汽车的热管理系统是调节汽车座舱环境、汽车零部件工作环境的重要系统,其通过制冷、制热和热量内部传导综合提升能源利用效率。简单的说,就好像是人们发烧了需要使用退烧贴;而当寒冷难耐时,需要使用暖宝宝类似的道理。而纯电动汽车复杂的结构无法通过人为操作来进行干预,因此其自身的“免疫系统”将起到至关重要的作用。纯电动汽车的热管理系统相比普通燃油车型则更加复杂,这是由于纯电动汽车拥有电池、控制器以及电动机等更多需要进行热控制的部件。纯电动汽车的热管理系统不仅包括了空调系统,而是根据热管理需求分别增加了电池包环境、功率电子器件以及电机散热等不同的部分。
01
为什么需要热管理
电动汽车的自燃事故相信已经是深入人心了,而自燃事故之所以会发生,原因不仅在于漏电或者短路这种电路上的问题,车上控制器的热管理策略和热管理回路设计都直接影响电动汽车的安全性。当然,电动汽车自燃毕竟是少数事件,只不过透过这种事件可以让每家车企和供应商的汽车事业部更加重视热管理这个技术部门,毕竟大多数公司的动力总成部门还是以电池电机电驱为主力,热管理为辅。自燃的部分原因是过度发热没有得到及时的冷却,那同时也还有一些其它场景的需求,是环境太冷而得不到及时的加热,比如电池低温预热和座舱加热,下文将分为加热和冷却两个需求来分别聊聊电动汽车的热管理需求。
1.1 加热需求:
加热需求之一:座舱加热冬天,驾驶员和乘客在车内需要温暖,这就牵扯到了热管理系统的加热需求。根据用户在不同地理位置,对加热需求也不尽相同。比如在深圳的车主可能一年都不需要开座舱加热,而北方的车主冬天为了维持座舱内的温度则消耗了大量的电池电量。这些不同的需求也就导致了热管理系统设计初期不同的定义,其背后的原因就在于不同市场的不同需求将带来不同的热管理选型,一个简单的例子就是:同一个车企供应北欧的电动车可能用的是额定功率5kW的电加热器,而供应赤道地区国家的可能就只有2~3kW甚至没有加热器。除了纬度以外海拔也有一定影响,但目前还没有专门针对海拔做区分的设计,因为保不准车主会开着车从盆地开到高原。另一个最大的影响因素就是车里的人了,因为不管是电动车还是燃油车,里面的人的需求还是一样的,所以设计的温度需求范围几乎是照搬的,一般在16摄氏度到30摄氏度之间,也就是说座舱里制冷不冷过16摄氏度,制热不热过30摄氏度,覆盖了正常的人体对环境温度的需求。
加热需求之二:高压电池现在大家听说最多的是锂离子电池,在自己的手机和笔记本电脑上都已经用了很久了,从来都是看着它们“为发烧而生”的,没听说它们竟然还需要加热的。这个主要是因为手机不会单独放在室外零下的环境里冻着,至少都有人的手或者口袋给捂着,可能也有用户体验过的是低温在户外开不了机或者刷一会儿手机耗电量极大。这就是锂离子电池娇贵的地方。硫酸铁锂电池低温充电受限制,比如宏光Mini电动车就为它的磷酸铁锂电池配上了低温充电加热功能。三元锂电池虽然低温比磷酸铁锂强一丢丢,但是温度低到-7℃以下也限制了充电功率。所以锂离子电池的加热一般都是为了保障在冬季低温环境中仍然能够对它充电。锂离子电池喜欢在15到35度之间充放电,低了或者高了都会限制充放电的电流,而且还影响它的SOH(State of Health)健康状况。环境平均温度以上海为例一年十二个月里可以从0度到35度,电池只能期盼着热管理系统能像对待车里的乘客一样照顾好它,不然就撂蹶子。然而电池在纯电动车上是个庞然大物,体积大重量大,要想从低温环境中加热到适宜的温度完成暖机,既要考虑电池能够承受的升温速度,又要考虑热管理系统能够稳定输出的加热功率,还要照顾用户等待暖机的耐心,这些都对热管理系统提出很高的要求。
加热这一块,电池和座舱的需求会对应到热管理系统的设计上,比如电池内的换热回路设计,电池和外部加热回路的换热设计,座舱换热器和加热回路的设计,电池预热策略和座舱相应用户温度调节的控制策略等等。
1.2 冷却需求
冷却需求之一:高压电池冷却电池自身由于内阻和放电均衡回路的存在,在充放电过程中流过的电流都将导致电池发热,文初提到的自燃事件就有这一部分的影子。连续开车的时间越长,加减速的次数越多,加减速强度越大,都是促进电池的升温。充电过程中的电流也在提高发热,尤其是直流充电的时候,以北汽新能源和比亚迪为例,直流充电时稳定功率能达到60kW,要知道的是许多大功率电机的额定功率也不过60kW,充电和放电都是发热,充电半小时几乎相当于连续半小时以额定功率在驾驶。这对电池的挑战可想而知,许多耳熟能详的自燃事件大多都是在车库充电时候造成的。而且按照下一步计划,充电功率还将继续提高,保时捷Taycan已经在挑战350kW快充,这样的技术如果没有热管理的保驾护航,光是电力电子方面技术提高是做不到的。电池的升温也根据不同的车和不同的电池有所不同,比如说有的微型车或小型车本身充放电功率不大,电池的持续升温也不会过大,此时使用一些风冷的方式或者较小的水冷散热回路即可;而一些SUV和豪车的电动款则需要以较强的电池冷却能力来满足大功率充电和大功率驱动的需求。考虑到电池工作中的发热,与上文的加热需求相比,冷却需求更能考验汽车电池热管理系统的技术人员,因为电池在预热以后自身的发热也可以提供部分热量,而且电池加热需求因南北方可能有区别而加热需求南北方比较接近,因为即使环境再冷,而电池中有局部积蓄的热量没有被及时散去的话也会影响电池的安全性。www.phoenixcontact.com冷却需求之二:高压功率电子冷却三电除了电池还有的就是电机和电控了,其实车上还有的车载充电机OBC(OnBoard Charger)、高压转低压DC/DC和高压配电箱也有散热需求。在许多车型里,因为这些功率器件中的功率电子组成都比较相同,只是互相的功率大小不同且内部设计不同,比如电控、车载充电机和DC/DC都会用到IGBT绝缘栅双极型晶体管,它的发热功率与开关速度相关,而它的开关速度也直接影响到这些功率电子的输出功率。车载充电机用于交流220V转车内电压给车充电,目前国内除了比亚迪其它几家都以6.6kW单相AC充电为主,而充电机效率一般在93%~95%之间,以95%计算的话大部分的车在交流充电过程中车载充电机也会有330W的发热量。DC/DC根据低压执行器组成的不同,一般在2~3kW之间,效率也在95%,那么从开机供应低压零部件起,DC/DC的稳定发热也接近150W。这些热量如果累积在OBC和DC/DC中的话势必导致零部件温升,而这些零部件供应商为保护元件都会在温度超过一定阈值时限制功率输出同时给整车控制器发出过热警告。电机和电控更是如此,大家熟知电机的效率图,基于不同的输出扭矩和转速,电机和电控将承受相应的热量损失,而且总的热量能达到千瓦级别,这些热量都期待由热管理系统带出元件本体。
Badin, Francois et al. (2015). Energy efficiency evaluation of a Plug-in Hybrid Vehicle under European procedure, Worldwide harmonized procedure and actual use.
冷却需求之三:座舱冷却这个和上文提到的座舱加热本质差不多。以国内为例,从南到北夏天都有开空调的时候,南方对空调依赖略高一些。因此车内空调的设计并无地域差异,太多的差异如果只能造成单辆车元件清单BOM成本低但不能在产量上使得总的生产成本低,那就没有差异化的意义了。有一个比较新的冷却需求是来自于上文提到的350kW直流充电,由于直流充电站直接与电池相连,不仅电池承受着大功率,中间的充电线缆同样流过大电流,那产生的热量也是不容小觑。最新的技术有的是从直流充电站端对充电线缆进行水冷,冷却回路在直流充电桩内循环;也有的提出利用车内冷却循环与线缆外圈相通实现水冷。无论哪种方法本质都是在助力大功率充电的实现,但目前看来复杂程度和背后的成本都比较大。可见未来要真正推行大功率充电仍有许多未能量产的技术需要落地。
www.ittcannon.com (HPC: High Power Charging)加热和冷却的需求催生了热管理系统的整个产业,而这些需求又来源于对电动汽车安全性、舒适性、零部件寿命、充电功率等多个方面。在满足需求的同时热管理系统又消耗了大量的电池电量。许多时候客户对热管理系统的期待都是间接的,既想要座舱内的舒适温度,又想要保护车内动力部件的安全,最重要的是还非常在意续航里程。这其实就奠定了当下热管理系统研发的主旋律:以尽可能小的能量间接地满足客户对整车系统各方面的直接需求。
02纯电动汽车热管理系统纯电动汽车的热管理系统通过最大限度地利用电池能量辅助进行驾驶,通过小心地将车辆中的热能重新用于车辆内部的空调、电池,热管理可以节省电池能量以延长车辆的行驶里程,其优势在极端的冷热温度下尤其显着。而纯电动汽车的热管理系统根据不同车型主要包括了高压电池管理系统(BMS)、电池冷却板、电池冷却器、高电压PTC电加热器以及热泵系统等主要部件。
而纯电动汽车的热管理系统解决方案涵盖了整个系统范围,从控制策略到智能组件,通过在运行过程中灵活分配动力总成组件产生的热量来管理两个极端温度。通过允许所有组件在最佳温度下运行,纯电动汽车热管理系统决方案缩短了充电时间并延长了电池寿命。
高压电池管理系统(BMS)相比于传统燃油汽车的电池管理系统更加复杂,该系统作为核心组件集成到了纯电动汽车的电池组当中。根据收集到的系统数据,该系统可将热能从电池冷却回路传递到车辆的制冷回路,以保持最佳的电池温度。该系统具有模块化的结构,其主要包括了电池管理控制器(BMC)、电池监控电路(CSC) 以及高压传感器等设备。
电池冷却板则可用于纯电动汽车电池组的直接冷却,其可分为直接冷却(制冷剂冷却)和间接冷却(水冷冷却)。其可以根据电池进行设计匹配,以达到电池工作高效和寿命延长。而双回路电池冷却器内腔为双介质制冷剂和冷却液,其适用于纯电动汽车电池组的冷却,可使电池温度维持在高效率区域并保证电池使用寿命的最优化。
纯电动汽车并没有热源,因此需要使用标准输出功率为4-5kW的高电压PTC电加热器为车内提供快速且足够的热量。而纯电动汽车的余热又不足以完全进行车厢加热,因此需要热泵系统进行加热。
03
新能源汽车热管理
热管理听起来是协调汽车系统内的冷和热的需求,似乎不会有什么差异性,但实际上针对不同的新能源汽车类型,热管理系统也有很大的区别,下面会对几类新能源车分别介绍其热管理系统的特别之处,先给大家贴个对比的表格,后面将详细讲解表里的技术异同点。3.1 微混动大家可能比较好奇为什么混动还要强调个微混动,这里分为微混动的原因是:混动车中使用高压电机和高压电池的车型在热管理系统上比较接近插电混动,所以这类车型的热管理架构将在下文的插电混动中介绍。此处的微混动主要指的是以48V电机和48V/12V电池为主,比如48V BSG (Belt Starter Generator)这种。它的热管理架构的特点可以概括为下面三点。电机电池风冷为主,也有水冷和油冷电机和电池如果以风冷形式散热的话,那几乎也就没有功率电子的散热问题了,除非电池使用12V电池,然后使用12V转48V的双向DC/DC,那这个DC/DC根据电机启动功率和刹车制动回收功率的设计,可能会需要水冷管路。电池的风冷可以在电池包内设计空气回路,通过控制的风扇的方式实现强制风冷,此时会增加一个设计任务,那就是对风道的设计以及风扇的选型,如果要用仿真来分析电池强制风冷的散热效果话会比液冷电池更难,因为气体流动换热比液体流动换热的仿真误差更大。水冷和油冷的话热管理回路就和纯电动车型比较相似了,只不过发热量比较小。而且由于微混电机工作频率不高,所以一般不会出现连续大扭矩输出造成快速发热的情况。有一个例外,近几年也有搞48V高功率电机,介于轻混和插电混动之间,成本比插电混动低,但驱动能力比微混和轻混强,也就导致了48V电机的工作时间和输出功率变大,使得热管理系统需要及时配合它的散热。冬季座舱加热可由发动机提供发动机的存在对于冬季是一个好事,它的热量可以直接传递到座舱内满足加热需求。车上的电加热器也只是48V的小功率类型(相对于纯电动车)。甚至于在大多数时候,发动机的热量还需要传递到对外的散热器中由风扇吹走。因此微混车不存在冬季续航里程短的问题,毕竟它的纯电行驶里程本来最多也就几十公里,没人期待它要经常纯电行驶。空调压缩机也为48V也有的车是和传统燃油车一样使用发动机输出轴驱动空调压缩机,有类似经验的司机应该体验过夏天开车途中开空调突然车子减了点速。作为混动车,48V空调压缩机也成为一个选择。但是由于48V电池的电量有限,通常需要发动机在驾驶的同时通过48V电机发电给空调系统运作。给用户的体验可能就是少了上面提到的这个开空调车子抖的体验了吧,也算是舒适性的提高。而且48V电控空调压缩机的转速调节也相对比较灵活,热管理系统就可以轻松地管理冷却量。架构简单,控制单纯由于需要通过热管理操作的部件不多,因此热管理架构较为简单,一般用不到并联回路,因此使用一些开关阀即可控制回路而用不到像是多路多通阀。温度控制有时使用一些节温器即可实现,没有对温度敏感的部件,冷却水泵也只需要简单控制型的即可。
3.2 插电混动
插电混动的电压就是高压等级了,微混动因为是低于60V的系统,对车上的电气安全要求没有插电混动的高。所谓高压当然是已经配上高压电机和高压电池了,而且由名字可知还得是能从外面给车插上充电。它的热管理系统与其它类型车的区别也可以概括成以下两点。车载充电机的冷却插电混动车为了让用户在家可以插上充电桩充电,车载充电机OBC就派上用场了。普通混动车中的电能只来源于发动机通过电机发电或者是制动能量回收,而插电混动多了个外部充电的选择。和纯电动车一样,大部分插电混动车型会把OBC和其它功率电子的冷却回路串联起来,比如说高压转低压DC/DC、电机和逆变器。但是与纯电动的区别在于,插电混动的电池容量一般没有纯电动的大,所以要么充电时间更短或者选用更小充电功率的OBC,因此在考虑OBC的发热量和流阻的时候会有些许不同。执行器的电压选择变多了空调压缩机、电加热器都可以选择高压的,带来的好处是效率的提高,大家都知道功率等于电压乘以电流,如果电压升高的话那同样功率需求下的电流就可以更小,电流小的话那损耗的功率也就小了,效率就高了。不过电压升高带来的电气安全的问题和由此造成的成本的提高也是个不小的麻烦。进气增压的冷却这个其实在混动车上一般都有,作为涡轮增压的一部分,空气进气侧的增压会带来空气温度的提高,而由于燃烧效率的考量需要提前将压缩后的进气降温,后面提到的燃料电池也会提高。这一部分的降温一般可以与其它功率电子串联或者并联,因为温度范围比较接近。
3.3 燃料电池汽车
虽然燃料电池还是以商用车上的为主,乘用车也只有丰田本田现代有产品,但是由于文章着重还是以乘用车为主,且其他对比的车型也是乘用车,所以这里就以丰田Mirai为例。燃料电池的热管理系统的特色主要是以下三点:燃料电池电堆散热需求电堆为氢氧反应的场所,在产生电能的同时产生热能。温度的提高对电堆的放电功率的提高有一定帮助,但又不能将热聚集,因此需要反应产物水和电堆冷却液共同流动换热带走热量。而且维持电堆温度能够有效控制输出功率,满足驾驶员对于驱动系统的动态需求。电堆和电机逆变器这些功率电子的发热冬天可以作为座舱供暖的一部分热能。电堆冷启动的问题燃料电池电堆在低温情况下不能直接提供电能,需要通过外部的热量将电堆先预热起来,然后才能进入正常的工作模式。此时方才提到的散热回路就需要反过来变成加热回路,此处的切换可能就需要用到类似三路两通阀的回路控制阀。加热可由外部电加热器完成,电加热器的加热电能从电池提供。貌似也有技术提到可以让电堆自发热,使反应产生的能量更多的以热能的形式给电堆本体升温。增压冷却这一部分有点像混动车方才提到的,为了满足电堆的功率需求,反应物氧气的量也有一定需求,因此空气进气需要增压以提高密度,从而提高氧气质量流量。为此带来了增压后的冷却,由于温度范围与其它部件比较接近,可串联在同一散热回路中。
3.4 纯电动汽车
写在最后的纯电动汽车是目前市场上最受瞩目的玩家了。电动汽车热管理方面的研发在各大车厂和供应商都有做,下面主要讲三点它与其它车种不同之处:冬季续航里程担忧续航里程大部分功劳是在电池能量密度、整车电耗、风阻系数这些非热管理的方面,但冬季就不是这样了。为了满足座舱内的舒适度和高压电池低温冷启动,大量电能被热管理系统消耗,冬季续航里程大幅缩水已经是常态。主要原因在于纯电动车驱动系统发热量远比不上发动机,电池又对温度敏感。目前常见的解决方案比如说热泵系统,将驱动系统的发热和环境的热通过压缩机循环提供给座舱和电池,还有威马EX5在用的柴油加热器,利用一部分柴油燃烧发热提供电池和座舱的预热,另外还有一种是电池自发热技术,让电池启动时先以小部分能量实现每个电池单体的升温,从而减少对外部换热回路的依赖。
大功率充电发热其它类型的新能源车电池都比较小,需要外插充电的场合也以交流低功率为主,而高压大功率直流充电几乎是每个纯电动车的标配功能,除了像宝骏E100这种车以外都或多或少支持几十千瓦的充电功率。大功率充电虽然是直接将直流充电桩与电池相连,中间没有像交流的OBC一样的部件,但是大功率下的电池和电缆升温也是不可小觑。尤其是夏天时,甚至为满足大功率充电,比如60kW的充电功率,需要用到制冷循环参与进来冷却电池,或者是热泵系统。这么看来,大功率充电虽然缩短了充电时间提高了充电效率,但是需要热管理的复杂度和成本增加来满足这样的需求,因此针对不同价位的车型来说,并不是想提高到大功率就可以提高的。
功率电子集成散热从目前的电动汽车高压系统趋势上可以看出,往后的功率电子将越来越集成,比如比亚迪的高压三合一集成了车载充电机、高压转低压DC/DC和高压配电箱,而吉利新能源和几何A用的DC/DC和高压配电箱的二合一集成等等。功率电子的集成必然带来冷却回路的集成,这对于热管理系统而言,高压集成内部的冷却回路设计和管路流体的压降都是新的问题。集成散热的好处就在于缩短了管路长度、共享了冷却管路接口、最终节约空间降低成本。
在这个热门行业里面,也少不了胶带的大量使用。由于各家车厂的设计不同,无法准确预估,不同设计,差异也蛮大的,但是排个脑袋,估计平均仅在电池PACK上,5,6个平方米的用量是有的。让我们来了解一下这些胶带。本文仅限于胶带,其实胶水的应用点和应用量也是非常多的,尤其是很多导热密封的胶水,有时间再介绍。首先,需要了解一下电池PACK的大致结构,除去各种线束等,大致结构如下:
最上面是盖子,然后下面是Module模组,主体是电池,再往下是冷却板,最下面的holder承载的外壳。
在Module电池模组里面,市面上比较多的是三种电池方式,特斯拉常用的圆柱电池,BYD常用的方形刀片电池,宁德和孚能等使用的软包电池。在这里可以看出设计不一样,很多用胶方式就差异蛮大的,没有统一的行业标准。胶带的应用点,典型有以下:
耐高温胶带以PI膜或茶色PET膜为基材,通常涂以高性能丙烯酸压敏胶,用于锂电池壳体的高温固定粘接,以及电芯内部电极、外部极耳的绝缘保护。
终止胶带在PET (聚酯)或PP(聚丙烯)薄膜上涂布独特的耐电解液腐蚀的丙烯酸酯或者橡胶压敏胶。另外,为了方便跟踪和追溯生产线,终止胶带可做成数字胶带,即在薄膜基材上先印刷阿拉伯数字后,再进行涂布压敏胶。
蓝膜胶带由双层PET基材涂布亚克力胶层构成,pack组装中起外观保护和绝缘的作用。具备了薄膜优良的电气及机械性能的同时,还具备稳定,良好的粘贴性能。双层复合基材柔软,弯折粘贴不起翘,不留残胶,同时还使产品拥有印刷般的鲜艳色彩。
过程保护膜保护膜是由透明PET或BOPP薄膜经电晕处理后,涂以特殊不同色膏的压敏胶,经热风烘烤之后加工而成。良好的透光率,优秀的挺度,易于模切,不残胶。在电芯装配过程中保护电芯外观。
阻燃双面胶主要用于泡棉等组件的粘接。
侧板热压绝缘膜是一个单面的热熔型胶带,热压贴合在电池PACK的内侧,起到绝缘电池和外壳的作用。
导热垫片等热界面材料,导热垫片是填充发热器件和散热片或金属底座之间的空气间隙,它们的柔性、弹性特征使其能够用于覆盖非常不平整的表面。热量从分离器件或整个PCB传导到金属外壳或扩散板上,从而能提高发热电子组件的效率和使用寿命。
膨胀胶带采用OPS树脂薄膜为基材,涂布防电解液压敏胶水,电芯入壳后,在高温和电解液环境下,薄膜有150-200%左右的膨胀,将内电芯和外壳之间缝隙填满,防止震动,主要用在有震动的电动工具行业。OPS的英文全称是Oriented Polystyrene Films,中文意思是定向聚苯乙烯薄膜。
铝塑膜铝塑膜也是一个胶膜类产品。软包电池的核心材料。
行业内有多家公司在锂电池胶带行业有多年布局。
摘录自深圳美信新材料官网
-
电动汽车
+关注
关注
156文章
12069浏览量
231115 -
电池
+关注
关注
84文章
10563浏览量
129481
发布评论请先 登录
相关推荐
结构胶导热粉体揭秘电动汽车散热关键技术:高效导热材料的选用与应用策略
下一代电动汽车充电的热管理技术
JAE电池管理系统解决方案助力优化电动汽车性能
EV电动汽车热管理系统研究及二维氮化硼材料导热方案
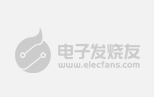
电池热管理系统的作用是什么
电动汽车热管理系统常见故障有哪些?
电池模组的热管理系统是如何设计的,有哪些高效的热管理方案?
电动汽车电池包电压及交流内阻测试解决方案
电动汽车的电池管理系统(BMS)技术解析
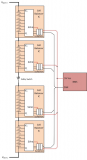
评论