半导体载带自动焊是一种集成电路组装工艺,适用于无常规封装体的裸芯片。其基本原理是将每个硅芯片粘在一条特制的挠性载带上。载带由在上面形成金属导体的薄塑料基板构成,像一种挠性印刷电路。在导体内部末端,引线图形具有和芯片连接焊点相匹配的图形。在导体最外端,由于电测试每个导体和焊点有临时接触,在芯片连接焊点和测试焊盘分布之间,有一段无绝缘膜支撑的长导体,最终会形成TAB封装的外引线。今天【 科准测控】 小编就来介绍一下半导体载带自动焊的分类、特点、优势以及载带自动焊技术的材料、设计要点,一起往下看吧!
1、载带自动焊的分类和特点
大载带自动焊TAB(TapeAutomatedBonding)主要有:Cu箔单层带、Cu-PI双层带、Cu站合剂-PI三层带、Cu-PI-Cu双金属带,其特点见表2-4。
载带自动焊技术的优点:
(1) 载带自动焊结构轻、薄、短、小。
(2) 载带自动焊的电极尺寸、电极与焊区节距均比引线键合小。
(3) 相应可容纳更高的I/O引脚数。
(4) 载带自动焊的引线电阻、电容和电感均比引线键合的小得多。
(5) 采用载带自动焊互连可大大提高电子组装的成品率,从而降低电子产品的成本。
(6) 载带自动焊采用Cu 箔引线,导热和导电性能好,机械强度高。
(7) 载带自动焊比引线键合的键合拉力高3~10倍,可提高芯片互连的可靠性。
(8) 载带自动焊使用标准化的卷轴长带(长100m),对芯片实行自动化多点一次焊接。
2、 载带自动焊技术的材料
载带自动焊技术的关键材料包括基带材料、载带自动焊的金属材料和芯片凸点的金属材料。
(1)基带材料要求高温性能好,与Cu 箔的粘合性好,耐高温,热匹配性好,收缩率小且尺寸稳定,抗化学腐蚀性强,机械强度高,吸水率低。常用的基带材料有聚酰亚胺、聚酯类材料、聚乙烯对苯二甲酸酯薄膜、苯并环丁烯薄膜等。
(2)载带自动焊的金属材料采用Cu箔,因为Cu的导电、导热性能好,强度高,延展性和表面平滑性良好,与各种基带粘结牢固,不易剥离,特别是易于用光刻法制作出精细、复杂的引线图形,又易于电镀Au、Ni、Pb-Sn等金属。
(3)载带自动焊技术要求在芯片的焊区上先制作凸点,然后才能与Cu 箔引线进行焊接,表2-5为芯片凸点的金属材料。
载带自动焊使用的凸点形状一般有蘑菇状凸点和柱状凸点两种。
蘑菇状凸点用一般的光刻胶作掩模制作,用电镀增高凸点时,在光刻胶(厚度仅几微米)以上凸点除继续电镀增高外,还向横向发展,凸点高度越高,横向发展也越大,由于横向发展时电流密度的不均匀性,最终的凸点顶面呈凹形,凸点的尺寸也难以控制。
柱状凸点制作时用厚膜抗腐蚀剂作掩模,掩模的厚度与要求的凸点高度一致,所以制作的凸点是柱状或圆柱状的,由于电流密度始终均匀一致,因此凸点顶面是平的。
从两种凸点的形状比较可以看出,对于相同的凸点高度和凸点顶面面积,柱状凸点要比蘑菇状凸点的底面金属接触面积大,强度自然也高I/O数高且节距小的载带自动焊指状引线与芯片凸点互连后,由于凸点压焊变形,蘑菇状凸点间更易发生短路,而与柱状凸点互连,则有更大的宽容度。
注意:不管是哪种凸点形状,都应当考虑凸点压焊变形后向四周(特别是两邻近凸点间)扩展的距离,必须留有充分的余量。
3、 载带的设计要点
载带自动焊的载带引线图形是与芯片凸点的布局紧密配合的。首先,预测或精确量出芯片凸点的位置、尺寸和节距,然后再设计载带引线图形,引线图形的指端位置、尺寸和节距要和每个芯片凸点一一对应其次,载带外引线焊区又要与电子封装的基板布线焊区一一对应,因此就决定了每根载带引线的长度和宽度。
根据用户使用要求和I/0引脚的数量、电性能要求的高低以及成本的要求等来确定选择单层带、双层带、三层带或双金属层带。单层带要选择5070μm厚的Cu箱,以保持载带引线图形在工艺制作过程和使用中的强度,也有利于保持引线指端的共面性。使用其他几类载带,因有PI支撑,可选择1835μm或更薄的Cu箔。
PI引线架要靠内引线近一些,但不应紧靠引线指端,也不应太宽,以免产生热应力和机械应力。
由于在制作工艺过程中腐蚀Cu箱时有相同速率的横向腐蚀,因此在设计引线图形时,应充分考虑这一工艺因素的影响,将引线图形的尺寸适当放宽,最终才能达到所要求的引线图形尺寸。
科准测控W260推拉力测试机
以上就是小编分享的半导体载带自动焊的分类、特点、优点以及设计要点介绍了,希望大家看完后能有所收获!如果您有遇到关于半导体集成电路、芯片、推拉力机等相关问题,可以给我们私信或留言,科准的技术团队也会为您解答疑惑!还想了解更多信息,欢迎关注!
审核编辑 黄宇
-
芯片
+关注
关注
458文章
51529浏览量
429508 -
集成电路
+关注
关注
5400文章
11691浏览量
364538 -
半导体
+关注
关注
335文章
27975浏览量
225162
发布评论请先 登录
相关推荐
半导体集成电路的可靠性评价
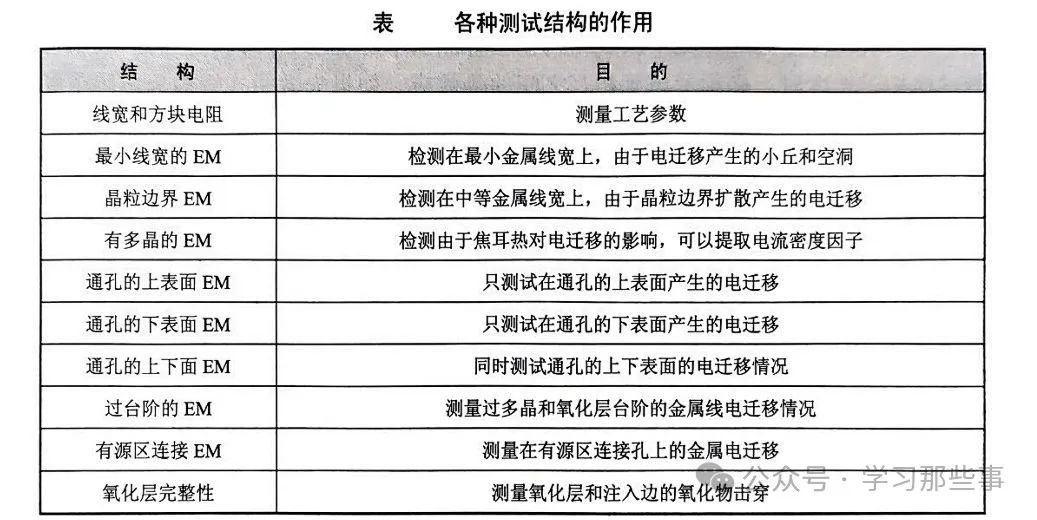
半导体封装材料全解析:分类、应用与发展趋势!
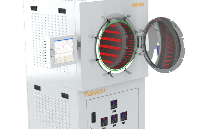
评论