经典单管TO直插封装有两类TO-220和TO-247,其使逆变器系统并联扩容灵活,器件成本优势明显,且标准封装容易找替代品,广泛应用于中小功率范围。在单管电驱应用方案中可以覆盖30kW到180kW功率范围,最多需要6-8个单管的并联来实现方案。
用于最新汽车级EDT2芯片的器件参数Vcesat/Vth分布比较集中,器件之间电气参数差异小,并联降额比例小,可以有效提升整体输出能力。相比第三代650V IGBT3电流密度1.6A/mm²,EDT2芯片电流密度可以达到2.8A/mm²,相同封装尺寸内单管封装额定电流也在增加,芯片技术提升了产品电流能力,但单管传统散热方式成为提升有效输出电流的掣肘,且功率脚需要通过电阻焊方式连接母排实现更大负载载流。这就是通常说的“芯片”和“封装”两手都要抓,想一下芯片内部结温奇热无比达到175°C,还要封装快速散热来多干活增加输出出力。尤其当汽车加速超车,想感受一下加速度时推背感,瞬时大扭矩大电流输出才能保证,那只能想办法将封装改进一下,但同时还要考虑汽车电驱长期可靠性运行,满足AQG 相关标准。
单管散热问题
单管TO-247 PLUS是在传统TO-247上经过优化内部布局,以放置更多芯片实现电流密度增加而开发的新封装,如图 1(a)。其内部键合绑定线数量达到4根,提升电流能力的同时也增加了产品可靠性,如图1(b)。
由于新封装上没有额外安装孔,安装时用夹具可以节省生产时间,且整个热扩散底板面积达到190mm2,相比TO-247-3封装也可以提升26%,热表征参数热阻RthjH也有一定改善。但这种局部封装变化对整个输出电流增加比较有限,如何改进封装来提升输出能力?要从单管实际应用中影响散热外部热传输的路径入手。
图1.单管TO-247 PLUS封装
如图2(a)是单管散热时的基本组成部分,由于芯片背面的集电极collector焊接在引线框架上,通过绑定线与外部功率端子相连,因此从背板到水冷板连接界面不仅要考虑散热问题,以确保低Rth(CH)热阻,还要保证绝缘能力达到低耦合电容Cσ的需求,确保电气长期工作的可靠性,这都使单管的生产安装相对复杂些,成本会高些。
图2.单管散热路径和方法
图2 (b)是典型两种单管散热绝缘方法,左边是直接涂敷即绝缘有导电的复合材料,但其厚度要达到230um,折弯安装时易损坏;右边是常规散热界面,采用厚度150um、导热率1.3W/m*k绝缘薄膜K10来实现,成本比较低。
由于单管背板沿对角线形状呈现中间低两头高的分布,有时需要50um、导热率2W/m*k的导热硅脂进行填充确保绝缘薄膜与底板、散热器之间有良好接触。更进一步的方法,则是在单管的底板预涂绝缘复合材料,能满足低耦合电容,2.5kV/1min 50Hz绝缘要求,这样不仅能降低35%热阻RthjH,增加器件输出功率,降低器件运行结温,而且能简化单管安装过程,降低生产成本,且100%出厂测试。但从复合材料自身导热率3W/m*K上看,降低热阻仍然有很大提升空间。从导热性能上看硅脂、绝缘膜、绝缘复合材料都不是最优的选择,都会影响散热性能发挥,进而成为单管输出功率增加的瓶颈。
背板回流焊接
那有没有即绝缘又保证散热良好的解决方法呢?英飞凌的TO-247 PLUS封装像SMD一样,其背板可以回流焊接在AL2O3DCB 或 Si3N4AMB上,同时该陶瓷基板需要再焊接到冷却板上。图3所示为典型结构,每层厚度和材料导热率如表1所示。焊锡材料采用无铅合金焊材SAC305,含锡量96.5%, 3%银和0.5%铜,符合RoHS,Reach并符合 IPC J-STD-006 标准,其润湿性好,流动性强,高可焊性和扩展性,其典型液相线温度为220°C。在实际应用中组件也有通过导热硅脂或相变材料与水冷板形成导热界面,此时需要夹具来固定确保很好接触,安装压力的不同会引起热阻的差异。
图3.单管组件背板焊接截面示意图
下表1是上图中200A/750V单管横截面中每层的物理材料厚度、导热系数以及热膨胀系数CTE值,其中陶瓷衬底DCB AL2O3是标准尺寸。
表1.每层厚度和热参数特性
陶瓷衬底是这个单管回流焊外部最主要的散热路径,除了表中标准AL2O3衬底外,还有其它如高性能ZTA AL2O3,主要性能如热膨胀系数CTE、导热参数、杨氏模量、介电常数基本都变化不大。通过在AL2O3中添加9% -30%氧化锆ZrO2,材料抗弯曲度大大提升,大于450Mpa左右。这能有效地减小由于器件安装时夹具产生应力或焊接中热膨胀产生的形变热应力引起绝缘衬底裂纹的风险。另外,传统DCB通过共晶键合法,铜和陶瓷之间没有粘结材料,尤其单管SiC在器件高温、大功率、高散热、高可靠性上很难满足需求。而氮化硅Si3N4-AMB作为绝缘衬底是在个不错的选择,抗弯曲度大于700Mpa,导热系数是80W/m*k,热膨胀系数2.5x10-6/k,与Si材料很接近。AMB覆铜基板利用活性元素可以润湿陶瓷表面特性,通过活性金属钎焊工艺形成粘结强度高的界面。因此,绝缘衬底选择以及焊接工艺参数是单管背板回流焊接是否成功的外部决定因素,但单管封装自身是否能满足回流背板焊接是关键的内部因素和基础,二者在应用层面不可或缺。
改善热阻Rth
单管背板回流焊接对散热和绝缘处理来说都是一个很好的解决方案,可以把影响单管输出电流流能力的两个关键问题克服。基于前表提供750V/200A EDT2单管各层材料的数据进行理论上热阻数据的直观对比,图4分为5种不同应用情况进行评估,覆盖DCB双面、单面焊接和涂导热硅脂相结合。这个只是理论上评估热阻差异,垂直散热看实际理论热阻,与实际芯片发热引起热阻会不同。考虑客户无法满足焊接工艺时,可以考虑导热硅脂和焊接配合的应用情况。从结果看,这种单管背板焊接工艺大大降低热阻,常用的DCB AL2O3相比导热绝缘薄膜K10而言最大达到减少了65%,进一步用导热性能更好的AMB S3N4陶瓷衬底,热阻还可以进一步优化降低。从输出电流能力和可靠性提升上,这是一个好选择,但从成本上讲不是最优。
图4.不同陶瓷衬底和导热硅脂结合热阻对比
从单管芯片到外部衬底焊接整个环节RthjH里面来看,图5和6是两种的热阻分布情况。从传统K10分布看其占据热阻比例达到77%,是整个散热路径的主要瓶颈和决定因素,因此,进一步印证用单管背板回流焊解决这个环节的必要性。从经典AL2O3DCB 热阻分布看,AL2O3绝缘材料在整个散热路径中占比达到54%,DCB两面的焊接层占比达到12%,因此,这也为如何进一步优化背板焊接增强散热能力提供了方向,改善焊接层工艺,如Sinter银烧结工艺,或高性能衬底材料,如Si3N4衬底,甚至单管芯片直接焊接在DCB上都是提升单管散热的方向,尤其使用芯片面积更小的SiC芯片。
空洞现象
在背板回流焊时界面空洞率是表征基板质量的重要因数之一,产生基板的空洞率主因有两个方面,其一原料表面有凹凸、划痕、有机污染等质量上的问题,其二焊接工艺参数影响焊料润湿性,不能形成有效焊接可靠的焊接层。
DCB焊接层形成的空洞不仅在周边有放电隐患影响电气性能,还会影响导热性能,这也是焊接中不可避免的问题,同时也是背板焊接好坏的关键,尤其电驱长时间工作进行高低温冲击时可靠性问题。图7中左边是小空洞联合起来形成大的空洞,右边是分散分布小的空洞。即使二者有相同的空洞百分比,但单个深大空洞对热阻和可靠性影响最为严重,热集中在该点上,容易出现热失效问题[3]。
可以进一步用具体化实例来看这个空洞影响,假定在单管芯片正下方有个圆形空洞,DCB尺寸20mmx23mm, 如图8所示初始热阻Rthja为0.292k/W, 当空洞增加到10%,热阻增加了10.3%;当空洞增加到25%, 热阻增加了34.2%。因此,空洞率和空洞大小成为单管背板回流焊接的关键。
回流焊接工艺要求
根据标准J-SDT-020E要求,非气密性封装按照湿气引起应力的敏感度来分类,以确保他们能正确储存、安装和回流焊时不被损坏。表2为无铅封装工艺流程的温度定义。按照EDT2 TO-247 PLUS 3pin的厚度5mm、体积1670mm3,4pin厚度4.8mm、体积为1729mm3,焊接最大允许峰值温度不超过245°C,如绿色方框所示。
表2 不同封装焊接温度
按照标准中根据封装含锡铅和无铅来分类,目前绝大封装都是无铅封装,如图9中红色方框所示来定义回流焊工艺要求,右图为图形化来显示焊接温度曲线,主要是要求单管封装从预热区域从Tsmin到Tsmax,升温区从Tl到Tp,回流焊接区及最大允许峰值温度Tp,到冷却区,在每个温度的变化区间都有温度上升斜率和持续时间要求。
图9.STD标准中回流焊温度
对于用户不要超过最大限制温度245°C,对于单管器件焊接过程由于焊接温度波动、背板平整度、焊料材料合金差异,其实际短时焊接峰值温度要大于最大温度限制,这对单管封装优化都带来了挑战。如图10为不同温度情况出现焊接层的空洞,这对焊接长期可靠性会带来一些可能的风险,需要工艺和器件封装同时优化来提升。关于单管真空回流焊接工艺和空洞分析,建议进一步与原厂进行沟通,会针对性地提出一些改进措施和方法。
图10.实际焊接空洞
改进单管封装
是不是现存的TO-247封装都能满足这种回流焊的能力呢?答案是明确不推荐。主要问题是塑封材料在运输储存过程中有空气湿气渗入其中,在高温回流焊中发生膨胀可能会引起塑封从引线框架上出现分层以及芯片焊接处熔化问题,如图11。当背板焊接曲线最高熔点温度越高,其分层和熔化现象约明显,如图12。所以有时需要通过预加热方式或采用低温焊锡膏来解决现存封装的问题,这都会增加应用成本和系统的长期工作可靠性。
改进封装TO-247 PLUS经过优化处理解决分层问题,使单管焊接在DCB上可以长期可靠工作。按照IPC/JEDEC J-SDT-020可以满足MSL1 等级和焊接曲线要求,包括芯片顶部与塑封材料,引脚/引线顶部以及芯片焊接引线框架部分都没有出现分层和熔化,如图13所示。
图13.改进封装后的焊接效果
英飞凌汽车级可回流焊单管有120A、160A、200A三种电流规格且该封装在规格书中都有相关回流焊接能力的标注和承诺,详情请参考相关规格书。考虑到电驱应用中水冷条件下单管电流出力能力很高,有效值电流水平几乎达到额定电流80%以上,其绑定线和引脚热应力会比较严重,功率回路需要母排来载流,单管功率脚也需要电阻焊能力;同时考虑未来SiC单管要做到9mohm,电流要到200A以上,TO-247 PLUS-4经过优化增加脚宽度来减少热应力,同时功率C-E之间Pin脚间距达到7mm,可以满足高电压470V应用需求。由于发射极kelvin脚的引入,损耗降低的优势进一步显现,大约12%降低,建议产品设计考虑该封装带来的效率提升。
-
新能源
+关注
关注
26文章
5499浏览量
107522 -
封装
+关注
关注
126文章
7924浏览量
143030
发布评论请先 登录
相关推荐
芯动能第100万只车规级电驱双面散热塑封模块成功下线
新能源汽车散热解决方案
BGA封装对散热性能的影响
解决方案丨EasyGo新能源系统实时仿真应用
新能源汽车电池三大散热方案
如何提升LM6171的散热性能?
EMS/PCS/BMS/充电桩/逆变器新能源设备处理器选型-米尔嵌入式
长电科技创新电源模组封装设计方案,提升AI处理器的供电性能
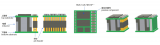
新能源汽车功率模块的“散热神器”——AMB基板
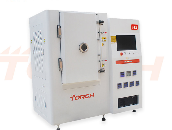
新能源汽车需要怎样的主驱逆变器?汽车厂商又如何选择合适的主驱方案?
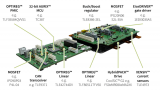
【换道赛车:新能源汽车的中国道路 | 阅读体验】新能源汽车值得买吗?未来又会如何发展
碳化硅模块使用烧结银双面散热DSC封装的优势与实现方法
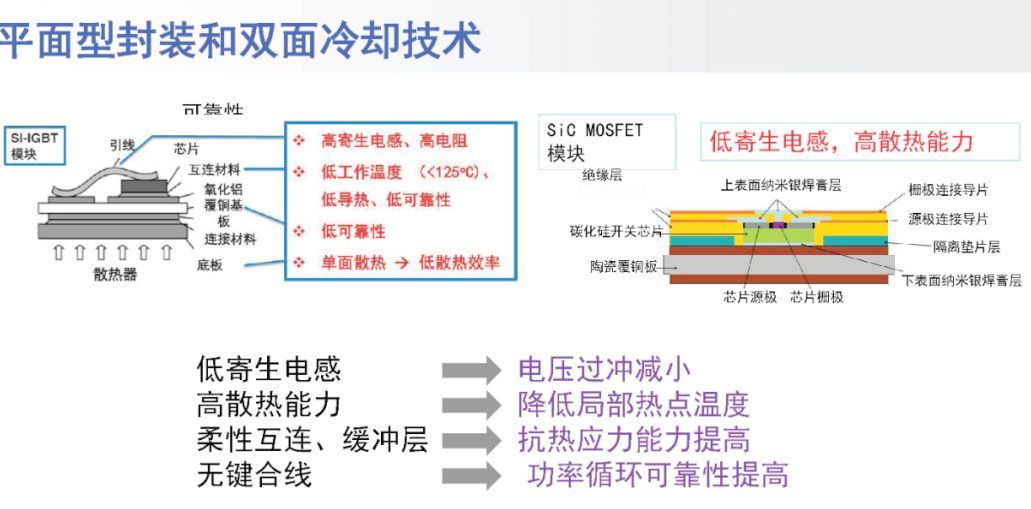
评论