本文梳理了电动汽车用电机的发展现状,根据目前已经量产的50多家电动车用电机的典型电机设计与应用进展情况,从不同的方向进行一个描述总结。从电机的角度主要的研发现状可以总结为以下几点:
电机类型永磁化
永磁化已经成为了行业的标配,电励磁及感应电机的研发应用逐渐增多。另外,一些特种电机的研发也在持续地进行。如开关磁阻电机、轴向电机、无稀土永磁电机等。目前市场上的各种纯电和混动新能源汽车,永磁同步电机占多数,感应电机占一小部分。相比永磁同步电机,交流感应电机体积较大,但是价格适中,但是感应电机可以做的功率很大并且不存在退磁问题,所以一些大型车或者追求性能的电动汽车,比如特斯拉Model S和蔚来ES8,都采用感应电机。总的趋势来讲,永磁化是一个方向,不过在大功率以及高速的应用下感应电机还是有自己的一席之地。
其他类型的电机主要是在特种车辆上进行应用;
开关磁阻电机:Turntide Technologies公司通过在电机中放置传感器来追踪转子运动,已经克服了很多此类电机的问题。工程师使用机器学习算法来确定开关电流的正确时间。工程师设计出一种无传感器开关磁阻电机,将振动最小化。
轴向磁通电机:比利时Magnax公司的产品减少电机重量、尺寸和成本。他们的设计旨在把转子和定子齿部的空气间隙减到最小。电机使用了SRS的方式,两个转子,各位于定子的一边。在这种配置中,定子支撑起电磁齿轮,但并不充当转子的支撑或轭。轭是一个占定子质量三分之二的钢制圆筒。若没有轭,电机重量可大大减轻,该公司估计这一做法可让电动汽车续航能力提升7%。
双向磁通电机:Linear Labs公司(位于美国得克萨斯州达拉斯-沃斯堡)采用了另一种方式,该公司选择在一个电机中结合轴向和径向磁通设计。该公司的“三维(3D)周向通量电机”包括围绕定子的4个转子。中央转子在定子内部旋转,而第二个转子在定子外部旋转。另外两个转子分别位于定子的左右两端,总共有4个磁通源,各个转子在运动的方向上都会产生扭矩。
扁线电机or圆线电机
扁线电机渗透率快速提升。2021 年特斯拉换装国产扁线电机,带动渗透率大幅提升,扁线电机的趋势已经确定。众多潜在爆款车型使用扁线电机,预计2025 年渗透率将快速提升至 95%。众多高端车型均搭载扁线电机,比亚迪的 DMI 车型和 e++平台全系都是扁线电机,大众 MEB、蔚来 ET7、智己 L7、极 氪 001 等明星车型采用的都是扁线电机。
扁线电机能大幅度提升转换效率。在WLTC工况,扁线电机比传统圆线电机的转换效率高 1.12%;在市区工况(低速大扭矩),两者效率值相差10%。按照典型的续航500km的 A 级轿车(搭载 60kwh电池包和 150kw 电机)计算,WLTC 工况下,搭载扁线电机的电池成本节约 672 元,市区工况下,电池成本节约 6000 元。
扁线的槽满率大于圆线,当槽满率越高时相同功率电机所需要的铜线更短,进而电阻降低发热减少。从理论上来说,圆线的净槽满率一般在约40%左右,而扁线则可以提升至70%。由于圆线的截面为圆形,不可避免在导线间存在不规则缝隙,而扁线间的间隙更小,槽满率更高。扁线电机的高效率区间比圆线电机高出许多,圆线电机的高效区一般要求是效率>85%的区间占比不低于 85%,被称为“双 85”。而扁线电机的效率>90%的 区间占比不低于 90%,被称为“双 90”。电机的效率与转速和扭矩相关,市区工况中出现的频繁启停工况属于低转速 高扭矩工况,而这正是圆线电机的低效率区间,而扁线电机在该工况下的转换效率更高。
扁线电机散热性能好:温升相对圆线电机降低10%。因扁线相对圆线更为紧密的接触,散热性提升,研究发现高槽满率下绕组间的导热能力是低槽满率的150%。绕组在热传导能力上具有各向异性,轴向的热传导能力是径向方向的100倍。更低的温升条件下,整车可以实现更好的加速性能。
电磁噪音低:整车更安静。扁线电机导线的应力比较大,刚性比较大,电枢具备更好的刚度,对电枢噪 音具有抑制作用;可以取相对较小的槽口尺寸,有效降低齿槽力矩,进一步降低 电机电磁噪音。
小体积带来高集成效率,契合多合一电驱发展趋势:因扁线更高的槽满率,同功率电机铜线用量和对应定子较少,体积有望下降30%。此外,扁线电机因更为先进绕线方式带来更易裁剪的电机端部,与圆线电 机相比减少15-20%的端部尺寸,空间进一步降低,实现电机小型化和轻量化。
扁线电机大规模应用也需要克服一些缺点,比如良品率低,转速上不去,标准化难以及专利壁垒等。在高端车型中为满足对高性能的追求,搭配扁线电机数量也开始由原来的单电机增加到双电机,例如保时捷首款纯电动跑车Taycan,甚至部分车型会搭配三电机。
绝缘车规级新能源汽车用扁线对耐热性要求高,主要采用耐温≥180℃的聚酯亚胺漆包线漆、聚酰胺酰亚胺漆包线漆、聚酰亚胺漆包线漆这三种耐高温绝缘材料进行漆包。聚酯亚胺漆具有较好的电气性能和机械强度,且耐热冲击和耐软化击穿。在180级及以上复合涂层漆包线制造中作为底漆涂层的主要材料,在高附着和耐氟利昂的家用电器中得到广泛应用。聚酰胺酰亚胺漆耐热性高,不仅漆膜硬度和非软化性很大,并且对导体粘合力较高,最先得到产业化,可在 210℃下长期使用。用于耐高温电机电气电子元件的线圈绕组,被用作电磁线的绝缘涂层。聚酰亚胺漆耐热性能优异,同时能够耐老化,耐高压电击穿等。其主要运用 于绝缘漆覆包电磁线,或作为耐高温涂料应用于电气行业、航空航天、石油管道 等。
高压化
研究方向:800V 被认为是下一代电动车必经之路,2019 年保时捷发布全球首款 800V 车型 Taycan。现代 E-GMP5、奔驰 EVA、通用第三代纯电动平台以及大众 Trinity, 都选择了800V 电压平台。吉利SEA浩瀚平台、广汽、奇瑞、上汽等车企都在规划800V的方案,800V成为车企新一轮竞争的制高点。
优势:800V能显著降低高压线束线径,减少发热,降低质量,节约线束成本。电压等级从400V提高800V,根据最简单的P=UI,在输出相同功率的情况下,800V系统所传输的电流就更小,线缆线径和重量就可以降低,节省线束的成本及安装空间。
劣势:800V平台下电晕腐蚀出现概率增加,电晕腐蚀会对电机绝缘造成重大危害。电晕放电是指气体介质在不均匀电场中的局部自持放电,是最常见的一种气体放电形式。通常发生在在曲率半径很小的尖端电极附近,如绕组出槽口处、绕组绝缘层内部等。电晕即气隙放电,部分能量转换为光、热、声、 电磁等,会造成
1)热效应局部温度升高,绝缘老化等;
2)机械损坏,大量带电 离子“电子和正负离子”以高能量和高速度撞击,造成绝缘层机械强度降低、局部放电区域绝缘层出现麻点、麻坑、孔眼等绝缘失效问题;
3)化学损坏,气体局部 放电形成臭氧,臭氧化学性质不稳定,易生成氧化氮,再与水蒸气反应生成硝酸, 腐蚀绝缘层。
技术路线:要满足800V的技术要求,主要通过两种技术路线:1)厚漆膜工艺,2)薄 漆膜+PEEK 膜包工艺;提升漆膜厚度是最简单有效的途径,漆包线的绝缘性能与漆膜厚度成正比,现在主流的新能源扁线的结构是:内层为铜扁线导体,根据扁线性能要求和使用 领域不同,铜扁线导体外涂设有二层或者三层绝缘漆膜,漆膜具体包括底漆层、 耐电晕漆层和面漆层。第一层为聚酯亚胺或者聚酰胺酰亚胺漆膜,第二层为耐电 晕漆膜,第三层为聚酰胺酰亚胺或者聚酰亚胺漆膜。
冷却形式多样化
电动机主要冷却方式有自然冷却、风冷和液冷。
在电机必须封闭防护,或者无强风的应用环境中,采用最多的是内油冷方式,比如AVL设计的高速电机采用的定子槽内油冷的方式的组合。有些电机也采用绕组喷油冷却+定子油冷+转子油冷等多种方式的组合。
液冷的形式:电机冷却系统处于较低温度时,冷却液泵不工作。温度上升后,冷却液泵工作。冷却液泵的工作温度不能超过75℃,最合适的工作温度应该低于65℃。电动汽车驱动电动机与控制器的冷却系统主要依靠冷却水泵带动冷却液在冷却管道中循环流动,通过在散热器的热交换等物理过程,冷却液带走电动机与控制器产生的热量。为使散热器热量散发更充分,通常还在散热器后方设置风扇。电动机在工作时,总是有一部分损耗转变成热量,它必须通过电动机外壳和周围介质不断将热量散发出去,这个散发热量的过程,我们就称为冷却。
水道设计要点:水道截面尺寸增大,其冷却水流速将下降,水道对流传热系数也将减小,受冷却水套机械强度的限制,水道截面尺寸不能无限制增大;若水道截面尺寸减小,冷却水流速将增加,其对流传热系数增大,但流动阻力也将增大。水道截面尺寸增大,其冷却水流速将下降,水道对流传热系数也将减小,受冷却水套机械强度的限制,水道截面尺寸不能无限制增大;若水道截面尺寸减小,冷却水流速将增加,其对流传热系数增大,但流动阻力也将增大。可见,在设计冷却水套时,除了工艺实施性和造价因素之外,更需要考虑包括冷却水套水头损失分析、水道内的对流传热分析以及整个水套的机械应力分析与计算。利用热流仿真分析软件可以对电机的冷却水套进行优化设计,实现最佳散热性能和最小泵功消耗的最佳匹配。
高功率化
高功率密度,整车动力更强劲。电机的功率与铜含量成正相关,扁线电机槽满率提升,相同体积下铜线填充量增加20-30%,输出功率有望提升20-30%,整车动力 更强劲。国外如大众、沃尔沃、克莱斯勒等驱动电机最高转速不断提升,最高达到14k~16krpm;从绕组结构上看,发卡式绕组/扁导线绕组(通用、丰田、本田、戴姆勒等)成为明确的技术方向之一,电机功率密度均达到3.8~4.5kW/L以上;无/低重稀土材料已经开始应用。国家政策层面倡导高电机功率密度。“十三五”规划中提出,新能源乘用车电 机功率密度应满足4.0kw/kg,高于当前圆线电机约 3.5kw/kg 的水平。在圆线电机 功率密度提升进入困难模式的当前,发展扁线电机是必然之路,根据摩恩电气的 公告显示,当前领先企业的扁线电机的功率密度约4.5kw/kg。美国DOE2025的电机功率密度指标大于等于5.7kW/kg。英国的Equipmake号称要研制峰值功率密度20kW/kg的破纪录电机。不过最后做了几轮的尝试,第一台电动机称为APM120,重量仅为14 kg,可在12,000 rpm下获得125 kW的峰值功率。此外,连续功率为75kW,峰值扭矩为130Nm。计算可知,功率密度约为9 kW/kg。第二台电动机性能更强劲,称为APM 200,重达40 kg,可在10,000 rpm下获得220 kW的峰值功率。此外,连续功率为110 kW,峰值扭矩为450 Nm。计算可知,功率密度约为5.5 kW/kg。
高速化
在电驱动总成输出转矩和功率不变约束下,通过提高驱动电机和减速器最高转速,降低电机体积和重量,提高功率密度水平。大众、沃尔沃、克莱斯勒等国外汽车企业通过不断提升电机转速来降低电机体积和重量,大众汽车模块化电驱动平台(MEB 平台)电机最高达到16000rpm,沃尔沃与克莱斯勒电机最高转速需求达到14000rpm,特斯拉Model3 驱动电机最高转速达到17900rpm。我国驱动电机功率密度、效率等整体技术提升很快,技术水平与国外同类产品相当,驱动电机重量比功率已达到 4.0kW/kg 以上新能源电驱动系统呈高速化发展趋势,转速水平从主流的15000rpm升级到18000rpm甚至20000rpm转以上。但是高速化带来的散热、转子结构、振动噪音、高效设计、轴承等问题又不得不去解决。高速电机的转子结构必须要克服的离心应力,一般在“高速”的范围内采用金属护套、转子本身结构等,而在超过18000的范围内采用碳纤维缠绕。
-
电动汽车
+关注
关注
156文章
12084浏览量
231211 -
电机
+关注
关注
142文章
9015浏览量
145443 -
电励磁
+关注
关注
0文章
7浏览量
1863
原文标题:干货丨驱动电机技术趋势
文章出处:【微信号:EDC电驱未来,微信公众号:EDC电驱未来】欢迎添加关注!文章转载请注明出处。
发布评论请先 登录
相关推荐
电机控制系统出现了哪些新的应用趋势和新技术?
轮毂电机技术也称为驱动电机技术
车用驱动电机技术的发展资料概述
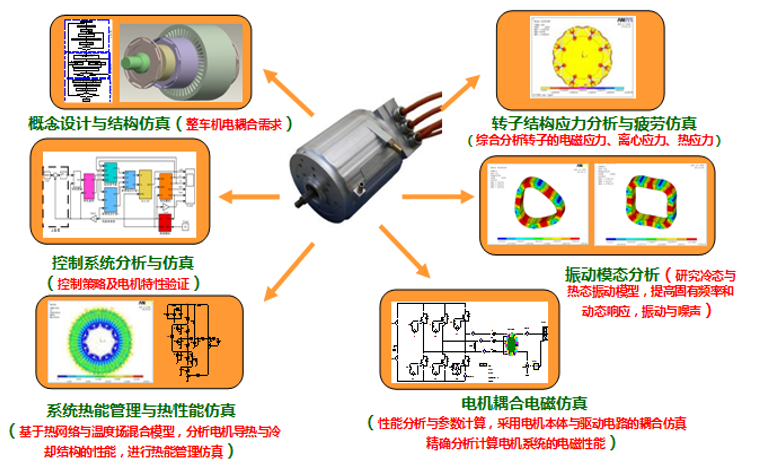
高速电机驱动技术及其发展趋势
驱动电机发展趋势
电动汽车驱动电机技术的发展趋势
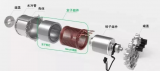
评论