极芯是一个电池系统的最小单元。多个极芯组成一个模组,再多个模组组成一个电池包,这就是车用动力电池的基本结构。电池就像一个储存电能的容器,能储存多少的容量,是靠正极片和负极片所覆载活性物质多少来决定的。正负电极极片的设计需要根据不同车型来量身定做的。正负极材料克容量,活性材料的配比、极片厚度、压实密度等对容量等的影响也至关重要。
一:搅拌与涂布
搅拌就是将活性材料通过真空搅拌机搅拌成浆状。这是电池生产的第一道工序,该道工序质量控制的好坏,将直接影响电池的质量和成品合格率。而且该道工序工艺流程复杂,对原料配比,混料步骤,搅拌时间等等都有较高的要求。这道工序就是将上一道工序后已经搅拌好的浆料以每分钟80米的速度被均匀涂抹到4000米长的铜箔上下面。而涂布前的铜箔只有6-8微米厚,可以用“薄如蚕翼”来形容。涂布工序最重要的是厚度和重量的一致性。涂布至关重要,需要保证极片厚度和重量一致,否则会影响电池的一致性。涂布还必须确保没有颗粒、杂物、粉尘等混入极片。否则会导致电池放电过快,甚至会出现安全隐患。
二:辊压
辊压车间里,通过辊将附着有正负极材料的极片进行辊压,一方面让涂覆的材料更紧密,提升能量密度,保证厚度的一致性,另一方面也会进一步管控粉尘和湿度。
三:叠片
叠片是所有工序中最重要的一道,叠片的好坏直接影响到电池的性能与质量。将辊压后的极片根据需要生产电池的尺寸进行分切,并充分管控毛刺(毛刺只能在显微镜下看清楚)的产生,这样做的目的是避免毛刺扎穿隔膜,产生严重的安全隐患。极耳模切工序就是用模切机形成极芯用的导电极耳。我们知道电池是分正负极的,极耳就是从极芯中将正负极引出来的金属导电体,通俗的说电池正负两极的耳朵,是在进行充放电时的接触点。
四:装配
将叠好的极芯装入铝塑壳中以便保护极芯且在注液工序封壳注液,通过焊接机器人焊接正负极极耳并裁切成需要的形状,通过X-RAY可以检测叠片工序是否有多叠少叠情况。
五:烘烤
水分是电池系统的大敌,电池烘烤工序就是为了使电池内部水份达标,确保电池在整个寿命周期内具有良好的性能。为了去除水分,极芯需要进行烘烤。
六:注液
而注液,就是往极芯内注入电解液。电解液就像极芯身体里流动的血液,能量的交换就是带电离子的交换。这些带电离子从电解液中运输过去,到达另一电极,完成充放电过程。电解液的注入量是关键中的关键,如果电解液注入量过大,会导致电池发热甚至直接失效,如果注入量过小,则又影响电池的循环性。
七:化成
化成是对注液后的极芯进行激活的过程,通过充放电使极芯内部发生化学反应形成SEI膜(SEI膜:是锂电池首次循环时由于电解液和负极材料在固液相间层面上发生反应,所以会形成一层钝化膜,就像给极芯镀了一层面膜。),保证后续极芯在充放电循环过程中的安全、可靠和长循环寿命。将极芯的性能激活,还要经过X-ray监测、绝缘监测、焊接监测,容量测试等一系列“体检过程”。化成工序当中还包括,对极芯“激活”后第二次灌注电解液、称重、注液口焊接、气密性检测;自放电测试高温老化及静置保证了产品性能。
八:PACK
单个的极芯是不能使用的,只有将众多极芯组合在一起,再加上保护电路和保护壳,才能直接使用。这就是所谓的电池模组。电池模组(module)是由众多极芯组成的。需要通过严格筛选,将一致性好的极芯按照精密设计组装成为模块化的电池模组,并加装单体电池监控与管理装置。从简单的一颗极芯到电池包的生产过程也是相当复杂,需要多道工序,一点不比极芯的制造过程简单。
-
动力电池
+关注
关注
113文章
4534浏览量
77660 -
电极
+关注
关注
5文章
813浏览量
27227 -
电池
+关注
关注
84文章
10576浏览量
129718
原文标题:动力电池生产工艺流程
文章出处:【微信号:智享汽车电子与软件,微信公众号:智享汽车电子与软件】欢迎添加关注!文章转载请注明出处。
发布评论请先 登录
相关推荐
固态电池的生产工艺流程
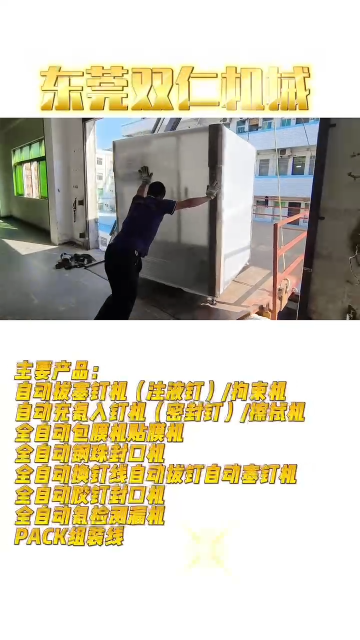
动力电池阻抗分析
温度是如何对动力电池的性能造成影响?
动力电池模组装配线:高效、精准的动力之源
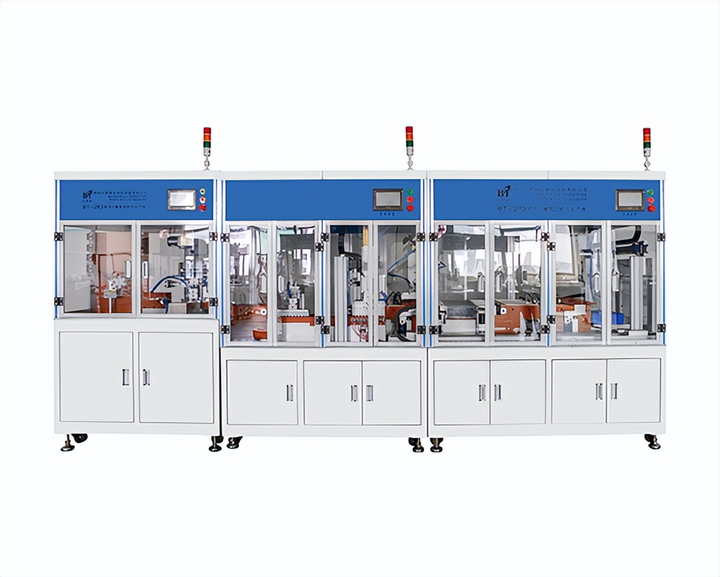
固态电池带动生产工艺、相关设备的革新
动力电池结构与原理介绍
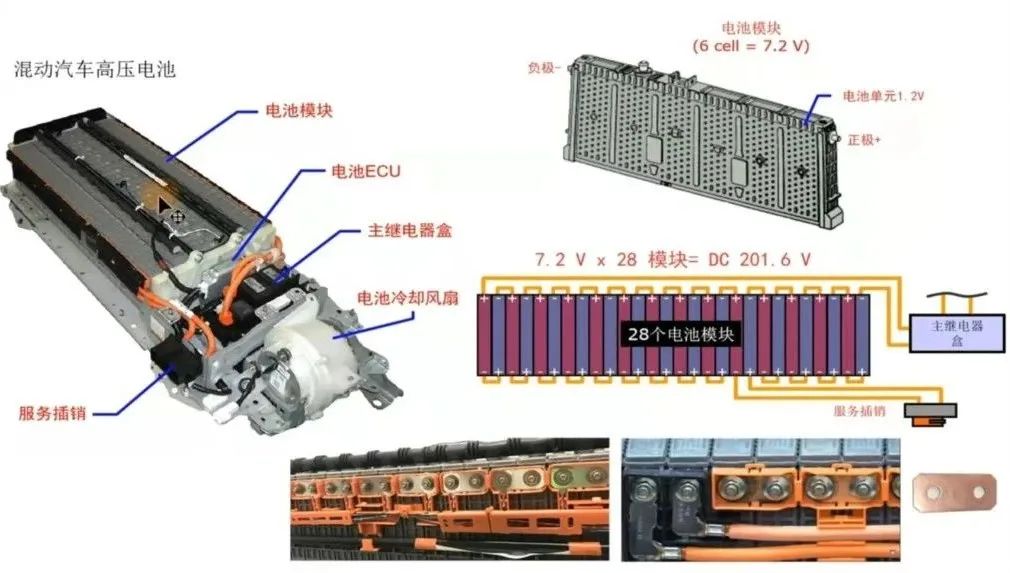
评论