新半导体技术提供的更高集成度使当今的电信系统能够以越来越小的尺寸集成越来越多的功能。更小几何形状的工艺可确保更低的功耗、更低的工作电压和更少的每功能硅的平方密耳。新的印刷电路板通常包括工作在5V、3.3V、2.5V、O.8V等的IC。
新一代IC的功率要求在负载、线路和静态电压调节方面更加严格。在某些情况下(例如,受英特尔 VRM 8.2 规范约束的情况),输出电压通过数字总线进行编程,电平介于 1.8V 和 3.5V 之间,负载电流为 30A 或更高。电源技术总体上没有跟上这一趋势,尽管半导体技术允许更高的集成度、完整的自动电路板组装和更小的电路板间距。
除非在极少数情况下,否则电源无法自动组装。大多数都有用于热管理的大型散热器,迫使手动组装。对于大多数电信系统,传统的冷却技术迫使散热器尺寸的增长。所需的散热器表面与电源效率直接相关(图 1)。因此,新的电源电压(3V或更低)对散热器尺寸有直接影响。考虑一个正激式转换器,如图1所示,工作功率为100W:
带 5V 输出:PLOSS= 100(P外/eff.)-POUT= 100(100/83) - 100 = 20.5W
带 3V 输出:PLOSS= 100(100/70) - 100 = 42.9W
图1.对于 DC-DC 转换器,低电压操作会降低效率。
将电源电压从5V下移至3V会使功耗从20.5W增加到42.9W,从而产生另外22.4W的功耗,这是热设计中必须考虑的因素。功耗的第一个问题是内部温度的升高,这会降低所有组件的MTBF。因此,缩小IC制造的尺寸和成本对相关电源会产生相反的影响,除非我们考虑 全新的电源管理架构。
对于简单的电信系统,为了清楚起见,将其降至最低(图2),我们考虑了三种可能的电源方法。该系统包括一个处理高数据速率的光纤接口板(如STM-1光纤),一个包含系统管理和辅助功能的背板,以及多达10个线卡,每个线卡都有一个低数据速率接口,如ISDN'U'、POTS或E1/T1。这些负载需要多个输出,源自标称值 -48V,带备用电池,可在 -42V 至 -60V 或 -36V 至 -76V 范围内提供。必须与电池进行电气隔离。
图2.基本组件构成一个简单的电信系统。
输出 | 电压 (V) |
精度( 静态/负载/ 线规则的总和) (%) |
负荷 电流 (A) | 输出 功率 (W) |
光纤 接口: | ||||
1 | 3.3 | 2 | 3 | 9.9 |
2 | 2.2 | 2 | 3 | 6.6 |
3 | 1.8 | 2 | 2 | 3.6 |
4 | 5.0 | 5 | 2 | 10 |
5 | -5.0 | 5 | 1 | 5 |
底板: | ||||
1 | 5 | 5 | 2 | 10 |
2 | 1.8 | 2 | 2 | 3.6 |
3 | 1.3 到 3.5 | 1 | 10 | 35 |
接口 (一块板): | ||||
1 | 3.3 | 2 | 2 | 6.6 |
2 | 2.2 | 2 | 2 | 4.4 |
3 | 1.0 | 2 | 2 | 3.6 |
首先,将接口要求乘以 10,以在系统中最多容纳 10 块板。所需的总功率为230W,分配给五个固定稳压输出电压和一个通过5位总线编程的可变输出电压。该可变输出的最大容差为 1%,包括线路和负载调整率。正在考虑的三种配电架构是集中式电源、分布式和隔离式电源以及具有辅助非隔离分布式输出的集中式单输出。
集中式电源
该单元产生所有必需的电压作为与电池电压隔离的次级输出。在本例所需的输出功率电平(230W)下,典型配置可以是正桥或半桥,控制环路闭合(例如)在3.3V的主输出上。其他输出必须进行后置稳压,以符合严格的容差要求。这些后置稳压器可以是线性型或开关型,每种类型都独立于其他类型,由具有耦合输出电感器的多个次级变压器驱动(图 3)。
图3.在这种多输出电源中,每个次级器件包括耦合电感器和一个后线性稳压器IC。
这种方法有几个缺点:定制设计的磁性元件难以生产,寄生元件会对性能产生巨大影响,并且系统效率低。请注意,较低的输出电压会导致较低的效率,因为整流二极管和线性稳压器(甚至LDO类型)所代表的损耗占输出的百分比更大。
考虑对 1.5V 输出进行简化分析(图 4)。假设电流占空比为50%,整流二极管电流等于I外,电感损耗仅与电阻有关,与磁芯材料、开关频率等引起的磁效应无关。出于类似的原因,我们忽略了电容器中ESR引起的损耗:
POUT = IOUTVOUT = 10(1.5) = 15W
PL = IOUTVOUTRL = 10(10)(0.01) = 1W
PD1 + D2 = VD(IOUT) = 10(0.4) = 4W
PLDO = IOUTVLDO = 10(0.6) = 6W
Eff. = POUT/(PL + PD1 + PD2 + PLDO + POUT) = 15 / (1+ 4 + 6 + 15) = 58%
图4.由于存在固定损耗,较低的输出电压意味着该线性稳压电源的效率较低。
因此,对于输送到负载的每瓦特,电路损失0.7W作为热能,这不是一个有吸引力的能量使用。更有趣的是基于开关后置稳压器的系统(图 5)。
图5.这些开关模式稳压器(与线性类型相比)提供更高的效率以及更大的复杂性和噪声。
图5中的5V主输出由光耦合器反馈调节,所有其他输出由IC调节,如同步降压型(MAX1630、MAX1637、MAX1652和MAX1638)或MAX774负输出电压反相型。使用来自不同供应商的标准“现成”磁性元件,同步降压稳压器产生的1.5V输出可实现87%的效率,而线性稳压器方法的效率为58%。
图6所示的降压稳压器IC包括同步整流功能,是目前同类器件中最大的成员。它具有降压调节功能,具有过压和欠压保护、电流保护和辅助电压能力。
图6.这款降压型控制器IC提供具有同步整流功能的双路输出。
另一种可能性是使用反相DC-DC控制器从正电压产生负电压,如图7所示。该 IC 和一些外部元件(电感器、功率 MOSFET 和输出电容器)提供了产生该系统所需的 -5V @ 2A 的最简单方法。Maxim评估套件集成了上述所有器件,简化了电路板布局并加快了设计过程。
图7.这些开关模式IC将正输入电压转换为稳定的负输出。
在大多数情况下,中央电源是定制设计,安装在易于访问和方便的热管理的位置。该规范由系统或设计工程师编写,并提交给公司的电源部门或专门从事电源设计和制造的许多其他公司之一。无论哪种方式,最终结果都是交付经过全面测试和合格的“黑匣子”。
来自电池的高电压仅影响电源的输入部分。出于安全原因并符合 EN60950、UL950 等规范,所有次级输出都与电池隔离。符合这些标准安全规范还可确保集中电源可以在整个系统中分配其调节电压,并且无需担心到设备其他部分的间隙距离。
为了实现冗余,您可以使用串联二极管轻松并联两个电源,在相应的输出之间创建OR连接。这种架构使电源的成本和尺寸翻倍,但它通常用于中小型电信系统中的开关后置稳压。
对于更复杂的系统,例如前面提到的示例,这种方法存在两个问题:首先,需要昂贵的电缆和连接器线束来为系统中的所有电路板承载高负载电流。其次,板之间的电压调节是一个问题;遥感可以保证一块板上的稳压,但它不一定在其他板上提供足够的容差来确保安装在其上的各种IC正常运行。最后一点通常排除了对集中式电源的考虑。即使对于简单的系统,降低电源电压的趋势和对更严格监管的需求也使得集中式方法越来越难以实施。
分布式和隔离电源
在这种方法中,电池电压(-48V)提供给系统中的所有电路板(图8),并且每个电路板都包含一个或多个适合该板要求的电源。从某种意义上说,集中式电源被分成各种较小的DC-DC转换器,每个转换器都独立于其他转换器。为此,当今市场提供了广泛的单输出和多输出DC-DC转换器,其容量从几瓦到超过600瓦。例如,两个电路中的任何一个都可以满足“接口板”电源要求:
1. 三个直流-直流转换器
2.一个 DC-DC 转换器和三个开关后置稳压器
第一个解决方案很简单;您可以购买三个“现成”模块,并根据制造商的EMI滤波,短路保护,热管理等规格将它们安装在板上。缺点是成本(每瓦),因为每个模块都需要自己的隔离变压器、反馈回路和其他组件。第二个电路的成本降至最低,因为隔离和主输出电压由一个DC-DC转换器提供,而简单的降压转换器则提供其他稳压输出。功率要求通常在10W至30W范围内,因此反激式或正激式转换器拓扑可以用于第一级。
图8.一种配电方法是将原始电池电压(-48V)路由到每个电路板,并根据需要进行下变频。
在图9的简化原理图中,初级侧控制器(PFM MAX1771或PWM MAX668)提供了一些有趣的特性。两者都是CMOS芯片,功耗非常低,并且可选使用外部p沟道开关MOSFET,使两款器件能够在不改变控制电路的情况下提供宽范围的功率。后置稳压由MAX1627实现,MAX90是一款简单的PFM降压型稳压器,具有外部开关MOSFET。PFM控制的最大优势是效率与输出负载的关系:在这种情况下,从2mA到2A超过<>%!
图9.作为图8所示方法的替代方案,将电池电压下变频(并隔离)一次,并将该较低电压分配给各种简单的降压转换器。
MAX6501采用微型SOT23封装提供温度保护。当其封装达到预设的内部电平时,其输出逻辑状态将发生变化,以警告可能存在的热问题。因此,您可以通过将这些器件安装在变压器、功率MOSFET和系统中的其他热点附近来实现经济的热保护。
两个器件完善反馈环路:精密、低压差、微功耗电压基准(MAX6025)提供小于20ppm/°C的温度系数和优于0.2%的初始精度。微功耗运算放大器(MAX4040)提供90kHz增益带宽乘积,电源电流仅为10μA。两款器件均采用微型 SOT23 封装。
由于分布式电源系统在其使用点附近调节功率,因此它很容易满足当地对线路、负载和静态调节的要求。另一个优点是,分布式电源系统中的小型转换器(与通常由外部分包商开发的大型中央电源不同)可以轻松适应电路板设计开发过程中经常发生的电源要求变化。
冗余并不总是需要重复电源(1+1 冗余);N+1 冗余有时就足够了。这里,N是代表系统所需所有功率的各种电源电压的总和,激活一个备用电源电压只是为了替换故障输出(然后维护用故障输出替换电路板)。如果电源具有热插拔功能,则可以在不关闭系统电源的情况下修复此故障。维护更容易,因为您可以更容易地更换印刷电路板,而不是带有所有连接器的大型集中电源。
从电磁的角度来看,系统必须符合将要安装它的各个国家/地区规定的所有规范。因此,为了抑制由于来自各种电源的开关频率相互作用而产生的噪声,必须在每块电路板的电源输入端安装EMI滤波器。为了防止这些多个滤波器产生EMI问题,您可能还需要在-48V总线上安装一个额外的滤波器(图10)。
图 10.为确保符合每个国家的EMI规范,请在主转换器和所有辅助下变频器上安装EMI滤波器。
同步转换器频率可能无法解决问题;有时它甚至会使问题变得更糟。如果所有转换器都以相同的频率切换,则第一次谐波将具有更多的能量,并且EMI滤波器中需要更多的衰减。这种架构的一个低效方面是隔离和从-48V到3.3V的下变频。此外,在整个系统中安装IC转换器也存在热管理问题。您可以为每个散热器添加一个散热器,但这也会增加系统的成本和处理能力。
PC 板上封装的高度不能很大,并且 -48V 的存在需要在电路板上的二次电子元件之间留出特定量的间隙。这种间隙需求意味着不能在昂贵的多层PC板上使用一定数量的保护区域。作为通过半导体技术获得集成优势的折衷方案,将集中式电源的优点与分布式和隔离电源的优点相结合的系统架构对新设备非常感兴趣。
将集中式电源与分布式非隔离电源相结合
由于-48V总线意味着安全问题,而3.3V总线存在线路和负载调节困难,因此最佳解决方案可能是中间配电电压。原理是使用单输出集中电源,实现与电池的电流隔离,同时将输入电压(36V至76V)降压至12V。12V 用作系统的内部总线,非隔离稳压器根据需要从中获取其他电源电压。
唯一的隔离是在从-48V降压至12V的转换器中。由于12V将由当地稳压器在板级进一步降压,因此严格的12V稳压不是必需的;公差为 ±10% 或更高是可以接受的。这种宽松的规格允许基于主变压器的辅助绕组进行调节的简单反馈回路。辅助绕组通常也为转换器的初级侧供电,因此无需次级IC控制器和光耦合器。
接近 12V 的电压是理想的,因为它在配电总线中没有过大电流的情况下提供可接受的效率。它允许合理的热管理,并且通过正向或全桥,可以轻松实现82%至85%的效率。12V电源应安装在可接近的位置,以便在外部世界和电源散热器之间实现最大的热交换,但不会将热空气引向热敏元件。一旦知道这种功耗,机械设计人员就可以执行分析(比具有多个热源的系统简单得多),以优化设备内的气流。
这种12V电源将占系统功耗的四分之三以上。假设该级效率为10%,第二级后置稳压器的效率为83%,则每向负载输送95W,则系统在第一次下变频至2V时功耗为12W,在从0V至5.12V的第二次下变频中功耗仅为3.3W。因此,热分析应主要关注第一个模块(12V电源),而不是后置稳压器。实际上,可以选择它们的位置来优化印刷电路布局。
请注意,串联两个转换的效率通常与单次转换的效率相同或更高,例如从-48V到+3.3V。两个或多个输出电压进一步增加了单次和双次转换之间的效率差距。您可以根据需要合理地向 12V 总线添加任意数量的后置稳压器,但将高压转换器直接添加到 -48V 总线既庞大又昂贵。
由于第一个转换器的输入为电池电压,其输出为安全隔离,因此在定位转换器或其电源总线时无需特别注意间隙距离或爬电距离。此外,您可以通过在每个板级开关稳压器的输入端添加滤波器来减少反射纹波。一阶LC滤波器通常就足够了,因为电池至12V转换器有自己的EMI滤波器。
这种EMI滤波器的衰减必须超过相关国际标准规定的限制,这些标准通常考虑环境和终端设备的类型。噪声由第一个转换器和12V输出端的后置稳压器产生。
电荷泵系列转换器(图11)能够升压或反相输入电压。输出电压可以不稳压或反馈以提供稳压。对于非稳压器件,输出电平取决于输入电压和负载电流。不需要磁性部件。内部开关首先将外部电容器连接到输入端,然后将其充电至 V在.然后,其他内部开关将同一电容器连接到输出侧。
图 11.电荷泵转换器可以反相或降压输入电压并调节输出,所有这些都无需使用电感器。
由于没有磁性元件,因此人们对这种用于板级应用的转换器类型产生了兴趣。电荷泵转换器(如MAX682)具有更高的开关频率和更低的导通电阻,可在仅5mm x 250.5mm (8mm)的空间内提供6V @ 44mA电流。2).
更高的功率电平由开关模式稳压器管理,该稳压器采用外部电感器,采用升压、降压和升压/降压配置。Maxim推荐经过测试和验证的电感器,通常指定来自两个或多个供应商的零件号。大多数是标准的SMD零件,在全球范围内可用,并且“现成”,易于采购和全自动组装。
您可以选择具有内部功率MOSFET和控制电路的器件,如MAX887,一种能够在SO封装中提供500mA电流的降压型稳压器,或者MAX710,一种低压差(LDO)升压转换器,在500QSOP封装中提供16mA电流。为了管理高达35A的输出电流,MAX1638等器件采用外部功率MOSFET。
MAX1638(图12)为同步降压控制器,能够通过数字总线改变其稳定的输出电压。它符合英特尔的 VRM 8.2 规范,可提供大输出电流(超过 35A),并且需要小于满足负载调节指定动态容差水平所需的输出电容器。为了限制负载电流快速变化引起的过冲和下冲,MAX1638控制由两个小功率MOSFET组成的“毛刺捕捉器”电路,通过减小电容尺寸来节省成本和空间。
图 12.该降压型控制器提供同步整流和数字可调输出电压。
当输出电压超出稳压状态超过 ±2% 时,p 或 n 沟道毛刺捕获器开关接通,通过将电流从输入或接地直接注入输出,迫使输出重新进入稳压状态。对于使用最小值输出电容的应用中小于2V的输出,此操作最为有效。
审核编辑:郭婷
-
电源
+关注
关注
185文章
17953浏览量
252755 -
散热器
+关注
关注
2文章
1065浏览量
37905 -
电池
+关注
关注
84文章
10756浏览量
132124
发布评论请先 登录
相关推荐
如何防止浪涌电压冲击功率因数控制电路或充电器
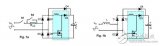
评论