摘要
进入规模化制造时代,电池行业的科技属性逐渐回归到制造属性。头部锂电厂商技术趋同趋势下,竞争核心将体现在企业的制造能力上。
随着电动化与储能市场需求的大规模启动,终端对能量密度、安全性、技术指标等提出更高的要求,实现锂电产业的智能制造,提升规模化、高质量交付水平迫在眉睫。
根据工信部发布的数据,2022年全国锂电池产量750GWh,仅电芯环节规划项目就达40余个,规划总产能超1.2TWh,规划投资4300亿元,TWh时代近在咫尺。
需要引起重视的是,锂电产业作为一个巨大的赛道,虽然历经了十几年的飞速发展,但是制造底层的信息化、数字化、智能化依旧薄弱,制造水平仍有较大的上升空间。
蜂巢能源工艺装备中心负责人、上海章鱼博士总经理尹东星认为,当前时代背景下,电池行业的科技属性逐渐回归到制造属性,所有的高科技在投入量产后将迅速平民化。
“进入规模化制造时代,头部电池企业的技术水平已经逐渐趋同,未来电池企业的核心竞争力将体现在制造能力上,包括质量控制能力、成本控制能力和智能化水平。”
同时,随着动力电池规模化演进,也将对电池制造的工艺路线产生深刻影响。
目前来看,动力电池领域存在方形卷绕、方形叠片、圆柱卷绕、软包叠片等多种制造工艺。其中,方形叠片在电芯长薄化趋势下实现市场快速渗透。随着锂电头部厂商掀起智能制造跃迁,也将牵动主流电池制造工艺的变革与升级。
高工锂电智能制造峰会期间,高工锂电与蜂巢能源工艺装备中心负责人、上海章鱼博士总经理尹东星进行了深度对话,围绕TWh时代动力电池智能制造挑战、蜂巢能源智造战略部署以及章鱼博士的布局等话题进行了详细探讨。
规模化制造能力将成竞争关键
“如果说,十年前,电池行业靠产品技术取胜;五年前,电池行业靠差异化定位取胜。那么到了TWh时代,电池行业将是得规模化制造能力者得天下。”
这是尹东星对于接下来动力电池企业竞争的研判。
如其所说,过去数年间,头部动力电池企业通过材料体系优化和系统结构创新,不断探寻向上的技术边界,目前基本抢占了全球电池技术创新的制高点。
与此同时,终端多样化应用场景对于产品性能的诉求,包括高安全性、高能量密度、长循环寿命、高功率快充等要求也驱动着电池产品在细分领域往更高性能突破。
总体而言,头部动力电池企业的技术水平正在趋同,未来最大的差异将体现在规模化制造能力上。
而当前,动力电池行业产能扩张的主要矛盾,来自于大规模扩产的需求与相对落后的生产线水平。尤其是随着自动化程度要求越高,越需要增强过程检验,但检验点越多,带来的是整线OEE越来越低。
根据测算,按现阶段投入1TWh电池厂75%OEE来算,每年制造损失将高达2500亿元,而这笔损失将足够再新建一个1TWh电池工厂。
尹东星指出,规模化制造能力是电池行业最核心、最基础的竞争力,是把20多个工序连续不断的每天重复上百万次,造出来的电池需要一样性能、一样精度、一样循环衰减、一样安全。
“规模化制造不是靠堆工位、无限制增加检测点,而是对产线进行极简化、集成化和智能化升级,以此实现检测点不断减少,最后实现消灭检验点。”
动力电池规模化制造要实现极致安全、极致效率、极致成本,其根本是要将动力电池由工艺品转变为工业品,从精益生产的“一个流”管理理念转向规模化制造的“多个流”并行处理。
基于对智能制造的理解,蜂巢能源通过工厂规划、产品工艺设计、设备管理、制造管理、品质管理、厂内仓储物流等六大主线来推动智能制造的落地。通过引领开发核心装备,突破锂电制造效率极限,并真正将人工智能充分融入整线,打通全过程数据链路,实现“用户侧-生产侧”的双向进化。
飞叠技术突破制造效率极限
围绕动力电池核心装备工艺革新与制造效率的挑战,过去几年,蜂巢能源已经做了一系列积极探索。
为提升规模交付能力,蜂巢能源“飞叠”技术应运而生。
蜂巢能源高速叠片1.0技术于2019年首次发布。随着技术和工艺的迭代,高速叠片技术核心优势体现在质量控制能力、优越的产品性能和整线智能化水平。
为进一步改善成本和效率,2022年蜂巢能源发布自主研发的高速叠片3.0:“飞叠”技术,其生产效率也从0.6秒/片提升至0.125秒/片,相比与第二代技术,“飞叠”技术实现单位占地面积减少45%,叠片工序单位投资减少53%。目前蜂巢能源正研发第四代叠片技术,叠片效率可达0.06秒/片,单台叠片机可实现1GWh产能。
在生产质量上,为了确保电池的安全,蜂巢能源一直采用最高端的陶瓷隔膜。在生产过程中,“飞叠”技术对电池内部每一片隔膜和极片的尺寸、定位公差、表面缺陷都是使用AI视觉技术100%全检,并根据检测结果在线实时修正,实现产品质量自适应调整。
作为新开辟的电池形态路线,相比于圆柱卷绕和方形卷绕工艺,蜂巢能源“飞叠”技术正体现独特优势。
一般来说,一条16ppm的卷绕型生产线会配备5-6台卷绕机,相同效率之下需要配置18-20台传统叠片机。如今在结合产品结构创新与叠片工艺的自主创新下,飞叠效率已逐步追平卷绕,最新数据来看,一条16ppm的短刀装配线只需要6台飞叠设备。
效率趋同之下,叠片工艺空间利用率更高,原理一致性、安全性更好。
借助“飞叠”技术,蜂巢能源也从动力领域快速切换到了储能领域。由于储能市场对产品的循环寿命要求更高。飞叠技术极片与隔膜完全复合保证了正负极反应界面在长寿命循环后的一致性,加上产品内部零缺陷的制造,能够为储能市场提供更高能量密度,更安全、更长循环寿命、更稳定内部结构的电芯。
在“飞叠”技术加持下,蜂巢能源最新推出的龙鳞甲电池不仅实现了热电分离,保证最大的安全系数,体积利用率更是达到了行业最高的76%,使磷酸铁锂体系的电池包达到了与三元电池包相同的续航里程。
尹东星透露,目前飞叠技术已成功导入蜂巢能源盐城、上饶等多个量产基地。
打造车规级AI工厂
推进锂电产业底层信息化、数字化和智能制造是解决规模交付的关键。
蜂巢能源提到,面向新周期的动力电池智能制造,要有标准和整体设计,专注于设备自动化、单项信息化或者专注某一点上数据分析,不足以支撑整体智能制造的发展。
在战略层面,蜂巢能源已经将AI智能制造战略作为四大子战略之一,并搭建一整套的实践体系,集中体现在蜂巢能源数智化“1441”战略:
“1”即代表一套数智化标准,两个“4”分别代表打造四大数字协同与四类领域的智能化,包括从试验到量产的研发协同,从寻源到齐套的供应链协同,从订单到交付的运营协同,从销售到回款的业财一体;以及装备智能、数据智能、平台智能、运营智能。最后的“1”则是一套支撑体系,涵盖AI蜂能联盟、工控智能硬件实验室、工业物联网平台等。
蜂巢能源目前已于金坛打造出首个数字孪生工厂,并凭借其车规级AI能力获得2022年世界智能制造大会的十大科技进展奖。
尹东星表示,蜂巢能源在金坛打造的数字孪生工厂,基于车间、环境、设备、物流、员工进行建模和仿真。通过IoT技术采集相关设备的信号,以及通过数据中台连接制造系统和管理系统,使得设备、物流状态、故障情况相关数据可完美孪生、追溯及再现,从而更好解决工厂生产出现的问题。
从工厂的架构体系变化来看,在智能制造赋能下,传统的智能制造架构已过渡到新型的端边云结合的架构。在这个转变中,核心要素并非硬件的更迭,而是经由底层的OS将硬件协议完全打开,从而实现通讯的无缝衔接和边缘端的智能处理。
作为蜂巢能源锂电产业智能化的“操盘手”,上海章鱼博士智能技术有限公司开展一系列前瞻性布局。
目前,上海章鱼博士在过程AI视觉检测、设备智能控制、大数据分析与自适应控制等领域打造了大量应用场景。针对传统数据传输效率无法满足动力电池生产对设备控制速度的要求,章鱼博士引入边缘计算及工业OS,在设备实时控制方面做了大量创新,开发出了线体智能控制器等边缘智能硬件。
同时,章鱼博士还构建了一整套AI大数据企业平台,基于自研智能硬件,融合AI深度学习+机器视觉算法,提供低代码AI大数据企业平台,实现对动力电池缺陷在线实时检测、大数据实时监控及企业其他场景AI应用。
未来,蜂巢能源也将构建章鱼型操作系统,打通硬件协议与通讯总线,实现生产制造的智能化。在底层硬件与软件实现融合,实现现场层、IDOS、应用层的联通,并借助产品化的应用与场景,服务于整个锂电产业。
在工厂智能化升级方面,蜂巢能源还提出了“工厂代差”的概念,通过不断优化核心装备工艺,保持先进的制造技术引领,打造标准化车规级AI智能工厂,在智能制造道路上持续探索,保证在全球范围内新建基地制造水平的持续升级。
审核编辑:刘清
-
锂电池
+关注
关注
260文章
8098浏览量
169943 -
动力电池
+关注
关注
113文章
4533浏览量
77612 -
OEE
+关注
关注
0文章
10浏览量
6242
原文标题:蜂巢能源智造方法论:“规模化+数智化”角力TWh时代竞争
文章出处:【微信号:weixin-gg-lb,微信公众号:高工锂电】欢迎添加关注!文章转载请注明出处。
发布评论请先 登录
相关推荐
大冲能源与和达能源合作浙江传化综合能源站项目
广汽埃安携手小马智行打造Robotaxi规模化量产车型
蔚来能源武汉制造中心规模化量产
江波龙自研主控芯片实现规模化导入
十字路口的全球化,中国企业的破局之道
助力企业数字化转型,数势科技发布行业首部指标管理专著!
IBM陈旭东:携手IBM加速 AI 规模化应用,解锁企业新质生产力
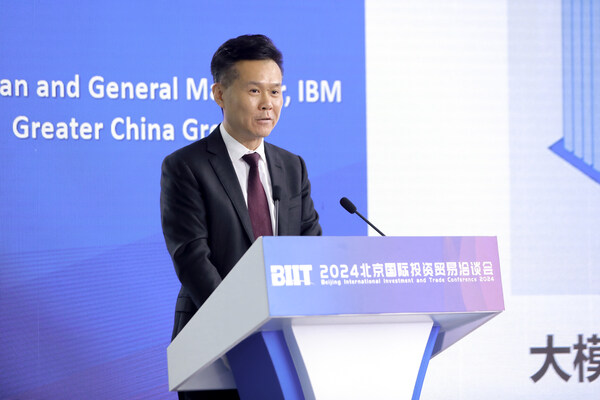
比斯特自动化|新能源行业降本攻坚:从自动化升级推动规模化生产新篇章
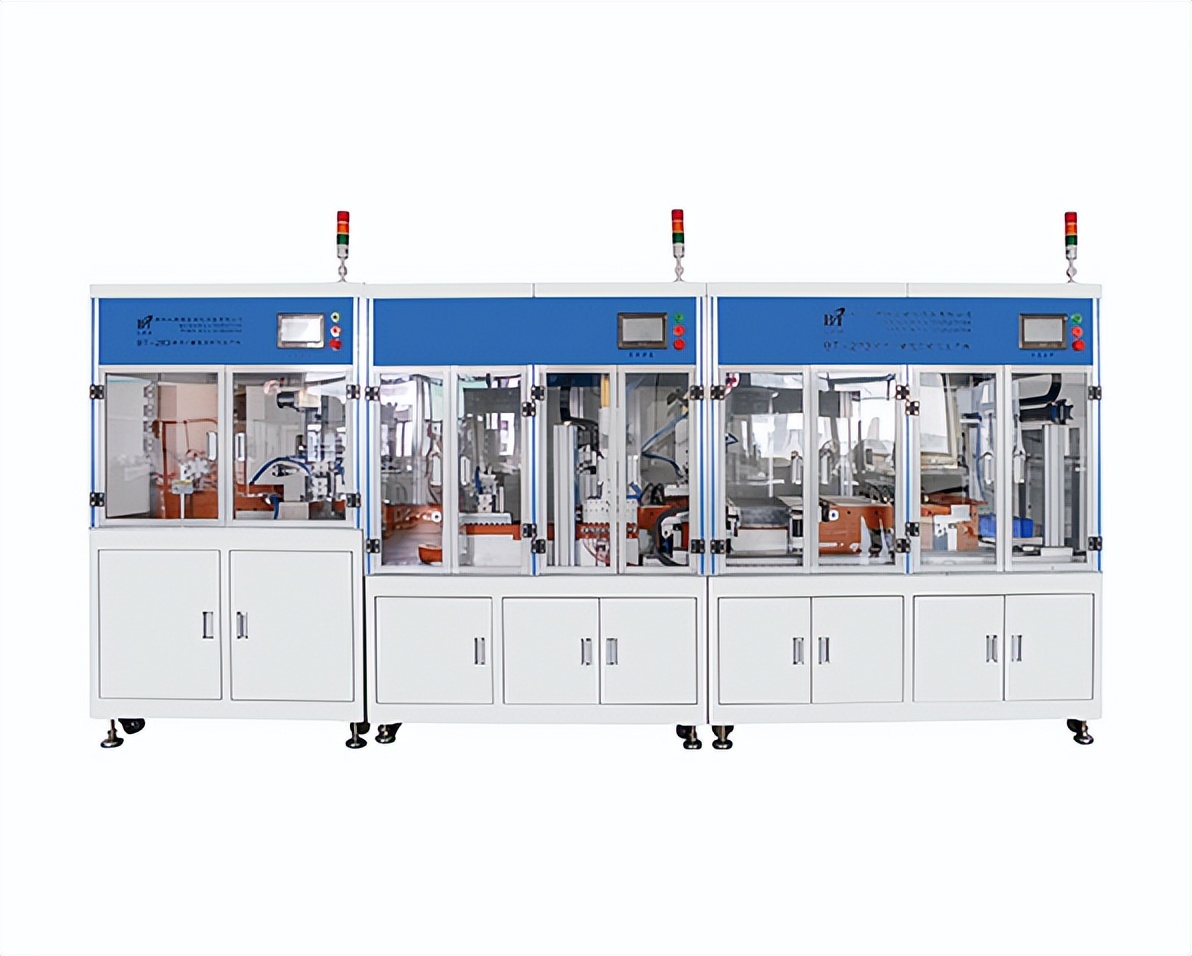
声通科技:高标准化及可扩展的产品能力,助力公司实现规模化经营
蜂巢能源第40万套PHEV电池包下线
迎接数智时代:数字经济引领可视化转型
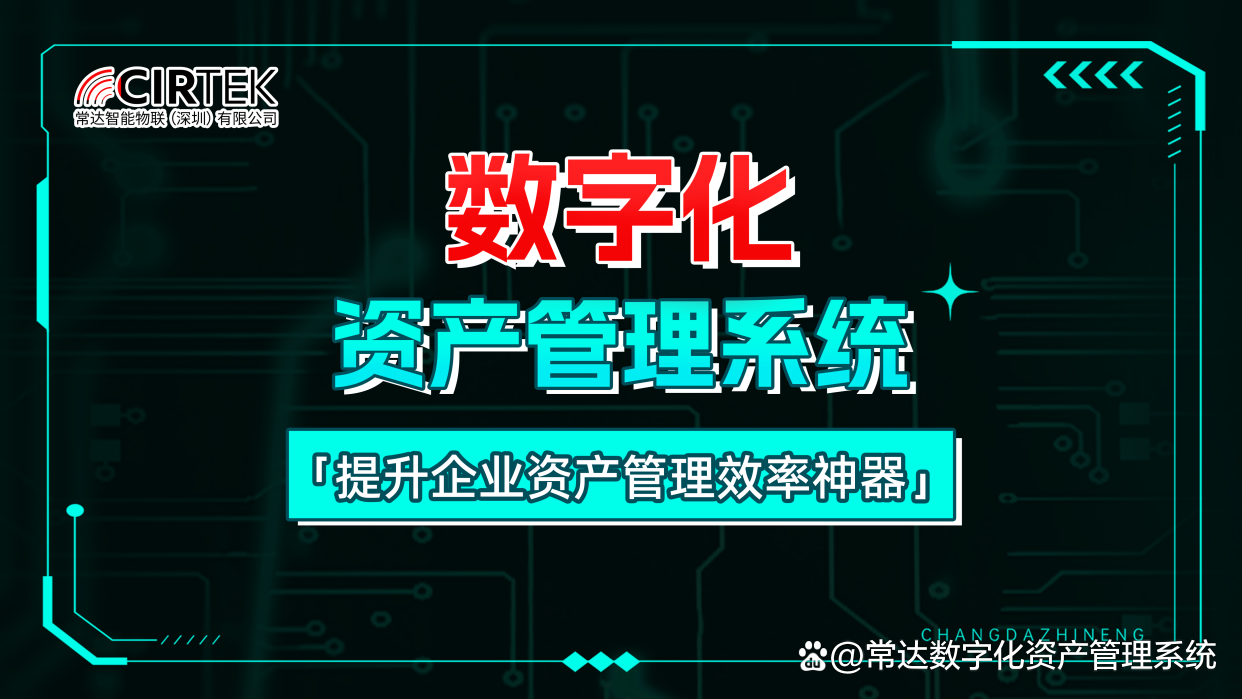
评论