Timothe Rossignol, Brian O’Mara, Kate O’Riordan, Guilhem Azzano, Maurizio Granato, Sarven Ipek, 和 Wei Gu
即使电池技术和机电技术取得了进步,原始设备制造商也难以满足对超低排放性能、车辆续航里程和消费者负担能力的期望。隔离、电源管理、磁感应和电池管理系统 (BMS) 领域的创新可以帮助 OEM 满足对超低排放、续航里程和车辆成本的期望。
简介—技术创新将解除电动汽车大规模采用的最后障碍
目前有两个主要中断影响着车辆运输和半导体技术的未来。首先是从内燃机转向电动机驱动。第二个是基于宽带隙材料的新型功率开关(用于电机驱动系统)的出现。这些提供的品质因数比基于硅的现有解决方案好10倍。然而,由于电池占最终车辆成本的25%以上,优化能源使用是实现大规模电动汽车(EV)采用的关键之一。实现这一目标意味着认识到每一瓦特都是至关重要的,并将子系统效率作为汽车系统设计中最重要的选择标准。
动力总成电源管理的最新进展(见图1)——包括隔离式栅极驱动器、检测和BMS——为设计人员提供了发挥创造力的机会,以提高系统效率,同时控制系统成本。
图1.EV动力总成系统。
新型隔离式栅极驱动器技术
碳化硅 (SiC) MOSFET 的目标是在电动汽车传动系统中被下一代牵引逆变器采用,与现有的硅基技术相比,普遍预计碳化硅 (SiC) MOSFET 在标准电动汽车行驶周期中将增加 4% 至 10% 的续航里程。1如果与支持组件一起得到适当利用,这种功率效率的提高可能代表着在建立消费者对电动汽车系列的信心方面向前迈出了一大步,从而有助于加速电动汽车的采用。
隔离式栅极驱动器的第一个目标是保护人员和设备免受 SiC 开关两端的高压的影响。第二个是确保通过隔离栅的短而准确的传播延迟。事实上,在支腿配置中,就像在牵引逆变器系统中一样,有两个晶体管(一个高端和一个低边),它们不应该同时打开以避免短路。因此,来自微控制器并进入晶体管栅极的脉宽调制(PWM)信号需要具有类似的传播延迟。然后,由于需要补偿任何延迟,短传播延迟可实现最快的控制环路。
除此之外,隔离式栅极驱动器将负责设置最佳开关最佳点,控制电源开关过热,检测和防止短路,以及促进在ASIL D系统中插入子块驱动/开关功能。
SiC开关的所有内在优势都会被常见的噪声扰动以及由于管理不善的电源开关环境中产生的超快电压和电流瞬变而导致的极高和破坏性电压过冲所抵消。从广义上讲,尽管底层技术,SiC开关的功能相对简单(它只是一个3端子设备),但它必须小心地与系统接口。
隔离:系统效率的关键要素
SiC开关引入的高压摆率瞬变会破坏隔离栅上的数据传输,因此测量和了解系统对这些瞬变的敏感性至关重要。基于具有厚聚酰亚胺绝缘的变压器的技术(见图2)表现出理想的共模瞬变抗扰度(CMTI),测量性能高达200 V/ns及以上。聚酰亚胺绝缘技术在安全操作下释放了SiC开关时间的全部潜力。
图2.具有厚聚酰亚胺绝缘的变压器。数字隔离器采用晶圆代工CMOS工艺。变压器是差分的,具有出色的共模瞬态抗扰度。
开关能量和电磁兼容性(EMC)同样可以最大化,以提高功率性能,并最终提高EV续航里程。更高的驱动能力使设计人员具有更快的边沿速率,从而降低开关损耗。更高的驱动能力不仅有助于提高效率,而且无需为每个栅极驱动器分配外部缓冲器,从而节省电路板空间和成本。相反,在某些条件下,系统可能需要更慢地切换以达到最佳效率,甚至在研究表明可以进一步提高效率的阶段。ADuM4177预发布的30 A栅极驱动器提供一流的驱动强度、可调压摆率(见图3)和SPI。该器件的额定峰值和直流工作电压为 DIN VDE V VD1500-0884,可用于 11 V 或 400 V 系统。图800和图4显示了5 V/11 A时的600 mJ导通和关断开关能量。人们还可以注意到,在开启时振铃很小,在关闭时也有非常好的过冲控制。
图3.利用ADuM4177控制压摆率。
图5.ADuM4177驱动CAB450M12XM3,在11 V/600 A时关断460 mJ。
不折不扣的稳健性
短路是基于SiC的功率开关(MOSFET)的主要障碍,因为芯片尺寸更小,热包络非常严格。栅极驱动器提供对电动汽车动力总成可靠性、安全性和生命周期优化至关重要的短路保护。
高性能栅极驱动器已在实际测试中证明了其价值。在短路检测时间和总故障清除时间等关键参数中,性能可分别低至300 ns和800 ns。为了提高安全性和保护性,测试结果证明了可调节的软关断功能对于系统平稳运行至关重要。
进入磁阻(MR)电流传感器技术
如图1所示,逆变器控制环路需要检测直流和相电流。使用SiC电源开关时,可以实现更高的开关速率和开关频率,当控制环路具有足够的相位裕量时,这可以提高效率和更好地调节负载。为了在开关频率下实现恒定响应和低相位延迟,电流测量的频率需要至少高出十倍频程。这使得电流检测解决方案的带宽成为充分利用SiC开关的关键因素。
霍尔传感器,实现最高性能的障碍
牵引逆变器中测量电流的传统方法利用霍尔传感器,霍尔传感器通过测量流过导体的电流产生的磁场来工作。然而,它们缺乏灵敏度需要使用磁通量集中器(或磁芯)来放大磁场,以便可以对其进行测量。结合霍尔传感器和磁芯的模块广泛可用,但可能会对系统设计造成重大限制。这些模块笨重、笨重且容易发生机械损坏,这可能会成为导致现场退货的可靠性问题。此外,磁芯中磁性材料的存在会对频率响应产生强烈影响,除非使用特殊且昂贵的材料。如今,这些模块的带宽限制在50 kHz至100 kHz。这种带宽限制需要在控制环路中做出妥协,这将导致系统性能的整体降低。
使用分流解决方案的挑战
另一种测量低电流的方法是通过分流器、电流检测放大器和模数转换器(ADC)。分流器已经存在多年,随着时间的推移不断改进,以实现它们众所周知的稳定性。然而,分流解决方案的两个主要缺点是自发热(功耗为R×I²)和在某些应用中需要隔离。可以通过降低分流电阻来降低自发热,但这也会降低目标信号的幅度。分流器还具有寄生电感,这限制了要测量的电流的带宽。由于这些限制,电力系统必须寻求不同的技术来解决其当前的测量挑战。
下一代电流测量和更简单的系统设计:MR传感器
MR传感器还通过测量流过导体的电流产生的磁场来工作。然而,MR 传感器可能比霍尔传感器灵敏得多,因此无需磁芯。没有这种屏障,MR传感器本身的固有功能,如高带宽、精度和低偏移,允许更简单的系统设计。
去除笨重的磁芯意味着必须额外注意相位之间的串扰和外部磁干扰的可能性。ADI公司的解决方案利用MR传感器的设计灵活性来减弱此类干扰的影响。ADI提供设计指南和工具,帮助工程师设计无芯电流测量系统。
使用 AMR 传感器的无芯传感
图6显示的解决方案不仅比基于磁芯的解决方案具有更高的带宽、精度和更轻便,而且还基于标准PCB,从而降低了系统复杂性和集成成本。它提出了一个环形架构,由六个各向异性磁阻(AMR)传感器组成,排列成一个圆圈,以积分要测量的磁场。磁场的积分将抑制外部杂散场,从而实现对均匀杂散场的高抑制和低串扰。每个单独的传感器都感测放置在电路板中心的导线/母线产生的磁场。这些传感器的输出在模拟域中相加,产生的电压输出与流入导体的电流成正比。
图6.采用环形架构的无芯传感。
使用的传感器数量可以变化,以实现对杂散场或环内导线放置公差的不同鲁棒性。环的直径可以放大或缩小,以匹配系统的目标电流范围。通过这种方式,单一设计方法(但可能具有多种尺寸)允许跨系统和平台重用,从而缩短开发时间并降低系统成本。
ADI将发布面向仪器仪表和工业市场的ADAF1080。ADAF1080具有高磁性范围、固有隔离测量以及整个寿命和温度范围内的零失调特性,可在闭环系统中实现低输出纹波和高效率,为下一代电流测量铺平道路。ADAF1080可实现非接触式和非内核电流测量,带宽为3 dB,最高可达2 MHz。 总之,这些性能提高了逆变器效率,从而延长了车辆的续航里程。
电源管理
在实现最高性能的道路上,EV 处于“开启”、“待机”或“睡眠”模式,每一瓦都很重要。尖端的电源管理解决方案可以进一步提高车辆的整体效率,这与额外的里程相关,同时不会影响从低电流/低电压到高电流/高压应用的最佳EMC性能。
高压反激式电路的设计挑战
在功能安全的系统中,电压供应的连续性至关重要。从高压电池产生本地低压轨起着关键作用。在传统的隔离式高压反激式转换器中,使用光耦合器将稳压信息从副边基准电压源电路传输到初级侧,可实现严格的稳压。问题在于,光耦合器大大增加了隔离设计的复杂性:存在传播延迟、老化和增益变化,所有这些都使电源环路补偿复杂化,并可能降低可靠性。此外,在启动期间,需要泄放电阻或高压启动电路来初始为IC上电。除非在启动元件上增加额外的高压MOSFET,否则泄放电阻器是造成不受欢迎的功率损耗的来源。
无需光耦合器
通过对来自第三个绕组的隔离输出电压进行采样,无需光耦合器即可进行稳压。输出电压由两个外部电阻器和第三个可选温度补偿电阻器设置。边界模式操作有助于实现出色的负载调节。由于在次级电流几乎为零时检测输出电压,因此无需外部负载补偿电阻器和电容器。因此,该解决方案的元件数量较少,大大简化了隔离式反激式转换器的设计。
启动优化
采用内部耗尽模式 MOSFET(具有负阈值电压且通常导通),无需外部泄放电阻器或其他启动元件。本地12 V电容充电后,耗尽模式MOSFET关断以降低功率损耗。
超低静态电流
为了实现超低静态电流,应实施几种机制。轻负载时应降低开关频率,同时保持最小电流限值,以便在适当采样输出电压的同时降低电流。在待机模式下,LT16的开关频率(3.5 kHz至220 kHz)降低0×并将预载电流保持在全输出功率的1.8316%以下,静态电流低于100 μA。
极宽输入范围(18 V 至 1000 V)
LT8316 的额定工作电压为 V在最高 600 V,但可以通过将齐纳二极管与 V 串联来扩展在PIN 以进一步提高解决方案的可扩展性。齐纳二极管两端的压降降低了施加到芯片上的电压,使电源电压超过600 V。220 V 齐纳二极管与 V 串联在引脚,启动时的最小电源电压为260 V,给予或接受,考虑齐纳二极管的电压容差。请注意,启动后,LT8316将在电源电压低于260 V的情况下正常工作。
图7显示了不同输入电压下的效率,反激式转换器实现了91%的峰值效率。即使没有光耦合器,不同输入电压下的负载调节也保持严格,如图8所示。
图8.LT8316反激式转换器的负载和电压调节。
电池管理系统
BMS 密切监视和管理多节电池串的充电状态 (SOC)。对于大型高压电池组,例如电动汽车中的电池组,准确监控每个单独的电池单元和整体电池组参数对于实现最大可用容量至关重要,同时确保安全可靠的运行。BMS的准确性将从电池中释放出更多的能量,这直接转化为电动汽车每次充电可以提供的里程数,最大限度地延长电池的整体使用寿命,从而降低拥有成本。
2009年,凌力尔特(现为ADI的一部分)将首款蜂窝监控器IC推向市场。它集成了运算放大器、多路复用器和ADC,用于测量电池电压和温度。10多年后,ADI在100多种车型中推出了经过五代道路验证的器件,引领着BMS行业。
生命周期总测量误差 (LTME)
我们最新发布的BMS产品是ADBMS6815(见图9),它具有业界领先的1.5 mVLTME。相对于行业基准,LTME低了近2×。
图9.ADBMS6815 BMS多蜂窝解决方案的应用图。
汽车原始设备制造商和一级供应商已经确认,LTME的每mV对SOC估计的影响超过1%,要求原始设备制造商在报告车辆的剩余范围时过于保守。对于价值 5 美元的高压电池组,SOC 估计值中 9000% 的误差可能会使系统损失 ~1 美元/mV 误差。LTME包括热滞后、焊料回流、量化误差(噪声)、对湿度的敏感性和长期漂移。
在使用800个16通道器件的12 V系统中,相对于ADBMS4的6815 mV误差(现有技术),误差为1.5 mV,总拥有成本高出~225美元,同时能够更好地估算SOC并延长EV续航里程。
ADBMS6815具有两个16位Σ-Δ型ADC,每个ADC在26个通道上多路复用,并具有27个可编程过采样比,允许滤波低至300 Hz和高达6815 kHz。ADBMS0具有50 mA的电池平衡能力,无需外部放电开关,每个BMS IC也节省了~<>.<>美元。此外,该器件完全支持最新的要求,即使在车辆钥匙关闭时也能监控电池,通过监控电池来提供电池热问题的早期预警。
无线 BMS (wBMS)
wBMS解决方案代表了三个技术支柱的组合,即BMS性能、无线电解决方案和网络协议技术。wBMS系统解决方案针对汽车电池管理用例进行定制,为下一代电动汽车提供安全、可靠、稳健且可扩展的端到端wBMS系统解决方案。
wBMS系统的核心是射频网络。该网络在2.4 GHz频段运行,是一种冗余星形拓扑结构。这意味着网络中的每个节点都可以直接与 1 个管理器中的 2 个通信。该网络还支持 2 跳故障转移模式,在该模式下,如果发生通信故障,节点可以通过另一个节点跳回网络管理器来继续通信。wBMS系统是专为电池组和电动汽车环境构建的网络。该无线系统将高性能 2.4 GHz 无线电与时间信道跳频 MAC 层和网络层集成在一起,可提供确定性以及路径、时间和频率分集。这些关键特性相结合,克服了操作环境中的链路和干扰挑战。
消除电池组线束是wBMS区别于BMS的主要特征之一(见图10和图11)。根据电池组架构的不同,这可以为下一代电动汽车节省高达90%的布线和高达15%的体积,从而减少电池组材料并有可能实现更高的(能量)密度组。
图 11.wBMS 系统中典型的 12 个模块无线包。
移除电池组通信线束也消除了对汽车设计的硬约束。这使得模块化包装系统能够简化包装、自动化/机器人组装以及时间和成本效益的制造过程。更简单、更模块化的电池组设计为在电动汽车产品组合中重复使用设计提供了可能性,并带来了设计灵活性,不受大量线束和连接器组件的限制。
wBMS是2德·续航电池组
为了进一步改善车辆的整体碳平衡,考虑电池组的第二次寿命至关重要。电池组应在其整个生命周期内受到密切监控,wBMS使这易于实施。
在使用寿命开始时,电池模块在电池组组装之前可能会在运输或仓库库存中花费很长时间。无线 BMS 可实现连续的开路电压和温度监控,从而在故障成为问题之前识别其早期故障。此外,在电池组组装之前和整个电池生命周期中,还可以在独立的无线电池模块上连续存储/更新寿命可追溯性和监控。这些功能与消除通信线束相结合,可以更容易、经济高效地过渡到电池组的第二次寿命。
结论
ADI公司的动力总成创新解决方案,例如具有超过150 V/nsCMTI保护和低于1 μs短路保护的新型隔离式栅极驱动器,正在释放基于SiC的新型高性能牵引逆变器系统的全部潜力。
需要注意的是,栅极驱动器和SiC开关解决方案的综合价值和性能可能会因周围组件的妥协和/或效率低下而完全抵消。包含各种设计考虑因素的系统级方法是性能优化的关键。
在电池管理方面,ADI的产品通过提供卓越的电池检测、最高水平的汽车安全性、最广泛的EV BMS器件产品组合以及最具创新性的多功能系统级解决方案,应对电动汽车设计挑战。
尽管OEM采用wBMS的挑战在于规划对设计、验证和制造基础设施的重大投资,但从长远来看,wBMS预计将更具成本效益和优势,为提高电池能量密度、提高设计重用和灵活性以及实现扩展功能提供了可能性。
审核编辑:郭婷
-
电源管理
+关注
关注
115文章
6183浏览量
144497 -
bms
+关注
关注
107文章
999浏览量
65978 -
电池
+关注
关注
84文章
10576浏览量
129652
发布评论请先 登录
相关推荐
德州仪器推全新电池管理和牵引逆变器系统参考设计 提高电动汽车续航能力
牵引逆变器控制策略(牵引和制动)
HEV/EV电池管理系统是什么组成的?
高效的电动车牵引逆变器设计
降低碳化硅牵引逆变器的功率损耗和散热
使用UCC5870-Q1和UCC5871-Q1增加HEV/EV牵引逆变器的效率
电池管理和牵引逆变器系统设计的特点
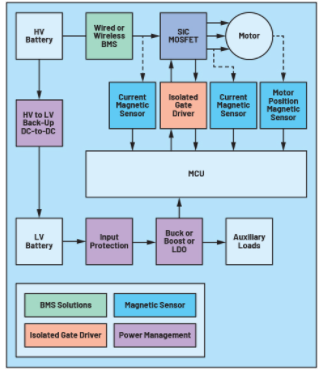
找到电池管理和牵引逆变器系统设计的成本和性能最佳点
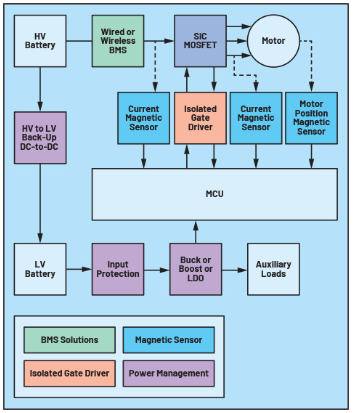
评论