Novelis(诺贝丽斯)最先进的第二代电池外壳内部,从上至下:铝顶盖、CTP电池系统(绿色)、s701和s650滚压成型铝型材、简单的模块化挤压框架外壳、结构集成冷却板(蓝色)和防火铝底板。(Novelis)
电动汽车电池外壳是子系统设计、材料创新和车辆整合技术的热门领域。
无论被称为电池包、电池盒或电池托盘,这个用来包裹和保护电动汽车电池及其辅助电气和热管理硬件的结构是电动汽车行业中最重要的子系统。OEM和供应商专家告诉SAE,优化电池组涉及到大量的制造工艺和材料的选择、重量和封装的权衡、安全规定、结构设计与工程挑战。
麦格纳为福特F-150 Lightning设计的铝电池结构。(麦格纳) 麦格纳全球研发集团车身和结构部高级经理Darren Womack最近在一场分析师会议上问道:“你希望将电池组用螺栓固定在车身上,还是集成到车身结构中?”他指出,热冲压、冷冲压、滚压成型、液压成型和铸造工艺,以及钢、铝、复合材料和热塑材料等,都是当前热门的电池封装技术。
Womack指出,OEM希望减少多余结构以优化封装空间,并减少重量和复杂性。将电动汽车电池集成到汽车底盘会涉及到各种配置。现已投产的比亚迪CTP(Cell-to-pack)技术将电池直接置入电池包中,取消了中间模块;CTC(Cell-to-chassis)技术则将电芯与汽车底盘、电驱动和热管理系统进行集成设计,将所有电池部件置入汽车白车身,并取消了单独的电池包。
在这种设计中,底盘和车身侧结构可以分别充当电池的底板和侧面,包括特斯拉在内的一些公司正在对该技术进行研究。此外,抗冲击性能、精确的电池包组装和牢固密封对这种设计至关重要。 著名铝制品企业Novelis的全球汽车战略和营销总监Mario Greco解释说:“每家OEM都想拥有一本‘指南’,使其能够根据自家标准(包括电芯的形态、电池尺寸和车型)从各种技术中进行挑选。不过,没有任何一种电池外壳解决方案能符合所有人的要求。”
Novelis的Mario Greco表示,每个OEM都有自己的电动汽车电池外壳设计和工程方案。(Novelis) 例如,单件冲压外壳是一种潜在的大容量封装解决方案。Greco表示,这种外壳可能包括集成式冷却结构,更适合CTC而非CTP设计。“我觉得将来可以看到‘滑板底盘’和下一代一体式架构的融合,因为正在进入电动汽车领域的OEM都拥有全新的一体式架构,而且这些架构都会使用很长时间。”
宽广的设计空间
麦格纳电池托盘部全球首席工程师GregorKlement表示,尽管液冷锂电池组非常沉重,但电动汽车的重量仍有下降空间。他认为,由于轻金属和复合材料的发展,“电池与车身整合将会是未来的趋势。麦格纳的研发部门正在研究CTC解决方案,而我们也发现客户也在关注这个方向。通过去除多余的结构部件,我们有望在减重和降本方面取得显著成效。”但他认为虽然电池成本一直在降低,但电池重量所带来的负担永远不可能被完全抵消。
麦格纳拥有福特F-150 Lightning、通用悍马电动汽车和雪佛兰Silverado电动汽车的电池结构业务(麦格纳) 凯迪拉克超豪华轿车——2024款Celestiq的项目工程经理Jeremy Loveday指出,由于汽车电气化刚刚起步,许多电动汽车的子系统开发正处于关键阶段。
在这种情况下,一级供应商推出了短续航和长续航两种解决方案供OEM进行评估。杜邦在2022年底发布的一款概念产品——三合一电池盒是模块化设计的新案例,这种设计将电池冷却系统、电气互连系统和结构部件进行整合,其外壳由杜邦的Zytel HTN树脂制成,这是一种耐高温的尼龙基聚酰胺。
杜邦公司的三合一电池盒概念产品是模块化设计的一个新例子,它整合了电池冷却、电气互连和结构部件。它的外壳是由该公司的耐热材料Zytel HTN制成的。(杜邦) 据杜邦集团交通和材料部电池材料业务开发负责人Frank Billotto介绍,概念款三合一电池盒拥有半直接冷却系统(电芯通过接线片进行冷却),而且电气互连系统便于电池盒的组装。他表示,这种设计能让电池拥有更大的能量密度,可以提高车辆的续航里程和封装效率。
“电池盒之争”再次激发出工程师和材料科学家的创造力。目前大约80%的电动汽车依然使用铝外壳,但工程师很快注意到,根据车辆类型、负载循环、容量和成本的不同,有大量替代方案可供选择。 铝挤压型材和板材供应商Constellium(肯联铝业)的北美汽车技术总监AndreasAsfeth博士提出:“我认为将来会有更多电池组使用轻质钢外壳,主要集中在小型短续航车辆上。”他承认钢材具有“强大的成本竞争力”,尽管钢比铝重得多,但对小型汽车的电池而言这不是一个严重的问题。
但对于大型长续航汽车而言,Asfeth认为:“电池代表了汽车的价值。电池越大,铝对电池组就越有意义”。不过,通用汽车旗下重达9000磅(4082千克)的悍马电动车反其道而行之,采用了复合材料电池外壳。另外,与Model S和Model X相比,特斯拉也减少了Model 3和Model Y电池外壳中的铝含量。特斯拉在一份公开声明中表示,其柏林工厂生产的电池组结构的上下盖预计将由钢材制成。
铝材主导市场
铝型材目前在电动汽车电池组的设计中发挥着重要作用。(Constellium) 与同等体积的钢外壳相比,铝外壳的重量可减少40%。Asfeth表示,最适合用于电池外壳的合金是6000系列铝硅镁铜合金,而且这些合金还高度符合报废回收要求。
他说,目前最先进的底板解决方案是使用峰时效态的高强度6111合金,与同等体积的5754-O态合金相比,其重量可减少30%。 据Asfeth介绍,肯联铝业正在密切关注车辆的抗冲撞要求,并且开发了一种具有“成本竞争力”的4xxx系列合金,该合金具有80 GPa的弹性模量和350 MPa的屈服应力,并有望减少40%的重量。
他补充道,4xxx系列合金的厚度和宽度与6000系列合金类似,并且兼容传统的冷成型技术。 肯联铝业还在开发一种7075-T6型合金。Asfeth在一场汽车研究中心网络研讨会上向观众透露,这种材料具有500 MPa的屈服应力和70 GPa的弹性模量。其潜在应用场景包括对抗冲撞性能要求极高的电池组底板。
然而,这种新合金需要使用特殊的制造工艺,其增加的成本可能抵消掉10%减重所带来的效益。这就需要在电池盒和电动汽车开发之间作出权衡。 6xxx系列铝合金被用于制造两种不同的先进挤压合金,这两种合金是肯联铝业最近推出的双框架电池组外壳原型使用的主要材料。
该原型的内框架(在受到冲撞时用于保护电池的第二层支撑)使用了经强度优化的6000系列合金(HSA6系列);用作冲撞缓冲区的外加固部件使用了延性6000系列合金(HCA6系列)。不过Asfeth指出,如果电动汽车行业转向使用固态锂电池,封装设计可能会随之发生改变。他说:“固态电池可能具备部分承重功能,因此这种电池对外壳结构的要求较低。”
模制电池包的前景
铝在电动汽车电池外壳中的主导地位并未吓退复合材料和塑料供应商。他们正在开发新的配方和工艺,希望匹配或超越铝的性能和成本竞争力。
SABIC为中国市场的本田CR-V插电式混合动力车型提供聚丙烯顶盖。(SABIC) 热塑材料巨头——SABIC(沙特基础工业公司)的电动汽车电池和电气部门全球汽车总监Dhanendra Nagwanshi说:“目前的电池设计大多采用现有材料和技术,使用了大量未经优化的金属。”他认为,与铝相比,新一代热塑材料可根据应用情况将重量减少30%至50%。他表示,新一代热塑材料还具有与铝同等或更好的抗冲撞性能,还可以通过简化组装工艺降低成本,对环境的影响也更小。工程师对热塑材料电动车电池托盘的兴趣始于通用汽车的1990款Impact概念车,随后的量产款EV-1使用了由玻璃填充聚丙烯(PP)制成的底盘。
SABIC的最新创新成果直接瞄准了铝的弱点之一——极高的导热性。铝在大约630摄氏度(1166华氏度)时开始熔化,内部热失控产生的高温可导致电池起火,温度可达1100摄氏度(2012华氏度)。铝在高温下也会直接燃烧,1975年美国海军贝尔克纳普号导弹巡洋舰与肯尼迪号航空母舰的相撞事件就是证明,相撞引发的大火融化了贝尔克纳普号上部结构中的大部分铝。
Nagwanshi指出,SABIC开发的新型Stamax FR长玻璃纤维PP具有特殊的阻燃性能。他说:“当这种材料与火接触时就会烧焦,随后焦炭会构成隔热层。”SABIC根据电池外壳材料UL2596标准进行的测试表明,这种塑料可承受1000摄氏度(1832华氏度)的高温长达30分钟,“这也是铝出现穿孔现象的温度阈值”,Nagwanshi指出。《电动汽车安全全球技术法规》(GTR 20)的目的是在热失控期间保护乘客至少5分钟。这项标准已被中国采用,欧洲和其他地区也将陆续采用。 目前,SABIC正在生产本田为中国市场设计的阻燃PP电池组盖板。这种盖板取消了热毯设计,其重量比同类型金属盖板低40%。
下一代热塑材料电池组和模块原型正在开发中。近日,总部位于罗德岛的Tri-Mack Plastics展示了仅由8层单向碳纤维增强热塑性复合材料(TPC)带制成的高强度轻质外壳,其厚度仅为1mm(0.040英寸)。该公司的工艺工程经理Ben Lamm指出,与Tri-Mack的制造工艺相结合,这种材料可为部件的几何形状设计、整合以及集成式EMI应对措施提供新思路。 树脂材料和化合物领域也出现了与电池盒相关的新进展。SABIC的全塑料电动汽车电池底盘集成了冷却通道和撞击保护元件。
Nagwanshi表示,与铝制电池组相比,这种底盘可以减少12%的重量。基于Stamax FR长玻璃纤维PP的塑料金属集成结构也正在研发,测试已表明这种结构符合跌落测试要求。工程师对其能够吸收“大量”能量的性能感到鼓舞,因为这同样是车辆侧面碰撞测试的要求。
Nagwanshi说,热塑材料的两个特点使其在电动汽车电池盒方面与铝相比具备竞争力。其中一个是各向异性导热性,即塑料在一个方向传导和消散热量的同时,在其他方向上确保隔热的特性。他指出,金属能够导热,因此电动汽车需要使用热毯,比如特斯拉使用的云母板。
对于热塑材料而言,Nagwanshi说:“几何形状不是问题,热塑材料很容易通过注塑成型技术打造出蜂窝结构,以实现零件需要的强度。若把几何形状与高性能玻璃纤维增强树脂结合起来,其结构性能可与铝相媲美。而且制造热塑材料部件所排放的二氧化碳比铝部件低10%至15%左右。” 他认为SMC之类的热固性塑料在某些方面是热塑材料的竞争对手,但他批评这种材料“没有得到优化”,因为“热固性塑料还需要热毯以及二次制造,而且无法进行回收”。 Teijin Automotive Technologies(帝人汽车技术公司),科尔维特C8的热固性外板供应商,公司的新业务发展和新市场总监——Hugh Foran可能不同意同行的观点。他认为,SMC再研磨技术还有许多二次利用的机会。在电动汽车市场方面,Teijin已经成为热固性电池盒顶盖的主要供应商。
Teijin多种材料的电池结构展出。(Teijin) Foran告诉SAE:“我们已经为各类电动汽车生产了30多种热固性电池盒顶盖。”顶盖通常是一块含有阻燃剂的聚合物或钢板,与铝相比,它能更长时间地阻止内部火灾并提供碰撞保护。但是,这家总部位于日本的供应商的目光不仅局限于顶盖。
Foran说:“我们的研发小组已经为电池盒开发出五种不同配方的SMC”,一种是“简单的乙烯基酯玻璃纤维”,另一种是含有阻燃剂ATH(三水铝)的SMC。Teijin也生产了膨胀型SMC,这种材料的表面可为底层基材提供热屏障和物理屏障。当感受到火焰或热量时,膨胀型材料可以通过“结痂(scab)”来进行自我保护。
此外,Teijin一直在使用酚醛树脂来打造部分电池盒原型的部件,这些部件可以耐受最高1100摄氏度的温度,公司的客户正在对其性能进行测试。 Foran说,电动汽车制造商努力解决的另一个鲜为人知的问题是电池包的泄漏问题,无论使用哪种结构材料都会出现这种情况。
为了解决这个问题,Teijin开发出一种不需要填料和密封的无通孔式底盘,不过,装配孔是有的。复合材料或塑料封装结构还具有模压装配点,而非焊接装配点。Foran说:“曾有一家OEM客户要求将应力传感器一起模压进材料中,这样他们就可以在车辆层面上了解发生的任何冲撞。” 2028年的电动汽车电池外壳会与2023年的有明显不同吗?麦格纳的Klement认为:“可以看到一些客户在未来几年内开始转向结构性电池和CTC电池设计,但其他客户仍处于概念阶段。这种转变已不再遥远,但不确定是不是所有厂商都会往这个方向发展。”
审核编辑:刘清
-
电动汽车
+关注
关注
156文章
12226浏览量
232853 -
OEM
+关注
关注
4文章
404浏览量
50553 -
汽车电池
+关注
关注
0文章
136浏览量
20237 -
热管理
+关注
关注
11文章
452浏览量
21921 -
SAE
+关注
关注
0文章
27浏览量
13296
原文标题:Battle for the Box ——“电池盒”的竞争刚刚开始!
文章出处:【微信号:SAEINTL,微信公众号:SAE International】欢迎添加关注!文章转载请注明出处。
发布评论请先 登录
相关推荐
DLPDLCR4710EVM-G2是否可以在flash或内部存储中设置投射的彩色图像?
ADS1251刚开始采集数据异常是什么原因导致的?
锂电池防水盒可定制加工厂家有哪些
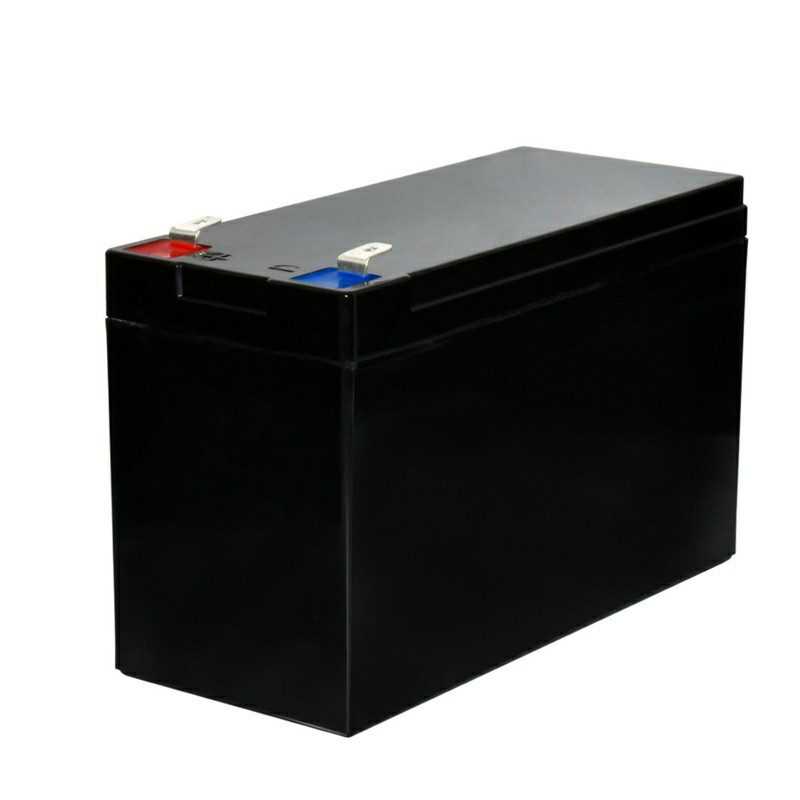
电池盒气密性检测仪的常见故障及解决方法

基于MC33772芯片的电池接线盒方案
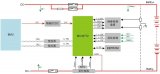
评论