摘 要:碳化硅单晶具有极高的硬度和脆性,传统加工方式已经不能有效地获得具有超高光滑表面的碳化硅晶片。针对碳化硅单晶衬底加工技术,本文综述了碳化硅单晶切片、薄化与抛光工艺段的研究现状,分析对比了切片、薄化、抛光加工工艺机理,指出了加工过程中的关键影响因素和未来发展趋势。
背景与意义
作为半导体产业中的衬底材料,碳化硅单晶具有优异的热、电性能,在高温、高频、大功率、抗辐射集成电子器件领域有着广泛的应用前景。碳化硅衬底加工精度直接影响器件性能,因此外延应用对碳化硅晶片表面质量的要求极为严苛。碳化硅硬度高、脆性大、化学性质稳定,传统加工方法不完全适用。受加工技术的制约,目前高表面质量碳化硅晶片的加工效率极低。
碳化硅单晶的加工过程主要分为切片、薄化和抛光。全球碳化硅制造加工技术和产业尚未成熟,在一定程度上限制了碳化硅器件市场的发展,要充分实现碳化硅衬底的优异性能,开发高表面质量碳化硅晶片加工技术是关键所在。本文主要针对碳化硅晶片的加工工艺做相关论述。
碳化硅单晶的切片
作为碳化硅单晶加工过程的第一道工序,切片的性能决定了后续薄化、抛光的加工水平。切片加工易在晶片表面和亚表面产生裂纹,增加晶片的破片率和制造成本,因此控制晶片表层裂纹损伤,对推动碳化硅器件制造技术的发展具有重要意义。
2. 1切片技术发展现状及趋势
传统的锯切工具如内圆锯片、金刚石带锯,转弯半径受限,切缝较宽,出片率较低,不适用于碳化硅晶体切割。目前报道的碳化硅切片加工技术主要包括固结、游离磨料切片、激光切割、冷分离和电火花切片,不同技术对应的性能指标如表 1 所示,其中往复式金刚石固结磨料多线切割是最常应用于加工碳化硅单晶的方法。
固结磨料线锯切片、激光切割、冷分离以及电火花切片等技术是针对碳化硅材料比较有效的切片方法,原理如图 1 所示。
固结磨料线锯切片技术是指将金刚石磨料固结在金属丝上,随锯丝运动实现磨粒的锯切加工,如图 1( a)。锯切区域磨粒分布均匀,具有效率高、污染小等优势。激光切割技术则是通过激光处理在内部形成改性层从碳化硅晶体上剥离出晶片,该技术处于研究阶段,如图 1( b)。冷分离技术具有材料利用率高,节能环保的优点,如图 1( c)。激光在晶锭内部形成角质层点平面,其上表面涂覆特制的分离材料并冷冻,遇冷收缩可分离晶圆薄片。电火花切片利用脉冲放电对碳化硅单晶进行腐蚀切割,精度和生产率高,如图 1( d)。加工后碳化硅晶片表面光滑,但切缝较宽,表面损伤层后续处理工艺需要进一步开发。
2. 2切片质量的主要影响因素与优化措施
表层裂纹损伤与切片质量密切相关。4 H-SiC 切片加工可能产生表层裂纹损伤,主要分为亚表面侧向裂纹损伤和中位裂纹损伤,如图 2 所示。该裂纹损伤在增加后续加工成本的同时,容易进一步扩展导致晶片断裂。锯切工艺参数、固结磨粒尺寸、工件进给运动,锯丝速度控制不当都可能导致切片出现表层裂纹损伤。在碳化硅衬底材料上进行外延生长、器件制造工艺及器件工作性能都与晶体取向相关。为了避免方向敏感性导致切片加工时晶片产生脆性裂纹,在碳化硅晶锭切片前,需要进行晶体定向检测。
碳化硅晶锭一般生长在 SiC{0001} 面上,沿平行于晶锭生长方向的 SiC 晶面进行切割,可有效降低切片表面贯穿螺型位错密度,提高切片质量。切片过程中锯切工艺参数的控制对于切片质量也至关重要。减小进给量和进给力可降低磨粒法向压应力,增大锯丝速度可降低磨粒切向压应力,小范围减小锯丝和镀层的磨损及磨粒的脱落,但需综合考虑锯丝损坏程度与锯切效率。此外需保持充足均匀的冷却液以减少残余热应力,减少锯丝的振动,避免磨粒应力场不稳定。
碳化硅晶片的薄化
碳化硅断裂韧性较低,在薄化过程中易开裂,导致碳化硅晶片的减薄非常困难。碳化硅切片的薄化主要通过磨削与研磨实现。
3. 1薄化技术研究现状
晶片磨削最具代表性的形式是自旋转磨削,晶片自旋转的同时,主轴机构带动砂轮旋转,同时砂轮向下进给,进而实现减薄过程。自旋转磨削虽可有效提高加工效率,但砂轮易随加工时间增加而钝化,使用寿命短且晶片易产生表面与亚表面损伤。加工缺陷的存在严重制约加工精度和效率,为了解决这些问题,研究人员开发出了不同的辅助技术,如砂轮在线修整,或研制新型软磨料砂轮,目前主要的技术包括超声振动辅助磨削和在线电解修整辅助磨削,加工示意如图 3。
图 3 ( a) 超声振动辅助磨削[20] ( b) 在线电解修整辅助磨削[21]
Fig.3 ( a) Grinding assisted by Ultrasonic vibration[20] and ( b) electrolytic in-process dressing[21]
超声辅助磨削是通过超声振动降低磨削力、砂轮磨损量,改善加工质量的方法。诸多研究表明,在一定的工艺条件下,相比于普通磨削,超声辅助磨削更适于硬脆材料的薄化加工。在线电解修整辅助磨削对 4 H-SiC 进行薄化加工原理如图 3( b) 所示。电解作用下,砂轮表面生成绝缘氧化膜,可以减缓砂轮的损耗,同时承托大量电解脱落的磨粒,与游离磨粒的研磨作用类似,有利于提高磨削表面质量。
研磨工艺可分为单面和双面研磨,小尺寸碳化硅晶片单双面研磨技术相继被开发。研磨加工碳化硅切片表面时,使用的磨料通常为碳化硼或金刚石,可分为粗磨和精磨。粗磨主要是去除切片造成的刀痕以及切片引起的变质层,使用粒径较大的磨粒。精磨目的是去除粗磨留下的表面损伤层,改善表面粗糙度,使用粒径较细的磨粒。
3. 2影响薄化效果的主要因素及研究趋势
研究发现,薄化工艺中晶片材料去除率和磨料粒径大小、密度、研磨盘转速、研磨压力等因素密切相关。研磨工艺中需要控制合适的压力参数,使磨粒具有足够的机械能实现材料去除。研磨压力和转速过小,则晶片去除率不足,影响加工效率; 若过大,则晶片几何尺寸变差,且晶片容易被压碎,影响成品率。研磨液中的磨粒硬度越高粒径越大,被加工晶片表面粗糙度越大。研磨盘过硬会损坏和污染工件表面,软研磨盘可允许磨料更多的滑动运动,加工后表面光洁度高,但平面度低。未来薄化加工的主要研究方向在于开发新型砂轮( 主要研究磨料与砂轮结合剂)、研磨液/盘( 如半固着磨料磨盘) ,优化研磨过程的工艺参数。此外,研究表明,当碳化硅材料去除深度小于 500 nm 时,高压相变现象会导致碳化硅材料以延性方式去除,延性域模式下的加工损伤深度低于脆性断裂模式,延性域磨削技术是薄化工艺的发展方向之一。为防止碎片,优化单面研磨技术是未来薄化加工大尺寸碳化硅晶片的主要技术发展趋势。
碳化硅晶片的抛光
抛光工艺的实质是离散原子的去除。碳化硅单晶衬底要求被加工表面有极低的表面粗糙度,Si面在0. 3 nm之内,C面在0. 5 nm之内。根据GB /T 30656-2014,4寸碳化硅单晶衬底加工标准如表2所示。
4. 1抛光技术研究现状
碳化硅晶片的抛光工艺可分为粗抛和精抛,粗抛为机械抛光,目的在于提高抛光的加工效率。碳化硅单晶衬底机械抛光的关键研究方向在于优化工艺参数,改善晶片表面粗糙度,提高材料去除率。
目前,关于碳化硅晶片双面抛光的报道较少,相关工艺参数有待进一步优化。精抛为单面抛光,化学机械抛光是应用最为广泛的抛光技术,通过化学腐蚀和机械磨损协同作用,实现材料表面去除及平坦化。晶片在抛光液的作用下发生氧化反应,生成的软化层在磨粒机械作用下相对容易被除去。作为单晶衬底加工的最后一道工艺,化学机械抛光是实现碳化硅衬底全局平坦化的常用方法,也是保证被加工表面实现超光滑、无缺陷损伤的关键工艺。目前报道的典型精抛工艺技术对比如表 3 所示。
碳化硅单晶的精抛工艺主要研究方向是开发结合化学和机械两方面增效的复合工艺,化学增效方法主要有电化学、磁流变、等离子体、光催化等,机械增效方法主要有超声辅助、混合磨粒和固结磨粒抛光等方法,相关加工原理如图 4 所示。
4. 2影响CMP的关键因素与发展趋势
CMP 的机械和化学作用达平衡时,抛光效果可达最优。CMP 的抛光效果主要受工艺参数、抛光液、抛光垫三方面参数的影响。抛光液和抛光垫是 CMP 的主要耗材,控制优化其性能以保证可重复的抛光效率对于工艺稳定性至关重要。对抛光液进行改良,研发具备自催化作用的抛光垫,是未来CMP 耗材的研究方向。上述新型抛光方法中如 PAP、CMRF 需要大功率高温装置,系统成本高,工艺可操作性差,目前主流的碳化硅晶片精抛工艺仍是 CMP。碳化硅 CMP 过程材料去除率模型的建立以及催化、电化学增效机理亟待进一步研究。综合利用碳化硅氧化理论及催化化学等方法,将多种化学和机械增效技术进行复合,如超声辅助电化学机械抛光、磁流变-催化复合辅助抛光、固结磨粒-超声-催化抛光技术等,以同时提高碳化硅表层氧化速率与氧化层机械去除速率,是未来优化碳化硅抛光工艺效率和质量的发展方向。
讨论
碳化硅晶片加工是单晶生长后的一大高难度工艺,国内相关单位现已能够加工出基本满足器件制备要求的衬底片,但晶片表面加工精度与国外相比仍然有较大差距,国外对相关理论和工艺都存在技术封锁,研究人员需要采用更先进的精密工艺设备,进一步研究切片、薄化、抛光过程中的机理,优化晶片加工方法,制备出高质量的碳化硅衬底。
审核编辑:汤梓红
-
单晶
+关注
关注
1文章
62浏览量
14201 -
衬底
+关注
关注
0文章
37浏览量
9429 -
加工技术
+关注
关注
0文章
17浏览量
7552 -
碳化硅
+关注
关注
25文章
2900浏览量
49472 -
切片技术
+关注
关注
0文章
5浏览量
5700
原文标题:碳化硅单晶衬底加工技术现状及发展趋势
文章出处:【微信号:cetc45_wet,微信公众号:半导体工艺与设备】欢迎添加关注!文章转载请注明出处。
发布评论请先 登录
相关推荐
碳化硅深层的特性
归纳碳化硅功率器件封装的关键技术
碳化硅单晶体二极管的优势及应用范围
碳化硅单晶衬底加工技术的工艺及现状研究
介绍超声加工技术的发展概况、研究现状及未来发展趋势
碳化硅行业现状及前景怎么样
SiC碳化硅单晶的生长原理
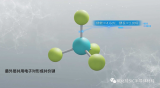
碳化硅单晶衬底的常用检测技术
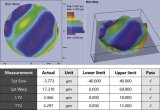
评论