本文采LiFePO4作为正极材料,锂片作为负极材料,制备成扣式锂离子电池,以面密度、压实密度和厚度一致性三个参数为指标,系统地研究这些参数对电池性能的影响规律,为锂离子电池极片的制作工艺提供基础数据和依据。
1 实验
1.1 极片制作
正极用量LiFePO4∶acetyleneblack∶PVDF=8:1:1,行星式球磨机将按比例配好的电极物质300r/min的速度1h正反转交替运行球10h,制得正极片浆料。研钵中浆料加入适量NMP溶剂,继续研磨均匀制得浆料。在2℃、干燥环境下,将浆料涂敷于铝箔(厚度20um)上,涂敷厚度设定为100、150和200um三种,烘干后进行辊压。其中涂敷厚度为100um的极片,分别在不同压下率、不同道次和温度下进行辊压,涂层压下率设定为30%、40%、50%三种,道次设定为1、2、3(道次为1时,压下量按照50um压下;道次为2时,压下量按照30/20um压下;道次为3时,压下量按照 20/20/10um压下)三种,温度设定为20、90 和160℃三种,共制得9种由不同工艺制作的极片。切片机切片16mm制得电池正极片。
1.2 电池制备
正极采用实验制作的正极片,负极均采用锂片。正极片、锂片、隔膜(Celgard2500)置于充满高纯氩气的手套箱,经注液、密封等工艺制备成CR2025扣式电池。将制备的电池按照不同的极片制作工艺进行编号,表1为不同电池的极片制作工艺参数,表中涉及的面密度ρ1和压实密度ρ2由式(1)和(2)求解:
式中:m1为极片质量;m2为铝箔质量;w为活性物质的质量分数;S为极片面积;h1为辊压后的极片厚度,h2为铝箔厚度。
1.3 测试方法
利用电子扫描显微镜对正极片进行微观形貌观察;用蓝电测试仪对电池进行恒流充放电测试;用电化学工作站进行循环伏安和交流阻抗测试。对上述测试的实验数据按电池编号进行记录。
1.4 实验仪器
行星式球磨机、涂布机、辊压机、手套箱、扫描电子显微镜、蓝电测试仪、电化学工作站。
2 结果与讨论
2.1 涂层压下率对电池性能的影响
由图1可见,随压下率从30%增加到40%再增加到50%,样品的放电比容量从142mAh/g 增加到153mAh/g再增加到158mAh/g,这是由于压实密度过小时粒子间距离大,离子通道多,电解液吸液量大,有利于离子移动,但因粒子间接触面积小,不利于电子导电,放电极化增大;一定程度内,随着压实密度增大,原材料粒子之间的距离减小,接触面积加大,导电通道和桥梁增加,增大能够参与反应的活性面积,从而显著提高电池的比容量。
由图2可见,随压下率从30%增加到40%再增加到50%,正极材料的电荷转移阻抗从 70Ω下降到35Ω再下降到28Ω,这是由于压实密度过小时较高的孔隙率造成部分颗粒形成绝缘状态,无法参与充放电,而高压实密度的电极有更高的断裂强度,从而避免在循环过程中电极颗粒脱落,形成绝缘状态颗粒。高的压实密度可以明显使电极的孔径和孔隙的分布更加均匀,导电剂和粘结剂分布更加均匀,降低电极的接触电阻和电荷转移阻抗。
2.2 涂覆厚度对电池性能的影响
由图3可见,随涂覆厚度从100um增加到150um再增加到200um,样品的容量保持率逐渐下降,50次循环的容量保持率从95%下降到93%再下降到91%,这是因为极片面密度越小,其极片就越薄,电池内阻也越小,在充放电循环中锂离子不断嵌入和脱出时对极片结构造成的变化也就越小,循环性能就越好,容量保持率就越高。面密度较大的极片使锂离子的迁移路径变长,电池内阻也较大,在锂离子的迁移路径上就容易发生拥堵,就会导致锂离子在短时间内不能完全脱嵌,最后导致比容量损失。
图4为各样品在不同倍率下的放电比容量。样品分别在0.1C、0.5C、1C、2C、5C倍率下各充放电循环5次,随着充放电倍率增加,虽然各样品放电比容量都减小了,但由于与上述同样的原因在同一倍率下,涂覆厚度为100um的样品放电比容量高于涂覆厚度为150um的样品,涂覆厚度为150um的样品放电比容量高于涂覆厚度为200um的样品。5C倍率下涂覆厚度为100um的样品仍然具有100mAh/g的放电比容量,而涂覆厚度为150和200um的样品分别只有60和40mAh/g的放电比容量。
2.3 辊压道次对极片及电池性能的影响
2.3.1 辊压道次对极片厚度一致性的影响
图5为涂敷厚度为100um的极片在不同辊压道次下的厚度曲线。道次为1时,压下量一次压下50um;道次为2时,压下量按照30/20um依次分批压下;道次为3时,压下量按照20/20/10um依次分批压下。如图5所示,随着辊压道次由1增加为2再增加为3,极片厚度偏差由±3.0um降低为±1.9um再降低为±1.4um,极片厚度一致性逐渐提高,这是因为随着辊压道次的增加,极片涂层压实密度也逐渐增加,使得极片表面厚度更加均匀。
2.3.2 辊压道次对极片表面形貌的影响
图6为不同辊压道次下的极片涂层表面SEM图。如图6所示,道次为1时,极片涂层表面部分区域颗粒结合较为紧密,部分区域结合还不够紧密;道次为2时,极片涂层表面颗粒紧密结合的区域增加;道次为3时,极片涂层表面颗粒紧密结合几乎成为一体,涂层的致密程度进一步增加。辊压道次的不同改变了极片涂层粒子间的距离和间隙,使得极片涂层表面具有不同的密实程度。
2.3.3 辊压道次对电池性能的影响
由图7可见,辊压道次从1次增加为2次再增加为3次时,各样品的循环性能有所提高。第50次循环的放电比容量分别为141、151和157mAh/g,这是由于随着辊压道次增加,极片的厚度一致性提高了。如果正极极片厚度显著不均匀,充放电过程就会在极片局部进行,造成电极材料与电解液界面处的电阻增大而降低比容量。
图8为各样品的交流阻抗谱。交流阻抗谱图由高频区的半圆和低频区的直线构成,高频区半圆在Z' 轴上的截距代表正极与电解液界面处的电荷转移阻抗,辊压道次从1次增加为2次再增加为3次时,各样品的电荷转移阻抗从45Ω减小为32Ω再减小为28Ω。
2.4 辊压温度对极片及电池性能的影响
2.4.1 辊压温度对极片厚度一致性的影响
图9为涂敷厚度为100um的极片在不同辊压温度下的厚度曲线。如图所示,随着辊压温度由20℃增加为90℃再增加为160℃,极片厚度偏差由±1.9um降低为±1.3um再降低为± 0.8um,极片厚度一致性逐渐提高。这是因为随着辊压温度的增加,极片涂层变形抗力减小,可塑性变好,使得极片表面厚度更加均匀。
2.4.2 辊压温度对极片表面形貌的影响
图10为不同辊压温度下的极片涂层表面SEM图。如图所示,辊压温度为20℃时,极片涂层表面部分区域颗粒结合较为紧密,部分区域还不够紧密,且存在少量微孔;辊压温度为90℃ 时,极片涂层表面颗粒紧密结合程度增加,紧密结合区域增加,微孔数量在减少;辊压温度为160℃ 时,极片涂层表面颗粒紧密结合程度进一步增加,紧密结合区域进一步增大,微孔数量进一步减少。辊压温度的不同改变了涂层的变形抗力,使得极片涂层表面具有不同的致密程度。
2.4.3 辊压温度对电池性能的影响
由图11可见,当辊压温度从20℃提高到90℃再提高到160℃时,样品的库仑效率也有所提高。库仑效率是在同一充放电循环中放电比容量与充电比容量的比率,极片的厚度一致性提高时电阻就会下降,库仑效率也会提高。
图12为各样品的循环伏安性能曲线,可见3个样品中当辊压温度为160℃时,向上的氧化峰与向下的还原峰对称性较好,峰位差也最小,充电和放电的可逆性也最好,证明库仑效率必然也高。
3 结论
锂离子电池正极片的制作工艺,涉及面密度、压实密度和极片厚度一致性三个重要参数。这些参数都是通过影响电池的内阻而影响电池的性能的,减小面密度、适当增大压实密度和提高极片厚度一致性都会减小电池的内阻,特别是减小电解液与正极片接界处的电荷转移阻抗。凡是能减小电池内阻的参数设置,都会提高电池的性能,反之则降低电池的性能:
(1) 涂覆厚度从100um增加到150um再增加到200um,面密度相应地从2.48mg/cm2增加到3.72mg/cm2再增加到4.96mg/cm2,第50次循环的容量保持率从95%下降到93%再下降到91%,5倍率放电比容量从100mAh/g下降到60mAh/g再下降到40mAh/g。
(2) 压下率从30%增加到40%再增加到50%,压实密度相应地从0.35g/cm3增加到0.42g/cm3再增加到0.49g/cm3,样品的放电比容量从142mAh/g 增加到153mAh/g再增加到158mAh/g。
(3) 正极片辊压道次从1次增加为2次再增加为3次时,极片厚度一致性逐渐提高,第 50次循环的放电比容量从141mAh/g增加到151mAh/g再增加到157mAh/g。
(4) 正极片辊压温度从20℃提高到90℃再提高到160℃时,极片厚度一致性逐渐提高,充电和放电的可逆性提高,库仑效率也提高。
审核编辑:刘清
-
锂离子电池
+关注
关注
85文章
3238浏览量
77700 -
接触电阻
+关注
关注
1文章
106浏览量
11922 -
电子显微镜
+关注
关注
1文章
92浏览量
9844 -
扣式电池
+关注
关注
2文章
11浏览量
10692
原文标题:极片面密/压实/厚度对电池性能影响!
文章出处:【微信号:Recycle-Li-Battery,微信公众号:锂电联盟会长】欢迎添加关注!文章转载请注明出处。
发布评论请先 登录
相关推荐
智能摊铺压实监测管理系统
为什么要在路面施工中使用智能摊铺压实监测管理系统
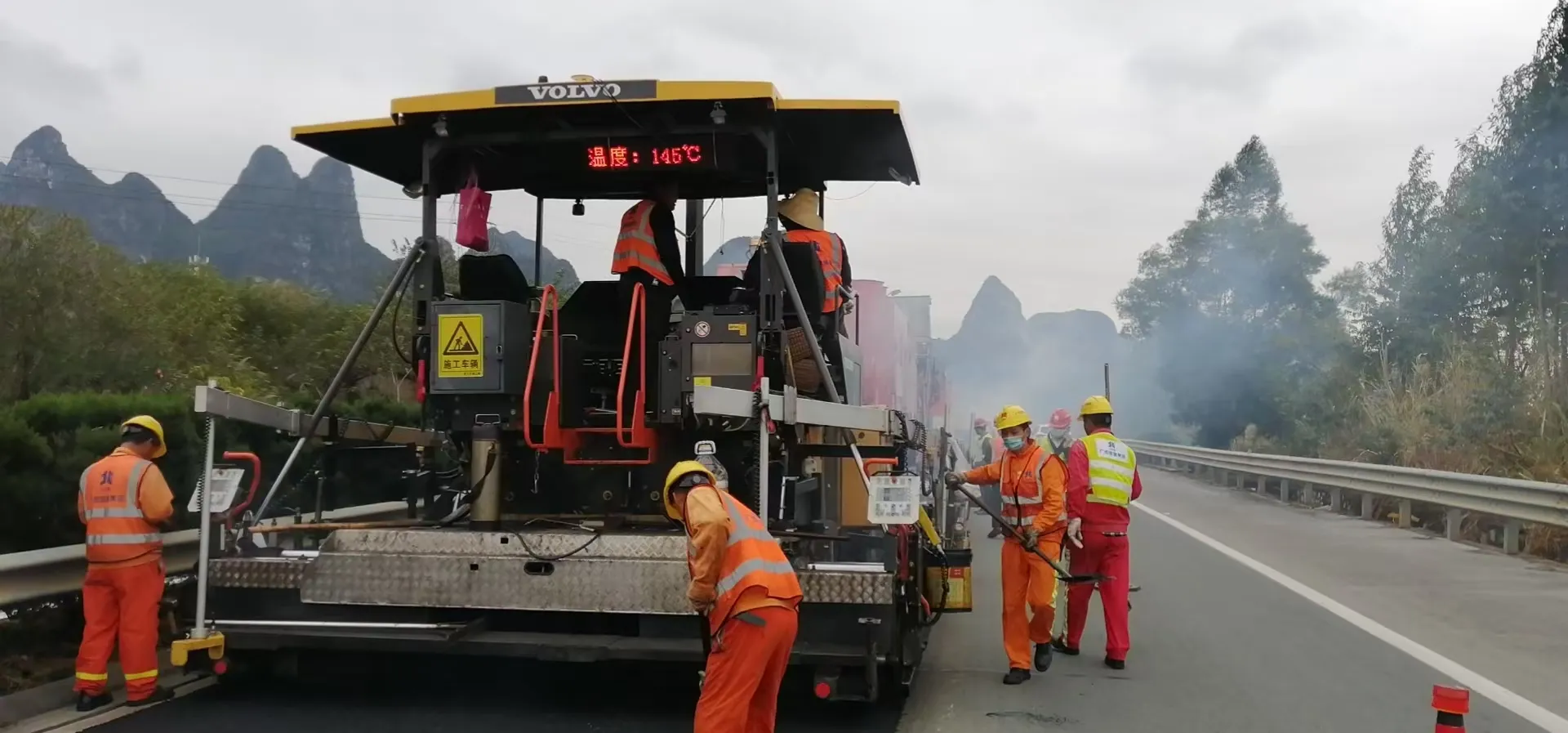
智能摊铺压实监测管理系统在公路建设中的应用介绍
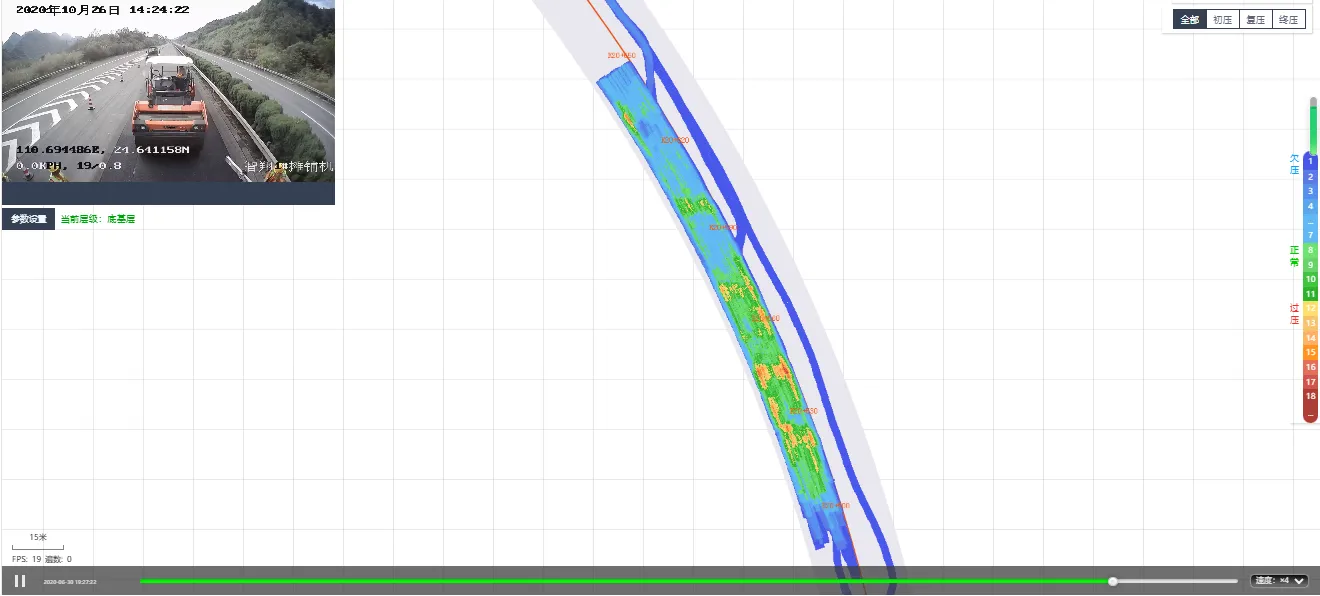
智能摊铺压实监测管理系统成为提升路面施工质量和管理效率的重要工具
智慧工地路面摊铺压实APP管理系统是路面施工过程管理好帮手
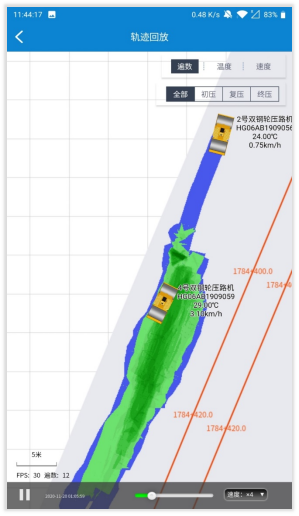
路面施工摊铺压实监测管理系统
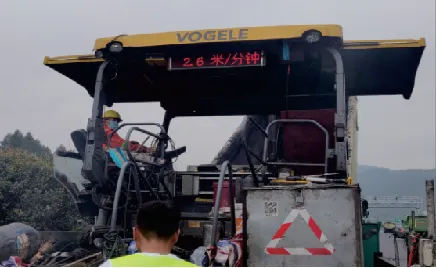
PCB线路板的厚度对性能的影响
路面施工智能摊铺压实监测管理系统
智慧工地摊铺压实管理系统应用简述
智能摊铺压实监测管理系统
Poly层厚度对TOPCon太阳能电池性能的影响
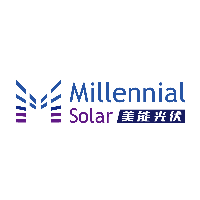
igbt导通压降受哪些因素影响
Poly层厚度对N型TOPCon太阳能电池电学性能的影响
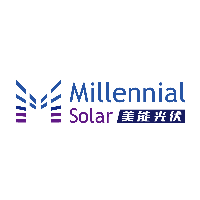
评论