这次聊聊目前行业的对于电池包BDU的发展趋势。其实说白了,电池包的电气化趋势无非就是高度集成化,低成本化,高性能化。围绕这三个点,说简单点就是电池包的高压配电系统,低压系统,都在围绕这几个趋势演变,各种集成,各种降本。
高度集成化:BDU集成BMU、高压连接器、热失控传感器,DCDC等;
低成本化:节省接触器使用,节省BDU塑料件,线束使用等;
高性能化:液冷BDU方案、800V快充切换方案、DCDC预充方案等。
方案一:BDU集成BMU/DCDC/快换连接器/热失控传感器:此方案用的最多的无非就蔚来目前的电气化方案;广汽早期的BDU集成BMU方案,物理上把五者集成起来,一是增大了整包的利用空间,给电芯留下更多空间发挥;二是塑料件可以节省。
方案二:BDU去线束化:这个之前我很早就关注这个了,起始这个可以说在很早就有雏形了,①商用车的高压配电箱,采用PCB电路板(集成高压铜排,高压检测点接插件)这种方案就节省了一定的采集线束,且高压铜排也集成了。②就是和我们目前电池包低压采集系统的发展趋势类似,最早电池包采样通过线束采样,发展到PCB/FPC/FFC/采样;同理,对于BDU内部的去线束化,也可以采用同样的方案,使用PCB/FPC/FFC的方案来代替线束。
方案三:BDU去塑料件化:BDU本省集成了接触器、熔断器、电流传感器这些器件,现在集成化方案也有将BDU塑料件和继电器的塑料件共用,这就对BDU厂家要求比较高,最好是能独立研发继电器,熔断器等一些器件的集成商;这一块国内的BYD/SCII目前有一定的方案。
方案四:BDU标准化,模块化:这一块的方案就是尽最大可能同一种产品匹配更多的车型平台,目前的方案有①主正模块,主负模块化,例如大众的MEB平台BDU,现在国内很多这种方案,国轩/西埃/BYD等等;②BDU总成的模块化,BYD方案,这种方案得益于OEM车型电压平台,电池系统的共用。
方案五:BDU液冷化:液冷BDU方案,这种之前简单的写过,①BDU自身带液冷板的方案,②BDU借用整包的冷板冷却。
方案六:BDU去预充电阻/预充继电器化:采用双拓扑的高压DCDC配合瞬时具有高倍率放电能力的12V锂电池来做到预充,这种方案目前量产使用也就特斯拉,目前专利上各家都能找到一些。
方案七:BDU快换化,快速维修化:这种方案的由来还是得益于目前行业电池包的CTC/CTB化,电子元器件本省就是易损品,动力电池包在不断使用过程中,就会出现老化损坏,当前的CTC/CTB电池包用胶量太大,电池包上盖充当整车的底板,需要承力,上盖II电芯II下箱体三明治粘胶。整包上盖与电芯、箱体集成在一起,无法拆解,所以单独设计电气BDU的维修窗口是当前的最优方案,对BDU/BMS快速维修。
最后总结就是电池包电气化发展趋势:一是愈来愈趋向集成化、高压连接器、高压采样检测板、电流传感器等电子部件不断地集成;二是愈来愈快捷化/标准化/低成本化;快换维修窗口、去线束化、模块化,研发/工艺成本降低。
审核编辑:刘清
-
连接器
+关注
关注
98文章
14476浏览量
136429 -
PCB电路板
+关注
关注
10文章
185浏览量
17313 -
电流传感器
+关注
关注
10文章
996浏览量
41141 -
BMU
+关注
关注
0文章
10浏览量
10145 -
电池系统
+关注
关注
9文章
390浏览量
29919
原文标题:浅谈电池系统BDU的发展趋势
文章出处:【微信号:新能源高压连接器联盟,微信公众号:新能源高压连接器联盟】欢迎添加关注!文章转载请注明出处。
发布评论请先 登录
相关推荐
TPMS技术与发展趋势
Multicom发展趋势如何?它面临哪些挑战?
比亚迪汉EV电池包BDU的高压部件拆解分析
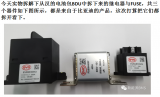
评论