锂离子电池是最早、最成熟、最稳定的锂离子电池型号,其具有制造自动化水平高、电池一致性好、单体能量密度高、散热性好等优点;夲文介绍锂离子电池的制造工艺流程,分析各流程的管控要点及其对电池电性能的影响,为锂离子电池应用及后继锂电池生产线污水处理及其他相关环保设备介绍提供重要的参考。
一、锂离子电池工作原理
1、 锂离子电池主要由正极、负极、隔膜和电解液组成,依靠Li+在正极和负极之间移动来工作。充电时Li+从正极脱嵌,经过电解质嵌入负极,负极处于富锂状态; 放电时则相反。
2、锂离子电池结构锂离子电池主要由正极、负极、膈膜和电解液四大主材组成。同时,一颗完整的18650圆柱形锂离子电芯还包括正负极引线、上下绝缘片、盖板及外钢壳等辅材。
二、锂离子电池制造工艺
1、锂离子电池的制造工艺复杂,工序众多,任何一个环节出现失误都将影响锂离子电芯的性能或带来安全问题,因此,只有严格管控每一道制造工序,才能制造出性能优异和安全有保障的合格电芯。
2、锂离子电池制造前段工艺与管控点电池制造前段工艺包括合浆、涂布、辊压、分切、制片、卷绕、入壳、底焊、辊槽及烘烤10道工序,前段工序的核心是将粉末状的正负极材料制作成一颗卷芯;制片工序应防止极耳虚焊、偏焊、漏焊或极片掉料及绝缘胶偏贴或漏贴等;
3、卷绕工序是圆柱形锂电池成形的重要工艺,由条状形正负极极片和隔膜通过卷绕机卷成圆柱形卷芯,这一工序管控要点在于负极极片必须完全包覆正极极片,而隔膜必须完全包覆负极极片,对工艺精度要求非常高。
4、锂电池的生产工艺比较复杂,主要生产工艺流程主要涵盖电极制作的搅拌涂布阶段(前段)、电芯合成的卷绕注液阶段(中段),以及化成封装的包装检测阶段(后段),价值量(采购金额)占比约为(35~40%):(30~35)%:(30~35)%。差异主要来自于设备供应商不同、进口/国产比例差异等,工艺流程基本一致,价值量占比有偏差但总体符合该比例。
5、锂电生产前段工序对应的锂电设备主要包括真空搅拌机、涂布机、辊压机等;中段工序主要包括模切机、卷绕机、叠片机、注液机等;后段工序则包括化成机、分容检测设备、过程仓储物流自动化等。除此之外,电池组的生产还需要Pack 自动化设备。
三、锂离子电池制造后段工艺:电池制造后段工艺包括注液、焊接、封口、清洗及套膜。注液即通过注液机将电解液注入烘烤后水分要求合格的卷芯,注液完成后,锂电池的四大主材均被应用到电芯之中,注液工序关键在于精控注液量、控湿控温及防水,且需达到电解液能够较好地浸润渗透到正负极极片的效果。
四、锂离子电池筛选工艺:由于电池原材料、生产工艺等差别,电池容量、电压、内阻等性能存在差异,使得电池组性能达不到单体电池水平,使用寿命远短于单体电池,影响电动汽车的使用。电池筛选工艺包括活化、化成、陈化、分选及分容工序;锂系电池分为锂电池和锂离子电池。手机和笔记本电脑使用的都是锂离子电池,通常人们俗称其为锂电池。
五、锂电池结构:锂离子电池构成主要由正极、负极、非水电解质和隔膜四部分组成。目前市场上采用较多的锂电池主要为磷酸铁锂电池和三元锂电池,二者正极原材料差异较大,生产工艺流程比较接近但工艺参数需变化巨大。若磷酸铁锂全面更换为三元材料,旧产线的整改效果不佳。对于电池厂家而言,需要对产线上的设备大面积进行更换。
六、锂电前段生产工艺
1、锂电池前端工艺的结果是将锂电池正负极片制备完成,其第一道工序是搅拌,即将正、负极固态电池材料混合均匀后加入溶剂,通过真空搅拌机搅拌成浆状。配料的搅拌是锂电后续工艺的基础,高质量搅拌是后续涂布、辊压工艺高质量完成的基础。
2、涂布和辊压工艺之后是分切,即对涂布进行分切工艺处理。如若分切过程中产生毛刺则后续装配、注电解液等程序、甚至是电池使用过程中出现安全隐患。因此锂电生产过程中的前端设备,如搅拌机、涂布机、辊压机、分条机等是电池制造的核心机器,关乎整条生产线的质量,因此前端设备的价值量(金额)占整条锂电自动化生产线的比例最高,约35%。
七、锂电中段工艺流程
1、锂电池制造过程中,中段工艺主要是完成电池的成型,主要工艺流程包括制片、极片卷绕、模切、电芯卷绕成型和叠片成型等,是当前国内设备厂商竞争比较激烈的一个领域,占锂电池生产线价值量约30%。
2、目前动力锂电池的电芯制造工艺主要有卷绕和叠片两种,对应的电池结构形式主要为圆柱与方形、软包三种,圆柱和方形电池主要采用卷绕工艺生产,软包电池则主要采用叠片工艺。圆柱主要以18650和26650为代表(Tesla单独开发了21700电池、正在全行业推广),方形与软包的区别在于外壳分别采用硬铝壳和铝塑膜两种,其中软包主要以叠片工艺为主,铝壳则以卷绕工艺为主。
3、软包结构形式主要面向中高端数码市场,单位产品的利润率较高,在同等产能条件下,相对利润高于铝壳电池。由于铝壳电池易形成规模效应,产品合格率及成本易于控制,目前二者在各自市场领域均有可观的利润,在可以预见的未来,二者都很难被彻底取代。
4、由于卷绕工艺可以通过转速实现电芯的高速生产,而叠片技术所能提高的速度有限,因此目前国内动力锂电池主要采用卷绕工艺为主,因此卷绕机的出货量目前大于叠片机。
5、卷绕和叠片生产对应的前道工序为极片的制片和模切。制片包括对分切后的极片/极耳焊接、极片除尘、贴保护胶纸、极耳包胶和收卷或定长裁断,其中收卷极片用于后续的全自动卷绕,定长裁断极片用于后续的半自动卷绕;冲切极片是将分切后极片卷绕冲切成型,用于后续叠片工艺。
6、在锂电封装焊接方面,联赢、大族、光大的主流激光技术集成应用厂家均有所涉及,能够满足需求、无需进口。
八、锂电后段工艺流程:锂电后段生产工艺主要为分容、化成、检测和包装入库四道工序,占生产线价值量约35%。化成和分容作为后段工艺中最主要环节,对成型的电池进行激活检测,由于电池的充放电测试周期长,因此设备的价值量最高。化成工艺的主要作用在于将注液封装后的电芯充电进行活化,分容工艺则是在电池活化后测试电池容量及其他电性能参数并进行分级。化成和分容分别由化成机和分容机通常由自动化分容化成系统完成。
九、锂电Pack工艺:动力电池组系统是将众多单个的电芯通过串、并联的方式连接起来的电池组,综合了动力和热管理等电池硬件系统。Pack是动力电池系统生产、设计应用的关键,是连接上游电芯生产和下游整车的应用核心环节,通常设计需求由电芯厂或汽车厂提出,通常由电池厂、汽车厂或者第三方Pack厂完成。
1、锂电池Pack产线相对简单,核心工序包括上料、支架粘贴、电焊、检测等工艺,核心设备为激光焊接机以及各类粘贴检测设备。目前,各大锂电设备厂商在此领域的自动化集成布局较少,而大族激光、联赢激光等激光设备厂商由于在激光领域的绝对优势,在Pack设备领域占有率较高。
2、目前Pack生产的自动化比例相对较低,是因为目前的新能源车单款车销量都不够大,上自动化生产线的成本较高。
十、磷酸铁锂和三元电池工艺:目前国内主流动力锂电池的正极材料分为磷酸铁锂和三元两大种类。其中磷酸铁锂是目前最安全的锂离子电池正极材料,其循环寿命通常在2000次以上,再加上由于产业成熟而带来的价格和技术门槛的下降,使得很多厂商出于各种因素考虑都会采用磷酸铁锂电池。然而磷酸铁锂电池在能量密度方面则存在明显的缺陷,目前磷酸铁锂电池龙头比亚迪磷酸铁锂单体电芯能量密度为150Wh,2017年底比亚迪预计将能量密度提升到160Wh,理论上磷酸铁锂能量密度很难超过200Gwh。
1、三元聚合物锂电池是指正极材料使用镍钴锰酸锂的锂电池,镍钴锰的实际比例可以根据具体需要进行调整。由于三元锂电池具备更高的能量密度(目前宁德时代等动力电池一流大厂三元锂电池能量密度普遍能达到200Wh/kg-220Wh/kg,业内预计到2020年三元电池单体电芯能量密度将达到300Wh/kg的水平),乘用车市场开始转向三元锂电池,而在安全性要求更高的客车上,磷酸铁锂则更受青睐。随着全电动乘用车的发展,三元锂电池正在占据越来越重要的位置。
2、两种材料的能量密度和成本有差异,不同的汽车、不同的车企有不同的选择。二者在生产工艺流程上大致相同,区别主要体现在材料的使用和配比上不同、具体工艺参数差异较大,设备无法共线生产,且单纯改造切换产能的成本较高(三元材料对真空除湿等要求严格,之前的磷酸铁锂生产线基本没有除湿要求),因此多家电芯厂在产能规划中会同时布局、分别采购设备。
审核编辑 :李倩
-
锂电池
+关注
关注
260文章
8098浏览量
169940 -
能量密度
+关注
关注
6文章
287浏览量
16470 -
三元电池
+关注
关注
6文章
169浏览量
9239
原文标题:锂电池制造工艺技术解析
文章出处:【微信号:智享新动力,微信公众号:智享新动力】欢迎添加关注!文章转载请注明出处。
发布评论请先 登录
相关推荐
锂离子电池的设计
锂离子电池的基本组成及关键材料
锂离子电池的的原理、配方和工艺流程
锂离子电池原理及工艺流程
锂离子电池原理及工艺流程
锂离子电池原理及工艺流程简介
锂离子电池回收处理工艺流程图
探究锂离子电池工作原理与制造工艺
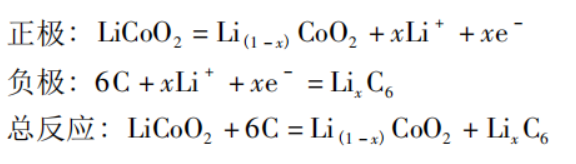
评论