随着4680产业落地。供应链内收益材料包括高镍正极、硅基负极、新型锂盐、复合集流体、设备及电池壳体,其中 PET 复合铜箔及硅基负极或将成为为最主要增量。
◆ 复合铜箔
锂电铜箔根据组成材料的不同可分为传统铜箔与复合铜箔。
传统铜箔:由99.5%的纯铜组成,根据厚度可分为极薄铜箔(≤6μm)、超薄铜箔(6-12μm)、薄铜箔(12-18μm)、常规铜箔(18-70μm)、厚铜箔(≥70μm)等,其特点为单位面积重量较重、金属铜材使用量高、导热性能高。
◆ 锂电铜箔技术趋势
PET 复合铜膜在锂电行业的大批量应用是必然的
例如,目前同样级别的6-8微米的PET铜箔大部分会替代目前6-8微米的传统铜箔,但是无法代替更薄的传统铜箔。取代逻辑主要是由 PET 复合铜膜的四个先进性所决定的:高安全、高比容、长寿命、高兼容。6-8μm传统铜箔极板在遭遇外力碰撞时容易造成燃烧、爆炸等安全隐患,研制更加安全的新式动力电池材料已成为未来发展的趋势。
◆ 性能特点
①高安全:消费端对锂电池的最大顾虑也是也是其不够安全,电池自燃是由于发热失控导致的内短路。PET复合铜膜对这一问题的解决方法就是高分子不容易断裂,即便断裂,1微米的镀铜的强度无法达到刺穿隔膜的标准,可以实现永不刺穿,把内短路的风险完全规避掉。
②高比容。PET复合铜箔重量更轻,目前集流体占电池重量的比重是15%,PET 技术可以提升5%-10%的电芯能量密度,实现高比容。
③长寿命。这主要是因为 PET 表面更为均匀。并且金融结晶体更容易热胀冷缩,高分子材料的膨胀率更低,更容易空置,保持表面完整性,提升程度在5%。
④高兼容。即很多性能可以更高的去进行匹配,比如铝箔和铜箔都可以应用 PET 技术
⑤成本更低:传统铜箔约占锂电池质量的9%、成本的8%。铜箔变薄可使相同电芯体积容纳更多活性材料,6μm和4.5μm铜箔相比8μm铜箔能量密度分别提升5%和9%;此外铜箔越薄,电池成本越低、受铜价影响越小;传统铜箔的铜原材料成本占比约80%,原材料环节难以降本;而PET铜箔原材料成本占比约31%。受产业化初期影响设备成本占比高达50%,PET铜箔生产通过规模效应降低成本的空间更大,主要降本路径为通过提高生产效率与良率摊薄单位固定成本。
◆成本结构
铜箔占电池成本比重
迫于成本压力开发新材料。动力锂电池整体朝着高能量密度的方向发展,但高镍三元材料较传统的 6 系三元材料和 5 系三元材料的成本有所上升,由此带来了原材料的成本压力,性能与成本的兼顾成为了亟需解决的问题。
锂电铜箔是锂电池最重要的原材料之一,充当负极活性物质载体的同时又充当负极电子流的收集和传输体。目前主流的铜箔产品约占动力电池总质量的 14%,更薄的铜箔可以为电池带来更高的能量密度,但同时也会带来更高的成本。部分企业为解决这一难题, 在铜箔产品中引入高分子材料,通过材料创新降低铜箔的重量与成本,从而进一步改善电池的性能与成本的兼顾问题。
使用PET铜箔可大幅降低铜箔原材料成本。传统铜箔由纯铜制备,铜成本占铜箔总成本约80%,而PET铜箔是在PET基膜表面进行镀铜,成本由PET价格和铜价共同决定,益于PET材料的低成本,PET铜箔能为电池带来更更低的材料成本。截至2023年4月10日,铜价约为6.9万元/吨,PET材料价格约为2.6万元/吨,经我们测算,6.5μm的PET铜箔较目前主流的6μm铜箔可降低62.42%的原材料成本,较目前最为先进的4.5μm铜箔可降低51.68%的原材料成本。
◆铜箔产业链
上游原材料及设备厂商:设备厂商包括磁控溅射设备厂商和电镀设备厂商;
铜箔制造:根据锂电铜箔工艺可分为电解铜箔以及PET铜箔,其中电解铜箔为市场主流工艺,PET铜箔为新工艺;
下游锂电池厂商:主要包括动力电池厂商、3C消费电池厂商以及储能电池厂商等。
◆设备厂商
传统铜箔多采用电解法制备,PET铜箔工艺核心为真空镀膜与离子置换
传统铜箔目前多采用连续电解法制备。锂电池发展初期多采用压延铜箔,但压延铜箔生产工艺复杂、成本高,且全球产能极度集中于少数几家公司;电解铜箔由于生产设备和工艺简单、容易操作,且产品性能良好,逐渐成为目前最普遍的铜箔生产方式。电解铜箔是在直流电流作用下,铜离子在连续转动的阴极辊表面还原沉积形成很薄的连续的铜层继而连续剥离形成的,其主要生产流程包括溶铜、生箔沉积、后处理及分切。
PET铜箔制造工艺核心为真空磁控溅射、铜堆积层和清洗抗氧化保护。PET铜箔生产工艺以高真空设备磁控溅射在基膜上金属化,再以离子置换机进行金属置换使金属层增厚,具体工艺流程包括真空溅射镀铜(非金属材料金属化)、液体电镀(铜层增厚沉积)、成品材料配切。
复合铜箔产业化的核心壁垒为工艺与设备——真空磁控溅射
真空磁控溅射是制备薄膜的主要技术之一,下游应用广泛。
磁控溅射镀膜是通过电场和磁场的作用,工作气体产生辉光放电,离子轰击靶材溅射出材料粒子形成薄膜,目的是在塑料薄膜表面制作一层金属层、使非金属材料金属化,具有镀膜稳定性好、重复性高、均匀度好、适合大面积镀膜、膜层致密、结合力好、工艺灵活度高等优点,主要应用下游包括消费电子、汽车、光学和玻璃等行业。
◆ 市场容量
预计2025年PET铜箔磁控与镀铜设备市场空间总计约80亿元
预计2025年PET铜箔真空磁控溅射设备市场空间约33.4亿元,镀铜设备市场空间约46.5亿元。相较于传统锂电铜箔,PET复合铜箔带来真空磁控溅射设备和镀铜设备需求,基于以下假设测算:
1)假设2025年中国/全球新能源汽车渗透率33%/21%,据SPIR预测,2022-2025年储能电池需求分别为56GWh、79GWh、108GWh、168GWh;
2)假设PET铜箔渗透率2025年提升至21.7%;
3)假设2021年单GWh磁控溅射设备价值量为3000万,单GWh镀铜设备价值量为3750万。随着设备技术迭代及规模效应,2022至2025年单GWh磁控溅射设备价值量分别为2900万、2800万、2700万以及2500万,单GWh镀铜设备价值量分别为3600万、3500万、3400万及3300万。
-
新能源汽车
+关注
关注
141文章
10648浏览量
100308 -
铜箔
+关注
关注
5文章
221浏览量
16393 -
圆柱电池
+关注
关注
0文章
183浏览量
9912
原文标题:PET铜箔增量!受益于4680圆柱电池产业落地
文章出处:【微信号:深圳市赛姆烯金科技有限公司,微信公众号:深圳市赛姆烯金科技有限公司】欢迎添加关注!文章转载请注明出处。
发布评论请先 登录
相关推荐
圆柱电池测试设备:确保电池性能与质量的关键
圆柱电池自动分选机:提升电池生产效率与品质的关键设备
亿纬锂能圆柱电池产能再获提升
大圆柱电池产业加速分化,特斯拉押注全干法4680动力
比斯特自动化 气动科技赋能圆柱电池生产:高效点焊机引领产业升级
特斯拉里程碑达成:第1亿颗4680电池震撼问世
RFID技术赋能4680大圆柱电池生产溯源
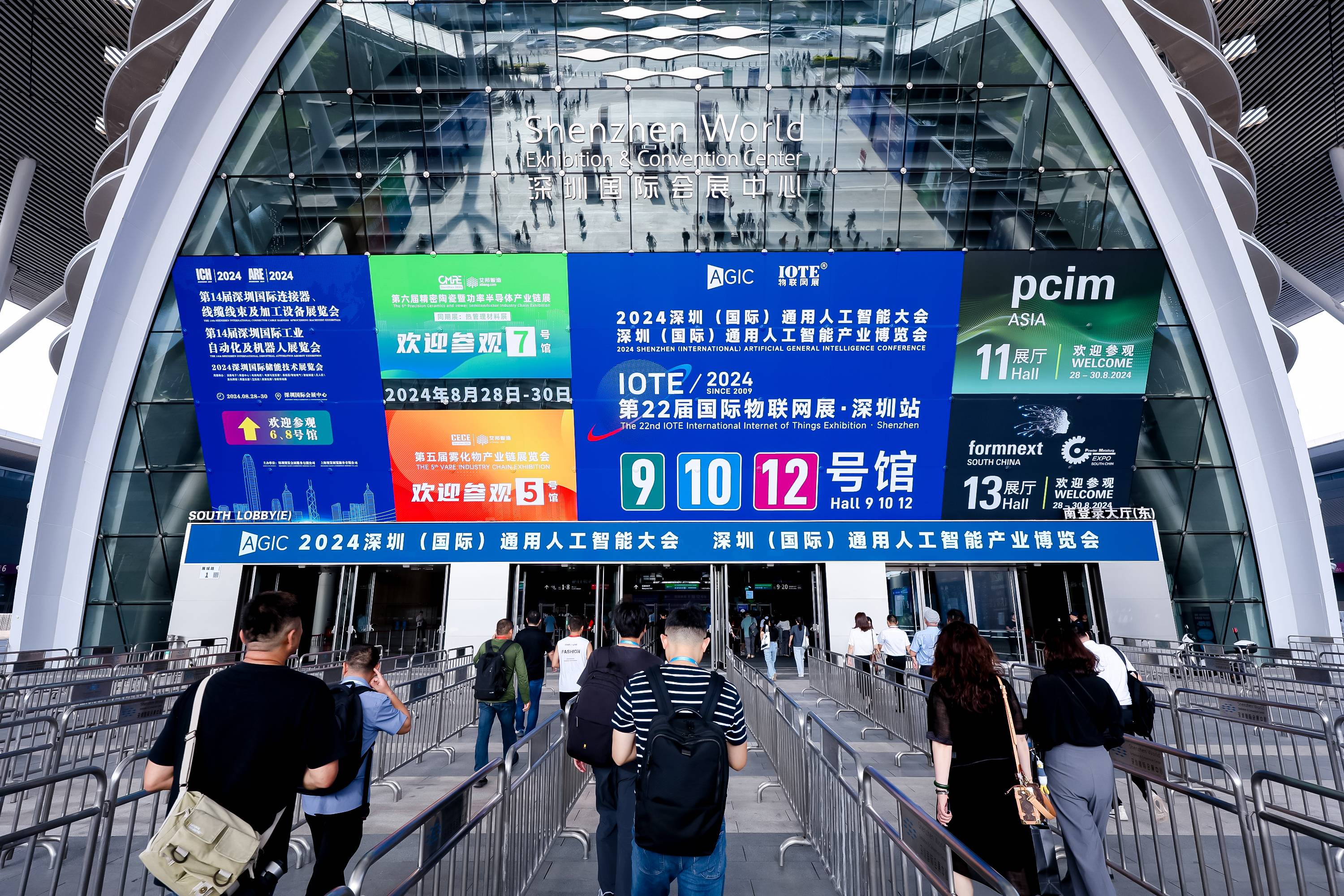
特斯拉4680电池产量环比增长50%,成本持续优化
Cybertruck的4680电池系统设计迭代
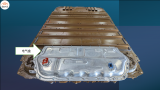
评论