一、
储能温控历史机遇
温控提高电池安全性,解决储能后顾之忧
新型电力系统中,我们可以从供给侧和需求侧两个角度来看待:
1.供给侧:新能源正在逐渐成为电力系统的主要装机和电量来源。
2.需求侧:终端能源消费已高度电气化,越来越多的“产消者”涌现。
3.从整个系统的角度来看,电力系统运行机理也发生了深刻的变化。新能源发电具有随机性和波动性,无法通过调节自身出力来适应用户需求的变化。因此,传统的“源随荷动”模式已经不再适用于新型电力系统。我们必须采取储能等措施,通过源、网、荷、储之间的协调互动来实现电力供需动态平衡。这是新型电力系统中的关键所在。
全球电化学储能高速增长
2021 年全球累计装机量为 24.4GW,为 2017 年的 8.4 倍;2021 年全球新增装机量为10.2GW/yoy+117%,高增长态势仍在持续。
锂电池安全性、容量衰减受温度影响较大。
锂电池最佳温度区间为 10-35℃,过度的高低温均会对锂电池寿命、安全性产生影响。持续的高温环境下,锂电池内部的 SEI 膜首先分解,随后负极材料与电解液产生反应、隔膜熔融,最终正极材料及电解液发生分解。
电池的这些变化会导致锂离子通道发生闭塞,引起正负极直接接触、短路,从而放出大量热。此外,这些材料分解的过程中还会产生大量气体和热量,电池内部压力迅速增加,从而发生如电池鼓包、破裂、泄压阀破裂、铝箔熔化等热失控现象。热失控一旦发生,电池内部温差可达 520 ℃,对安全性带来严峻挑战。
高温会导致电池内阻增加、活性材料和有效锂离子流失,进而降低电池容量。而在低温环境下,电池负极会析锂形成锂枝晶,严重时刺穿 SEI 膜,影响安全性。低温会导致电解液凝固,阻抗增加,进而降低电池容量,磷酸铁锂电池容量保持率在 0 ℃下为 60%-70%,在−20 ℃时降低至 20%-40%。(根据《锂离子电池低温特性研究进展)
除温度外,电池间温差亦会对电池性能产生影响。电池使用过程中,负荷变化会引起电流波动起伏,进而引起电池组生热不均匀。电池组往复使用后,各单体电池的老化程度会有所不同,导致木桶效应。为达到电池一致性要求,单体电池温差需小于 5℃。
温控保障锂电在最佳温度区间工作,降低电池间温差,重要性凸显。通过应用温控系统,储能电池可在 10-35℃最佳温度区间工作,且电芯间温差可控制在 5℃以内,可最大程度避免热失控、容量衰减。
相较电动汽车,储能系统由更多电池单体连结而成,故发生热失控概率更高,对安全防护提出更高要求。根据清华大学车辆与运载学院,电池热失效概率为 1-(1-P)n,P 为单体电池热失效概率,n 为电池数量。
对于动力/储能电池,P 约为 10-7,假设电动汽车单车含100 节电池,储能电站含 100000 节,则根据公式,二者发生热失控概率分别为 10-5、10-2,储能电站发生热失控概率达 1/100 量级,对热管理提出更高要求。
高倍率、长时间充放电增大放热量,温控重要性愈发显著。电化学储能包括能量型与倍率型储能,前者需满足长时间放电需求,主要应用于能量时移;后者则需具备瞬时高功率输出能力,主要用于电力系统调频。
现阶段,风光发电占比不断提升,电力系统对调峰、调频均有更高需求。因此,能量型储能愈发长时化,倍率型储能需具备更高功率。在相同温度下,储能功率越高、放电时间越久,其储能系统放热量越高。因此,在长时储能、高倍率储能应用增多的背景下,储能温控重要性愈发显著。
风冷主导存量市场,液冷加速渗透
储能温控主要包括风冷、液冷、热管冷却、相变冷却等技术。其中,风冷系统结构简单、可靠性高、寿命长、成本低、易于实现,是目前国内主流技术路径。液冷系统散热效率高、散热速度快,在高倍率、高容量场景下优势凸显,故全球储能系统正呈现液冷加速渗透,取代风冷的趋势。相变冷却与热管冷却目前实际应用较少,尚处于实验室阶段,故本文主讨论风冷、液冷技术趋势。
20℃条件下放热量与放电功率的关系
1C倍率下放热量与放电时间的关系
综合来看,良好的温度控制可有效减缓电池容量衰减、防止电池热失控,对电化学储能当前两个最大的痛点,即度电成本与安全性,均有积极作用,重要性凸显。未来,高容量、高倍率储能应用增多,将对温控提出更高要求,其应用必要性将愈发突出。
储能温控技术分类
温控技术对比
液冷能耗低、电池寿命长,具更低 LCOE,正加速渗透。为达到相同电池平均温度,风冷需比液冷高 2-3 倍能耗,而相同功耗下电池包的最高温度,风冷比液冷要高 3-5 摄氏度。(根据埃泰斯新能源实验)
此外,根据阳光电源,其液冷系统可更好地控制电池间温差,从而解决电池一致性问题,其液冷储能可将系统寿命延长 2 年以上。综合说,液冷具有更高的散热效率与散热速度,并且可以更好的控制电池间温差,因此,其能耗更低、系统寿命更长,从而协助储能系统降低全生命周期成本。
液冷温控电池一致性更佳
液冷加速渗透趋势明显
目前,国内主流系统集成商均已推出液冷系统解决方案,印证其日益旺盛的需求。此外,国内部分项目在招标时指定储能系统需配备液冷温控,如淮北皖能储能电站一期、宁夏穆和储能电站等。
目前,国内储能以风冷为主,而美国等成熟市场有较高比例液冷应用。美国储能已形成自发性需求,利用率高,运营商更多考虑安全性、全生命周期成本。未来,随着全球储能利用率提升,液冷将加速渗透。
二、
储能温控产业链
上游:各种核心部件,包括风冷核心部件和液冷核心部件;压缩机上市企业包括四川长虹、长虹华意等,换热器企业包括三花智控、双良节能等,液冷板企业包括东山精密、盾安环境等。
中游:风冷系统和液冷方案;企业主要为英维克、申菱环境、同飞股份、高澜股份、松芝股份、奥特佳、宁德时代、海亮股份、龙源电力、亿纬锂能、巨化股份、三花智控、当升科技、中鼎股份、安克创新、盾安环境等。
下游:储能电池厂商、储能系统集成厂商。
三、
1、储能温控中上游如何用温度传感器
温控设备提供商:譬如英维克、 申菱环境、佳力图、高澜股份、黑牡丹、网宿科技、 依米康,温控系统能耗占数据中心非 IT 能耗的 80%,温控系统的能耗是 PUE 是否能降低到合理水平的关键因素之一。
1)散热制冷:空气冷却系统、液体冷却系统用温度传感器。
(特普生-风冷温度传感器)
(特普生-液冷温度传感器)
2)供配电:配电柜用到温度传感器、机器温控器与温湿度传感器。变压器用到温度控制器、变压测温传感器。温度传感器在柴油发电机组冷却液系统和燃油系统中,均有应用。
(特普生-配电柜温度传感器)
IT及网络设备:
“监控交换机各个硬件,比如芯片温度、扣板温度等,都设置温度传感器,并取最高值就行”。特普生曾老师说,“温度监控对服务器很重要,应对不同环境、平衡机架密度、停电预防。机架外/室内温度传感器,非常适合检测不同环境温度,提供机架的特定温度映射。机架内温度传感器,可以获得CPU、GPU、入口、出口温度的准确读数。”
2、储能温控下游如何用温度传感器
储能系统竞争格局未定,电池厂、逆变器厂商、电站厂商均进入储能系统竞争。储能系统由电池组、 消防、温控、PCS、EMS、BMS构成。储能设备主要由电池组、储能逆变器( PCS)、能量管理系统( EMS)、电池管理系统( BMS)构成。
电池组为最主要的构成部分,其主体由电芯构成。电池组中涵盖其他辅助系统包括温控(散热),消防。储能逆变器为必不可少的重要组成部分,负责直流交流转化,是电站并网运行的必备条件。EMS、 BMS主要集中于系统软件层面,由储能投资商负责设计, EMS负责数据采集、能量调度;BMS负责电池监控、管理,保证充放均匀稳定。
“拥有储能BMS配套、储能线束加工优势的我们,为储能管理,做性价比高的温度采集管理方案。方案为BMS提供锂/氢电池本体、电池冷却介质与BMS控制板的温度管理,也为储能CCS集成采集母排提供温度采集管理,”——温度传感器专家特普生曾总告诉温度床传感器研究院说。
“目前,市场反馈的传感器失效模式为两种:防水与耐压情况不佳。防水是指吸潮后传感器阻值下降,主要为潮气影响;耐压则是传感器绝缘层被击穿。为妥善解决传感器失效模式,特普生传感器针完全胜任。一是针对潮气影响,特普生传感器在保持耐温175度的条件下、耐水煮168小时。打破行业48小时极限;二在绝缘度问题上,特普生传感器可长期耐压5VDC,远高于行业3500VDC的标准要求。”
1)特普生储能CCS集成采集母排
(特普生户储CCS隔离板)
“我们为电池包、电池模组、电池族、储能箱公司,也为BMS产品,提供定制化的储能CCS隔离板。譬如支架,可以选择注塑或吸塑隔离板+线槽;采集组件,可以选择线束、FPC、PCB或FFC;温感采集线,可以选择环氧头、OT端子、镍端子(都含NTC);铝巴当然是含铝量达到99.6%的1060铝板。连接方式,可以选择打胶、打螺丝、超声焊或激光焊”。
储能CCS隔离板,在锂离子电池系统中实现以下主要功能:通过铜铝巴实现电芯的串并联,输出电流。采集电芯电压。采集电芯温度。提供均衡和补电通道。
2)BMS系统温度管理
“用于动力电池模组电芯的电压和温度采样,采集数据通过数据采集模块汇总、分析再传输给给电池管理系统主控制器模块,主控模块对数据进行分析和处理后,发出对应的程序控制和变更指令,做出均衡措施。适用于纯电动、混合动力乘用车、物流、客车、特种车等车型及48V动力系统 。它具有组装工时短、小型化、轻量化、薄形化、可挠性、弯折性好等特点。”
(电池BMS温度传感器)
“也有一些客户需求电池芯内温度采集线束。这时,NTC温度传感器特别适合用于电池内芯与芯之间。最小直径尺寸可以做到0.7mm ,最薄可以做到0.6mm。柔性化,可弯曲,便于安装。”
(电池芯内温度采集线束)
“固定片NTC温度传感器主要用于电池PACK模组。它采用单端玻封NTC热敏电阻,外围用环氧树脂+外壳封装,热敏电阻和导线的焊接点完全密封在树脂涂层里面,具有良好的防水性及密封性。环氧树脂封装温度传感器将高精度、高可靠的NTC热敏电阻与PVC或Teflon导线连接,用绝缘、导热、防水、防潮材料封装成所需形状,便于安装与远距离测控温。通过测量NTC热敏电阻的电阻值来确定相应的温度,从而达到了检测和控制产品温度的目的”
(电池外围温度采集线束)
3)储能冷却(风冷/液冷)系统温度管理
“储能风冷或液冷,这些冷却温度管理,要采用单端玻璃封装热敏电阻,精度高、可靠性好。譬如双85测试1000小时,耐水煮测试1000小时。采用特殊的内部结构,正常使用寿命10年以上。”
(储能冷却(风冷/液冷)温度传感器)
4)储能消防系统温度管理
“我们发现储能消防系统温度管理这套传感器,特别适合用于储能消防用,最小直径尺寸可以做到:0.7mm。响应速度最快可达1.5S(液体介质)。温湿度模块、温度气体模块等,也可以无线化数据传输。”
(储能消防温度传感器)
四、
技术路线
目前,储能温控系统的技术路线可分为四类:
(1)空气冷却,以空气为介质,通过空气对流实现热交换;
(2)液体冷却,以液体为冷却介质,既可以通过液体与电池直接接触换热(直接接触型),也可以通过冷却管中液体流动换热(间接接触型);
(3)热管冷却,利用压差及多孔材料的毛细力实现非重力方向的热传导;
(4)相变冷却,通过无机或有机相变材料,在温度不变的情况下通过物理状态的改变来实现放热或吸热。
储能温控市场的参与者可以大致分为三类:
1、传统工业温控企业,他们凭借在水冷设备方面的技术积累,进入储能温控领域的壁垒较低。这些企业和储能温控技术有同源性,代表企业包括同飞股份和高澜股份。
2、精密温控企业,他们在数据中心温度控制方面有着丰富的经验。由于集装箱储能与数据中心温控具有相似性,这些企业有望实现技术外延,代表企业有英维克和申菱环境。
3、汽车电池热管理企业,他们在锂电池温控技术和经验方面积累较为丰富。代表企业有松芝股份和奥特佳。
总的来说,储能温控市场的参与者大多具有相似的技术背景。这些企业进入储能温控领域的壁垒较低,有望取得先发优势,并共同推动该行业的高速发展。
作者简介
吴憨子:传感器应用营销老师。投资及担任森霸传感、特普生传感应用营销顾问,欢迎交流传感器应用与投融资,微信:mckinsin
您对本文有什么看法?欢迎在传感器专家网公众号本内容底下留言讨论,或在中国最大的传感社区:传感交流圈中进行交流。
您对本文有什么看法?欢迎留言分享!
顺手转发&点击在看,将中国传感产业动态传递给更多人了解!
审核编辑黄宇
-
温度传感器
+关注
关注
48文章
2988浏览量
156738 -
电池
+关注
关注
84文章
10756浏览量
132124
发布评论请先 登录
相关推荐
储能系统中,要如何选择好的温度传感器
温控开关双金属温度传感器及其应用
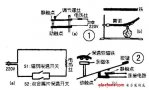
吴憨子:一文读懂储能温度传感器优缺点及应用(专家干货)
专家观点分析储能消防 吴憨子:一篇入门储能消防
吴憨子:一篇入门IDC数据中心用温度传感器
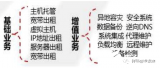
多通道温度变送器应用于液冷温控系统和储能空调
吴憨子:电网级储能温控中温度传感器的应用
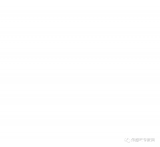
评论