作者:陈一峰丨上海汽车变速器有限公司
1 引言
变速器润滑油在整个变速器中有着不可或缺的作用,润滑油用于变速器内部的齿轴、轴承等零部件以减少摩擦,主要有润滑、冷却、抗腐蚀防锈、清净冲洗、动能传递、密封和应力分散缓冲等作用。因此,一旦在变速器工作过程中发生润滑油的泄漏,变速器在工作状态中的性能将受到影响,甚至会产生因润滑不良而齿轮抱死等故障,从而导致行车的安全性问题。因此,变速器的密封性也是变速器壳体设计中的重要指标之一。绝大多数整车厂对此也有严格的考核标准。
2 变速器壳体结合面密封性能有限元分析
2.1 问题描述
某项目的变速器在pt耐久的试验中发现变速器壳体有漏油渗油现象,经过使用荧光剂,可以判断漏油位置如图1所示(图中绿色荧光剂部分)。因此,对壳体的结合面进行了有限元密封性分析,找出漏油的具体位置并对壳体密封面行进有效的优化,以改善密封效果。
2.2 接触应力计算的有限元基础
假设主动轮为弹性体A,从动轮为弹性体B。A和B在相互接触的地方有许多接触点对,在外载荷{PA}和{PB}的作用下,产生了位移{UA}和{UB}。根据有限元基本理论可得到平衡方程:
图1 壳体漏油位置
其中,[KA]、[KB]为A,B的整体刚度矩阵;{UA}、{UB}为A,B的节点位移向量;{PA}、{PB}为A,B的整体外载荷向量;{RA}、{RB}为A,B的接触力向量。
当A,B材料、单元类型、外载荷条件确定后,上式中的[KA]、[KB]、{PA}、{PB}就已 知 了, 但 是 有 {UA}、{UB}、{RA}、{RB}4个未知量,只有方程(1)和方程(2)两个方程无法解出,所以要补充接触点对的接触连续条件。按接触面状态可分为分离、黏结接触和滑动接触3种,其对应的接触面的位移和力的条件是各不相同的。假设取A,B上的一个接触点对,分别为接触点对的法向接触力,
为接触点对的切向接触力,
为接触点对的法向位移,
为接触点对的切向位移,则以下方程便是接触点对的定解条件。
可见对于一种特定的接触状态,如果有m个接触点对,就可以找到4m个定解条件作为补充方程,那么方程(1)和方程(2)就可以求解了。
接触求解的过程是,对于有限元模型中的一个接触点对,首先给它一个假定的接触状态,将其定解条件代入平衡方程(1)和方程(2),求出节点位移和接触点对接触力向量。然后根据节点位移和接触点对向量检查计算得到的接触状况和假设的接触状况是否相符,如不符即要重新假定接触状态再次选择定解条件,重新进行迭代求解平衡方程,直到计算前后接触状态完全符合。
2.3 有限元模型的建立
该变速器为横置变速器,壳体由离合器壳体和主壳体组成,所以仅存在一个结合面。本次仿真的主要目的是为了验证壳体结合面的密封情况,因此,仿真模型中并未加入变速器齿轴,并且采用将齿轴载荷通过轴承孔传递给壳体的方式给壳体进行加载。为了使仿真的边界条件更加接近整车的工况,仿真模型中加入了悬置支架。同时,仿真模型中使用rbe2和beam单元的方法代替螺栓连接,螺栓加载预紧力约为15~18KN。壳体结合面建立摩擦接触对,摩擦系数约为0.15~0.2。将数模进行几何清理后,划分网格,壳体及悬置支架网格的平均尺寸约为3mm,并将结合面网格局部细化并保证网格质量,如图2所示。
图2 变速器壳体与悬置支架有限元模型
2.4 边界条件与工况
为了使分析与实际整车工况较为接近,将悬置支架约束6个自由度(也可加入悬置的实际刚度值),同时将离合器壳体的大端面也约束6个自由度。由于汽车在实际行驶中工况比较复杂,仿真中选择了比较典型的1档工况和倒档工况来分析问题。变速器壳体内部所受的载荷一般由齿轮的啮合传递至轴承,再由轴承传递至壳体,因此从MASTA软件提取轴承的受力情况加载于壳体上。(表1、表2)
表1 一档工况各轴承孔的受力情况
2.5 有限元分析结果
2.5.1 螺栓预紧力分析结果
首先考察壳体结合面仅在螺栓预紧力作用下的间隙(间隙),如图3所示为在仅受螺栓预紧力情况下的壳体结合面的间隙云图,从图中可以看到,壳体定位销孔附近的间隙较其他位置相对大一些,但最大值也小于0.003mm,因此可以得出结论,在仅受螺栓预紧力的工况下,壳体结合面的密封性能良好,不会有漏油渗油的风险。
表2 倒档工况各轴承孔的受力情况
图3 壳体仅受螺栓预紧力时结合面间隙
2.5.2 动态工况分析结果
壳体1档工况下结合面的间隙,如图4所示,壳体上部分有部分间隙大于0.012mm并且贯穿了整个壳体结合面,最大间隙约为0.029mm。变速器壳体结合面之间通常是涂有密封胶的,根据这种密封胶的性质,其最大断裂延伸率为260%,结合密封胶的最大厚度及其他因素后,可以近似认为当壳体结合面间隙大于0.012mm且间隙贯穿整个结合面时可以就有漏油渗油的风险。尽管图中所示区域在整个油液面的上方,但齿轮工作时会把油甩到壳体上方,因此出现了渗油的情况(具体渗油位置与前文所述渗油位置相吻合)。
图4 变速器壳体1档工况下结合面间隙
壳体倒档工况下结合面的间隙,如图5所示,壳体结合面的最大间隙为0.026mm,但其中大于0.012mm的部分在结合面的宽度方向上的区域很小,因此认为壳体在倒档工况时漏油渗油的风险并不大。
3 变速器壳体结合面密封性能优化
3.1 变速器壳体结合面密封性能的优化方法
通常情况下,与变速器结合面密封性能有关的因素有以下几种:1.密封胶的属性与性能直接关系到密封性能;2.螺栓的拧紧力矩(预紧力);3.螺栓之间的布置位置;4.壳体结合面的宽度;5.壳体整体的结构刚度。
当然,上述方法中最有效的还是方法3,螺栓布置的松密会直接影响结合面的工作时的间隙,因此,在相同条件且空间允许的情况下布置更密的螺栓可以直接优化壳体的密封性。而从增加壳体整体刚度的角度来说,实际可行性就相对较差,效率也不高,通常在实际项目中很少使用。
根据本项目的具体情况,首先,渗油的位置处于壳体安装后的上方位置且渗油的情况并不是很严重,基于壳体的实际状态和优化的成本,最终采取了方法4对壳体结合面进行优化。优化后的壳体如图所示,螺栓中心的连线被结合面宽度所包络。
图5 变速器壳体倒档工况下结合面间隙
3.2 变速器壳体结合面密封性能的优化结果
按上述优化的方法对壳体进行优化后,对渗油的1档工况重新进行了仿真,结果如图6示。结果显示,结合面的最大间隙有原来的0.0295mm降到了0.0187mm,间隙下降了近36%,同时大于0.012mm的区域由原来的贯穿整个结合面下降到了仅40%左右,因此从理论上可以得到密封性能满足要求的结论。
图6 优化后的变速器壳体1档工况下结合面间隙
经过后续的试验,并没有再次发生渗油现象。
4 结论
漏油渗油是变速器常见的故障之一,一旦发生故障,就会给变速器甚至行车安全带来巨大的危害,因此确保变速器的密封性能非常重要。本文通过有限元的计算方法,可以准确地计算出变速器壳体在具体工况下的结合面的密封性能,并可以通过试验的验证。变速器壳体的密封性能与许多因素有关,其中包括:密封胶的属性与性能、螺栓的拧紧力矩(预紧力)、螺栓之间的布置位置、壳体结合面的宽度、壳体整体的刚度等等。普通工况下,保证结合面之间的贯穿的间隙不大于0.012mm就可以在密封胶的作用下确保变速器的密封性能。通常变速器壳体渗油漏油的位置都在油液面一下,但并不排除油液面以上的部分出现渗油现象。
审核编辑:汤梓红
-
变速器
+关注
关注
5文章
317浏览量
34324 -
密封性
+关注
关注
0文章
34浏览量
7154 -
优化
+关注
关注
0文章
220浏览量
23890 -
有限元分析
+关注
关注
1文章
35浏览量
9574 -
离合器
+关注
关注
0文章
111浏览量
14605
原文标题:变速器壳体密封性的有限元分析与优化
文章出处:【微信号:EDC电驱未来,微信公众号:EDC电驱未来】欢迎添加关注!文章转载请注明出处。
发布评论请先 登录
相关推荐
MATLAB有限元分析与应用
如何有效的学习CAE有限元分析
求一种有限元分析中PCBA的简化建模方法
光纤电场传感器的有限元分析
有限元分析及应用_曾攀
abaqus动力学有限元分析指南
有限元分析相关知识的解析
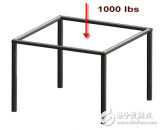
基于箱形梁CADCAE有限元分析
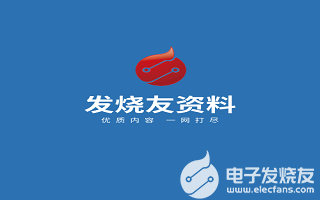
评论