一、问题背景
某水泥厂针对合肥院HFCG180-160辊压机动辊非减速机侧轴承位磨损,轴承型号为232/900CAKF1/W33/C3,轴承位小径尺寸901mm,宽度540mm,锥度1:12,单边磨损量最大处约3mm。
轴承位一旦出现磨损企业如果采用传统修复方法如堆焊后机加工、热喷涂和电刷镀等手段来修复,花费时间较长而且均存在一定弊端,无论是堆焊后机加工还是热喷涂方式,都避免不了热应力无法消除的现象,易造成材质损伤,导致部件出现弯曲或断裂;而电刷镀受涂层厚度限制,容易剥落,且以上几种方法都是用金属修复金属,无法改变“硬对硬”的配合关系。
小编今天要说的是一种轴承位磨损修复新技术---高分子复合材料修复技术,让我们结合现场案例一起看一下。
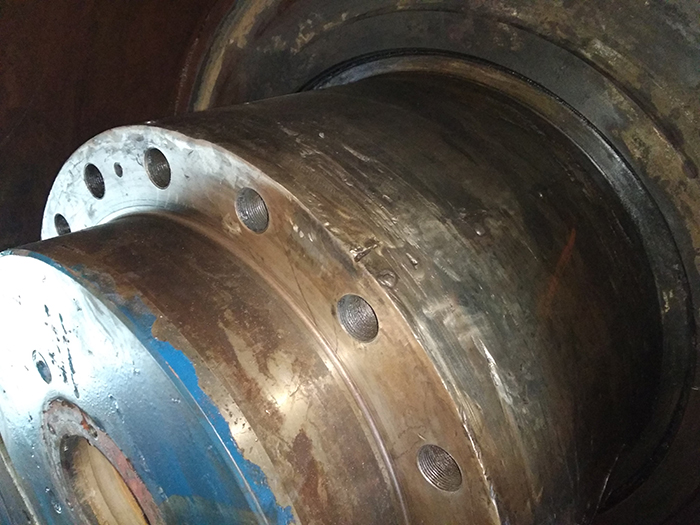
二、高分子复合材料现场修复辊压机动辊非减速机侧轴承位磨损
利用高分子复合材料现场对磨损部位进行修复,是近几年兴起的一种检修模式,其原理是在最大程度减少停机时间,在保证修复精度和满足安装要求的基础上进行修复。高分子复合材料具有超强的粘着力,优异的抗压强度、耐磨性和抗腐蚀性等综合性能,应用于现场金属磨损问题修复时,可以减少设备拆装、减少离线时间,无补焊热应力影响,修复厚度不受限制,同时产品所具有的耐磨性及金属材料不具备的退让性,可确保修复部位达到百分百的面接触配合,降低设备的冲击震动,并大大延长设备部件的使用寿命,为企业提供优异的设备维修维护手段、节省大量的停机时间,创造巨大的经济价值。综合现场情况企业决定采用福世蓝焊接支撑点配合高分子复合材料工艺进行修复。
此类修复材料以应用二十余年的福世蓝高分子复合材料材料的综合性能和性价最为突出,本文案例用的是福世蓝高分子复合材料。
三、修复步骤
1、表面处理:使用氧气乙炔炙烤待修复表面并使用磨光机打磨轴承位表面,直至露出金属原色;
2、焊接支撑点:首先根据螺栓孔的分布在整个轴承位表面均匀画线,支撑点沿线焊接,高度略高于单边磨损量;
3、修磨支撑点高度:以弧度样板尺为基准,使用磨光机打磨支撑点,使其高度与单边磨损尺寸一致;
4、空试支撑点:空试轴承直至在较小的预紧力作用小,保证10-15mm的预紧量,且轴承内圈的压痕分布均匀;
5、清洗表面:使用无水乙醇清洗轴承位表面和轴承内圈表面,轴承内圈表面涂刷福世蓝803脱模剂;
6、涂抹材料:计算材料用量并充分调和均匀后涂抹福世蓝高分子复合材料,建议首先用手直接涂抹,保证高分子材料的填充效果,然后用刮板均匀涂抹,厚度略高于支撑点高度,快速安装轴承,保证预紧量在10-15mm之间;
7、拆卸轴承:待材料固化后拆除压盘和轴承,并去除多余材料、打磨材料釉面;
8、涂抹第二遍材料:再次调和少量高分子材料涂抹薄薄一层;
9、安装轴承:快速安装轴承,整个安装紧固过程控制在时间控制在30-40分钟之内。紧固螺栓时,对称紧固。此次安装螺栓全部紧固到位,剩余预紧量保持在10-15mm左右为宜。
10、后期预紧:设备空载3-5小时紧固一次螺栓,载料6-8小时紧固一次,载料12小时紧固一次,载料24小时紧固一次。
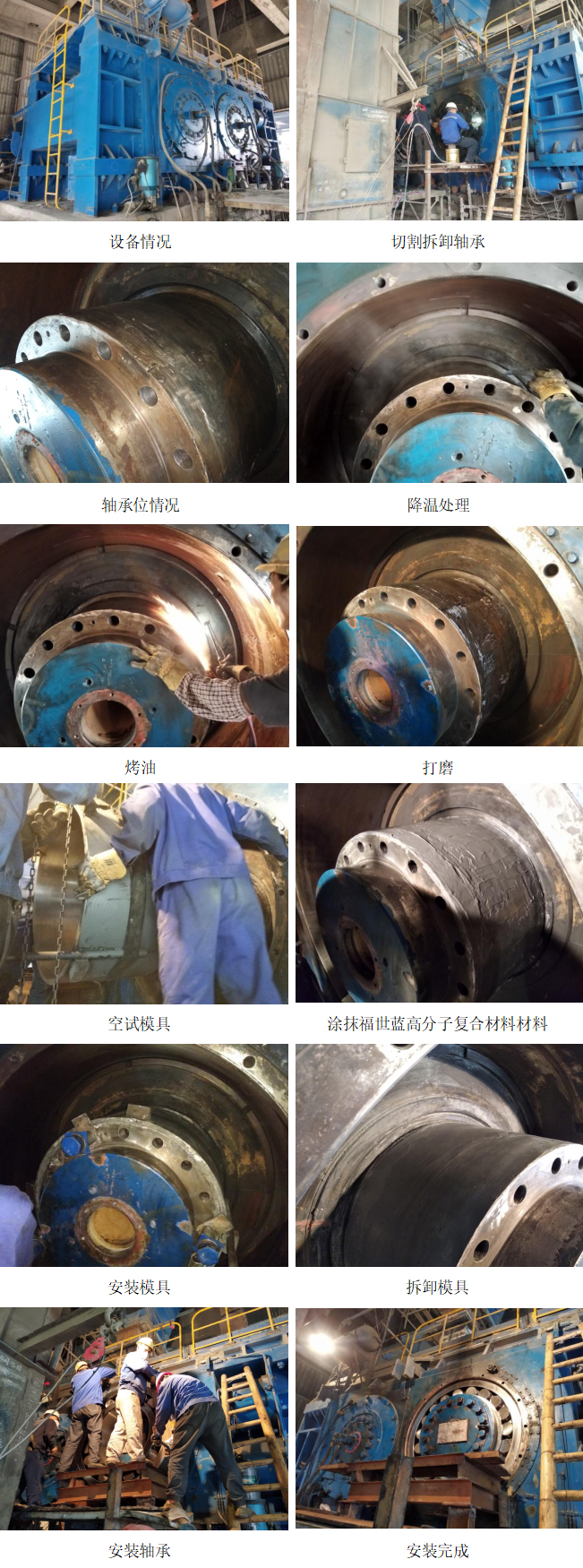
发布评论请先 登录
相关推荐
评论