SMT
Surface Mount Technology,表面贴装技术。
是一种电子元器件的表面安装技术,也是当前电子制造业中最流行的一种技术。相比传统的插件式电子元器件,SMT 元器件更小巧、轻便、功耗低,并且可以实现更高的集成度和性能。在 SMT 工艺中,元器件被直接焊接到 PCB(Printed Circuit Board)的表面上,通过贴片机等设备完成元器件的精确定位和安装。
SMT 技术具有生产效率高、工艺稳定、成本低等优点,逐渐成为电子制造行业的主流技术,被广泛应用于手机、电脑、家电、汽车等各个领域。SMT 技术的发展也推动了整个电子制造业的转型升级,促进了电子产业的快速发展。
SMT生产线中有哪些制程和注意事项?
1空板载入
将空板整齐重叠排列放置于料架上,然后由机构装置从最上面的板子一片片送入SMT生产线的输送带中,感应器时时刻刻记录下这个过程,并传送到电脑中,然后判断何时该推送板子,并下指令何时停止板子前进。
以下是需要注意的事项:
确认空板尺寸和厚度与工艺要求一致,避免安装位置不准确或者插针过长等问题。
确认空板表面的状态良好,避免表面凹凸不平或者划伤等问题。
在空板的生产过程中,尽可能避免静电干扰,以防止静电损坏电子元器件。
需要将空板放置在干燥、无尘、无油污的环境中,避免灰尘、油脂等物质附着在空板上。
在载入空板时,需要确保操作人员的手部干净并佩戴手套,避免手部污染空板表面。
对于不同的空板类型,需要根据工艺要求选择不同的载入方法,例如对于薄板载入需要使用专门的载板架,以避免空板弯曲和变形。
总之,在SMT空板载入过程中,需要注意细节,保证生产环境干净整洁、人员操作规范、设备检测严格,以保证整个生产过程的质量和效率。
2印刷锡膏
这个步骤会把锡膏透过钢板印刷在PCB需要焊接零件的焊垫/焊盘上面,锡膏的位置与体积会影响到后续的焊接品质,这些锡膏会在后续SMT制程-回流炉的高温区时融化并在重新凝固的过程中将电子零件焊接在电路板上面。
使用「锡膏」来作为电子零件与PCB结合的主要原因如下:
1)焊锡完成前将电子零件黏贴固定在电路板,使其不至于因为PCB的移动或振动而偏移。
2)经过回流高温后将电子零件焊接固定于PCB上,使其在终端用户使用的过程中不至于掉落,并达到电子讯号传递的目的。
锡膏的选择和质量对SMT工艺的影响非常大,需要根据元器件的要求和生产要求选择合适的锡膏种类和牌号。
同时在工艺流程中需要注意:
印刷之前需要检查印刷机和刮刀是否处于正常状态,以避免印刷质量不佳。
锡膏的厚度需要根据元器件的要求和生产工艺的要求进行调整,过厚或过薄都会影响元器件的安装质量。
锡膏的质量需要通过检测来保证,例如检测锡膏的挤出量、粘度、黏度等指标。
在印刷锡膏时需要注意保持生产环境干净整洁,避免灰尘、油脂等物质附着在锡膏上。
在锡膏印刷完成后需要对印刷质量进行检测,以避免印刷不良、短路等问题。
3锡膏检查
锡膏印刷的优劣会直接影响到后续零件焊接的良莠好坏,所以为求品质稳定,会先在锡膏印刷之后额外多设置一台光学仪器,用来检测锡膏印刷是否为良品,有无少锡,漏锡,多锡等不良现象。检查后如果发现有锡膏印刷不良的板子就可以先挑出来,洗掉上面的锡膏在重新印刷锡膏就可以,或是采用修理的方式移除多余的锡膏。
SPI之所以重要,是因为锡膏如果经过回流后就固化了,锡膏固化后才发现零件有焊接问题就必须动用烙铁修复或是报废,如果可以在早期固化前就发现锡膏印刷问题并加以改善或解决,就可以大幅降低生产不良率并降低修理的成本。
4贴片
高速贴片:将电子元器件SMD准确安装到PCB的固定位置上。这类SMD被动元件(如小电阻、电容、电感)又称「Small Chip」的体积通常比较小,而且一般只有两个端点需要被焊接,所以在将这类小零件摆放在电路板上时相对的位置精度要求也比较低。所以就高速贴片机,一般会有好几个吸嘴头,而且速度非常地快,一秒钟可以打好几颗零件,但大型零件或是有一定重量的零件就不适宜用高速贴片机来处理,一来会拖累原本打得飞快的小零件速度,二来怕零件会因为板子快速移动而偏移了原来的位置。
多功能贴片:它几乎可以用于所有SMD零件的贴片打件需求,但因为其追求的不是速度,而是打件的精度,所以慢速机一般拿来打一些体积比较大或是比较重或是多脚位的电子零件,如BGA积体电路、连接器、屏蔽框/罩…等,因为这些零件需要比较准确的位置,所以其对位及角度调整的能力就变得非常重要,取件(pick)后会先用照相机照一下零件的外观,然后调整零件的位置与角度后才会置,所以整体速度上来说就相对的慢了许多。
5炉前AOI
会在回流炉前多设置一道「炉前AOI」,用来确认回流前的打件贴片品质。还有一个情况是某些板子会在SMT阶段就直接将「屏蔽罩」焊接于电路板上,一旦屏蔽罩放上电路板就无法在经由AOI或是目检方法检查其贴片与焊锡品质,有这种情况一定要扩多设置一道「炉前AOI」,放置在「屏蔽罩」贴片之前。
6回流焊
将锡膏通过高温融化,冷却后使电子元件SMD与PCB板牢固焊接在一起。温度的上升与下降的曲线往往影响到整个电路板的焊接品质,根据焊锡的特性,一般的回流炉会设定预热区、吸热区、回焊区、冷却区来达到最佳的焊锡效果。另外回流炉中的最高温度最好不要超过250℃,否则会有很多零件因为没有办法承受那么高的温度而变形或融化。基本上电路板经过回流炉后,整个电路板的组装就算完成,手焊零件除外,剩下的就是检查及测试电路板有没有缺陷或功能不良的问题而已。
7清洗
其作用是将组装好的PCB板上面的对人体有害的焊接残留物如助焊剂等除去。所用设备为清洗机,位置可以不固定,可以在线,也可不在线。
8炉后AOI
炉后AOI几乎已经成现今SMT的标准配置,但并不一定每条SMT的产线都会配置有光学检查机(AOI」,设置「炉后AOI」的目的之一是因为有些密度太高的电路板无法有效的进行后续的开短路电路测试(ICT),所以用AOI来取代,但由于AOI为光学判读,有其先天上的盲点,比如说零件底下的焊锡无法被检查,邻近高零件的位置会有阴影效应无法有效检查,而且目前AOI仅能针对看得到的零件检查有否墓碑、侧立、缺件、位移、极性方向、锡桥、空焊等,但无法判断假焊、BGA焊性、电阻值、电容值、电感值等零件品质
因此有些先进的EMS工厂就会有X-RAY,用于品质要求高,可靠性要求高的产品和客户,来检测引脚的焊接品质。
9收板
当板子组装完成后再收回到分料架内,这些分料架已经被设计成可以让SMT机台自动取放板。
10成品目检
不论有没有设立炉后AOI,一般的SMT线都还是会设立一个电路组装板的目视检查区!人工检测检查的着重项目:PCBA的版本是否为更改后的版本;客户是否要求元器件使用代用料或指定厂牌、牌子的元器件;IC、二极管、三极管、钽电容、铝电容、开关等有方向的元器件方向是否正确;焊接后的缺陷:短路、开路、假件、假焊。
审核编辑:汤梓红
-
pcb
+关注
关注
4332文章
23197浏览量
400909 -
元器件
+关注
关注
113文章
4756浏览量
93041 -
smt
+关注
关注
40文章
2934浏览量
69891 -
表面贴装
+关注
关注
0文章
391浏览量
18633 -
贴片机
+关注
关注
9文章
653浏览量
22666
原文标题:【干货】一文让你秒懂SMT生产线中有哪些流程和注意事项?(2023精华版),你值得拥有!
文章出处:【微信号:SMT顶级人脉圈,微信公众号:SMT顶级人脉圈】欢迎添加关注!文章转载请注明出处。
发布评论请先 登录
相关推荐
【原创】LED应用产品SMT生产流程防硫注意事项
SMT贴片工艺有哪些需要注意事项
一条smt生产线多少钱_smt生产线设备组成介绍
SMT贴片机操作流程 SMT贴片机的安全使用规则和注意事项
SMT贴片产品加工中有哪些事项需要注意
SMT贴片加工制程与注意事项
SMT生产加工及品质检验注意事项
SMT贴片常识和注意事项有哪些
SMT生产过程中的相关知识和注意事项
智能焊接生产线操作注意事项有哪些
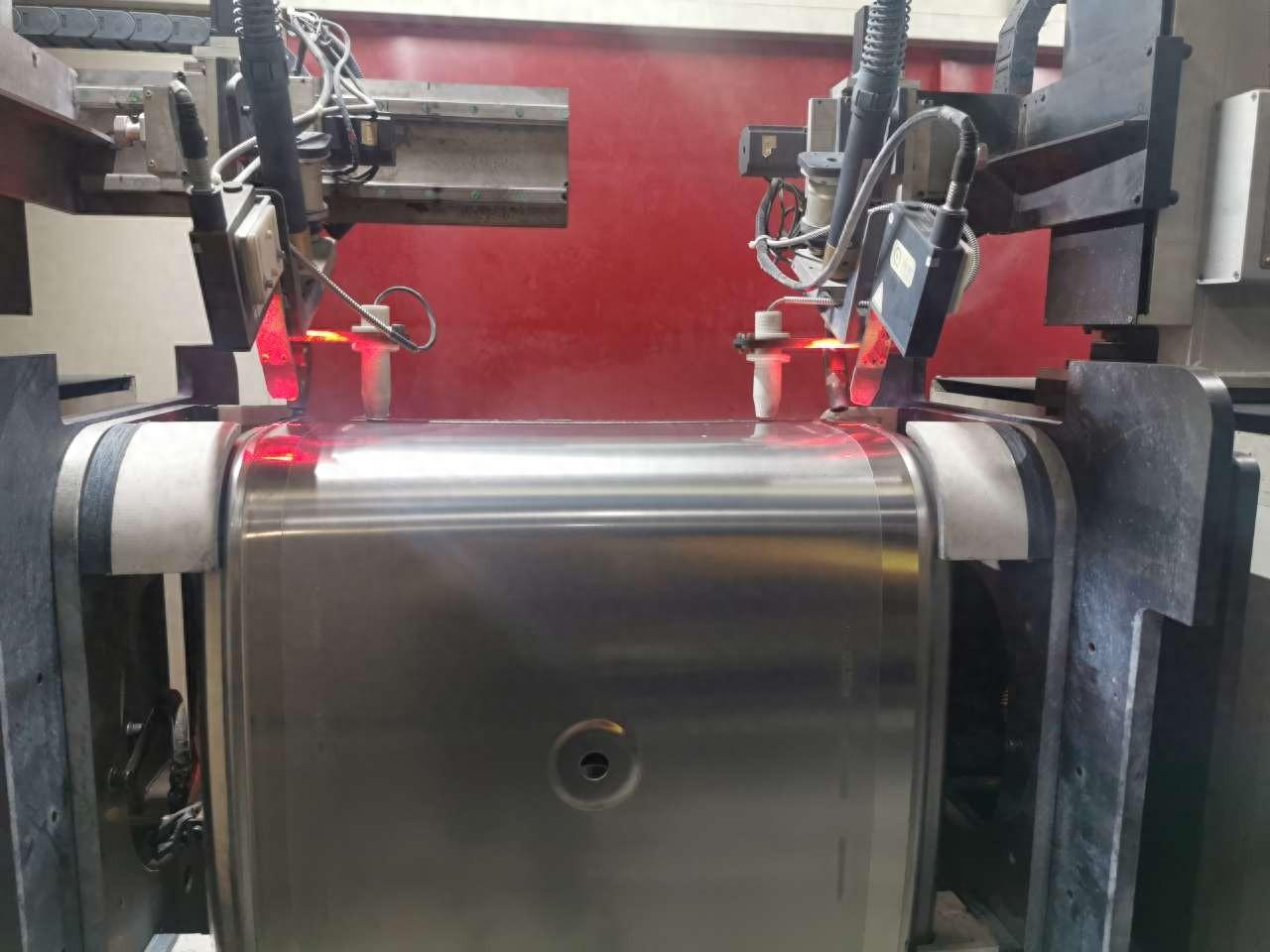
评论