由更严格的一氧化碳驱动2法规和更具环保意识的消费者, 向电动汽车迁移的步伐继续加快,随着 预计到2025年,所有售出的车辆中将有高达10%由电池供电, 相比之下,今天不到1%。1尽管成本很高 电池,顽固地保持在总成本的一半左右 的车辆。
虽然有许多因素决定了电池的成本,但一个 制造商可以在减少减排方面取得重大进展的领域 成本是在制造的最后阶段。具体来说,在电池期间 形成和测试,可占成本的20% 电动汽车的电池。
电池化成和测试是一个耗时的过程,涉及多个 充电和放电激活电池的化学成分,可以采取 最多整整两天。此必要程序使电池准备好使用时 对于确保其可靠性和质量至关重要。由于速度太慢 工艺是,这是阻碍电池制造的重大瓶颈 从实现更高的吞吐量,从而降低总体成本 生产电池。电动汽车电池制造商与 具有化成和测试系统专业知识的供应商使他们能够 增加他们的注意力,以减少这一关键所需的时间和成本 制造阶段,同时仍保持所需的精度 用于先进的电池化学成分。
更快的吞吐量等于更低的电池成本
为了降低电池成本,制造商需要采取整体措施 从利用供应商的系统级专业知识开始的方法 减少整体电池测试电路占位面积,同时增加 通道数。重要的是要注意,两者都必须同时完成 保持电池的准确性、精度、可靠性和速度 化成和测试测量,以确保安全性、性能和 满足可靠性要求。
这并不容易做到。对于前端,驱动 电池充电电路需要严格控制。更深入,电池 化成和测试需要密切监测电流和电压 在电池循环期间使用的配置文件,以防止过度充电和充电不足。 这确保了测试过程中的安全性,同时也最大限度地提高了电池电量 使用寿命长,大大降低了最终用户的总体拥有成本。
对于这些关键的电池测量,需要非常高质量的仪器 需要放大器(仪表放大器)和相关分流电阻来测量 电池充电/放电电流精度优于±0.05%, 即使在恶劣的工厂条件下。同样水平的精度适用 到用于监控整个电压的差动放大器 热工作范围。
有许多方法可以将这些组件合并到完整的 解决方案,但最大限度地提高性能和 最小化系统占用空间。这就是ADI集成背后的原因 模拟前端、电源控制和监控电路中的 单IC,AD8452。这些IC可以包括电池反转预防, 过压保护开关和智能控制,防止过充电 电池,它们可以将系统占地面积减少 50%。这间套房 功能允许电池制造商整合更多功能 进入测试系统,同时更有效地利用 工厂占地面积。此外,它们允许制造商设计系统 具有更多功能和更强大的测试程序。
反过来,高效的功率转换是另一个进一步推动的机会 系统性能。通过使用先进的交换架构, 测试系统可以通过实现双向 来最大限度地降低功耗 与电网进行能量交换。高效的功率转换也减少了 对热管理设备的需求,这可能会增加系统的 总体成本和功耗。最终结果是减少 浪费能源和制造成本。启用这些功能 需要了解系统特性,例如隔离式栅极驱动器, 支持新型碳化硅和镓的更快开关需求 氮化物功率开关技术。
与具有系统级的供应商密切合作的好处 专业知识和广泛的产品组合不仅仅是获得 更复杂的组件和构建块。它还提供电池 制造商访问系统架构的参考设计 可以更容易地采用,将上市时间缩短三到四倍 比电池制造商开发化成和测试更快 从头开始的系统。
预计全球对电动汽车的需求将以 到 2021 年的复合年增长率为 21%,2电池之间需要密切的伙伴关系 制造商和供应商再伟大不过了。供应商需要 提供可靠、成熟的解决方案,使制造商的系统能够 实现新的效率水平。最好的供应商可以帮助制造商 将这些新功能更快地推向市场,结果将 让电池和电动汽车生产蓬勃发展。
审核编辑:郭婷
-
电动汽车
+关注
关注
156文章
12210浏览量
232729 -
放大器
+关注
关注
143文章
13640浏览量
214401 -
驱动器
+关注
关注
53文章
8302浏览量
147237 -
电池
+关注
关注
84文章
10706浏览量
131717
发布评论请先 登录
相关推荐
大规模电动汽车生产需要先进的电池化成和测试系统
电力工业的发展,不少中、小型电厂需要扩大生产规模
新能源电动汽车
电动汽车电池断开系统
大规模的电动汽车生产有什么要求?
电动汽车整车线束测试方案研究
回收电动汽车电池,电动汽车电池回收,回收电动汽车电池组,电动汽车电池组回收,回收电动汽车电池组回收
大规模电动汽车生产需要先进的电池化成和测试系统
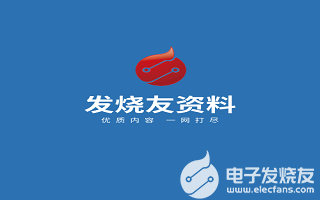
评论