引言
工程机械是国之重器,无论是在能源、交通、水利和科研等重大基础设施建设中,还是在生产厂房、生活设施建设中,已成为保障各类现代工程建设质量、效率、安全和环保的刚需。伴随着我国基建与城镇化的长期高速发展,国内工程机械行业持续高质量发展,整体已具备国际竞争力。面对新国际竞争格局、新一代客户群需求、国内新一代劳动力择业观和行业长期特有的强周期性挑战,过去的跟随式发展已然不能满足新发展需要。
近年来,中央经济工作会议等着重强调:“着力推动高质量发展,打造一批有国际竞争力的先进制造业集群,提升产业基础能力和产业链现代化水平”。然而与大批量离散生产模式的汽车、家电和电子等成熟制造体系不同,工程机械属于多品种小批量离散生产模式,产品复杂程度不弱于汽车,但产品差异化远胜于上述行业,导致工程机械等重型装备行业制造水平明显落后大批量离散制造业先进水平。借助我国制造业高质量发展转型政策的东风,与工业互联网、人工智能和自主工业机器人等新兴技术的新动能,我国工程机械行业以智能制造灯塔工厂建设为优先切入点实现了针对以上问题的原创式探索。本文以工程机械首批启动高质量发展转型升级的灯塔工厂为例进行分析论述。
灯塔工厂方案
2.1需求分析
该工厂是典型的多品种小批量离散型制造模式,集聚了重型装备制造业多种典型特征,如工厂订单淡旺季两极分化、产品型号多(> 200 种)、客制化高(约30%)且尺寸跨度极大(25 ~ 86 m)、结构差异明显(底盘:2 ~ 5 桥、燃油 / 电动)和产品及工件总体超重超大等。尽管该工厂产品已经取得全球领先,但上述特征带来的生产计划调度困难、工艺复杂、体力劳动强度大、安全隐患较大、耗能较高和招工难等问题成为企业保持竞争力与更进一步的阻碍。此外,随着我国互联网经济的发展与人们生活水平的提升,新一代劳动力对高体力劳动强度、重复枯燥作业和脏乱工作环境的容忍度已降低到危及传统制造业长期稳定生产的程度。新一代客户群对产品的智能化、多功能化和节能化等也有着更高的要求,产品复杂度、多样化程度提升也为生产效率与质量保障带来更多的挑战。让机器与数字应用代替或减轻新一代劳动力不乐意、不擅长的工作成为一种两全其美的方案,此举既提升了工厂生产效率与质量,也提升了劳动力工作舒适性与安全性。所以传统工厂转型方向是具备足够自动化、柔性化、数字化、智能化和绿色化的智能工厂。作为工程机械龙头与产业链链主企业,有责任率先探索建设具备行业标杆意义的智能制造灯塔工厂。
2.2总体方案
该灯塔工厂建设需在现有正常运营的工厂上进行改造升级。与全新规划、建设新工厂不同,在正在运营的工厂上改造升级需要兼顾生产保供与改造进度,相对更复杂但也更具备研究价值。因为在工厂全生命周期中,新建只有一次,改造才是常态,而且相比推倒重建的方式,改造能够保留大部分旧有设备设施,投资更小、成本更低、周期更短。对大部分传统工厂来说,在兼顾工厂正常保供交付的情况下,改造更是最经济、最理想的高质量发展转型升级方案。该灯塔工厂建设主要从新兴智能制造装备、技术研究与应用,工业互联网集成平台升级两个方向展开。
(1)新兴智能制造装备、技术研究与应用1)中厚钢板下料成型工艺段。主要包括引进高速自动精细等离子切割机、大吨位智能高速天车,以及自动分拣、清渣、抛光和校平机器人等自动化设备,升级改造零件智能识别、自动套料、自动折弯和开坡口、全规格多形零件自动装框码放、台套智能集配,以及切割烟尘净化等智能控制系统。
2)结构件焊接机加工艺段。针对构成产品主体结构的核心部件,完成焊接自动化升级,主要包括引进自动化焊接机器人、柔性变位机、智能吊具和夹具等自动化设备,升级改造大尺寸和高重量部件自动化组对、柔性工装、智能围栏和智能除烟等智能控制系统。
3)结构件涂装工艺段。针对多种结构件混线喷涂,进行全自动化改造,主要包括引进自动抛丸、底漆和面漆喷涂机器人、自动化输送链等自动化设备,升级改造在线脱脂、自动调漆、自动喷淋和烘干、自动喷涂、智能检测和废气余温循环利用等智能控制系统建设。
4)精密零件机加热处理工艺段。针对液压系统精密金属零件与大型机械结构活动连接件,开展机加工作中心的柔性和智能化的升级,形成无人化的黑灯作业工作岛,主要包括引入全自动化上下料、在线检测、去毛刺、码垛和包装等机器人,升级改造热处理智能调质、刀具自动化检测、自动打磨和去毛刺等智能控制系统。
5)部装总装调试工艺段。针对主流数十款 ABC 多系列装配,开展自动化升级,主要包括引进装配机器人、自动拧紧机、智能平衡吊和压装专机等自动化设备,升级改造智能加注、智能拧紧、自动化检测和清洗等智能控制系统,通过调试现场实时监控和大数据分析,推进全自动智能调试。
6)仓储分拣与物流配送区域。主要包括大吨位长尺寸自动化立库构建(单件物料重达 5 t,长度达 9 m)、多类型全规格立库改造,重载(5 t)AGV 联合研发,以及全厂多类型、多通道、全过程的 AGV 无人化配送和自动化调度。
(2)基于工业互联网的集成平台升级改造以智能制造和网络协同制造为主线,重点打造 IoT 智能互联系统、MOM 协同制造运营系统、WMS 仓储配送管理系统,并实现与 PLM、CRM、ERP、GSP、BPM 流 程 总 线、PO集成总线、MDM 数据总线和 DIP 产业链集成下料平台等基础平台的全面集成应用,打造可靠、全面和可行的一体化运营与管控平台,工业互联网集成平台架构如图1所示。
1)IoT 系统:基于树根互联自主 IoT 平台,完成设备、人员、物料和 6S 等多源结构化和非结构化数据互联互通,建立生产大数据管理和分析中心,实现数据 100% 在线、能源智能监控和管理。
2)MOM 系统:主要包括数字化工艺建模和自动化执行、智能化生产执行管理、高级计划排产和预测及数字化生产运营等模块,实现制造全过程 100% 在线、实时、动态和智能管控。
3)WMS:主要包括仓储全流程数字化管理、配送全过程智能化管管控、无人化理货和智能化盘点等,实现仓储和配送全过程 100%,提升配送及时率和仓储到货率,消灭仓储“盲点”。
典型场景成效
该灯塔工厂融合应用了智造大脑 MOM 系统、数字孪生、机器视觉、AGV无人配送、AI 机器人群、智能水电油气表、IoT 及 5G 等智能化技术和算法,累计智能化升级改造投资 5 亿元。实现了生产周期缩短 59%、人均产值提升 83%、单台制造成本降低 29%,并总结形成了系列模块化场景解决方案,成功推广至集团内 45 家智能工厂。重点场景如下:
1)“智造大脑”集成调度。整合升级MOM、APS、AS、QIS、WMS、PCS、IoT 和 DIP 等系统,构建工厂“智造大脑”,如图 2 所示,实现从生产计划到成品入库全过程的数字化管控。打通销售计划、生产计划及采购计划,应用寻优、遗传、追溯和动态规划等算法,实现主机和结构件计划协同制定、生产智能排程,跨工厂跨地区钢板切割等产能共享。自主研发派工算法,精准派工到设备和个人,实现机器适配性作业、AGV 自动配送。自主研发钢板套料算法,实现最小余料混合套料排版和共边切割,钢材利用率整体提升 15%。通过数字孪生技术,实现对全场设备、物料和加工动作进行 1∶1的模型构建和数据驱动,推动制造现场高颗粒度的可视化、透明化。总体实现生产周期缩短 59%,订单准时交付率提升 13%。
2)AI 机器群高柔性制造。通过融合机器人、机器视觉和智能算法形成 AI 机器人群,实现 263 种机型全工艺流程混线柔性制造,如图 3 所示。包括超大尺寸超强钢板智能化切割、分拣,多形状多材料多厚度钢板智能化折弯和开坡口,大型复杂钢结构件自动组对和弧焊,喷漆部件身份识别,液压阀块去毛刺、表面粗糙度检测、阀组自动拧紧等。研发重工行业首个深度适配性优化的高精度 3D/2D 工业视觉检测系统,实现 10 m 级大尺寸、2 万种工件、模糊特征材料钢板亚毫米级测量,准确率达99.99%;应用自适应点阵磁吸控制技术实现不同尺寸工件柔性装夹;自主研发基于电弧寻位的自动纠偏算法,攻克重型工件易震动工况下稳定跟踪定位问题,焊缝合格率提升 13%;应用“智造大脑”、视觉和 RFID 等技术实现数控程序自切换,焊接、喷涂、加注和拧紧等加工参数自适应。总体实现人均产值提升 83%,设备作业率提升 40%。同时,在重工行业中小件工件领域首次实现从下料(上海东普)、折弯(埃斯顿)、焊接到库内分拣(大族)、物流配送(海星、国自、嘉腾)全流程国产机械手及 AGV 应用。自主机器人多场景应用如图 4所示。
3)AGV+ 立库驱动无断点重载物流。研发全场无断点的精准高效、绿色集约型重载物流系统,如图 5 所示。应用电动 AGV、大跨距超重载堆垛机实现 8 t 级物料厂内自动运输、出入库;自主研发行业首个基于 5G 的端云协同室外无人叉车,实现料斗等直供物料跨厂房转运;应用 0.1mm 高精定位、智能避障和智能防摇摆天车,实现 10 t 级物料自动上下料;研发贪婪算法,实现立库托盘空间规划和出库序列最优化;研发融合时序协调算法,实现多台桁架机器人多种拣选任务协调作业;通过“智造大脑”智能调度和低时延、高可靠 5G 通信,实现物料台套高效配送。总体实现配送及时率提升 11%,库存周转率提升 51%。
4)设备能耗、健康一体智能运维。如图 6 所示,应用智能传感器、智能仪表及 IoT 系统,实现对全厂所有关键设备运行数据(电机运行电流、核心元件运行温度、执行机构动作次数寿命和轨道震动量等)、能耗(电耗、油耗、气体消耗和水耗)等 44 534 项数据统一平台实时监控。通过故障机理分析、大数据和深度学习等技术,进行机床、风机等设备失效模式判断、预测性维护及运行参数调优,总体实现设备故障停机时间降低 18%;通过末端电能平衡模型、能效分析模型,智能识别异常电路负荷点,优化设备动态运行效率。总体实现万元产值碳排放降低 8%。
结束语
工程机械产品复杂、工艺复杂、工况复杂、数据复杂且周期性强,该灯塔工厂在最难的领域,在没有先例的情况下,用创造性思维打通了核心技术,得到了中国科协、麦肯锡和麻省理工等国内外权威的一致认可。卓越的领导力、“嫉慢如仇”的文化、清晰明确的数字化战略、短而迅速的决策流程、灵活的业务架构、高效的人才引进及批量培养机制、高质量的大数据和快速迭代的数据分析模型等共同支撑了方案快速落地。
虽然该工厂取得了一定的成绩,但是建设过程中不乏发现方案缺陷及时调整的案例,而不是将错就错降低预期目标。此外,随着灯塔工厂全面投入使用,可以发现智能化程度越高,其容错能力越弱,问题排查越困难,维持高可靠性的挑战越大。所以灯塔工厂不是一次性工程,其完善空间依然很大,需要长期持续迭代。
该灯塔工厂建成后又衍生了许多新的待解决事项,但不影响其作为全球首家探索重工行业灯塔工厂建设给行业带来的启发意义。其自主创新向业界及国内制造业证明了中国制造从“跟随发展”向“先发创新”转变,做到“以我为主”是可行的。有利于提升中国制造从业者开拓创新的自信与攻坚克难的勇气,鼓舞国内制造业全面自主创新,推动制造大国向制造强国快速转变。
-
制造业
+关注
关注
9文章
2235浏览量
53583 -
智能传感器
+关注
关注
16文章
596浏览量
55303
原文标题:主题策划 | 工程机械灯塔工厂建设探索
文章出处:【微信号:CADCAM_beijing,微信公众号:智能制造IMS】欢迎添加关注!文章转载请注明出处。
发布评论请先 登录
相关推荐
工程机械的故障分析与排除
2010沙特建筑工程机械,建筑机械及建筑设备展
2012年巴西工程机械展
2016年中国工程机械行业发展趋势:后市场建设潜力大
逐步拓展数字化接入与服务 工程机械企业的工业互联网之路
ZWS-CAN智慧云如何赋能工程机械?
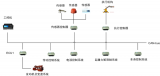
PTC工程机械行业成功案例
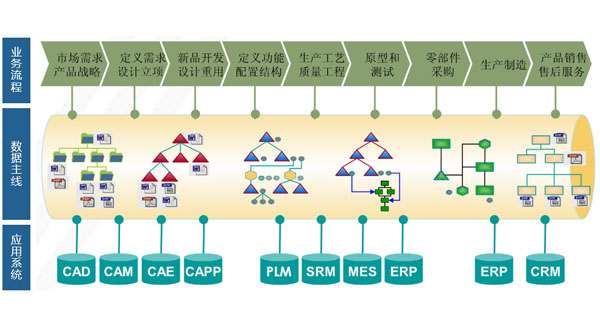
工程机械远程监控解决方案
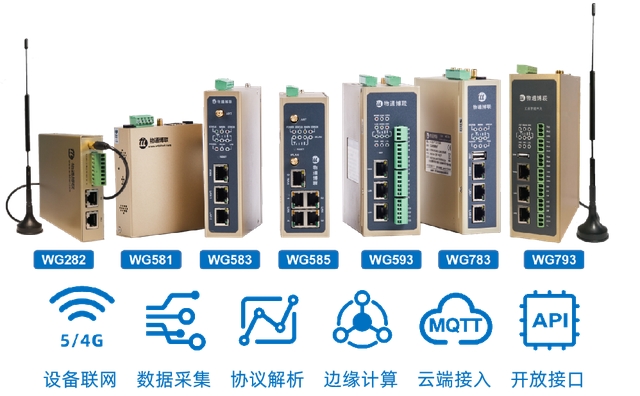
工程机械远程租赁运营解决方案
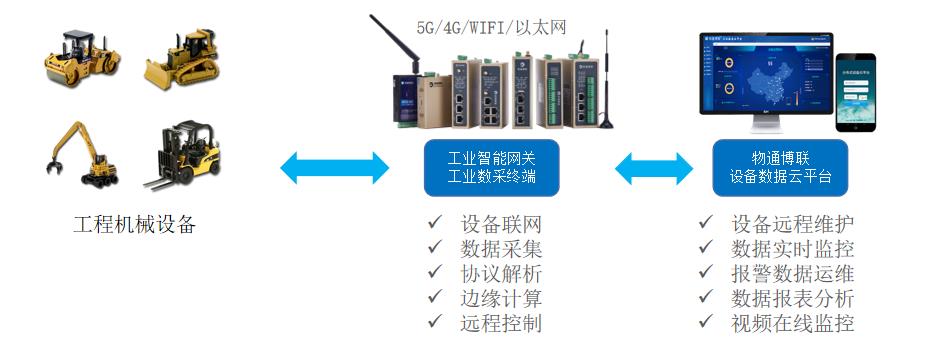
评论