内容提要
燃料电池用空压机开关频率高,空间有限,集成度高,采用单管设计的主要挑战是如何提高散热效率。本设计中功率器件和散热器采用DBC+焊接工艺,提高了SiC MOSFET的输出电流能力,从而有效降低了系统成本的,并且简化安装方式。
氢能源称为人类社会的“终极能源”,以氢燃料电池驱动的汽车,行驶过程中没有污染,只生成水。燃料电池系统由电堆和BOP(Balance of Plant)构成。燃料电池BOP为电堆稳定运行提供了必要的外部环境,包括空气系统、冷却系统、增湿系统、功率输出控制等部分组成。
由于大功率燃料电池工作时需要消耗大量的氧气,这就需要高速空压机输送大量的空气。空压机的作用对空气进行增压,为燃料电池电堆提供合适流量、温度、压力、湿度的洁净空气,满足电堆的功率输出需求。空压机是空气循环系统的核心,其性能对燃料电池系统的效率、紧凑性等有着重要影响。
常用的空压机主要有离心式、螺杆式、涡旋式等,根据不同的燃料电池选择不同类型的空压机。其中离心式空压机由于转速高、尺寸小、质量轻等特点,目前被广泛采用;由于电机最高转速超过15万rpm,空压机电机控制器的输出频率超过2500Hz,功率器件需要很高的开关频率(超过50kHz),因此SiC-MOSFET是这类应用的首选器件。
本项目空压机系统基本参数如下:
电机种类:永磁电机(一对极)
输出功率:25kW
输出电流:70A
最高转速:150,000rpm
输入电压:DC450~750V
控制器最高效率:>98%
01
焊接技术降低系统热阻
本项目是动力源新能源主导,晶川联合参与开发。功率器件采用英飞凌的CoolSiC MOSFET IMW120R030M1H。拓扑如图1所示,两个CoolSiC MOSFET并联以实现25kW的输出功率。
图1.拓扑结构图
IMW120R030M1H器件采用TO-247封装,管壳背面是裸露的金属,有利于散热但不绝缘,因此首先面临的问题是在满足绝缘要求的情况下尽可能的降低热阻,从而满足高功率密度要求。原始的散热方式为陶瓷+两面导热硅脂+压接,接口热阻0.1K/W,热硅脂的热阻占比超过90%。为了进一步降低接口热阻,有必要采用高导热材料替代导热硅脂,优化这部分热阻分布,本项目采用敷铜陶瓷(DBC)+焊接技术,接口热阻降低到0.011K/W,接口热阻降低89%。敷铜陶瓷(DBC)+焊接技术的方式不需要压接环节,因此可以简化组装工艺。
图2.陶瓷+硅脂 和 DBC+焊接示意图
图3.两种导热绝缘方式热阻对比
图4.采用焊接方式的TO-247
图5.空压机控制器实物
02
基于滑膜观测器的估算模型
实现精确位置控制
由于电机的转速高、空间小,不便于安装角度传感器,因此控制器采用基于滑膜观测器的估算模型对电机转子位置进行估计。在启动阶段,电机转速较低,反电动势较小,滑膜观测器无法准确估算转子位置。控制器采用“转速环+IF控制”方式来完成电机启动。在IF控制方式下电流处于闭环受控状态,电流矢量的角度为虚拟角度,来自于给定转速的积分,电流的期望幅值来自于转速环路的输出;电机运行至一定转速后,将虚拟角度切换至估算的实际转子角度。启动过程如图所示。
图6.启动阶段电流波形
由于空压机电机工作转速比较高,是燃料电池系统最主要的噪音源;因此如何降低空压机系统的噪音是一个挑战。本项目通过优化开关频率、死区时间等措施优化电流波形(高速电流波形如图7),进而改善高速带载的噪音。
图7.高速带载波形
03
DBC+焊接工艺提升系统输出能力
为了评估热性能,在SiC MOSFET管壳上方粘贴热电偶,分别针对陶瓷+硅脂、DBC+焊接两种方案分析了进行了对比测试,测试对比结果详见图8。测试结果表明:在相同的散热条件下,随着输出电流上升,两种方案之间的温差逐步增大。当输出电流为90A时,DBC+焊接方案壳温比陶瓷+硅脂的方案壳温低24.8℃。由此可见,采用焊接的方式可以有效降低系统热阻,提高系统输出能力。
图8.陶瓷+硅脂和DBC+焊接测试对比
04
总结
综上,可以看到,对于空压机这样高压高频的应用,CoolSiC MOSFET能够实现极低的导通阻抗与方便灵活的驱动方式,DBC+焊接方式能够实现极低的热阻,基于滑膜观测器的估算模型能够实现精确的位置控制,实现了高性能的控制功能,满足氢燃料电池空压机的特殊要求。
-
电池
+关注
关注
84文章
10544浏览量
129442
发布评论请先 登录
相关推荐
燃料电池测试负载如何进行负载测试?
燃料电池与氢气的关系 燃料电池与电动汽车的比较
燃料电池的主要材料 燃料电池的效率和性能
燃料电池的应用领域 燃料电池车的优缺点
燃料电池工作原理 燃料电池与传统电池的区别
燃料电池测试负载的工作原理是什么?
什么是燃料电池?燃料电池和动力电池区别
燃料电池系统的优势及应用分析
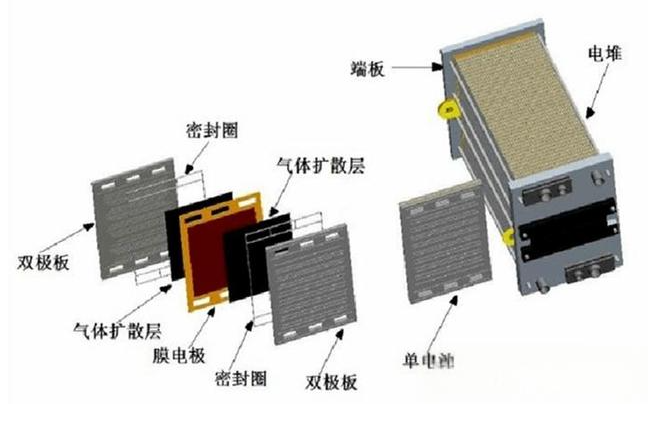
燃料电池的分类及其特点
ZBK380矿用一般型空压机综合保护装置
应用分享|高性能电子负载助力燃料电池抗反极性能评价
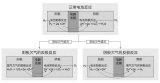
评论