增强现实技术是元宇宙重要的人机交互平台,其中光学成像部件和微显示屏是成像质量的关键。目前有五种微显示技术:硅基液晶、硅基 OLED、硅基 micro LED、DLP 显示以及激光扫描振镜等。本文将着重介绍不同技术微显示屏的组成结构、工艺流程、硅基驱动方式方法、发展现状以及面临的挑战。在硅基驱动的部分,将从像素驱动的不同电路以及不同驱动电路的优缺点入手,分析不同显示技术硅基部分的设计和指标挑战。并对目前不同技术所能达到的指标进行了汇总比较。硅基背板的设计关注点和发展趋势也将得到讨论。在本文的最后对不同微显示芯片的应用场景和发展进行了讨论。
一、引 言 |
增强现实概念最早出现在 1968 年,但受制于显示和光学技术,一直未能普及。1990 年代,美国军方要求提升空军作战效率,才开始对显示屏的更新换代提出明确要求。一些公司开始了对基于硅基的液晶屏的研发。2012 年谷歌推出了基于硅基液晶(LCoS)和棱镜光机的轻便式单目 AR 眼镜,使得更多的机构和消费者对 AR 眼镜产生了浓厚的兴趣。随着增强现实的应用场景和需求越来越多,相应的对 AR 眼镜的要求也就越来越高。如需要长时间佩戴的增强现实(AR)眼镜需要满足体积小重量轻并且待机时间长的需求。而户内或者是工业场景应用中,则对分辨率、对比度和可视角有更严苛的要求。为了构建更好的 AR 系统,AR 眼镜中的不同模块,如处理器、光机和微显示屏也引起了关注。如处理器从前期的直接用现成的通用处理器,到现在的针对 AR/VR 的专用处理器。光机从早期的棱镜光学到现在的光波导技术,显示从 LCoS 一枝独秀(Google glass 1、Hololens 1, Magic leap 1 等)到现在的 LCoS、硅基有机发光二极管(OLED)(INMO AIR)、激光扫描振镜(LBS)(HOLOLENS2)和微型发光二极管(MICRO LED)(OPPO Air Glass)等多种微显示技术都得到了应用和推广。也有厂商通过提高制造精密度,采用了高温多晶硅液晶显示(HTPS LCD)技术来达到 AR眼镜的要求(EPSON)。
LCoS 脱胎于 LCD 技术,借助成熟的半导体工艺和液晶产线,发展迅速,有工艺成熟成本较低等特点。而后硅基 OLED 随着工艺和制造逐渐成熟,凭借其高对比度的优势备受青睐。但是硅基 OLED 的寿命、亮度都是瓶颈,使其在户外应用场景一直受限。其后 Micro LED 凭借其高亮度和更长的预期寿命被认为是更适合于 AR 的微显示技术,但是由于制造工艺还未成熟,良率很低,通常认为离量产还有一些时间。另外,由于微软在 HOLOLENS 2 里面大胆采用了 LBS 微显示技术,使得这一技术得到一些产家的青睐。
对于时下流行的光学和显示技术,Bernard Kress 在其著作第七章中针对不同微显示技术的发光方式、发光效率和显示效果进行了详尽介绍,其中也介绍了市场上的主流产品所采用的技术。Shin-Tson Wu 等人在文献中对不同微显示器件的材料特性和器件结构做了详细论述。文献对不同显示技术的显示原理和整个光学系统的搭配做了介绍。文献则是对不同技术进行了分类和指标对比。然而,微显示技术,从制造流程或者说设计来看,又可以分为前道的硅基部分和后道的发光层部分。如LCoS可分为硅基背板和液晶盒子,OLED-on-Silicon 可以分为硅基背板和上层的有机发光层。本文将从硅基背板的角度对不同的微显示技术进行介绍。即从应用场景出发,针对不同应用对微显示的不同要求,从硅基背板设计的角度对不同技术进行分类阐述。这对 AR 眼镜的系统性设计将提供有效帮助。
基于这一思考,本文从第二部分到第五部分,分别介绍 LCoS 技术、硅基 OLED 技术、硅基 micro LED 技术、DLP 和 LBS 技术的器件结构、硅基电路设计架构和发展趋势。在第六部分将对各类技术进行对比分析。
二、硅基液晶(LCoS) |
2 .1 LCoS 的器件结构
LCoS 一开始是以小型化的 LCD 为目标,但是随着技术的进步,还发展出了丰富的应用,如全息、光通讯和光镊等。尽管如此,LCoS 从结构上看,依然是最初的硅基加液晶盒子方式。跟薄膜晶体管(TFT) LCD 的最大区别就是用单晶硅晶圆取代了 TFT ARRAY。LCoS芯片的剖面图如图 1,除了硅基背板,还包含由框胶、液晶以及 ITO 玻璃所构成的液晶盒子。
其简要生产流程如图 2。
▲图1:LCoS 结构图
▲图2:LCoS 生产流程图
在显示应用中,可以根据制造工艺分为带滤色片的空间彩色 LCoS 和不带滤色片的时序彩色 LCoS。带滤色片的 LCoS 可以直接使用白色光源,数据类似传统 LCD,因此系统架构较为简单。但由于滤色片对光的损耗可以达到三分之二以上,因此系统光效损失较大。而采用时序彩色的方案由于是通过控制不同颜色光源的时序来实现混色,不需要滤色片,可以大幅度的提升光效。时序彩色方案的另一个优势是因为不需要三个不同颜色的子像素来混色形成最终的像素,像素密度提高,同样分辨率的屏可以做的更小。因而现在市场上的大部分LCoS 屏都是时序彩色方案,以满足 AR 眼镜微型化的需求。
LCoS 的成盒方式也与 LCD 一样有多种选择。如配向方式有摩擦配向、无机配向和光配向等。采用的液晶也有多种,有响应迅速的 TN 液晶,也有高对比度的 VA 液晶,以及近年来备受关注的蓝相液晶。从显示的角度看,出于对高对比度的追求,比较常用的是无机配向和 VA 液晶的组合。在后道工艺的支持下,LCoS 也能达到较高的对比度,如南京芯视元针对 HMD 的 LCoS 对比度可以达到 1500:1,Sony 和 JVC 针对高端大屏投影的 LCoS 对比度分别做到了 4000:1 和 5500:1 。
2.2 LCoS 的硅基背板设计
LCoS 硅基背板的设计,按像素驱动方式分,可以分为模拟像素驱动和数字像素驱动,如图 3 所示。
▲图3:LCOS 的模拟像素驱动电路和数字像素驱动电路
可以看出模拟像素驱动比较类似传统 TFT 驱动方式,先通过 DAC 将数字视频信号转换为模拟灰阶电压,而后传输到液晶层通过控制液晶的不同翻转程度来控制光的反射。而数字像素驱动则通过将原视频信号分为不同的数字子帧,利用脉冲宽度调制来控制液晶的灰阶显示 。在一个时间周期内,液晶上的等效的灰阶电压为 :
对于时序彩色 LCoS,采用红绿蓝三色光源分时照射到屏幕上。如果是数据通过单个晶体管和电容直接写入,那么光源只能在数据完全写入以后照射,有效显示时间短,亮度低。因此为了提高光效,一般采用一个缓存帧来预存数据,显示上一帧图像的同时写入下一帧的图像数据,增加光源照射时间和亮度。由于时序彩色的数据流与常见视频源的数据流不太一样,所以一般需要一个驱动 IC 来对数据进行处理。为了进一步减小智能眼镜的体积,也可以采用更小的工艺节点将驱动 IC 部分集成到显示屏里。这样能更好的满足可穿戴的要求,只是成本将大幅上升。
对于一些特殊的高分辨率的应用场景,需要 4K 甚至 8K 的分辨率。此时如果依然按原先的方式直接叠加更多的像素,屏的面积会大幅增大,走线长度大幅增加,信号质量和数据带宽将成为挑战。因此也出现了通过抖动来提高视觉分辨率的做法。即屏幕的物理分辨率并没有达到要求的数值,但是通过时序上的抖动,不同子帧的时间叠加效应形成一个视觉上的高分辨率屏,也可以通过两个屏幕的光学错位来实现。但是由于抖动算法会增加功耗,在可穿戴的应用中并不一定适合。
总体来说,LCoS 的发展,主要是根据应用需求不断演进。早期受限于工艺和应用,一般是低分辨率大像素的屏(720P 以下)。随着 AR 光学的发展,开始对中等分辨率(720P 和1080P)高光效低功耗的屏产生需求。激光电视的推广使得高分辨率高对比度高可靠性成为考虑的焦点(4K 和 8K)。而 AR 市场的普及又使得极小尺寸低功耗的显示屏成为一大趋势。在小尺寸方面,有减小分辨率和减小像素尺寸两种方式。目前有报道的 LCoS 最小像素尺寸是 3.015μm, 来自 Compound Photonics 公司。从设计角度,几种产品采用的系统架构和设计关注点都会有区别。
三、硅基 OLED |
3 .1 硅基 OLED 的器件结构
硅基OLED从结构上也可以分为两种,一种是采用白光发光层加滤色片的结构,如SONY、京东方 和弗兰霍夫研究所等,其基本结构如图 4;一种是直接做 3 种不同发光材料的结构。采用第一种结构主要是为了规避蓝光 OLED 材料的寿命问题。不管哪一种结构,硅基 OLED 的亮度问题也是一直被诟病的缺点之一。文献的研究发现,同样的 OLED 器件结构下,可以通过适度的调高工作电压并降低占空比的方式提高显示亮度并延长器件的使用寿命。另外,也有很多基于堆叠发光层提高 OLED 亮度的研究。有研究认为,三层堆叠、双层堆叠的 OLED 和单层 OLED 的电流出光比大约为 31。
▲图4:OLED 器件结构
硅基 OLED 的后道工艺也是从硅基晶圆开始,如图 5,先进行发光层的蒸镀,而后进行密封处理和玻璃盖板贴合,最后切割和封装成单独的芯片。为了进一步提高发光效率和亮度,SONY 于 2019 年还提出了使用微透镜增加出光率的工艺。
▲图5:硅基 OLED 工艺流程图
3.2 硅基OLED的背板设计
OLED 材料是电流驱动器件,像素驱动也可以分为模拟像素驱动和数字像素驱动,如图6。对于硅基 OLED 背板来说,模拟像素驱动指的是显示信号通过 DAC 转换为模拟电压之后,通过驱动像素的 MOS 管再转换为 OLED 器件所需要的电流。这种方法需要的 MOS 管少,但是因为屏幕亮度基本和像素电流成正比,而像素和像素之间的驱动 MOS 管的开启电压 Vth 在制造过程中会形成偏差,使得屏幕出现亮度均匀性问题。大屏通常会另外使用算法 IC 来补偿这一亮度不均匀,然而对于微显示来说,由于像素和像素之间的亮度差异是由电流差异造成的,并且这种电流差异十分微小(nA 级别),难以片外补偿,所以通常采用像素内补偿的方式来改善屏幕的亮度均匀性。此外,由于低灰阶情况的像素电流都在 nA 级别,随环境和工艺变化明显,灰阶精度很难保证,所以也有采用 10bit 的 DAC 来完成 8bit 灰阶的设计。硅基 OLED 的数字驱动也可以采用 PWM 的方式,但是此时的脉冲宽度根据需要的显示亮度来计算。文献都采用了这种方式。PWM 驱动方式在灰阶调节和对比度上表现更好,但是需要的数据带宽要更高。
▲图6:硅基 OLED 的模拟驱动和数字驱动
硅基 OLED 的背板发展趋势还有一个特点,就是有超高分辨率高帧率大尺寸屏和低分辨率低帧率低功耗两个截然不同的发展方向。高分辨率大尺寸屏主要针对一些对显示要求高的 AR 以及最近流行的 PANCAKE 光学架构的 VR。而低分辨率低功耗主要应用在野外需要电池续航时间长的场景。Philipp Wartenberg 甚至在 2022 年的 Displayweek 上提出了点亮功耗只有 1mW 的双色 OLED 屏。
四、硅基 MICRO LED |
4 .1 硅基 MICRO LED 的器件结构
由于 MICRO LED 在发光效率、寿命和工作温度上都有优势,一直备受关注。与 LCoS 和硅基 OLED 不一样的是,目前 MICRO LED 的制造工艺尚未成熟或者说有比较统一的趋势。虽然 MICRO LED 的定义目前还没有统一的意见,有认为像素间距在 100um 以下就算 micro LED的,也有认为像素间距在 50um 以下才可以算。由于本文专注于应用于 AR/VR 的微显示芯片,将不包含像素大于 50um 的 MICRO LED 显示。从 MICRO LED 发光结构上看,有横向结构也有垂直结构。横向结构指 LED 的阳级和阴极连接触点是横向摆放的,即使不在同一高度,却需要消耗横向的面积。而垂直结构是指整个发光结构在垂直方向形成,阳极或阴极的其中一极是公共电极,一极连接像素,从发光面来看,不消耗额外面积。可知,对于对PPI 要求较高的 AR 应用来说(>1000ppi),垂直结构是一个更合理的选择。从全彩显示的角度看,有几种不同的方案,可以键合三种不同颜色 LED,也可以加量子点或量子阱对蓝色或是 UV LED 进行色转换,也有三片不同颜色的 LED 芯片垂直堆叠合成彩色的工艺。Micro LED 的器件结构面对的另一个挑战是随着单颗 LED 面积的减小,发光效率也大幅度下降。
从制造工艺上看,有倒装焊工艺也有晶圆级的制程。从硅基 MICRO LED 的角度看,倒装焊工艺主要是通过金属键合或是其它微结构将 LED 芯片和 CMOS 硅基芯片在像素级别一一对应的连接起来。而晶圆级的制程则更多的借助于半导体制造工艺。一个常见的基于色转换的倒装焊工艺流程如下:首先分别制作 CMOS 驱动晶圆和 LED 晶圆,通过倒装焊键合两种不同的晶圆后剥离 LED 衬底,在 LED 上制作色转换层,而后进行封装。而晶圆级工艺又分为几种,有将外延片转移到硅基晶圆后再刻蚀单个的 LED 像素的方式,也有在LED 晶圆基础上进行 TFT 制作的方式,也有先将 LED 晶圆切割并转移到硅晶圆基底而后进行晶圆级键合的方式。
4.2 硅基 MICRO LED 的背板设计
Micro LED 像素也是电流驱动,驱动方式也可以分为模拟驱动和数字驱动,如图7。然而和 OLED 不一样的是,对于现有的 MICRO LED 工艺来说,模拟驱动方式除了有 Vth 变化造成的亮度不均问题以外,还面临发光效率随电流值改变的问题以及电流变化引起的发光波长蓝移问题,所以数字驱动的方式通常选择 LED 芯片 EQE 较高的电流区间进行 PWM 控制而形成灰阶,而亮度不均匀和工艺偏差可以通过算法解决。
但是对于面向 MICRO LED 的硅基背板来说,有一个设计矛盾。对于 micro LED 像素,发光效率最大的电流密度在 10-1000 A/cm2之间。而单个微显示芯片通常显示面积也就在1cm2以内。对于普通 CMOS 工艺来说,如此大的电流密度很难实现。尤其如果考虑金属走线的寄生电阻,对于高像素密度的屏,大电流将引起过大的压降(屏的尺寸一般在0.5-1cm2,按低的 10 A/cm2 计算,0.1 欧姆的寄生电阻将引起 1V 的额外压降,而大部分供电电压在 5V 或以下),反过来影响屏的亮度。所以我们会看到一个有趣的现象,分辨率高且像素小的微显示芯片,通常功耗反而低,分辨率低且像素大的屏,功耗可能反而大。表1 是我们对一些文献中的 CMOS 芯片部分的参数做了一个汇总。LCOS 和 OLED on Silicon 的像素间距和像素大小差别不大,所以一般只给一个间距。而在 MICRO LED 的情况,考虑制造工艺和走线,两者差距有可能较大,因此在表中尽量做了标注。
▲图7:硅基 uLED 的模拟驱动和数字驱动
对于 AR 的应用场景,屏作为可穿戴终端上的芯片,对功耗是希望越低越好。动辄上瓦的功耗并不适用。因此,可能需要在发光亮度、效率和功耗之间做一个平衡。
▲表1:micro LED 相关文献中的硅基部分的参数
五、DLP和激光扫描MEMS微镜技术 |
DLP(Digital light processing, 也称为 Digital Micro-mirror Device, DMD)技术和 LBS 技术原理上都属于 MEMS 技术,但是二者的工作原理完全不同。
DLP 芯片当中,CMOS 驱动部分和微镜是在一颗芯片上,其工作原理非常类似数字驱动的时序彩色 LCOS,屏是在 CMOS 工艺之后,经过 CMP 制程,接着制造了用于反射的众多像素级微小镜面,每个像素下面都是一个 6T SRAM 单元,用高低电平来控制光的开启和关断。其详细结构和制造工艺流程可参考文献。这一技术由于专利和生产原因,一直只有 TI 一家供应商。
激光扫描微镜技术在微显示技术中是比较特殊的一类。图像是通过微镜将被调制的激光有序的发射到某个投影表面不同的位置,让人在视觉上感觉到一幅图像 。也因为显示画面不是由物理像素构成的,微镜技术也被寄予厚望能不受制造的物理极限而实现更高的像素密度。这一技术在通常微显示的显示区用一个毫米级别的微镜取代了其它技术的像素显示部分(众多的微米级别的单个像素),屏上通常包含了微镜、制动器和感应器,微镜的驱动信号由另外的混合工艺制造的芯片提供。虽然基于 MEMS 微镜的微显示技术在之前就有提出,但是由于微镜的制造属于特殊工艺,很少受到关注,一直到微软在 HOLOLENS 2 中大胆采用了 LBS 技术才发生了改变。微镜的制造工艺可以参考。
微镜的控制可分为静电控制(eletrostatic)、电磁控制(eletromagnetic)和压电控制(piezoelectric)。这里微镜根据扫描方式又可以分为两种,使用光栅扫描加线性扫描两个微镜的方案,以及使用单个微镜的方案。不论哪种方案,微镜都是实现反射光的作用。而微镜的控制部分,主要通过算法控制微镜的偏转角度,逐点成像。在算法上又分为光栅扫描算法和双振算法。光栅扫描算法就是传统的快速翻转光栅微镜形成图像的行,再通过线性微镜以稍慢的速度完成不同行图像的扫描。而双振算法则是通过单个微镜在两个轴上都快速翻转,并多次写入形成完整图像。两种算法都有丢失像素点的缺点,所以基于 LBS 技术的眼镜的视觉分辨率都会比标称的分辨率要小。优点在于微镜对高低温耐受强,且亮度高。
六、结 论 |
通过以上几个部分的介绍,我们可以看出,每一种微显示技术都有自己的优缺点,也各有需要面对的挑战。比如 LCOS 屏的制造工艺成熟,亮度高,对比度中等,硅基背板设计灵活,功耗中等,但是由于是反射式的而非自发光的屏幕,在 AR 应用中会比 OLED 屏和 MICROLED 屏的方案需要多一个投影光机,增大了系统的体积、功耗和复杂度。对于不是特别在意体积的如 HMD 等应用场景,LCOS 是一个非常合适的选择。硅基 OLED 屏对比度高,制造成熟度中等,亮度较低,硅基背板有针对不同场景的功耗优化方案,在一些对亮度要求不高的室内场景,以及一些对光路进行处理的方案上会比较有优势。Micro LED 屏的亮度高,预期寿命长,长期看非常适合 AR 和 VR 的应用,但是目前制造工艺还不是很成熟,材料、良率和功耗等方面都有挑战。在 AR 应用上,目前主要在一些主要做信息提示的不需要高分辨率的场景应用,量产能力有待证明。至于 LBS 方案,主要优势在于有完整方案,工作温度相对宽泛,对一些恶劣环境的应用有优势,缺点在于激光容易色偏,需要温控,系统功耗和实际分辨率都没有优势,且供应链薄弱。
如今,大陆方面对微显示的研究也方兴未艾。之前由于产业链的不完善,硅基微显示的发展一直比较缓慢。2001 年南开大学团队就发布了分辨率为 640*480 的模拟驱动 LCoS 芯片。中科院团队于 2009 年发布了分辨率为 320*240 的模拟驱动 LCoS 芯片。电科 55 所于2019 年发布了分辨率为 1400*1050 的单色硅基 OLED 芯片,并于 2022 年对 MICRO LED 的发光材料和后道工艺做了综述研究。上海大学团队 2021 年发表了对硅基 OLED 屏的寿命研究。福州大学团队于 2020 年对 MICRO LED 微显示技术从驱动到转移技术,以及研究发展状况做了综述研究。笔者团队于 2020 年 6 月发布了分辨率为 1920*1080 的模拟像素驱动 LCoS 芯片,2020 年 11 月发布了基于数字像素驱动的 FHD LCoS 芯片,2021 年发布了分辨率为 480*270 的单色 MICRO LED 芯片,2022 年联合南方科技大学团队共同发布了 FHD单色 QLED 芯片。可以看出,2020 年后,大陆微显示产业进入了高速发展期。
表 2 对不同硅基微显示技术的重要参数进行了一个比较。如何减小像素特征尺寸对于各种微显示技术来说都是非常有挑战性的一个课题。这里选择了在能够实现全彩显示前提下的最小像素尺寸。对于空间彩色(如 OLED 和 MICRO LED 技术),一个完整显示像素通常需要由 3 到 4 个子像素构成,因此其子像素的尺寸可能小于表 2 所标注的尺寸。而对于 LCoS技术和 DLP 技术,由于单像素就能实现彩色,显示像素和物理像素可以一一对应。在最大分辨率这个指标上,将不考虑通过算法提升的显示分辨率,也不考虑功耗,只考虑能够制造出来的实际物理像素数量。如 8K 的 LCoS 屏,由于价格昂贵,目前主要用于大型投影仪。又如对于 DLP 技术,可以通过抖动算法,用 1920*1080 的屏实现 3840*2160 的分辨率,大于屏的物理像素分辨率。针对 micro LED 技术,有单色分辨率可以达到 1080P 的产品,这里选择的是目前有报道的最大全彩分辨率 960*540。对于 LBS 技术,理论上,通过足够快的扫描算法,可以实现任何大小的分辨率。然而微镜扫描速度受半导体器件工作速度和微镜翻转速度的限制,目前主要的方案主要还是 720P 和 1080P。成熟度的判断依据主要为生产制造工艺是否成熟以及产品是否已经得到广泛的使用。LCoS 和 DLP 分别在 AR 眼镜和投影领域应用多年,尽管仍在改进,都算是很成熟的技术。硅基 OLED 也在 EVF 和 VR 领域得到了应用,但是不论是材料还是工艺,都在改善当中。LBS 由于可以借鉴之前的 MEMS 工艺,相对来说制造工艺还比较成熟,主要是针对 AR 应用的改进。而 MICRO LED 技术不论是材料、制造工艺,还是跟硅基背板的配合,都还百家争论的阶段,并且没有大量应用的产品,因此认为成熟度较低。功耗数据主要来自实测、相关产品手册和综述文献。硅基 OLED 和 microLED 的最小功耗分别来自文献和文献。对比度数据主要参考实测数据和文献。
▲表2:不同微显示技术的参数对比
综上所述,可以认为,在 AR 领域,LCoS 是一个比较成熟可用的微显示技术,其次是硅基 OLED,micro LED 技术有望后来居上。但在一些特殊的成像领域,如全息成像,LCoS 依旧是最佳选择。不管哪一种微显示技术,屏侧与硅基背板部分的配合都是很重要的。将来可以通过试验优化,对不同的屏选择更合适的驱动方案和架构,实现更优异的性能。例如通过升级使用的半导体工艺节点将驱动电路和屏侧集成到一颗芯片上以减小功耗,或通过 CPU 侧预处理视频信号,针对性的优化屏侧的功率,都可以让现在的微显示技术更加适合可穿戴设备的需求。
-
芯片
+关注
关注
455文章
50816浏览量
423674 -
晶体管
+关注
关注
77文章
9693浏览量
138194 -
增强现实
+关注
关注
1文章
712浏览量
44954
原文标题:硅基微显示芯片:LCoS、Micro OLED、Micro LED、DLP、MEMS 显示
文章出处:【微信号:AIOT大数据,微信公众号:AIOT大数据】欢迎添加关注!文章转载请注明出处。
发布评论请先 登录
相关推荐
如何将LED晶粒转移到玻璃或塑胶基板上,是Micro LED技术取代平面显示技术的关键
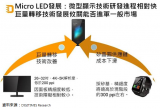
LCoS显示技术的显示原理和LCoS关键问题
直线马达助力的索尼Micro OLED显示屏
什么是Micro-LED?Micro-LED的显示原理是什么?
12英寸硅基Micro OLED微型显示器进入商业化量产阶段
一文解析TFT LCD、OLED、Micro LED的显示技术原理
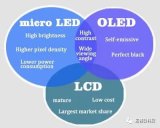
评论