压力与温度
和在刻蚀工艺中一样,半导体制造商在沉积过程中也会通过控制温度、压力等不同条件来把控膜层沉积的质量。例如,降低压强,沉积速率就会放慢,但可以提高垂直方向的沉积质量。因为,压强低表明设备内反应气体粒子的数量少,粒子之间发生冲撞的概率就少,不会妨碍粒子的直线运动。施加高温则可以提高膜层的纯度。当然,这样一来就无法使用铝(其熔点为550度)等熔点低的金属材料。
▲ 图7:压强对沉积工艺的影响
因此,在不同需求下,沉积相同材料也可采用完全不同的沉积方式。例如,同样是沉积二氧化硅(SiO2),栅极绝缘层与STI所需特性就不同,其沉积的方式也不同。栅极绝缘层是核心元件区域,要求较高的沉积质量,应采用高温低压的方式;STI则不然,它只要起到两个元件间的绝缘作用即可,通过低温高压的方式加快沉积速率才是关键。
材料选择上的难题
您或许常会在新闻中看到这样的报道:“发现了性能高出XX倍的新材料”。只看新闻内容,会感觉一场翻天覆地的半导体革命似乎即将来临。但在所谓的“新材料”中,真的能派上用场的却寥寥无几。因为,材料本身的特性好,并不代表它一定能制成高性能的半导体。对沉积材料的要求可不比沉积设备低。下面,我们来看一看材料的特性会对半导体制程产生什么样的影响。
▲ 图8:加热导致图形损坏
物体遇热体积会变大,这种现象被称作热膨胀。铁轨之间留有缝隙就是为了防止铁轨在炎热的夏天因膨胀变形。半导体制程中也会出现这种热膨胀现象。问题在于,每一种材料的热膨胀程度不同,例如铝的热膨胀系数是氧化硅的40倍之多。举个比较极端的例子:如果在氧化硅上沉积了铝薄膜,即便铝薄膜沉积很成功,一旦进入后续的高温工艺,其内部结构就会完全被破损。换句话说,如果采用膨胀系数完全不同的材料替代之前的沉积材料,会严重影响高温条件下的产品良率。
▲ 图9:电迁移现象
除此之外,还要考虑材料的电迁移(EM,Electromigration)现象。电迁移是指在金属布线上施加电流时,移动的电荷撞击金属原子,使其发生迁移的现象。铝等轻金属很容易发生这种电迁移现象。为防止铝的电迁移现象,半导体制造商们开始用铜布线替代铝,结果是又多了一道防止铜扩散的阻挡层沉积工艺。随着半导体不断微细化发展,铜布线也开始出现电迁移现象。为攻克这一难关,英特尔又用钴布线取代了铜。而既然核心金属布线层的材料发生了变化,上下层的工艺也肯定要跟着变。可见,想解决材料的电迁移现象,前后方的工艺也要随之发生很大变化。
要始终铭记:半导体制程是数百个工艺错综复杂紧密连接而成的,牵一发而动全身。新材料是好是坏,不能单看材料本身的特性,还要看能不能与前后方工艺相连,毕竟沉积材料不能独立存在。
结论:一种材料,多种方法
读到这儿,估计读者们已经发现了几点有趣之处了:首先,同样的材料可以通过不同的方法制成。例如,二氧化硅(SiO2)可以通过氧化工艺,也可以通过沉积工艺形成。即便是相同的材料,如果通过不同工艺涂敷到半导体上,其物理特性也会截然不同。
其次,氧化、刻蚀、沉积等看似完全不同的工艺其实有很多共同之处。比如,物理刻蚀中采用的溅射方法,在沉积工艺中同样也会使用,区别在于“是溅射要刻蚀的晶圆本身”,还是“把溅射出来的粒子沉积到晶圆上”。化学刻蚀中最重要的一点就是刻蚀气体与反应源生成的废气是否易于排放,化学气相沉积也同样如此。CVD过程中生成的副产物也要易于挥发、易于排放,这样后续工艺才会变得更容易。
可见,受半导体制造商青睐的新材料,并不是其本身特性有多优秀的材料,而是其沉积速率、纯度等特性易于控制的材料。而且,沉积材料还要易于通过刻蚀或CMP7等工艺去除。如果采用需要过高温度的材料,可能会因高温改变已沉积的其他材料。而若采用对温度非常敏感的材料,又会出现在下一道工艺中无法加热的问题。
化学机械抛光(CMP,Chemical Mechanical Polishing):通过物理、化学反应研磨, 去除非所需物质,使半导体晶圆表面变得平坦。
如上文所述,“半导体制程由数百个制造工艺紧密连接而成”。想做好每一道工艺,对其他相关部门的业务也要有很好的把握。要擅于与同事沟通,更要懂得准确无误地传达自己的想法。一个半导体产品需要多人合作才可以完成,虽然过程有些辛苦,但也很值得。(回顾上一期)
审核编辑:汤梓红
-
半导体
+关注
关注
334文章
27250浏览量
217917 -
制造工艺
+关注
关注
2文章
179浏览量
19751 -
刻蚀工艺
+关注
关注
2文章
37浏览量
8414
原文标题:半导体前端工艺:沉积——“更小、更多”,微细化的关键(下)
文章出处:【微信号:闪德半导体,微信公众号:闪德半导体】欢迎添加关注!文章转载请注明出处。
发布评论请先 登录
相关推荐
半导体前端工艺之刻蚀工艺
半导体工艺讲座
《炬丰科技-半导体工艺》IC制造工艺
半导体设备行业跟踪报告:ALD技术进行薄膜沉积工艺优势
半导体前端工艺:沉积——“更小、更多”,微细化的关键(上)
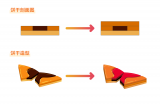
半导体前端工艺之沉积工艺
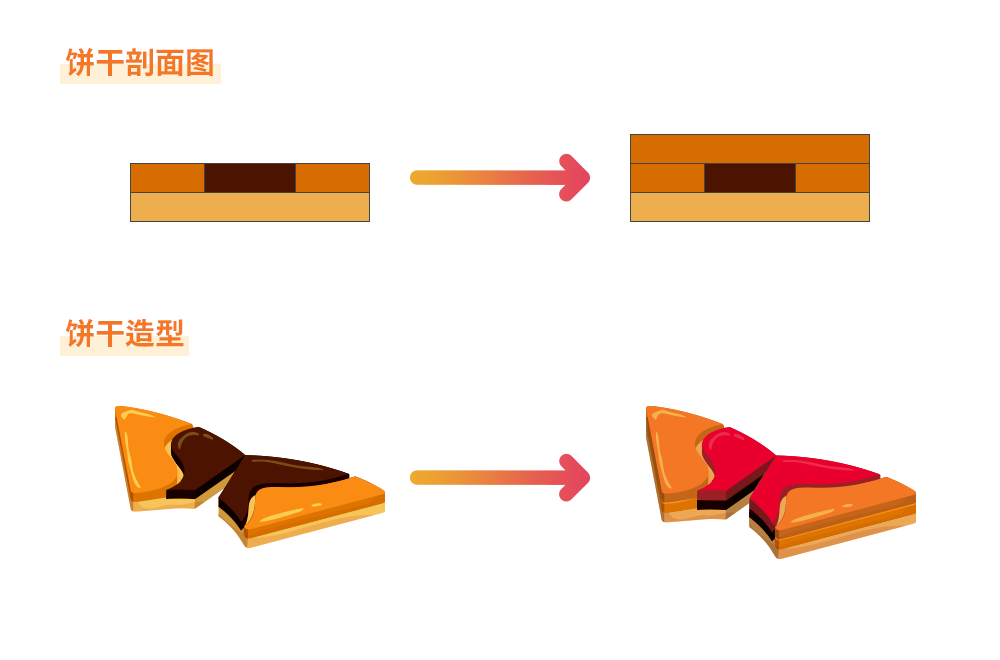
一文详解半导体薄膜沉积工艺
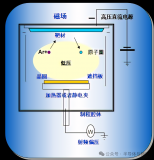
评论