这种双面冷却可实现更好的热性能,从而实现更高的功率密度和效率。DSC 电源模块通常在模块的每一侧使用铜板进行冷却,它们还可能具有额外的功能,例如温度感应二极管和电流感应 IGBT。
图一:DSC与单面电源模块对比(:1)
单面冷却模块存在一些局限性,包括:
高寄生电感 (15-20 nH)
高热阻 (0.1-0.8 K/W)
引线键合是一种主要的失效模式。
这些问题可以使用基于 DSC 的电源模块来解决,该模块具有以下特点:
低寄生电感(小于 10 nH)
热阻降低高达 50%
无焊线,更可靠
延长寿命(按数量级)
增加电流能力和更高的功率密度。
多年来,阿肯色大学开发了不同架构的DSC功率模块,从直接焊锡连接的高压功率模块封装(2012年)到多层LTCC基板堆叠功率模块(2020年)。
建议的解决方案
UA Power Group 针对牵引驱动应用提出的解决方案是集成 DSC 功率模块,目标功率密度为 100 kW/L。
拟议的设计(其分解图如图 2 所示)具有以下特点:
设计新颖:
金字塔形或45度垂直连接块,提供散热路径
基于 LTCC 的中介层。该解决方案提供电气隔离和机械强度,便于上下基板对齐
基于 LTCC / PCB 的交流电源端子,有助于电流感测
可靠的技术:
银烧结
无焊线
综合特点:
去耦电容
基于 SOI 或 SiC 的栅极驱动器
GMR 或霍尔效应电流传感器
温度感应器
图 2:建议的 DSC 电源模块解决方案的分解图(:1)
底部包含焊接到 DBC 基板的 50 μm 铜金属平面。顶部提供用于 SOIC-8 封装焊接的金属焊盘和用于引线键合到 PCB 的连接迹线。引入去耦电容器(参见图 2)有助于显着降低电源环路电感(1.5nH,相对于没有电容器的设计的 11nH 电感)。此外,800V、160A 时的电压过冲减少了 65%(60V 相对于 110V)并且器件应力更小,从而实现更可靠的设计。
栅极驱动器可基于 XFAB 的 180 nm 绝缘体上硅 (SOI) CMOS 工艺构建,具有系统保护功能,如有源米勒钳位、过流检测和欠压锁定。除了极低的栅极环路电感(小于 10 nH)外,该栅极驱动器的栅极驱动器管芯面积很小,约为 3.14 mm x 3.14 mm。对于高温功率模块(高达 175℃),可以集成基于碳化硅 (SiC) 的栅极驱动器。因此,栅极驱动器有两种选择:基于 SOI 或基于 SiC。
电流传感器可以通过 GMR 电流传感器(放置在载流导体顶部)或霍尔效应电流传感器(放置在载流导体附近)来实现。在这两种情况下,传感器都必须位于电源模块的底部开关基板上(交流电位)。PCB 有助于路由来自 AC 端子的 I/O 信号。
底部开关基板上还放置了NTC温度传感器,需要离功率器件很近。PCB 将栅极驱动器、电流传感器电路和温度传感器引脚路由到顶部开关栅极驱动器板上的 I/O 端子(见图 2)。电流密度模拟表明,通过将电流传感器放置在交流端子上,可以实现交流端子上和周围的电流密度。
使用 SolidWorks 热模拟器软件对建议的设计进行了完整的热模拟。建模的触点组包括附件银烧结膏(TC= 60 W/mK,50 μm)和热界面材料(TC= 9.6 W/mK,0.5 mm),而结到环境的热阻 (K/W)为 0.06 K/W。
应用的边界条件如下:
对流系数:10,000 W/m 2 K
环境温度:65°C
每个芯片的估计功率损耗:120 W。
将六个建议的功率模块集成到 200 kW 分段两级三相逆变器中,并在 EV 系统中使用 PM 牵引电机,实现了 100 kW/L 的体积系统功率密度 (PD)。该值比用于带 DSC 功率模块的牵引驱动的体积 PD(约 30 kW/L)要好得多。
-
二极管
+关注
关注
147文章
9647浏览量
166594 -
IGBT
+关注
关注
1267文章
3796浏览量
249141 -
功率密度
+关注
关注
0文章
90浏览量
16896
发布评论请先 登录
相关推荐
如何冷却电源模块,采用双面间接冷却还是单面直接冷却?
高频电源模块驱动电路设计
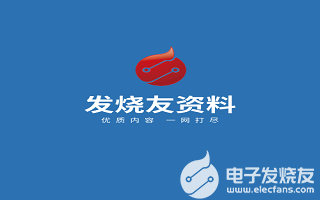
电源模块特点及分类
适用于 200kW 驱动装置逆变器的 AC Propulsion 电源模块
如何看电源模块型号参数,电源模块选型指南
DC电源模块和AC电源模块都有各自的优点和适用场景
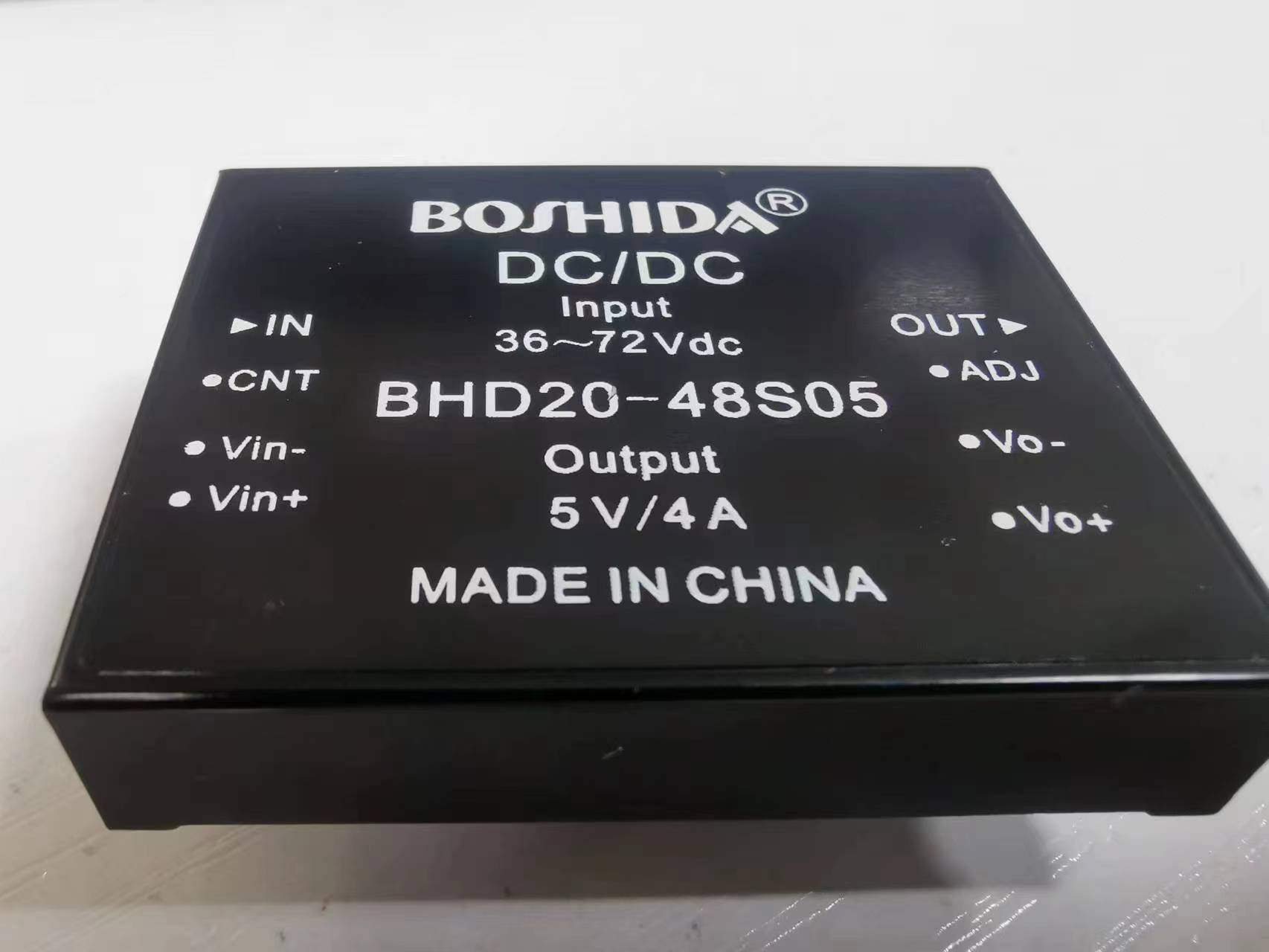
AC/DC电源模块的设计与实现技巧
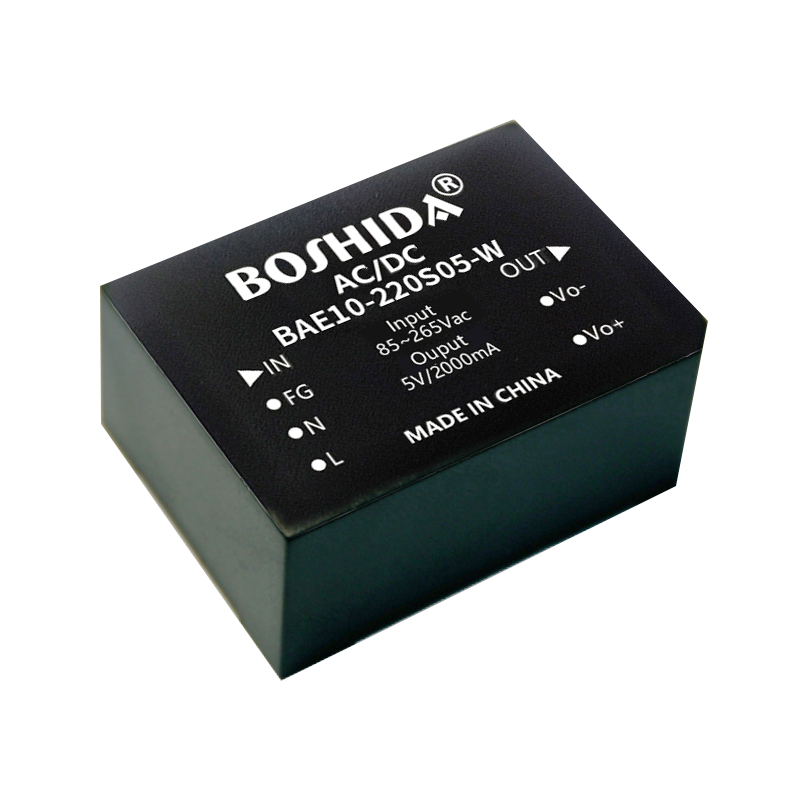
评论