α-氧化铝(下称氧化铝)导热粉体因来源广,成本低,在聚合物基体中填充量大,具有较高性价比,是制备导热硅胶垫片最常用的导热粉体。氧化铝形貌有球形、角型、类球形等,不同形貌对热界面材料的加工性能、应用性能、成本等有不同影响,加之不同粒径的影响,在体系中会形成一定的孔隙,影响导热界面材料的导热系数。本文将从以下几个方面探讨不同形貌、不同粒径的氧化铝导热粉体的搭配工艺,为制备高导热硅胶垫片提供参考。
1、同等粒径相同添加量下,不同形貌
选取5μm和45μm的球形、类球形氧化铝形、角形氧化铝在添加量75%下测试其对导热硅胶垫片加工粘度的影响,相同粒径球形氧化铝的加工粘度最小,角形氧化铝加工粘度最大;相同形貌粒径越大,加工粘度越低。主要是因为同等粒径下,球形氧化铝表面能越小,球的表面流动性越好,与基体搅拌成膜均匀,体系粘度就越低,而角形氧化铝形貌不规则,其颗粒的表面能大,颗粒之间越易粘附在一起,粘度就越大;而在相同相貌下,粒径越大,吸油值越小。
2、同等粒径不同形貌下,不同添加量
选取45μm类球形氧化铝形、球形、角形氧化铝,分别在75%、80%、85%添加量下测试对导热硅胶垫片导热系数的影响,在同等添加量下,75%添加量时角形氧化铝制备的导热硅胶垫片的导热系数较高。添加量在80%和85%时,类球形氧化铝形氧化铝制备的导热硅胶垫片导热系数较高。在添加量较少时,随着添加量增加,三种形貌氧化铝制备的垫片导热系数不断升高。由于角型氧化铝比表面积大,在基体中形成的导热网络会更多,因此垫片的导热效果较好。当添加量增加,由于类球形氧化铝是单晶颗粒、转化率高、颗粒表面光滑,导热系数最高,虽然球形氧化铝球形度好,但是转化率较低并且颗粒表面粗糙,导致导热系数较低。
3、同等形貌不同添加量氧化铝导热粉体,在不同复配比例
考虑最佳性价比和粉体颗粒堆积原理,选取45μm球形氧化铝、45μm类球形氧化铝和5μm角型氧化铝以2:2:1,2:1:1,1:2:1,1:1:1复配分别在80%、85%、90%的添加量下对导热硅胶垫片导热系数的影响。相同复配比例,随着添加量增加,四种复配粉体填充的垫片导热系数不断增加,这是由于随着粉体添加量增加,颗粒之间的接触点越多,逐渐形成致密导热网络,因此导热系数增加。另外,由于类球形氧化铝的转化率高,导热系数高,因此其比例较大,导热硅胶垫片导热系数的提升越明显。
4、同等添加量及不同复配比例对复配氧化铝导热粉体堆积性能的影响
选取45μm球形氧化铝、45μm类球形氧化铝和5μm角型氧化铝以2:2:1、2:1:1、1:2:1、1:1:1比例复配,球形氧化铝、类球形氧化铝与角形氧化铝比例1:2:1时堆积密度最大,这是因为颗粒之间的缝隙被相互填充,空隙小,密度大。
另外制作导热硅胶垫片时,常常会遇到粘膜、表面掉粉问题。造成这一问题原因之一是粉体与硅油相容性差,油粉粘度高、混合不均匀,使得垫片内聚强度低,分子间作用力小于垫片表面与离型膜的吸附力,导致垫片剥离时出现粘膜、表面掉粉现象。如何解决这个问题?
导热剂等产品可较好解决这样问题。与普通导热粉体不同的是,这类导热粉体采用我司独有的改性技术制备而成,增强了粉体与硅油之间的相容性,确保硅胶中即使填充了大量该导热粉体,仍能分散均匀,使导热硅胶垫片具有较高的内聚强度,从而改善垫片撕膜时粘膜、表面掉粉现象。
导热硅胶垫片时,由于粒径太粗,导致垫片有针眼。怎么办?
通过限制高导热粉体最大粒径,同时配以复合搭配和表面改性技术,研发了一款高性能导热粉体。该产品堆积密度大,应用时可以降低复合体系的空隙,不仅能避免体系出现针眼,还能提高材料导热系数。另外,改性技术降低了粉体表面极性,改善了粉体与树脂的相容性,使体系易排泡。
综上,要制备高导热率导热硅胶垫片,需要寻求合适的导热粉体原料、粉体形貌,确认粒径级配等,非一步即可完成。东超新材料在氧化铝、氢氧化铝等的应用研究已经有10+年的经验,可根据客户具体的产品指标、工艺特色、应用目标,提供个性化的导热阻燃高分子材料解决方案。
审核编辑黄宇
-
导热
+关注
关注
0文章
306浏览量
13017 -
硅胶
+关注
关注
0文章
44浏览量
3673
发布评论请先 登录
相关推荐
导热氧化铝粉(DCA-S)增强锂电池散热性能的机理与效果分析
导热硅胶片在无线充电器中的应用
氧化铝隔断粉在氧化铝陶瓷基板的应用
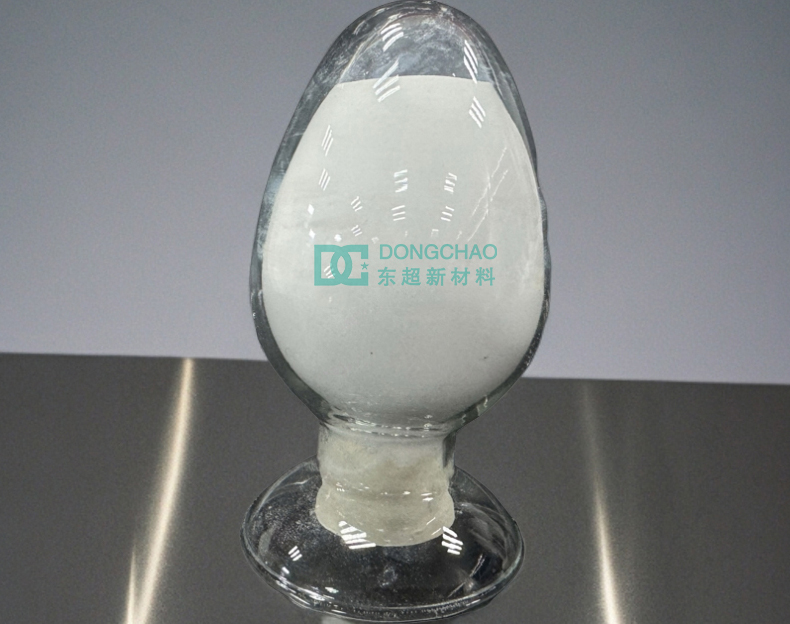
汽车ADAS系统高效散热,球形氧化铝导热粉体解决方案
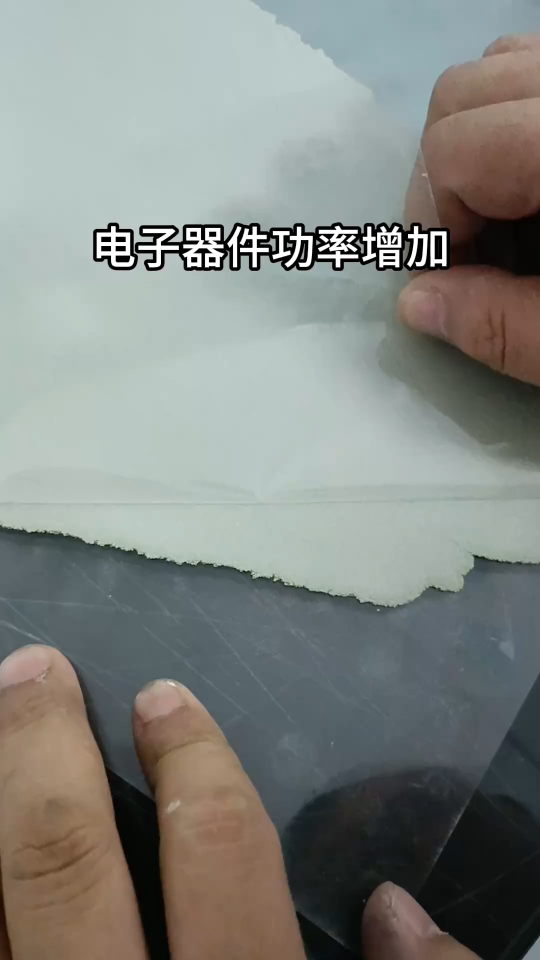
探索新能源汽车电池三大散热方案及氧化铝导热粉导热界面材料的应用
5G时代下,无机填料氧化铝导热粉在覆铜板市场的发展趋势与重要性
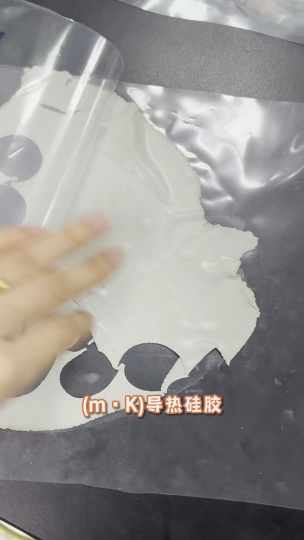
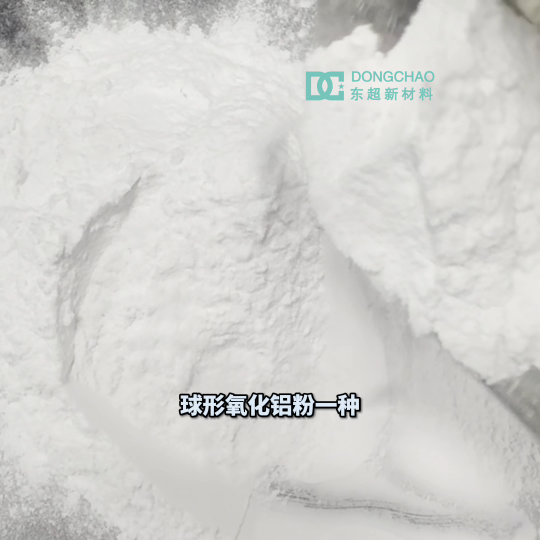
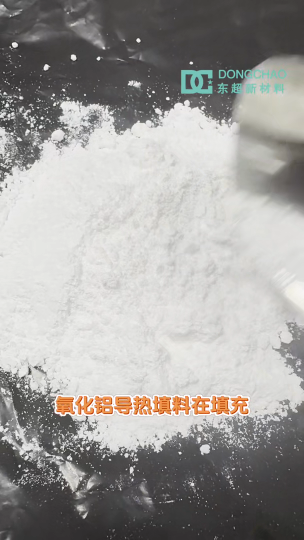
评论