焊接是光伏组件生产中重要的工艺流程,就拿光伏组件中常见的组成部分——接线盒来举例,作为完成组件电力传输的关键器件,在组件的自动化生产过程中,接线盒的电极焊接质量直接关乎组件的性能,焊接质量检测的重要性不言而喻。
以往,工厂常用的检测方式为人工目检,由于检测项多、检测要求高,人工检测不仅成本较高,还常会发生检验不充分的问题,在制造企业数智化升级的趋势下,将智能机器视觉检测技术方案引入生产流程,助力生产效率和产品质量提升已经成为越来越多企业的选择。
针对光伏组件企业在生产中遭遇的种种痛点,维视智造自2017年以来,专注于接线盒焊接设备方案的实践、研究。在这六年时间里,针对“热压焊”、“加锡焊”和“激光焊”的焊接工艺进行了深入验证、开发。配套的视觉方案经过多次迭代后,均实现了标准化的量产方案。尤其是最新的激光焊视觉方案,在经过了3代设备的量产后,从精准度到稳定性均得到了行业内的广泛认可。
解析场景痛点,维视智造独创“三级AI定位方案”
在接线盒生产的焊接场景中,大致包含两种工艺;一是“盲焊”工艺。顾名思义,就是焊接过程中不定位“汇流条”位置,仅定位“接线盒”位置,直接在接线盒极片上打出激光焊疤。该工艺劣势是无法保证汇流条上的焊疤数量,无法保证焊接强度,同时也会损伤接线盒极片。
(VisionBank AI基于盲焊工艺的焊接效果检测示意图)
第二种是精准焊接。就是在焊接之前精确的获取汇流条的坐标、角度,实现焊疤的精准焊接。可以保证激光焊疤全部在汇流条上,保证了焊接强度,也不会影响接线盒极片。因此逐渐成为行业广泛选择的焊接工艺。
但激光焊工艺也对视觉系统的匹配提出了更高的要求,这是因为在实际生产环境中,在汇流条按压等环节经常会发生各种情况,需要人工介入处理,这不仅使整体生产效率变低,也导致后续的视觉检测方案极难设计,稳定图像难以获取,视觉检测失败率增高。
维视智造针对性研发出“三级AI定位方案”:将复杂的接线盒激光焊接定位检测,依据实际生产工艺流程中按压前、后和焊后的不同检测需求,基于维视智造强大的系统解决方案能力,采用AI图像专用算法工具和正反检测技术的综合处理,融合创新的光伏定制化软件算法模块,配合软硬一体的系统化解决方案,实现关键点精确定位,在保证定位精度的前提下,满足了近100%的定位成功率。
自研专用神经网络模型+硬件系统支撑检测表现更出色
智能工厂时代,任何自动化设备的生产结构都需要进行检测,从而完成闭环控制,激光焊接机也不例外。激光焊接机的焊后检测需求一般包括漏焊、焊歪、焊疤成型不良、虚焊(焊疤过浅)等缺陷。维视智造基于近20年的行业服务经验,研发了专用焊接缺陷检测专用的神经网络模型。
通过维视专业团队定制的硬件方案和VisionBank AI的软件处理能力,系统可稳定检测出各种常见的焊带和汇流带焊接质量缺陷,如:焊带超出、焊带偏移、虚焊、内缩、无汇流条、焊带缺失等,完美解决焊后检的问题。在接近“0漏检”的前提下,“误检率”低于0.5%。
(基于VisionBank AI的焊后检测系统)
维视智造依托20年的技术积累和对光伏生产工艺的深刻理解,和自主研发的智能机器视觉软件开发平台VisionBank AI的强大算法能力及数据管理能力,配合自研行业定制化的硬件系统解决方案,针对国内光伏行业现实需求场景,联合众多优秀上下游合作伙伴,推出了大量光伏行业专业、系统、稳定的视觉检测解决方案,可满足不同自动化程度、不同产能、不同工艺水平的各类光伏企业生产需求。
如今,以光伏组件视觉检测系统为代表的维视方案已批量落地国际光伏头部企业,为数百条光伏产线的数智化升级提质增效;其中,针对光伏电池板接线盒相关生产工位的智能装备视觉检测解决方案,更是集合了维视多项技术专利能力,作为维视光伏组件系列解决方案中的“明星产品”,目前在部分应用场景中已达成80%的市场占有率。维视智造致力成为“光伏组件视觉检测系统领先者”,将持续致以高可靠性、高稳定性的产品,与更多光伏企业联合创新,共赴未来,赋能中国光伏行业高质量发展。
(维视智造光伏应用场景图)
审核编辑黄宇
-
光伏
+关注
关注
44文章
3024浏览量
69046 -
机器视觉
+关注
关注
162文章
4385浏览量
120423 -
焊接
+关注
关注
38文章
3158浏览量
59863 -
维视智造
+关注
关注
0文章
74浏览量
150
发布评论请先 登录
相关推荐
光伏组件的种类与选择 光伏发电的未来发展趋势
中兴通讯展示创新方案与实践成果
大研智造 光伏板线盒引线焊接:激光焊锡机技术的精密制造优势
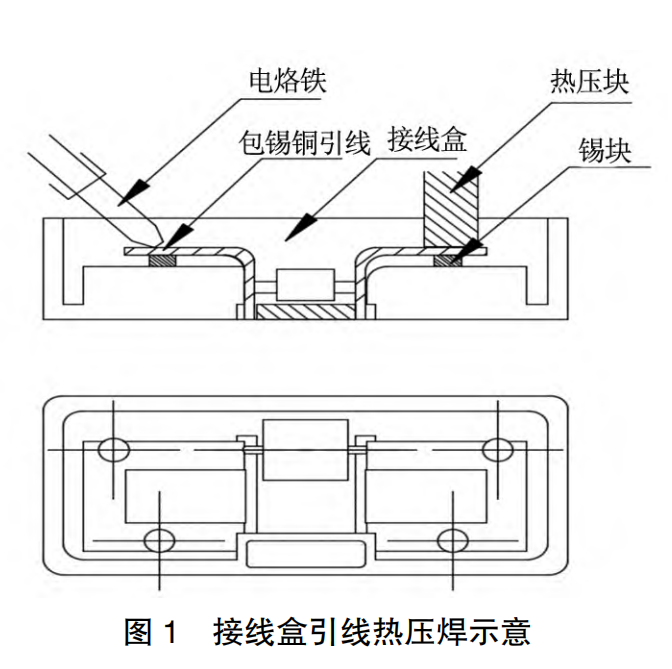
美能光伏带您回顾第二届TOPCon高效电池组件技术高峰论坛高光时刻
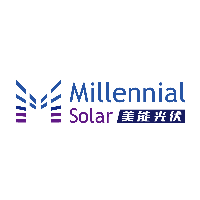
评论