作者:Luis Orozco and Wenshuai Liao
锂离子电池广泛用于笔记本电脑和手机等便携式设备,但由于其存储容量低于5安培小时(Ah),对制造效率的担忧已退居制造成本的次要地位。同时,车辆中使用的电池具有更高的总容量,通常为数百安培。这是通过数千个小型电池或一些高容量电池实现的。在这种情况下,功率效率与制造过程中的测试成本一起变得尤为重要。具有讽刺意味的是,这些环保车辆使用以浪费大量能源的方式制造的电池。
锂离子电池制造概要
图1显示了锂离子电池制造工艺的概述。生产线末端调节步骤的化成和测试是工艺瓶颈,对电池寿命、质量和成本的影响最大。
图1.锂离子电池制造工艺。
化成可能需要数小时,具体取决于电池化学成分。在化成过程中使用0.1 C(C是电池容量)电流是非常典型的,完整的充电和放电周期需要长达20小时,占电池总成本的20%至30%。
电气测试可以使用 1 C 的电流进行充电,0.5 C 的电流进行放电,但每个周期仍然需要大约三个小时。典型的测试序列需要多个周期。
化成和电气测试具有严格的精度规范,在规定的温度范围内,电流和电压控制在优于±0.05%。相比之下,在便携式设备中为电池充电时,电压精度为±0.5%,电流精度为±10%。
汽车电池制造面临的两个主要挑战是成本和功率效率。应从材料到制造和维护的全过程控制成本。充电过程中还必须保持高效率,如果可能,应在放电过程中回收能量。
化成和测试系统拓扑
设计工程师经常使用线性稳压器来轻松满足便携式设备中使用的电池化成和测试的精度要求,同时牺牲效率。在较大的电池上,这种方法会导致热管理方面的挑战,并且由于温度漂移而降低效率。
电动/混合动力汽车中使用的大量电池都必须很好地匹配,对精度提出了更严格的要求,使开关拓扑成为一个非常有吸引力的选择。表1显示了不同电池类别在功率容量和终端功能方面的比较。
电池尺寸 | 小 | 中等 | 大 |
容量(安时) | <5 | 10 到 15 | 30 至 >100 |
应用 | 便携式设备 比如手机, 摄像机等 | 笔记本 | 混合动力汽车, 电动汽车, 滑板车 |
数量 每个通道数 系统 | ~512 | ~768 | 16 到 64 |
专门的 要求 | 漂移更低 温度和 时间 | 更高的精度 过温 和时间 | 最高精度 过温 和时间; 均流 |
系统拓扑 |
线性或开关; 转换趋势 |
开关; 效率更高; 能源回收 首选 |
图2所示为采用ADI公司新型集成芯片组AD8450和ADP1972构建的单通道系统。两个独立的电路板使系统能够轻松配置不同的功率级。
图2.围绕AD8450和ADP1972构建的单通道系统。
AD8450测量和调理环路中的电压和电流信号。ADP1972是一款PWM发生器,可配置为降压或升压模式。模拟控制器和PWM发生器之间的接口由低阻抗模拟信号组成,这些信号不会受到抖动的影响,从而导致数字环路出现问题。CC(恒流)和CV(恒压)环路的输出决定了ADP1972的占空比,ADP1972通过ADuM7223驱动MOSFET功率级。当模式从充电变为放电时,AD8450内部测量电池电流的仪表放大器的极性反转。CC和CV放大器内部的开关选择正确的补偿网络,ADP1972将其PWM输出更改为升压模式。整个功能通过单个引脚和标准数字逻辑进行控制。
在此实现中,AD7173-8高分辨率ADC监控系统,但它不是控制环路的一部分。扫描速率与控制环路性能无关,因此单个ADC可以测量多通道系统中大量通道上的电流和电压。DAC也是如此,因此AD5689R等低成本DAC可以控制多个通道。此外,单个处理器只需要设置CV和CC设定点、工作模式和内务管理功能,因此它可以与多个通道接口,而不会成为控制环路性能的瓶颈。
配置有 4 V 电池和 20 A 最大电流的系统在 25°C ±10°C 范围内可实现优于 90% 的效率,典型精度为 90 ppm,电压环路为 51 ppm。CC 到 CV 的转换无毛刺,并在 500 毫秒内发生。从1 A到20 A的电流斜坡需要不到150 ms。 这些规格是车辆电池制造和测试的理想选择。
图3显示了CC放电模式下10 A和20 A下的效率。完整的测试结果可直接从ADI获得。
图3.经测试的系统电源效率。
降低电池成本
降低电池成本的挑战需要解决整个制造过程。这里描述的系统可以在不牺牲性能的情况下实现低成本的电池化成和测试系统。更高的精度允许更短和更少的校准周期,从而延长正常运行时间。此外,由于开关频率较高,设计更简单,电力电子元件更小,也有助于降低系统成本。通道也可以组合在一起,以最小的努力输出更高的电流。这种方法还可以通过在模拟域中执行所有控制来最大限度地降低软件开发成本,从而消除了对复杂算法的需求。最后,能源回收与高系统效率相结合,大大降低了持续运营成本。
能源回收
许多现有系统将其电池放电到阻性负载中。一些客户将这种能量用于建筑供暖,或者只是将热空气排放到室外。虽然这是最简单的电池放电方法,但当必须对大量电池进行充电/放电循环时,成本会迅速增加。我们提出的系统具有很高的单通道效率,但其真正的价值在于它能够以最小的额外复杂性从放电电池中回收能量。
围绕AD8450和ADP1972构建的系统无需将电池放电至阻性负载,而是可以控制电池电压和电流,同时将该能量推回公共总线,其他电池组可以在充电周期中使用。
每个电池通道可以处于充电模式,从直流母线汲取能量,也可以处于放电模式,将能量推回直流母线。最简单的系统包括一个单向交流/直流电源,它只能将电流从交流电源源入直流母线,如图4所示。这意味着必须仔细平衡系统,以确保来自 AC/DC 电源的净电流始终为正。将更多的能量推入直流母线,而不是充电通道消耗的能量会导致母线电压增加,可能会损坏某些组件。
图4.具有电池间能量回收的电池测试系统。
如图5所示,双向AC/DC转换器通过将能量推回交流电网来解决这一挑战。在这种情况下,可以先将所有通道设置为充电模式,然后设置为放电模式,将电流返回到电网。这需要更复杂的AC/DC转换器,但为系统配置提供了额外的灵活性,并且无需仔细平衡充电和放电电流以确保来自电源的净正电流。
图5.具有交流电源能量回收的电池测试系统。
具有能源回收效率
为了进一步说明能量回收的好处,请考虑一组 3.2 V、15 Ah 电池。这些电池可以存储大约 48 瓦时。要为完全耗尽的电池充电,假设充电效率为 90%,系统必须为每个电池提供大约 53.3 W-hr 的能量。在放电模式下,系统将消除 48 W-hr,要么将能量转换为电阻器中的热量,要么将其回收回总线。如果没有回收,则为两个电池充电大约需要 107 W-hr。但是,如果一个系统(如上所示的示例)可以以 90% 的效率回收能量,则第一个电池的 43.2 W-hr 现在可用于为第二个电池充电。如前所述,系统可以以 90% 的效率充电,因此再次需要 53.3 W-hr,但 43.2 W-hr 来自放电电池,因此我们只需要提供额外的 10.1 W-hr,总所需能量为 63.4 W-hr。这样可以节省超过 40% 的能源。在实际制造环境中,数百个电池在制造过程中被放置在不同的托盘中,因此这不会通过将每个托盘设置为一组处于充电或放电模式来增加总制造时间。
结论
开关电源为现代可充电电池制造提供了高性能、高性价比的解决方案。AD8450和ADP1972简化了系统设计,系统精度优于0.02%,能效高于90%,能量回收能力强,有助于解决可充电电池制造瓶颈问题。它使混合动力和电动汽车从制造过程开始环保。
审核编辑:郭婷
-
锂离子电池
+关注
关注
85文章
3241浏览量
77729 -
开关电源
+关注
关注
6465文章
8342浏览量
482176 -
电池
+关注
关注
84文章
10582浏览量
129785
发布评论请先 登录
相关推荐
TI能量回馈型的锂电池化成分容测试设备应用案例
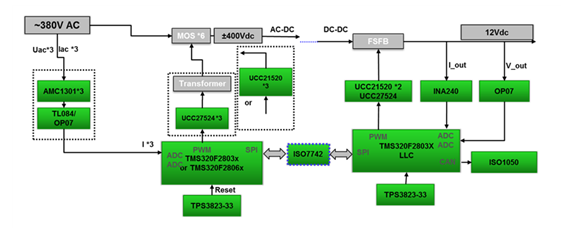
锡柴能量回收系统,针对如何回收各种热机,提出一套科学有效的解决方案
蓄能器各参数对能量回收和制动安全的影响

能量回收 对于电动汽车有很大的意义
电瓶修复技术:电池制动能量回收的详解
能量回馈型锂电池化成分容测试设备方案介绍
电机能量回收原理
电机制动能量回收原理
电动汽车制动能量回收系统的工作原理、组成、实现过程及优缺点
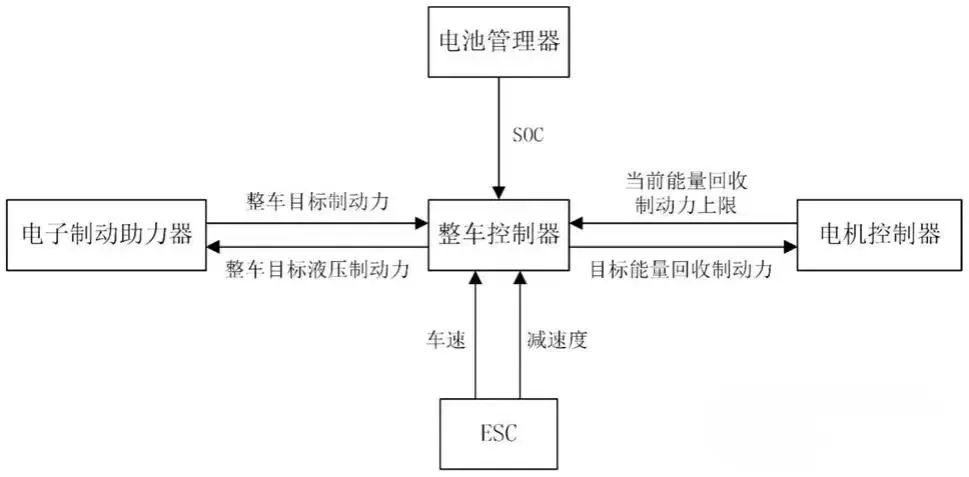
评论