工业4.0正在使工业自动化技术更接近工厂车间的边缘。在本设计方案中,我们展示了集成DC-DC转换器的MAX22513浪涌保护IO-Link收发器如何降低大电流工业传感器的功耗和元件面积。
每一场名副其实的革命都应该得到同样值得的 座右铭。“自由,平等,博爱”被法国人选中。 第四次工业革命(谢天谢地没有流血事件 或冲突)可能会对 人民的生命比任何政治革命都要多。可以说 “智力,适应性,功效”可能使合适的 工业 4.0 的口号,因为这场革命是 经常提到。
不管你是否认为这是一个有价值的口号,它不可能是 对这些条款中的每一个都适用于 IO-Link 技术,是该行业的先锋 革命,正在促进更智能、更具适应性和 工厂车间的工业传感器效率越来越高。为 工业系统设计师,无情的挑战是 确保这种提高的性能不会在 增加功率或散热的费用,以及 因此增加了传感器尺寸。在这个设计解决方案中,我们 查看设计大电流时的功率约束, 小型外壳 IO-Link 传感器,可在恶劣的无风扇环境中运行 工业环境。在考虑妥协之后 遇到现有解决方案,我们提出了一个新的 IO-Link 收发器 IC 克服了这些限制,同时 同时提高设计灵活性和改进 传感器坚固性。®
什么是 IO-Link?
IO-Link 是一种标准化技术 (IEC 61131-9),用于调节 工业系统中的传感器和执行器如何与 一个控制器。它是点对点通信链路 标准化连接器、电缆和协议。The IO-Link 系统设计用于在行业标准的3线内工作 传感器和执行器基础设施,由“IO-Link”组成 主设备“和”IO-Link 设备“产品(图 2)。
图2.IO-Link 主/设备接口
引脚 1 (L+, 24V) 和 3 (L-, 0V) 用于电源,而引脚 4 (C/Q) 根据需要传输通信或交换信息。 引脚 2 可以保持未连接 (NC),也可以配置为 用作数字输入 (DI) 或数字输出 (DO) 以提供 C/Q引脚用于传输时的开关信息 传入/传出 IO-Link 传感器的数据。IO-Link 标准规定 通信必须在 20 米以内且未屏蔽 使用工业通用标准连接器的电缆 系统。主设备与从设备之间的通信是 具有 3 种传输速率的半双工:COM1 4800 波特, COM2 38.4k 波特,COM3 230.4k 波特。IO-Link 设备 仅支持一种数据速率,而 IO-Link 主站必须 支持所有三种数据速率。
中联传感器设计
大多数工业传感器使用M8或更大的M12(图) 3)电缆连接器。使用的连接器类型将影响 传感器的外壳尺寸以及因此的热量 可以消散。在下面的示例中,我们将设计 总功耗不会 如果使用 M8 连接器,则超过 400mW,如果使用 使用 M12 连接器的传感器。
除换能器(压力/温度/接近度)外, IO-Link 工业传感器通常还包括一个模拟传感器 前端 (AFE)、微控制器、状态 LED,可能还有 驱动执行器响应传感器的输出级 读数。工业传感器使用24VDC信号电压,但 在恶劣的工厂环境中,这一比例可能高出 50%。 虽然这些电压电平可以安全地用于为 输出驱动器级、AFE、LED 和微控制器需要 工作电压低得多(3V至5V)。许多 IO 链路 收发器以线性稳压方式提供这些电压电平 输出。但是,使用它们的决定可能会产生负面影响 对传感器整体功耗的影响(以及 因此,散热)。如果 低效板载LDO电路用于提供电流 对于这些输出。例如,考虑以下功率 仅消耗15mA电流的小型传感器的预算 通过 LDO,由(典型值)30V 直流电源轨供电,如图所示 在图 4 中。
图4.典型 IO 链路传感器的功率预算 (mW)
由于LDO内部的高损耗,这种相对较低的功率 传感器已超过~400mW功率预算 在典型的 M8 连接传感器中耗散,因此, 需要更大的 M12 连接外壳。图的 还表明,传感器仅消耗30mA的电流将 耗散900mW,甚至超过了M12的目标数字 连接器传感器。
常规解决方案
为了降低整体功耗(和散热), 最常见的解决方案是使用外部 DC-DC 降压 转换器,为收发器上的线性稳压器供电。为 例如,DC-DC降压转换器为30mA传感器供电 采用 3V 输出电压时功耗仅为 90mW。若 转换器的效率为 90%(即仅 9mW 功率损耗), 总功耗仅为 90 + 9 = 99mW。清楚 功耗降低约 9 倍 与使用 LDO (900mW) 相比。包括 输出级消耗的功率(100mW),总功率 功率降低为 1000mW/199mW,或大约 系数为 5,如图 5 所示。
图5.使用降压转换器降低功耗与LDO的比较
显然,传感器的整体功耗 (~200mW)现在远低于传感器的目标数字 使用任一类型的连接器。但是,这种功率降低是 仅以牺牲额外的外部电路(即 DC-DC转换器和电感器等笨重的分立器件, 二极管和电容器),这增加了 传感器。典型的 IO-Link 收发器解决方案需要 如图6所示,组件面积为16.5mm2,其中 DC-DC 转换器比 IO-Link 消耗更多的面积 收发器本身。为了防止电压浪涌,一些 收发器可能还需要外部TVS二极管, 进一步增加元件(和电路板)面积。
图6.典型的 IO 链路收发器解决方案
集成双通道收发器
图7所示的IO-Link收发器IC具有多个 与传统方法相比的优势。 首先,一个反极性保护降压DC-DC转换器 已完全集成到IC封装中,这意味着 不需要单独的 DC-DC 转换器 IC。这 转换器可提供高达300mA的输出电流 (用于大电流传感器应用),2.5V至12V 可编程输出电压。其次,与大多数其他不同 IO-Link收发器,IC还包括第二个(双) IO-Link 通道,可用于 DI/DO 传感器切换 当数据在 C/Q 通道上传输时。尽管 包含这些额外功能,整体封装尺寸 在 WLP 中仅为 2.1 × 4.1 = 8.6mm2。这代表几乎 组件面积减少 50%。此外,坚固的传感器 在恶劣工业环境中的性能由 集成浪涌保护(高达 1kV/500O)电路 无需外部TVS二极管。
图7.MAX22513双通道IO-Link收发器
结论
在此设计解决方案中,我们回顾了电源约束 在为恶劣的无风扇工业设计 IO-Link 传感器时 环境。我们已经证明,使用 LDO 供电 传感器电流并不总是高电流的可行选择 传感器,因为它大大增加了功耗。直到现在, 减少散热的唯一解决方案是 使用单独的DC-DC降压转换器IC,但这来了 需要注意的是,要增加整体传感器尺寸。然而 MAX22513浪涌保护双驱动器IO-Link器件 收发器现在为大电流提供完全集成的替代方案 传感器,提供更大的灵活性,结合 强大的性能,更小的外形。
审核编辑:郭婷
-
微控制器
+关注
关注
48文章
7708浏览量
152567 -
传感器
+关注
关注
2554文章
51700浏览量
758544 -
收发器
+关注
关注
10文章
3524浏览量
106444 -
转换器
+关注
关注
27文章
8778浏览量
148716
发布评论请先 登录
相关推荐
IO-Link传感器发送器快速原型设计平台包括BOM及层图
24位RTD前端的完整IO-Link传感器参考设计
用于IO-Link v1.1的LT3669-2温度传感器
io-link传感器变送器参考设计
IO-LINK与设备的智能连接和联网是怎么实现的
IO-Link如何满足工业传感器网络的要求
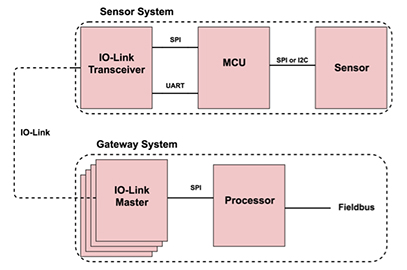
IO-Link智能传感器在各种执行器设备中的应用解析
IO-Link为应用提供完美的解决方案
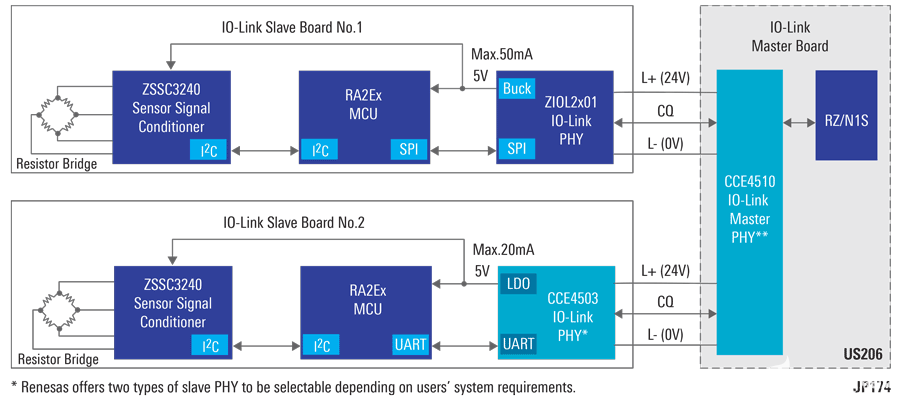
IO-Link的工作原理及组成部分
如何使我的大电流传感器IO-Link兼容?
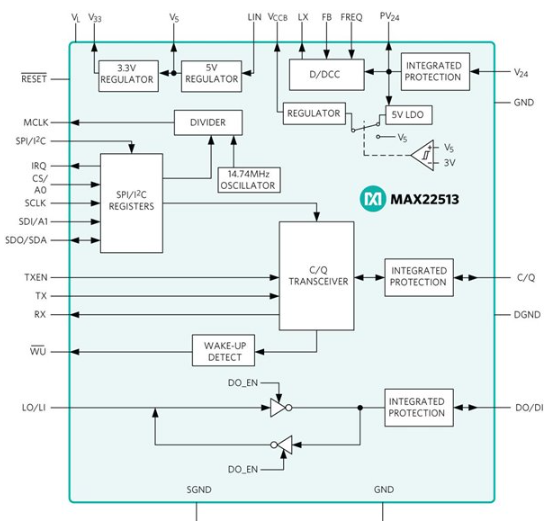
IO-Link Master/IO Hub/IO-Link传感器和执行器解决方案
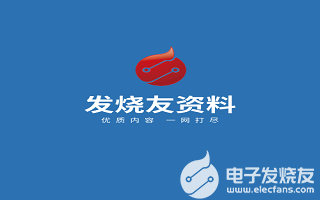
IO-Link编码器特点
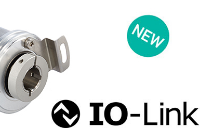
评论