一个热处理“患者”在工作过程中,发生了断裂失效问题,经过“医生”的检查发现原来是因为混晶的存在。
其实在机械制造行业当中,热处理工序过后金相观察时,经常会发现混晶现象,今天我们就来聊一聊混晶问题。
一、什么是混晶
混晶,顾名思义,就是晶粒度大小不一的混杂在一起。晶粒度是表征金属材料韧性好坏一个指标,晶粒度级别越高,材料韧性越高,反之韧性越差。如果在高级别晶粒的区域中混入低级别的晶粒,就会拉低金属材料整体的性能,低级别晶粒所占比例越大,材料的整体性能越不稳定。
一般情况下,我们把相差3-4级晶粒度的晶粒同时出现在组织当中的情况,就认为发生了混晶。当大晶粒所占比例超过10%时,我们就不得不重视大晶粒可能造成机械零件的早期失效。
混晶所产生的不稳定因素,让我们无法预知机械零件可能在什么时候失效,所以混晶对于热处理工作者来讲,是非常不愿意看到的。
混晶金相图片如下图所示:
二、混晶的起因
混晶产生的根本原因有两个大类:
A、合金元素偏析(合金元素分布不均匀)
B、临界变形度(钢铁发生了变形,晶粒发生变化)
围绕这两个原因,从钢材冶炼开始谈起。
1、钢材冶炼:
我们都知道钢材冶炼过程,就是用铁矿石和各种原料经过复杂工艺最终冶炼成钢水,然后浇铸形成钢锭。钢水的形成过程钢厂是最专业的,并且作为液相的钢水来讲,均匀程度自然不在话下,所以此处不做评价。我们只说钢水冷凝成为钢锭的过程。
钢锭偏析是我们最为常见的一种偏析形式。用通俗的话来讲,钢锭产生偏析原因很简单,就是合金元素在凝固过程中,容易先凝固,而合金元素少的地方会稍后凝固,这样就造成了合金元素的分布不均匀的现象,最典型的金相组织是枝晶偏析。还有一些杂质,夹渣随着钢液的翻滚冷却过程,也会在特定的位置聚集。
偏析最大的问题就是会导致合金元素的分布不均匀。也就是说会导致碳、铬、镍、钼、铝等等合金元素的分布不均匀。这些元素的分布不均匀就会形成一个个相对独立的小区域,这个区域内有着不同的化学成分。严重一点说,每一个区域都是一个钢种。
在这个阶段,我们仅仅看到了这样的晶粒,还和混晶说不上,你是不是依然很疑惑呢?
2、钢材轧制:
从钢锭到钢材出厂,需要一个过程,这个过程就是轧制。钢锭变成我们需要的棒材、板材、线材、型钢等等,需要对钢锭再加热,然后经过N道轧制,最终满足我们的需求。
轧制前一般会对钢材进行扩散退火,扩散退火的目的就是为了让钢材合金元素均匀化,就是在1中提到的,凝固过程中合金元素的偏聚导致了成分不均匀,这样的钢材会有很大的问题,所以通过扩散退火,温度在1200℃左右,这时候合金元素活性增加,活动范围加大,会在钢铁内部做扩散运动,也就是从浓度高的地方跑到浓度低的地方,这样就可以提升钢材的均匀性。同时,毕竟这个钢铁还是固体的,没有变成液相,虽然合金元素发生了移动,只是对钢材均匀性进行了改善,不能达到完全消除的目的。
轧制的过程相当于锻造和挤压过程。在这个过程中,钢材经受了加热、锻打、挤压、降温、再结晶、退火、再挤压等等工序。原始钢材的一些缺陷在这个过程中被逐步缩小,合金元素的偏聚程度也逐步降低。
如果这个两个过程是完美的,那么就不存在后边的问题了,但是现实是残酷的。为了节约费用、降低成本,钢厂在这两个环节会提高生产效率,就有可能会扩散退火温度不足、时间不足,轧制过程省去退火工序、加大锻造比等等手段来提升生产效率。这样一来,原材料的缺陷有可能会被掩盖,但是没有根除,甚至在轧制过程中会越演越烈。这个变化,我们在3中讲述原因。
3、变形问题(锻造、挤压):
机械加工厂拿到钢材以后,形状结构复杂的一般情况下会采用热锻造、冷挤压的方式,让工件预成型,然后再精加工,热处理,磨削最后做成成品。那么在这个过程中,问题来了。其实加热锻造和2所讲的钢材轧制是一个道理,只是设备不同,压缩比不同,产品结构不同而已。冷挤压是在不加热的情况下,利用钢材本身的韧性产生塑性变形来成型的工艺。这两个工艺都牵扯了一个问题那就是塑性变形。
我们知道金属的韧性就是指他的形变能力,通俗的说就是拉伸或者压缩的能力,能够被拉伸的越长,说明韧性越好,能够压缩的越短,说明韧性越好。在拉伸或者压缩的过程中,晶粒发生了什么变化呢?我们想想一下橡皮筋。一开始橡皮筋的直径是10mm的话,如果你拉伸了长度的10倍,那么它的直径变成了多少?肯定不是1mm,但是为了说明问题,大家都知道他会变细,继续拉,他会更细,直到你拉断他。
金属的变形就是晶粒发生变化的过程。没有发生形变以前的晶粒虽然形状不规则,但是大家还都相安无事,基本上是以团状存在,随着外力到来,大家就像橡皮筋一样被拉扯,生存空间被挤压,只能随着外力变细,不断变细。原来是一堆土豆,现在变成了一束麦子。在这个过程中,大家还是相安无事,没有太多的事情发生,甚至你会惊奇的发现,晶粒度超级好。从土豆粗细,变成麦秆大小,确实细了不少。但是我们要擦亮眼睛,不要被表象迷惑。
4、热处理:
热处理作为中间工序,看不见摸不着,不能即时检测,过程中无法调整,只能通过过程控制和最终检验确定产品状态。前边的所有工序所产生的问题都在热处理集中爆发了。热处理的渗碳、淬火工艺,都要求加热到钢材的奥氏体化温度以上才能进行。这就不得不将工件加热到AC3温度以上进行作业,在这个过程中,发生了很多奇妙的转变。体心立方的铁素体晶格转变为面心立方的奥氏体晶格,溶碳量增加,合金元素融入量增加,合金元素的扩散等等都在这个过程要发生。晶粒之间的界限也会被打破,重新结晶,原始晶粒要发生变化,晶粒要重组。
晶粒重组的过程,说的简单点就是比拼能量的过程,有点恃强凌弱的意思。就比如我们目前的国际形势一样,高科技、核武器、作战能力等决定了国家的大小,能力越强国家越大,能力越小,国家越容易分裂。合金元素所形成的碳化物就像一个一个据点一样,扎在这些国家当中,阻碍晶粒的长大,而另外一方面,在合金元素稀少的地方,所到之处,所向披靡,版图不断扩大,晶粒逐渐长大。
为了保证产品的变形尺寸,加热温度不能太高,就会导致合金元素的扩散行为受到牵制,加热温度太低,不能满足奥氏体化,就会导致相变无法进行,所以热处理的加热问题属于中温加热,大大受到制约。
一般情况下,渗碳温度在900-940℃左右,淬火温度一般在AC3温度以上30-50℃进行。这些都是教科书上留下的数据。那现在就讨论一下在这个温度下,1、2、3可能会给我们带来什么后果。
a、合金元素的偏析的影响:
随着奥氏体化的进行,存在不同区域的合金元素含量不同,会导致这些区域的奥氏体化温度高低不同,在工件达到同样温度的前提下,有的区域已经开始了奥氏体的转变,有些区域还在准备过程中;有的区域已经奥氏体转变完了,有的区域还没有结束,这就势必导致那些先转变为奥氏体的区域的晶粒不断长大,而那些还没有转变完了的区域的晶粒细小。如果此时终止奥氏体化,快速冷却,就会产生大小晶粒的并存,严重的话就会产生混晶。
合金元素当中大多数元素都会阻碍晶粒长大:如V、Ti、Nb等;有合金元素会减慢奥氏体形成速度,如Cr、Mo、W等;这样的元素会影响晶粒度变大,起到细化晶粒的作用。同时也有少数元素会促进晶粒长大:如Mn、P等。如果这些元素在钢材中偏析严重,就可能发生混晶。
b 、轧制过程和锻造过程以及冷加工过程的形变的影响:
这个过程中晶粒受到拉扯和挤压导致的晶粒变形,使得原本的晶界虽然存在,但是能量降低。
随着加热温度上升,到了钢材本身的再结晶温度的时候,晶粒就会重组。此时合金元素的能量越来越大,两个相邻的细条状的晶粒。原本只能在晶粒内活动的元素,突破两个晶界之间变得更加容易,他们就会走捷径,两个细条状晶粒就会在极短时间内合并形成一个大晶粒。随着加热温度和加热时间的变化,这些晶粒不断的长大,直到没有能量再去突破晶界的约束的时候才会停下来,此时已经形成了很多的大晶粒。这样的形变晶粒并不是所有的都会产生这种情况,只有当达到临界变形的晶粒才会长大,这样还存在一些正常的晶粒,于是就产生了混晶。
C、温度的影响:
锻造过程、热处理过程温度和时间的影响对于晶粒的影响也非常大。当温度较高时候,保温时间较长的情况下,晶粒也会长大。这个温度根据材质而定,不同的材质的极限温度不同。
热处理的温度一般比较固定,常规渗碳温度一般不会超过950℃,这个温度下,大多数的本质细晶粒钢不会发生较大变化。但是也不排除参数错误或者温度不准确导致的超温,而使钢材发生晶粒粗大。
锻造超温发生的晶粒粗大,一般会在锻造后的金相中发现魏氏组织。可以通过多次正火来消除魏氏组织。从本质上来讲,温度造成的晶粒变化,可以通过正火来弥补。但是现实中如果出现魏氏组织,一般不建议使用。
小结:
综上所述,混晶产生的最重要的原因就是元素偏析,并且在后续的过程中很难通过热处理方法来消除。
其次,就是能够产生形变的每一道工序,需要注意晶粒的大小,纯粹的因为形变导致的晶粒度混晶,是可以通过热处理工艺来进行改善的。如果晶粒已经长大,并且状态稳定,合金元素已经在晶界上析出的,处理起来也会比较麻烦。
-
机械零件
+关注
关注
0文章
20浏览量
7771 -
晶粒
+关注
关注
0文章
28浏览量
3777
原文标题:什么是混晶?
文章出处:【微信号:深圳市赛姆烯金科技有限公司,微信公众号:深圳市赛姆烯金科技有限公司】欢迎添加关注!文章转载请注明出处。
发布评论请先 登录
相关推荐
好多人都不知道led电子显示屏隐藏的几大误区
ADC应用领域中的混叠简介
新能源车的48V轻混动系统
什么是混控
如何巧算混联电阻
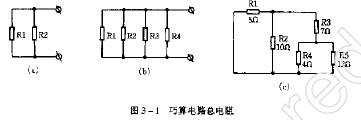
什么是混联电路_混联电路的分析和计算

混联电路图怎么看_如何简化混联电路图
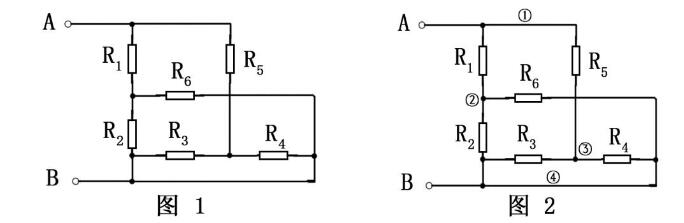
晶电开发出能让混光区域趋近于零的芯片
中欣晶圆混改和扩产增资轮投资完美收官
第一、二、三代半导体的区别在哪里
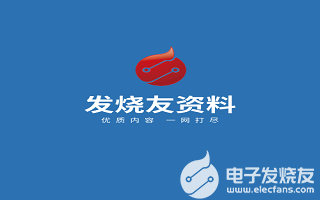
面向氮化镓光电器件应用的氮化镓单晶衬底制备技术研发进展
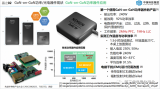
第一代、第二代和第三代半导体知识科普
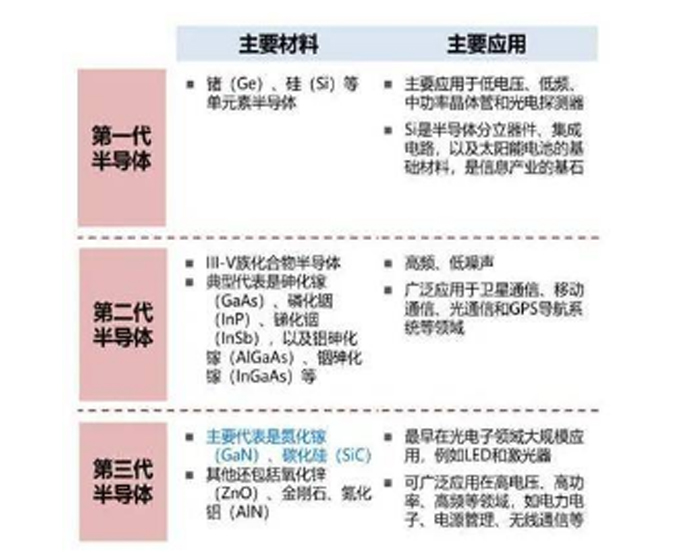
评论