 mm时,锁紧效果最好。
表7 不同的宽度对压力的影响
表8 刀具角度100°对应的变形值
2 实验验证
根据仿真结果,确定刀具角度为100°,L2为9.2 mm时的壳体在所有模型中是最优的,此时卡扣锁紧部分的宽度T为2 mm。下面对此参数下的模型制作样机,来验证仿真的精确性。
实验通过两个测试来确定仿真方案是否可行,首先是压力测试,而后是端盖的平面度测试。
2.1 刀具锁紧卡扣实验
卡扣锁紧实验主要进行压力的评估,通过限定力学试验机的位移进行,通过传感器测量压入过程中的压力大小。实验中按照仿真数据,加工了五个样件,每个样件随机编号,将样件放到夹具上,放稳并确定电机壳体没有翘曲。
实验后的数据如图17所示。从图17中可以得出,实验过程中,材料没有表现出非线性变形,壳体在压缩过程中表现出较为一致的线性,而仿真数据表现出一定的非线性。刀具位移为1 mm时的仿真和实验数据结果如表9所示,实验的压力值分布范围为3 215~4 783 N,实验分布范围较大。用相同位移的结果进行对比显然产生较大的误差。对实验数据进行整理,将初始的非线性段删除,取线性较好的一段数据进行拟合,在Excel中可以得到拟合曲线的线性公式,并得出斜率,就是实际位移1 mm对应的近似压力值。取斜率的平均值,通过数据分析可以得出,实际壳体下压1 mm,需要5 964.92 N的压力。仿真与实验的误差为8.5%。
图17 实验数据与仿真数据
表9 实验数据和仿真数据压力对比
2.2 平面度测量
平面度测量用于检测电机壳体在进行端盖锁紧的过程中,是否发生了其他部位的变形,导致壳体扭曲或者端盖轴心偏心,影响电机质量。在实验样本中,取三个样本作为测量对象,通过对电机壳体进行四个点的平面度测量,平面度测量位置如图18,测试结果表10、表11所示。分析结果表明,锁紧卡扣前后的平面度差值在0.02~0.10 mm之间。
图18 壳体平面度测量位置
表10 实验前后壳体的平面度测量
表11 实验前后的壳体变形情况
2.3 端盖推出力测量
在压紧端盖后,为了保证端盖的结构稳定,对端盖进行推出力测试。通过推力计穿过电机壳体推出端盖,从而测试卡扣结构的强度。固定电机壳体,而后沿着壳体轴向施加载荷,端盖和卡扣失效瞬间会伴随“嘭”的一声声响,得到数据如表12所示。根据表12数据,可以直观地看出,端盖在锁紧后较为坚固。
表12 端盖推出力测量
3 结 语
本文建立电机壳体锁紧卡扣的仿真模型,通过ANSYS Workbench有限元软件分析,确定了合适的刀具角度以及卡扣部分结构的尺寸,阐明了电机壳体加工过程中的重要尺寸及其影响,进行了网格无关性验证,确定合适的网格尺寸以及数量,用于快速计算求解结果,以适应工程需要。
研究结果发现:
1)电机壳体封装端盖的过程中,刀具的角度以及卡扣的尺寸对锁紧效果影响较大,材料在受到刀具压缩后,开始呈现出屈服硬化现象,并沿着设计好的方向进行塑性变形。变形过程中,变形只出现在卡扣部位,未传到电机壳体的其他部位,保证了加工的精确性。
2)虽然材料参数和实际使用镀锌钢板材料一致,但是在实际的仿真和实验中,二者也表现出了不同的性质。仿真中,材料表现出较为明显的非线性性质,并且曲线弧度较为平滑,与理想的材料力学拉伸实验曲线较为接近;实验中,材料随着刀具的下落位移增加,表现出接近线性关系的性质。且随着位移的增大,仿真的压力趋近于平缓,而实验的压力趋势仍然呈现原有线性性质。二者在相同位移的情况下,实验与仿真误差较大,对实验数据进行线性拟合后,误差在可接受范围内。由于实验中很难确定凹槽部分的具体尺寸并保证一致性,在压缩的过程中也存在其他因素干扰,无法达到仿真的理想情况。并且刀具的初始位置直接影响了实验结果,按照仿真曲线所表现出来的趋势,仿真1 mm的位移情况对应实验的位移会在1.2 mm~1.6 mm位移之间。
3)根据仿真数据进行样件制作并实验,仿真中,壳体除卡扣部分外皆无变形情况;实际的实验中,在对壳体进行端面平面度测量时,检测的三个壳体均有少量变形,变形量非常小,最大只有0.1 mm,仿真和实验有一点差异,差异在可接受范围内。端盖锁紧后的强度较高,满足生产要求。
审核编辑:郭婷
-
连接器
+关注
关注
98文章
14463浏览量
136403 -
电机
+关注
关注
142文章
8990浏览量
145318
原文标题:电机壳体封装工艺研究
文章出处:【微信号:EDC电驱未来,微信公众号:EDC电驱未来】欢迎添加关注!文章转载请注明出处。
发布评论请先 登录
相关推荐
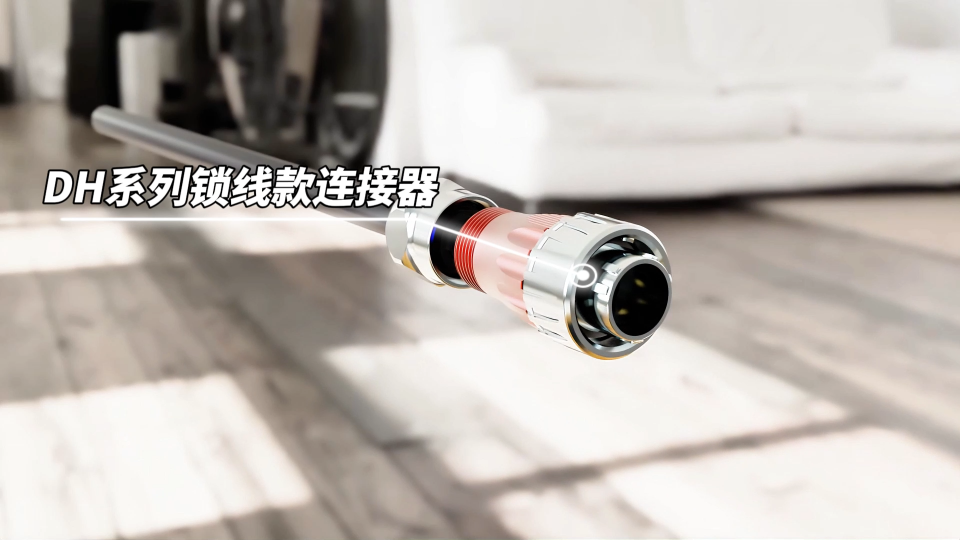
I-PEX连接器,内置锁扣功能的新款射频连接器-行业中的创举
TE Connectivity 三重锁扣式电源连接器
为您介绍:三重锁扣式电源连接器
重载连接器能广泛应用于需要进行电气和信号连接的设备
卡扣设计的排针和母连接器更适用于汽车测试设备
连接器外壳的作用是什么
康瑞连接器--KR2014 单排-带扣-线对板连接器
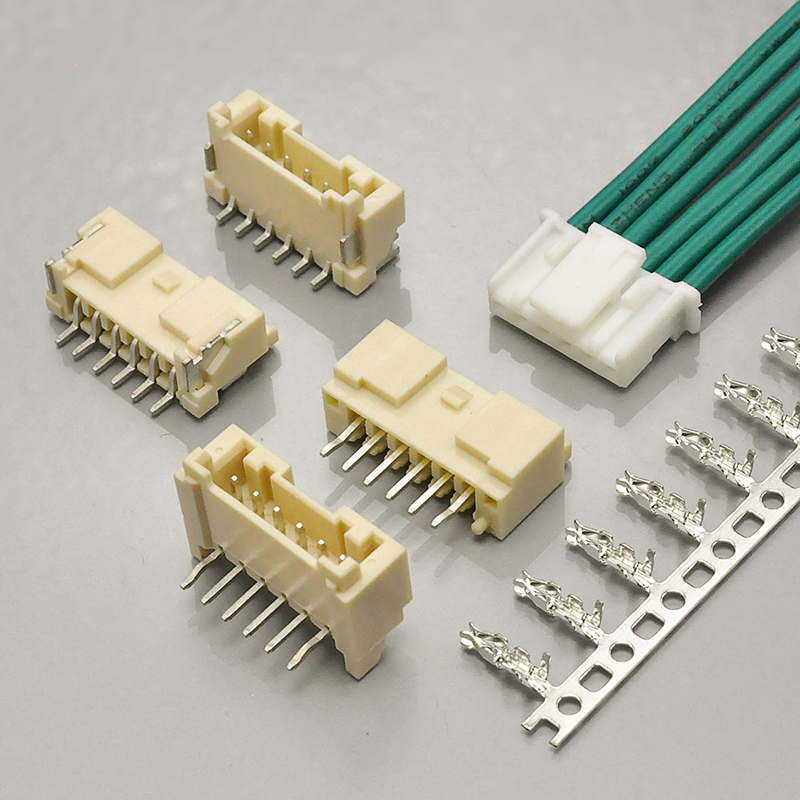
评论