11月29日,在由36氪举办的WISE2022未来能源创投新风向大会中,阿丘科技联合创始人郑慧伟发表了题为《AI视觉检测助力企业数字化质量和品质闭环的构建》的主题演讲。
郑慧伟认为,AI质检需要帮助企业最终实现质量和品质的数字化闭环,构建整个质量管控闭环系统,使得质检结果能够追溯工艺过程,实现工艺、生产过程的反馈优化。AI供应商主要提供工具和平台,客户借助AI平台沉淀符合自身需求的工艺数据模型,最终打造出以AI驱动的数字化质量管理平台。
以下为本次演讲实录:
大家好,今天我分享的题目是AI视觉检测助力企业数字化质量和品质闭环的构建。也就是说从质量管控到良率提升到整个质量闭环的构建,最终希望能够走向整体的灯塔工厂。
整个智能制造的核心关注点无非就是四点:提质、增效、降本、扩柔。
其中提质顾名思义非常简单,提升产品质量,提升可控度。增效就是增加产量和提升良率。降本就是降低固定成本和系统成本。扩柔不管是增加切拉换洗的自动化程度还是增加整个切拉换洗的速度,总之来说提升规模效应,扩大柔性事业能力是整个智能制造的核心关注点。
对于我们锂电行业来说的话,特别特殊的是安全性是行业的一个生命线。下游市场对于安全性的关注度是非常高的,对于我们整个电池制造来说整个电池制造一致性、良品率、安全性等都是有非常高的要求。
01
工厂质量管控的现状、痛点以及实现难点
当前来说主要以人工目检为主,这就会存在主观判断和目视疲劳,检测结果难以量化,过漏检指标难以管控等问题。如果用一些传统的AOI检测设备的话,大家可能也都用过,通常会有厂家一致性比较差、整体检出率比较低,品质管控非常烦琐困难等问题,很难满足最终的过漏检指标。还有整体数据孤岛的问题,比如检测图片散落在各个独立的设备上难以进行排查,难以回溯,数据容易丢失,而且也不好做相应的改善和优化。最后一个是属于质量管控和段划,质量管控和上游的生产工艺无法形成一个回溯关联,没有办法从源头改善品质。
那工厂质量管控存在哪些难点呢?
1. 产量大,工艺控制点非常多,所以说检测次数很多也比较繁杂。
2. 极限制造对于精度和品控要求越来越高,特别是现在随着产线速度越来越快,对整个检测的效率要求越来越高。
3. 缺陷种类非常复杂细小,而且区分度比较低。在整个检测过程中,因为不同的缺陷是由不同的工艺造成的,对缺陷的区分其实是要做到精细化的处理,不然的话整体很难做到工艺追溯包括很难做到过漏检的优化。
4. 当前阶段需要耗费大量的人力财力,不管是质检员还是相应的管理成本都比较高。
我们从内部看一下质量管控的现实难点,客观来说对于任何一家企业来说,品质部跟生产部多多少少还是互相有不同的关注点的。品质部关心的是质量怎样能够满足相应的要求,而生产部关心的是生产的量,所以说这就是一个天然的矛盾,意味着品质管控和产能之间的矛盾是不以人的意志为转移的,是天然存在的。而且,矛盾会随着时间变化,也会随着客户的要求变化而变化,最终临界点意味着不同客户或不同的时间点对整个可接受良率的极限是在这个临界范围之内波动的。
02
构建企业数字化质量&品质闭环的价值
构建整个企业数字化质量和品质闭环的价值:
保障品质检查的一致性。
保障品质数据的可视化和可预警。
保障品质数据的统一化管理,实现缺陷精准分类和工艺改善。
建立真正的无忧的质量保障系统,构建人、机、AI复合质量检查体系。基本上要把AI检、机器检、人工检有机的结合起来,充分发挥各自特长,发挥各自的优点,规避各自的缺陷,实现无忧的质量保障体系,打通设备和人的屏障。
视觉检测的价值本质来说就是两点:
第一点,产品出厂的质量控制,毫无疑问产品卖出去或者给到下游的时候,这一块做相应的检查。
第二点也是更重要的点,生产过程的工艺控制。在各个工艺的点上把相应的缺陷给剔除出来或者发现了,同时在这个点上能建立缺陷和工艺之间的映射关系,为整个质量闭环提供数据基础,从而提升相应的良率。
03
阿丘科技工业级AI的实践和路径
下面由我来介绍下,阿丘科技在工业级AI质检是怎么做的,我们都做了哪些相应的实践。
总的来说,主要围绕以下四点:
自己的修行之路。
工业AI的软件平台和工具链构建的比较完善。
深入工艺打造行业的工艺包。
以质量数据为核心构建整个质量闭环。
第一点,自己的修行之路,我们从一开始就有完全自己能够深度学习的算法和引擎,面向工业的而不是面向泛行业的,工业有工业非常强的工业特点。第二块有标准的软件平台和解决方案,整体团队是来自清华人工智能实验室的,整体的研发团队也比较强大,最后我们有非常丰富的落地案例和方法论。
第二点,构建的平台+工具的端-边-云架构,为过程检和终检服务完整的架构。要想实现工业AI质检,其实对算法特别是对小缺陷的检测能力、对小样本的学习能力、对非监督的要求以及对于快速训练的要求非常高,我们关于这方面都做了对应的优化。
构建了整个AI检测质量质检落地的闭环三要素:算法、软件工具链、落地方法论。所以说从大的维度来说,也就意味着工业AI检测本质上从通用AI走向了工业AI,工业AI有非常强的特点。第二块,AI不仅是算法更是系统工程,所以说不能只考虑算法,要考虑怎么落地,怎么把落地方法论构建起来,怎么把软件工具链构建起来。第二点AI本质上是算法和数据,我在后面会讲数据的价值。
第三点,就是深入工艺,打造行业工艺包。以锂电行业为例,从前到后整个的工艺点非常多,每个点都需要管控,所以说我们可以针对每个工艺点结合这个工艺点的特征构建对应的工艺包,顶盖的工艺包、密封钉的工艺包、六面电芯外观检的工艺包等等。每个工艺包的工艺特点是不一样的。
从检测系统的发展来看,其实共经历了三个阶段:
第一代的检测系统就是图像获取到基于规则的图像处理到基于规则的图像分析,最终结果出来,我们把它定义成传统的数据系统,这一块以消费电子行业为主。但是随着整个缺陷检测难度的提升和整个复杂度的提升以及对于相应的工艺闭环要求的提升,这一代系统整体检出率和使用率体验也是非常不好的。第二代的检测系统,是以传统数据为主,以AI为辅的检测模式,这一块只是一种中间过渡的状态。
其实我们已经迈入了第三代的检测系统时代,也就是说以AI为主检,以传统算法为辅的时代。本质上是回归了品质管控的本质,品质管控本质上都是围绕工艺来的,要么过工艺管控,要么做工艺提升,最终实现整体的品质良率提高。
我们基于尺寸规则逻辑进行缺陷检测,原来是多少乘多少尺寸的缺陷,但是因为缺陷发生的形态老是在变化,就会经常出现各种各样的边边角角的问题。现在走向以形态检测为主,也就意味着把划痕检出来,把脏污检出来,并不在意脏污到底是圆形的、方形的、菱形的还是不规则形的。我们只关心脏污,这就会回到整个事物最初始、最本质的状态。
第三点以AI检测有一个非常大的好处,它的工艺是以模型、以数据形式沉淀下来的,可追溯的,可优化的,而不像传统的都是一种过程的量,是没办法做追溯优化和沉淀的。
第四点构建整个质量管控闭环系统。毫无疑问在当前阶段从生产到品质的过程其实大部分还属于开放状态,生产归生产、品质归品质。品质主要是对整个质量进行管控,但是最终很难往前追溯或者真正定量化改善。
大家如果学过控制论相应理论,就知道闭环系统是最稳定的系统,特别是负反馈闭环系统。不管是整体的可控度、稳定性、决却度还是抗干扰能力都非常好,所以就倒逼我们在整个质量管控方面也要构建闭环系统。
闭环系统在我们视角看来分为三个层次,从AI闭环最终走向质量闭环有三个阶段:
第一阶段,工业AI落地。用AI结合相应的算法落地方法论和工具链能把第三代AI检测系统做得比较完善和比较好。
第二阶段,数据驱动的AI系统优化,也就意味着以数据为核心而不是以AI为核心来看待这个问题,本质上是AI、数据、质量标准三位一体循环优化,最终走向质量数字化闭环。最终阶段是以客户的关注点来看待的一项工艺。AI已经变成AI工具或者平台,还有客户关心的解决方案等。
第三阶段,我们统称为以AI驱动的数字化质量平台。所以闭环系统是循序渐进而且是层层深入的。我们如果从终局角度或者长线角度看来,这么做的方式解答了客户和AI供应商之间的各自定位问题,意味着AI的供应商和终端客户双方有不同的生态位和价值沉淀。
AI供应商如何把AI相应工具做好,以数据为核心、工艺沉淀为核心、以工艺优化为核心,最终将工艺数据模型沉淀在客户这里,这也是客户最想要的东西。
那么,如何构建整个质量管控的闭环系统?
01
把质量标准数字化、检测模式数字化
原来用表格或者纸质方式记录的缺陷标准要回归到本质以数字化方式建档起来,可以优化和改善。原来是人工目视,现在通过机器视觉的方式把它转化成数字化信号存储起来,相当于原图也可以存储起来,最终实现可反馈、可存储、可复制。
02
实现缺陷检测的AI化
将工艺沉淀到模型池。刚才说了通过AI高泛化的适应能力结合AI的抽象能力,把原来检测不出来的缺陷检测出来,把能检的全部检出来。对造成这些缺陷的原因进行相应的分析,把它沉淀到相应的模型池。
03
AI强缺陷分类,实现工艺溯源,闭环优化实现真正的零缺陷管控
AI有非常强的缺陷分类能力,在把缺陷分完类之后或者精细化分类完之后,再相应地往前追溯工艺就成为一种可能。举个例子,划伤有对应的原因造成,气泡产生的原因也不一样。在缺陷形态来看,异物和气泡可能长得很像,但是从最终工艺的角度来看,这两个是由不同的原因造成。所以最终我们要实现工艺的数字化、制造的数字化、误差的数字化和品质的数字化,以此来实现构建完整的质量管控闭环。
04
以数据为中心、以AI为动力,构建完整的闭环
有了相应的数据中心之后,对应上层相应的质量算法,缺陷分类和质量溯源体系,预警和预测体系,工艺改善体系还有质量重要度分析,以及相应的良率分析体系。整体质量控制就有了相应的数据和土壤,就能把相关工作做得比较细致和有价值。工业AI质检的典型应用场景包括外观检测、缺陷分类、装配确认、有无检测、分选定级等。
04
典型行业案例
下面展示2个案例,看一下我们是如何开展相关工作。
第一个是过程检测,这部分属于在整个锂电过程中焊接耗的质量AI检测包括密封电焊结合顶盖焊接。这一块是用AI和3D的方式混合检测的最终做到零过筛或过筛在0.5%左右,已经批量使用了。这部分核心在于把一些像针孔比较难检的缺陷通过AI和3D方式检出来
第二个案例是电芯外观用面的全检,这块本质上属于终检,终检毫无疑问缺陷率检查非常之多,基本有三四十种。而且因为最终检,所有工艺都汇聚到这个点来,所以缺陷类型也非常之多。而且还需要对缺陷进行相应的分类。整体要求非常高,因为牵扯到出货,如果检测要求不严格的话,最终到下游客户还是会有投诉的情况。
在这个过程中都有几个难点和亮点:
1. 对缺陷进行精细化分类,如果做不到精细化分类,终检基本不可行。因为哪怕都检测出来了,但是没办法进行分类,缺陷的优先级和检测度不一样,最终会导致整体过检率非常高。换句话说你设备整体良率非常之低,你的设备根本开不起来,或者产能根本上不去,所以需要对缺陷进行精细化分类。
2. 对小缺陷进行精细化抠取,这个也非常重要,否则就会产生漏检风险。如果设备有比较大的漏检风险,设备可用度依然比较低。
3. 多工位和多视觉的交互验证,这块也是比较大的难点。最终我们这块做到了关键缺陷零过筛,一般缺陷会有小比例的可控的漏差,同时过筛率控制在3%左右,目前已经在头部客户做到相关的批量复制。
-
AI
+关注
关注
87文章
30661浏览量
268827
发布评论请先 登录
相关推荐
北美运营商AT&T认证中的VoLTE测试项
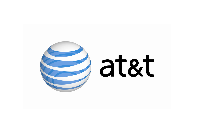
北美运营商AT&amp;amp;T认证的测试内容有哪些?
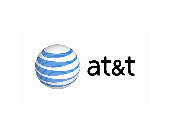
北美运营商AT&amp;amp;T认证的费用受哪些因素影响
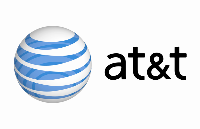
onsemi LV/MV MOSFET 产品介绍 &amp;amp; 行业应用
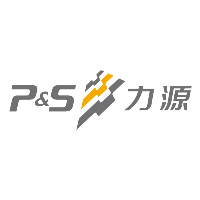
软通动力携手华为启动&quot;智链险界&quot;计划,强化生态链接共启保险AI新时代
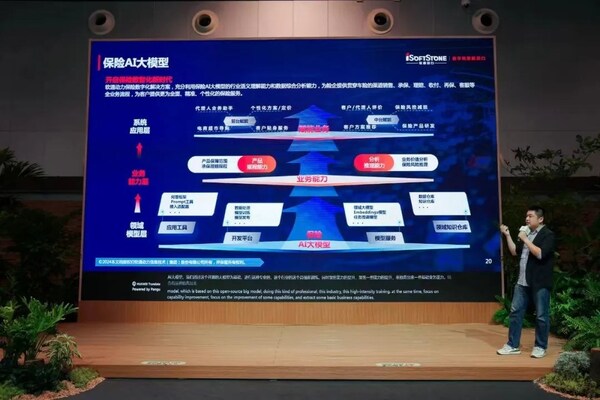
从边缘到云端,合宙DTU&amp;amp;RTU打造无缝物联网解决方案
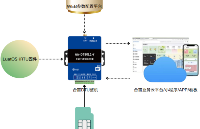
FS201资料(pcb &amp; DEMO &amp; 原理图)
北美运营商AT&amp;amp;T认证入库产品范围名单相关
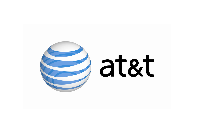
解读北美运营商,AT&amp;amp;T的认证分类与认证内容分享
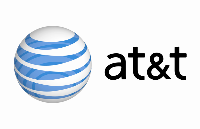
科沃斯扫地机器人通过TÜV莱茵&quot;防缠绕&quot;和&quot;高效边角清洁&quot;认证
Open RAN的未来及其对AT&amp;T的意义
中创新航荣获逸动科技2023年度&quot;优秀战略合作伙伴奖&quot;
第二代配网行波故障预警与定位装置YT/XJ-001:守护电力线路的超能&amp;quot;哨兵&amp;quot;
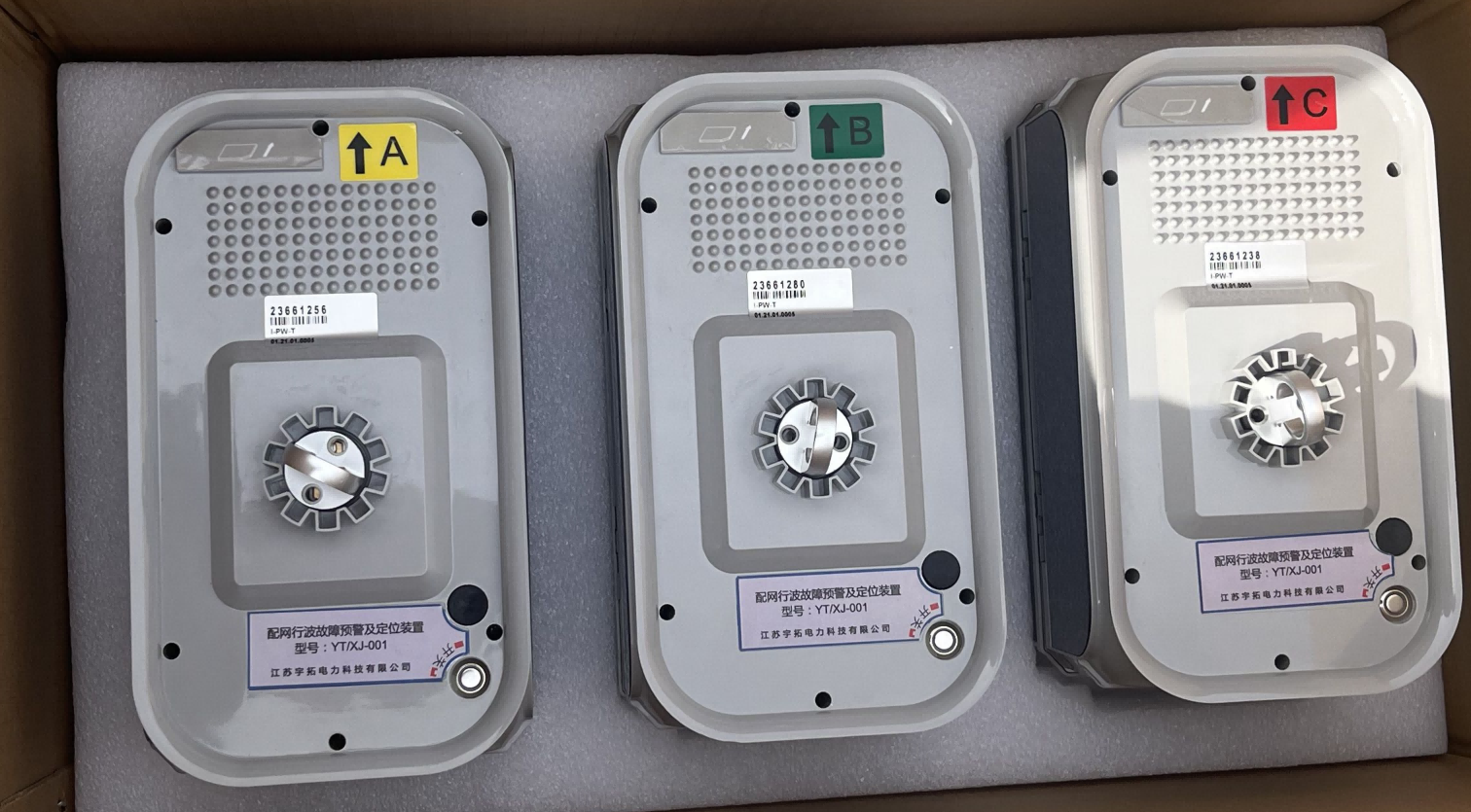
评论