在可持续发展理念的不断深化之下,电动汽车迎来了高速发展,其保有量也在迅速提升。据BCG预测,到2030年,电池供电的电动车(BEV)与插电式混合动力汽车(PHEV)将占据全球近四分之一的汽车市场。
随着电动汽车的发展,新能源电池行业也水涨船高。一块电池的落地需要经历复杂的工序,包括涂布、焊接、封装等重要工艺流程。为了保证电池制造的高质量,在多个环节需要采用视觉检测技术,明确制造中是否产生缺陷/错漏,这对检测手段提出了自动化、高精度的要求。
— 超声探伤—
基于超声波在金属内部传播的反射信号分析获取缺陷信息,人工手持接触式操作,无辐射
— 射线探伤—
基于射线的穿透能力,获取材料内部透射图像,非接触式,但具有电离辐射,对人体有伤害
常规的金属材质的缺陷检测方案大多采用射线检测与超声检测,然而射线具有电离辐射对人体有害,且多用于单一部件的缺陷检测;传统超声技术需要耦合剂辅助的接触式检测,难以实现自动化安全的在线检测。因此,对于电池行业的工厂制造流程而言,非接触式的可自动化检测的方案是非常急需的。
虹科无损检测技术
虹科LEA(激光激发声学)超声无损检测技术利用非接触式超声波检测电池单元的质量问题。与传统的超声检测相比,该技术不使用任何偶联剂或凝胶,不需要接触样品表面,因此可以实现自动化的在线检测。该技术的核心是作为超声探测器的无膜光学麦克风产品,没有任何机械振动部件,能够实现非接触式的宽探测范围的声信号检测。
点击了解无膜光学麦克风技术原理
基于光学麦克风与高频激光的无损检测LEA系统,是采用了激光超声的技术原理:激光激发样品表面产生超声信号,光学麦克风在同侧或者对侧探测超声信号,实现内部缺陷的扫描成像。
激光声学无损检测技术原理图
此过程可识别可能对电池性能和使用寿命产生重大影响的属性。鉴于电池在电动汽车、可再生能源系统和电子设备等应用中的广泛使用,通过识别和解决可能出现的任何潜在问题来确保其安全性、可靠性和性能至关重要。
> 查看电池芯内部!
> 无接触或偶联液的电池无损检测
> 全自动高速电池单元检测
> 以0.2 mm 分辨率检查电池单元的电解液润湿状态
> 确保袋细胞的完美密封
> 检测模块外壳壁后导热膏中的空隙区域
> 实时监测超声波箔片到片焊缝
电池行业应用案例
虹科电池检测解决方案>箔片焊接过程监控> 软包电池密封检测> 导热膏检测> 激光焊接母线检测> 棱柱形电池和软包电池内部电解液分布状态检测
1
电解液分布检测
电池单元与电解质的均匀润湿是电池预期寿命和可靠性的决定性因素。LEA(激光声学)技术通过使用独特的非接触式超声方法,可以非接触式检测棱柱形和软包电池内的电解质润湿状态。
原理如图所示:短激光脉冲在电池中产生超声波。波穿过电池,并在由于高声阻抗不匹配而被电解质适当润湿的区域反射。光学麦克风拾取离开电池的超声波。然后,LEA系统的软件会创建一个图像,让您看到电池内部,并突出显示电解液润湿正确和不正确的区域。
2
电池焊接检测
电极箔片焊接到集流器接线片上,这对于电池的稳定性和安全性至关重要,并且使用超声波焊接机可以快速、经济地完成。虹科的光学麦克风与WeldAlyzer数据分析软件相结合,可以对这一重要的电池生产步骤进行快速可靠的在线过程监控。
母线用于永久性的电池到电池和模块到模块的连接。激光焊接通常是首选方法,因为它是连接母线最为快速且经济的方法。虹科的非接触式超声波检测方法可以检查这些焊缝的质量,并避免在交付后出现故障。
3
软包电池密封检测
软包电池是指以聚丙烯薄膜为基材,涂覆一层或多层有机电解液后加工而成的可弯曲的圆柱体或卷状结构的新一代锂离子动力电池。由于这种新型材料具有良好的柔韧性及良好的导电性,因此可以制成各种形状的电芯产品,并且能够适应于不同的使用环境要求而进行相应的调整和优化设计以满足用户的不同需求,在电子行业应用广泛。
软包电池依靠聚合物涂层铝箔外壳,这些铝箔的密封错误会导致电解液泄漏,在制造流程中需要避免这种情况。LEA系统可以自动检测密封中最小的泄漏,并优化生产线的产量。
4
导热膏分布检测
为避免过热,电池组或模块中包含的所有电池单元都需要热连接到外壳,这是通过用导热膏填充任何间隙来实现的。
LEA系统的单侧检测技术允许快速检查,以查看所有间隙是否被填充,即使在大型电池模块中也是如此。
-
检测
+关注
关注
5文章
4484浏览量
91445 -
电池
+关注
关注
84文章
10564浏览量
129505
发布评论请先 登录
相关推荐
虹科应用 为什么虹科PCAN方案能成为石油工程通讯的首选?
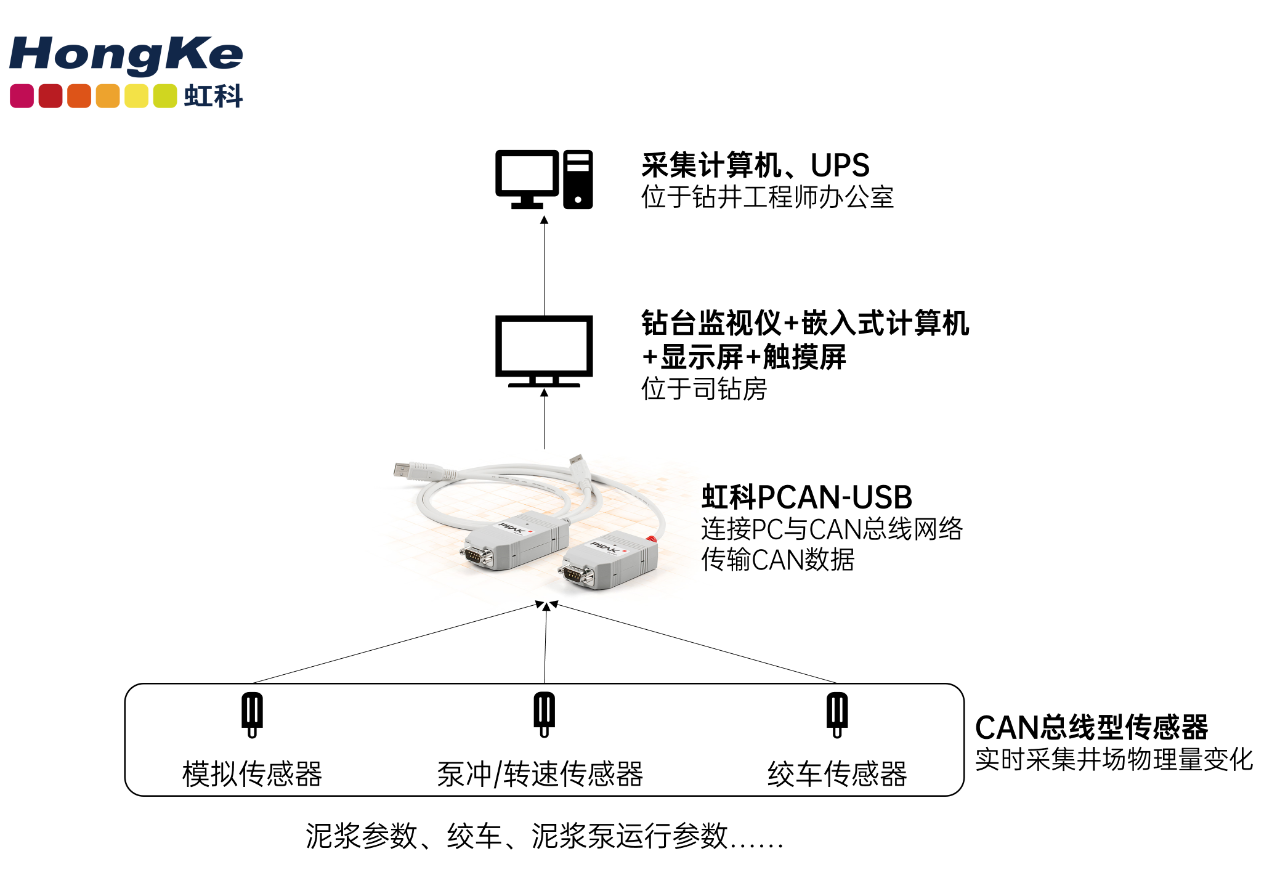
虹科方案 | 精准零部件测试!多路汽车开关按键功能检测系统
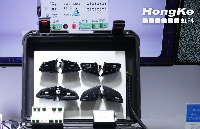
电应普传感器 | 工业非接触式液位监测方案
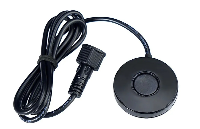
虹科方案 领航智能交通革新:虹科PEAK智行定位车控系统Demo版亮相
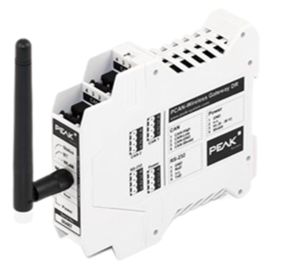
电池仓气密性检测行业解决方案
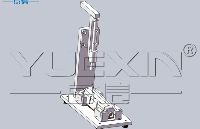
虹科方案丨低负载ECU老化检测解决方案:CANCAN FD总线“一拖n”
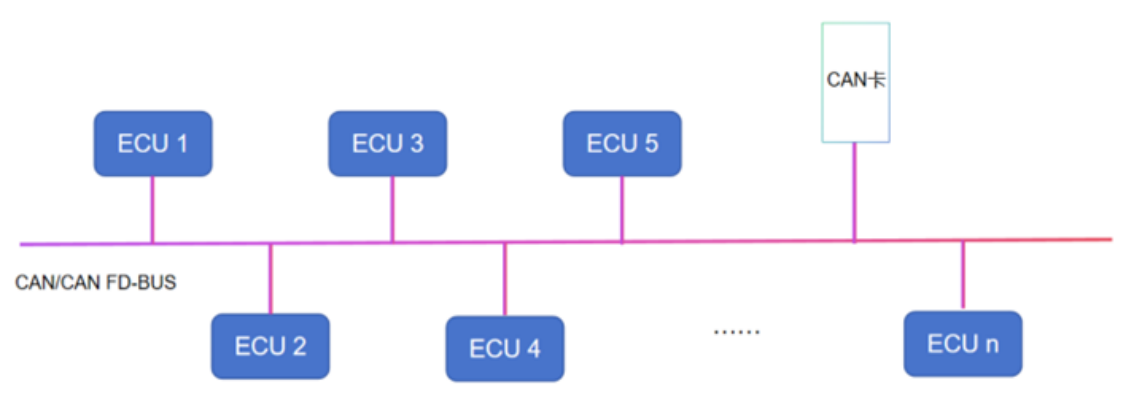
虹科方案|低负载ECU老化检测解决方案:CAN/CAN FD总线“一拖n”
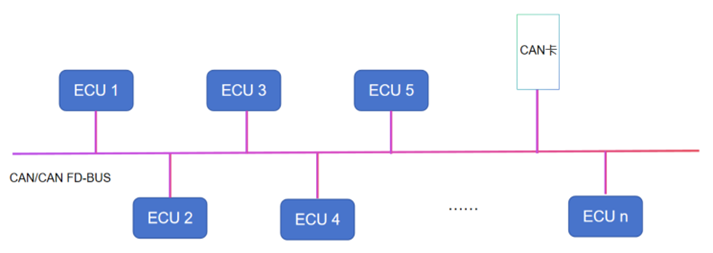
评论