在过去四十年间,刀片(blade)与划片(dicing)系统不断改进以应对工艺的挑战,满足不同类型材料切割的要求。行业不断研究刀片、切割工艺参数等对切割品质的影响,使切割能够满足日新月异的晶圆材质变化。
划片机制(The Dicing Mechanism)
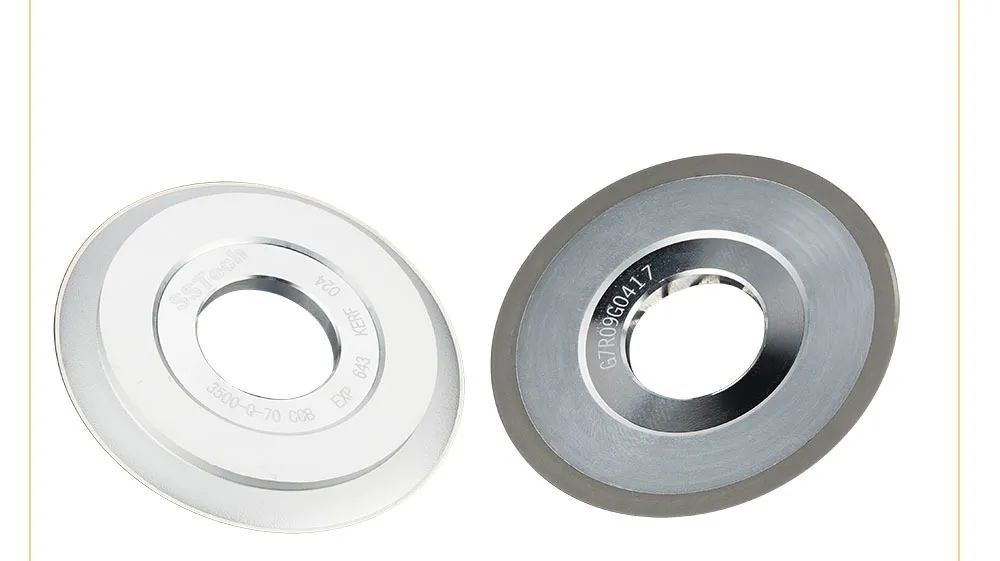
硅晶圆划片工艺是“后端”封装制程工艺中的第一步。该工艺将晶圆分成独立带有电气性能的芯片,用于随后的芯片粘合(die bonding)、引线焊接(wire bonding)和测试。划片机空气静压主轴以每分钟30000~60000rpm的速度(83~175m/sec的线性速度)转动刀片。该刀片由嵌入电镀镍矩阵结合剂中的研磨金刚石制成。
在晶圆切割过程中,刀片碾碎基础材料,同时去掉所产生的碎屑,冷却水(通常是去离子水)用于冷却刀片并改善切割品质,通过帮助去掉碎屑而延长刀片寿命。
关键工艺参数
晶圆切割追求生产效率和合格率最大化,同时投入的成本最小。但是,面临的挑战是,生产效率增加往往导致合格率降低,反之亦然。随着进给速度增加,切割品质会下降,同时也影响刀片寿命。
晶圆切割经常遇到较窄的切割槽,要求设备能将每一次切割都精准放在切割槽中心几微米范围内。这不仅需要非常高的设备精度,更需要一款高精度超薄划片刀。
可是,越薄的刀片(比如:10µm)越脆弱,更容易过早破裂和磨损,导致其寿命和工艺稳定性较之稍厚的刀片差。对于50~76µm切割槽的刀片一般推荐刀片厚度应该是20~30µm。
崩边(Chipping)
正崩(TSC, top-side chipping),发生在晶圆的表面,当划片刀接近晶圆的有源区域时,主要依靠主轴转速、金刚石粒度、金刚石浓度、冷却水流量和进给速度等因素控制。
背崩(BSC, back-side chipping),发生在晶圆的背面,当不规则微小裂纹从晶圆的背面扩散开并汇合到一起时,这些微小裂纹足够长而引起较大颗粒从切口掉出,背崩就会影响到产品合格率。通常,切割硅晶圆的质量判定标准是:如果背面崩缺尺寸在10µm以下,忽略不计;当尺寸大于25µm时,可以看作是潜在的受损;一般,50µm以内的平均大小在可接受范围内,具体要求可示晶圆的厚度来定。
可以用来控制崩边的的方法和技术,主要是优化刀片,以及优化工艺参数。
刀片优化(Blade Optimization)
除了尺寸,有三个关键元素决定刀片特性:金刚石(磨料)尺寸、金刚石含量和粘结剂的类型。这些元素的结合效果决定刀片的寿命和切割品质(TSC与BSC)。改变任何一个参数都将直接影响刀片性能。
为一个既定的划片工艺选择最佳刀片,要求在刀片寿命与切割品质之间作出平衡。高寿命,品质降低;高品质,寿命降低。划片刀所用金刚石越细,对工艺参数的变化越敏感。
其它因素,诸如进给速度和主轴转速,也可能影响刀片选择。切割参数对材料去除率有直接影响,它反过来会影响刀片的性能和工艺效率。刀片厂家(例如:深圳西斯特)会对这些规律做深入研究,以应对市场诸多材料精密划切过程中面临的多样需求。
为了选择一款合适的刀片,重要的还是要理解刀片外表硬度的影响,刀片外表硬度通常叫做基体硬度。基体硬度通过金刚石尺寸、浓度和粘合物硬度来决定。通常,较细的磨料尺寸、较高的金刚石浓度和较硬的粘合物将得到相对增加的基体硬度。通常建议,与其它因素综合考虑,较硬的材料需要较软的(基体)刀片来切,反之亦然。例如,砷化镓(GaAs)晶圆一般要求较细的金刚砂尺寸(较硬的刀片),而钽酸锂(LiTaO3)晶圆最适合用较粗的金刚砂尺寸和较低的金刚石浓度(较软的刀片)。
结语
总而言之,划片工艺变得越来越精良且要求高。切割迹道变得越来越窄,且迹道内可能充满测试用的衰耗器(test pad),并且刀片可能还需要切割由不同材料制成的各种涂敷层。在这些条件下达到最大的划片工艺合格率和生产率,要求有精准选刀能力与先进工艺控制能力。
-
晶圆
+关注
关注
52文章
4920浏览量
128039
发布评论请先 登录
相关推荐
晶圆制造中的T/R的概念、意义及优化
晶振常见的切割工艺有哪些
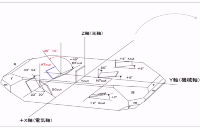
晶圆级封装的五项基本工艺
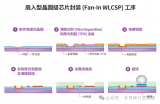
评论