来源:《噪声与振动控制》-金文辉, 郭峰, 段龙杨, 钟秤平
根据驱动能源传递方法典型的传动结构可分为3种:(1)传统驱动模式;(2)电机驱动桥集中式驱动模式;(3)轮毂电机分散驱动模式。传统驱动模式在一定程度上仍采取传统内燃机车辆的驱动系统布置方式,保留原有的变速器、传动轴和驱动桥等结构,仅将电机替换了原有的内燃机,属于改造型电动车[1]。其传动效率较低,无法充分发挥驱动电机性能。在轮毂电机分散驱动模式中电机直接装在车轮里,结构紧凑,传动效率高,但成本较高、控制难度较大。本次研究的轻客所搭载的电驱动后桥属于电机驱动桥集中式驱动模式,其成本较低,具有较高的传动效率,且便于维修。
随着发动机噪声掩蔽效应消失,以及受新增电驱系统的高频噪声的影响,电动汽车的噪声、振动与声振粗糙度(Noise vibration harshness,NVH)性能受电驱系统噪声水平影响较大。行业内针对电机噪声[2]和减速器啸叫[3–5]进行了大量研究,但主要集中在单个部件参数上,很少对电驱总成进行系统性研究。本文针对某电动轻客加速时电机及减速器啸叫问题进行实验诊断,对可能原因进行分析,得到引起啸叫的根本原因,从整车路径和减速器设计及加工方面进行优化,最终解决该问题。
1 电驱动后桥啸叫概述
1.1 电驱动后桥结构及相关参数介绍
电驱动后桥布置在后排地板下方,电机输出轴通过花键与减速器一轴连接,经过两级齿轮减速后,通过后桥驱动后轮传递动力。减速器为偏置式结构,一轴与电机转子轴同轴,二轴、差速器轴与转子轴平行。其相关参数如表1 所示,结构简图如图1所示。
表1 电驱动后桥相关参数
图1 电驱动后桥结构简图
1.2 问题描述
在中大油门加速工况下,在20 km/h~50 km/h车速区间车内存在明显中低频啸叫,在50 km/h~90 km/h 时存在高频啸叫,主观不可接受。经测试确认,20 km/h~50 km/h 时啸叫主要为二级齿轮(7.11阶、14.22 阶)和一级齿轮(26 阶)啮合噪声,50 km/h~90 km/h 时主要为一级齿轮(26 阶、52 阶)噪声以及电机48阶噪声,如图2所示。
图2 大油门加速车工况下内后排噪声彩图
2 实验分析诊断
2.1 啸叫分析流程
根据NVH 问题分析中常用的“源头-传递路径-响应”重要分析理论[6],本文针对电驱动后桥啸叫的影响因子绘制出鱼骨图(详见图3),运用LMS Test.Lab测试分析系统对其逐一分析。
图3中噪声源分析是通过试验明确不同车速下啸叫的主要激励源,并确定其关键影响因子;传递路径分析包括整车声包、气密性、减振器隔振以及板簧隔振等4 个方面。下文根据以上思路进行分析和排查。
图3 啸叫影响因子鱼骨图
2.2 噪声源分析
针对噪声源激励的问题,运用LMS Test.Lab软件对电驱桥总成噪声及振动进行数据采集和分析。整车试验工况为大油门加速电机转速从1 000 r/min至10 000 r/min,噪声测点为电机近场车头方向50 cm处,振动测点为减速器壳体底部。其中测点布置如图4所示。
图4 电机噪声及减速器振动测点
电机近场噪声和减速器壳体振动速度曲线测试结果如图5、图6所示。在不同转速下固定阶次的噪声及振动的频率计算方法如式(1)所示:
图5 电机近场50 cm 48阶噪声曲线
图6 减速器壳体振动速度曲线
式中:f为频率,r为转速,n为阶次。
图5中电机近场噪声曲线显示大油门加速工况下在6 800 r/min~7 700 r/min存在峰值87 dB(A),对应频率为5 440 Hz~6 160 Hz,超出目标值。结合图2 的车内噪声彩图可知,车内48 阶噪声在7 000 r/min~7 700 r/min 存在峰值,为70 km/h~80 km/h时高频啸叫的主要来源。
电机结构上影响48阶噪声主要因素有:
(1)齿槽扭矩,即电机齿数与槽数配合带来的定位力矩;
(2)径向力波,即定子与转子之间在不同电流工况下的径向力;
(3)转矩波动,即在不同工况下电机转动方向的力的波动;
(4)电机刚度。其影响电机壳体振动幅值及壳体模态。考虑到该电机除外壳外均为借用件,在不改变电机原设计方案前提下,从源头优化仅能通过改变电机壳体材质,趋势性增加电机壳体刚度,以降低电机壳体振动,减弱壳体辐射噪声。
图6 中减速器壳体一级减速齿轮26 阶、56 阶振动幅值异常,该齿轮在设计或加工上可能存在较大问题。二级减速齿轮7.11阶、14.22阶振动在部分转速段也超过参考值(0.5 mm/s),需作进一步优化。
2.3 传递路径分析
2.3.1 空气辐射路径
本次研究的轻客车身面积相对较大,且存在较多孔洞及钣金缝隙,整车基础气密性相对较差,且电驱动后桥所处的整车后排声包偏弱。较差气密性以及较弱声包导致整车声衰减较小,特别是针对中高频噪声。提升整车气密性及加强声包能有效提升声衰减,从而实现降低车内啸叫幅值。
2.3.2 结构传递路径
电驱动后桥主要通过左、右两侧板簧安装在车身上,同时通过减震器与车身纵梁连接。其结构传递路径主要为板簧和减震器。
综合减震器耐久性及整车舒适性评估,其衬套邵氏硬度最大允许降低10度,经验证若采用该方案车内仅14.22阶噪声在3 500 r/min~6 000 r/min可优化2 dB(A)。
板簧作为电驱动后桥与车身间的主要减震件,其弹簧钢以及与车身连接处的橡胶衬套由于受布置空间和耐久性能限制而无法进行较大变更。且通过在板簧上加质量块并未取得明显效果。板簧路径不作为本次优化的主要方向。
2.3.3 模态测试分析
借助LMS Test. Lab 测试分析软件中Spectral testing模块,建立电机、减速器和车桥的电驱动桥实验模型。为保证模态振型的可识别性,整个模型共计采用50 个测点,采用力锤激励形式,用多输入多输出法进行测试,并运用PolyMax modal analysis 分析模块计算2 000 Hz~7 000 Hz范围内的模态振型。针对电机48阶噪声问题,测试结果显示电驱动后桥综合频响函数在5 926 Hz 附近存在峰值,与车内噪声频率一致。经进一步分析确认,该频率振型为电机筒状壳体沿径向的外扩振型。其中电驱动后桥实验模型图如图7所示。综合频响函数测试结果如图8所示。5 926 Hz振型结果如图9所示。
图7 电驱动后桥实验模型
图8 电驱动桥综合频响函数曲线
图9 电机总成外扩模态振型
根据本章分析结果可得,在5 926 Hz 电机总成存在外扩模态,电机48阶噪声在7 000 r/min~7 700 r/min 偏大原因是48 阶激励频率与电机壳体固有频率发生耦合,产生共振,并向外辐射噪声,最终传至车内。
3 优化方案研究
根据客观测试分析可得,电机啸叫的根本原因是电机48 阶激励频率与电机总成的壳体固有频率发生耦合,产生共振。减速器啸叫的根本原因是减速器齿轮设计及加工不合理,导致其壳体振动超标。其次整车声包及气密性未达到理想状态,最终导致车内电机及减速器啸叫明显。
经分析,可从如下途径进行优化:
(1)降低减震器橡胶硬度,提升其隔振性;
通过对白酒生产过程的全面跟踪、检查,了解到白酒产品中的塑化剂属于特定迁移,主要来源于塑料接酒桶、塑料输酒管、酒泵进出乳胶管、封酒缸塑料布、成品酒塑料内盖、成品酒堵料袋包装、成品酒塑料瓶包装、成品酒塑料桶包装等[21-22],且塑化剂在白酒中的含量随着时间的延长而越来越多。白酒中塑化剂主要有以下几种:邻苯二甲酸二异丁酯(DIBP),邻苯二甲酸正丁酯(DBP),邻苯二甲酸二(2-乙基)己酯(DEHP)以及微量的邻苯二甲酸二甲酯(DMP)和邻苯二甲酸二乙酯(DEP)[23]。
(2)优化整车气密性及声包,提升其声衰减;
(3)加强电机壳体刚度,减弱壳体振动;
(4)降低电机和减速器激励。
上述方案中,1 和2 对噪声抑制效果有限,无法根本解决问题。3仅对电机啸叫有轻微抑制作用,且会导致成本增加。4是最直接有效的方案。
3.1 整车路径优化
经整车气密性检测,确认车身尾部钣金及侧拉门泄露较大。针对这两处泄漏点,在钣金缝隙增加密封胶封堵,在侧拉门迎宾踏板处增加密封软垫以及在地板下方增加吸声棉。具体措施示意图如图10所示。
图10 路径优化示意图
通过提升整车气密性及声学包,车内后排7.11阶噪声在5 000 r/min~7 000 r/min 降低5 dB(A)~10 dB(A),48 阶噪声在整个转速段降低3 dB(A)~5 dB(A),噪声数据如图11所示。
图11 空气路径优化前后车内后排噪声曲线
3.2 减速器加工及装配工艺优化
3.2.1 增大齿轮倒棱角尺寸
图12 齿轮倒角优化前后对比
3.2.2 齿轮装配工艺优化
将一级减速被动齿轮内花键与二轴外花键由间隙配合改为过盈配合,齿轮和二轴分开加工再压装改为压装后再磨削,以增加齿轮加工精度。齿轮与轴的结构如图13所示。
图13 一级减速被动齿轮与二轴结构示意图
3.2.3 减速器壳体加工工艺优化
将减速器壳体加工由二次装夹改为一次装夹,并将壳体加工定位方式由壳体螺纹底孔改为工艺基准孔,以减小壳体轴承支撑孔位置度偏差。原设计壳体加工定位方式为螺纹底孔,且加工中存在二次装夹,导致定位累计误差较大,影响轴承位置度。而轴承座位置度会影响齿轮中心距、接触面积及传递误差,导致减速器三根轴的空间位置变化,轴线发生偏移,齿轮啮合不均,见图14。
图14 减速器轴系发生偏移示意图
3.2.4 减速器啸叫优化效果
对加大齿轮倒角、优化减速器壳体加工工艺和齿轮装配工艺后的样件进行测试,发现在大油门加速工况下,车内后排7.11 阶噪声在5 500 r/min~6 500 r/min受抑制明显,测试结果如图15所示。
图15 减速器加工及装配工艺优化前后车内后排噪声曲线
3.3 齿形优化
3.3.1 齿形误差优化
齿形误差一般是由滚齿机分度齿轮系统误差或滚刀振摆造成。为了减小齿形误差,就要提高滚齿机分度传动系统精度和滚刀精度,从而提高齿轮的加工精度[7]。原始设计中使用普通刚玉系或碳化系砂轮加工齿轮,齿形偏差(齿廓波纹度)ffα较大,影响齿轮啮合面积及啮合区域,从而导致由齿轮啮合产生的冲击较大。而砂轮的直径越大,齿轮精度越容易保证。改用大直径的金刚滚轮加工齿轮可有效优化ffα,控制其在2 μm 以内。齿形偏差ffα示意图如图16所示,其实测结果如表2所示。
图16 齿形偏差ffα示意图
表2 齿形偏差ffα实测值/μm
3.3.2 齿轮微观修形
Xu[8]提出齿轮激励力最有效的优化方法为修形。修形分为齿形修形和齿向修形。前者是沿齿根到齿顶方向进行微量修整,使其偏离理论齿形;后者是沿齿线方向修形,可改善载荷沿齿线的分布。
本次修形方案为调整二级减速被动齿轮齿形鼓形量Cα和齿形倾斜偏差fHα。齿形修形参数示意图如图17所示,其实测结果如表3所示。
图17 齿形修形参数示意图
表3 齿形修形参数数值/μm
3.3.3 减速器啸叫优化效果
经实验验证,优化ffα以及调整齿轮微观参数Cα和fHα对抑制减速器阶次噪声均有明显效果,噪声数据如图18所示。
图18 齿形误差优化及齿轮修形前后车内后排噪声曲线
3.4 方案确认
针对大油门加速工况下电机和减速器啸叫问题,以车内后排右侧外耳噪声为评价指标,通过提升整车气密性及加强声学包,抑制电机啸叫较明显,整体评估可接受,但减速器啸叫仍偏大。针对减速器啸叫问题,在路径优化基础上,对减速器加工与装配工艺以及齿轮齿形进行优化,经验证该方案优化效果明显,整体可接受。
其中在钣金缝隙处增加密封胶封堵、在侧拉门迎宾踏板处增加密封软垫、在地板下方增加吸声棉等路径优化方案和齿轮倒角优化、齿轮装配、减速器加工工艺优化等方案以及齿形误差优化、齿轮微观修形等方案均已工程化。优化后,电机啸叫主观评分由原始状态5.5 分提升至6.5 分,减速器啸叫主观评分由5.0 分提升至6.5 分。具体优化效果如表4所示。
表4 各方案优化效果
4 结语
本文针对某电驱动后桥轻客在中大油门加速工况下电机及减速器啸叫问题,建立啸叫关键影响因子鱼骨图,通过实验对可能存在原因进行诊断分析,从源头振动、路径传递等方向提出了气密性优化、声学包加强、齿轮加工及装配工艺优化、齿轮修形等可工程化的组合方案,彻底解决了电驱动桥工作所引起的整车啸叫问题,对此类车型NVH优化具有重要的借鉴和参考意义。
审核编辑:汤梓红
-
噪声
+关注
关注
13文章
1130浏览量
47622 -
电机
+关注
关注
143文章
9139浏览量
147005 -
电机驱动
+关注
关注
60文章
1244浏览量
87127 -
啸叫
+关注
关注
0文章
36浏览量
8795 -
减速器
+关注
关注
7文章
400浏览量
23519
原文标题:轻型电驱桥啸叫优化分析
文章出处:【微信号:EDC电驱未来,微信公众号:EDC电驱未来】欢迎添加关注!文章转载请注明出处。
发布评论请先 登录
相关推荐
驱动桥啸叫整车试验及后桥啸叫机理分析
轻型空箱围堤对邻近桥梁桩基影响分析
PHS网络优化分析
无功优化分析软件设计
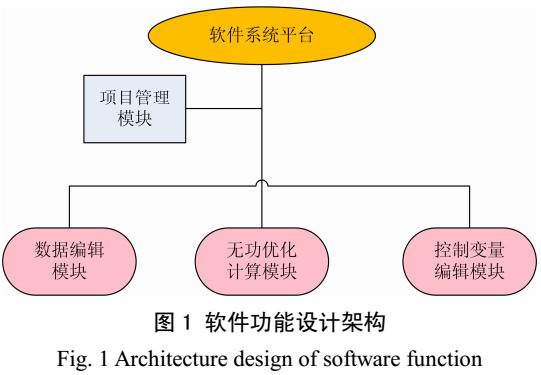
通信产品EMC/EMI仿真优化分析
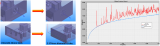
纯电动汽车电机啸叫噪声优化
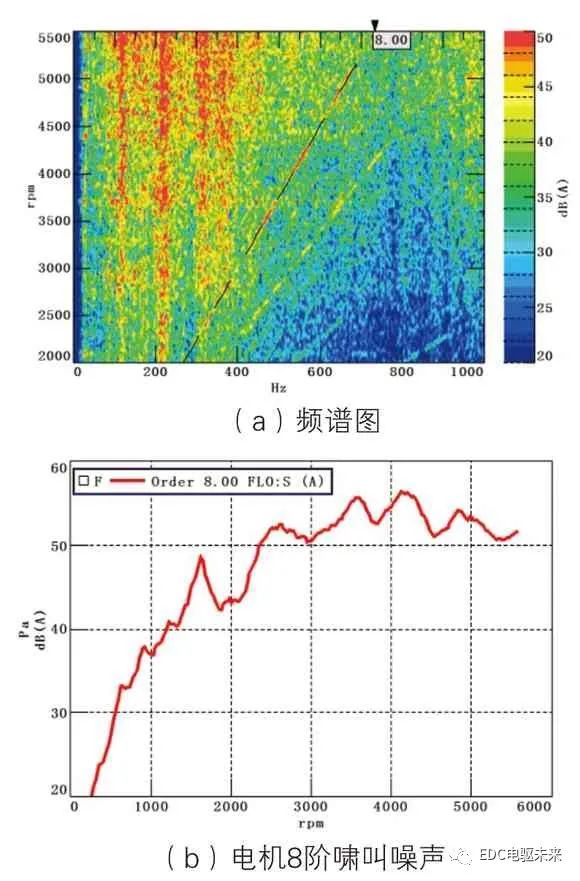
轻型电驱桥啸叫优化分析
基于MASTA软件电驱桥减速器齿轮的优化设计方案
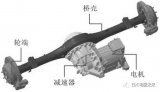
高速电驱系统电机NVH开发与优化
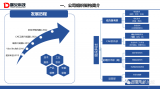
评论