来源:电子与封装
摘 要
随着异构集成模块功能和特征尺寸的不断增加,三维集成技术应运而生。凸点之间的互连 是实现芯片三维叠层的关键,制备出高可靠性的微凸点对微电子封装技术的进一步发展具有重要意 义。整理归纳了先进封装中的凸点技术,包括凸点的制备方法与材料、微观组织与力学性能、电性 能与可靠性、仿真在凸点中的应用,为后续凸点研究提供参考。最后,对凸点技术进行了展望,凸 点工艺将继续向着微型化、小节距、无铅化和高可靠性方向发展。
1 引言
近年来,随着半导体技术的迅速发展,工艺制程 的节点已逐步接近原子尺寸级别,先进封装逐渐成为 延续摩尔定律的主要方式。从行业发展趋势看,封装 正在向着小型化、轻质量、更多I/O数、高性能、高速 度、高频率、高集成化的方向发展。倒装(FC)焊接技 术应运而生,在某些高要求应用中逐渐取代传统的引 线键合技术,以减小封装体积,提升封装密度,缩短互连长度,从而减小寄生电容,提升传输速度。
倒装焊接技术作为一种先进封装技术,其发展离不开焊点技 术的革新。倒装焊接技术的精度要求进一步提升了凸点(尤 其是微型凸点)制备的复杂性。微小的凸点间距和高 度增加了填充工艺的难度。同时,多应力作用下的凸 点极易产生诸如界面空洞、金属间化合物(IMC)扩展 等缺陷,加速芯片失效的过程。因此,在后摩尔时 代,针对凸点小型化、材料选择、可靠性等问题,需要建 立合理的评判机制。本文主要介绍先进封装中凸点 技术的研究进展,并结合应用端,展望凸点技术的发 展趋势。
2凸点的制备方法与材料
凸点按照制备方法可以分为蒸发沉积、丝网印 刷、植球、电镀、喷射、化镀等。
凸点最早使用的制备方法为蒸发沉积法,由IBM公司研发并用于芯片FC键合,并随着可控坍塌芯 片连接(C4)技术而流行起来。该凸点材质最初选用 铜,后逐步转变为锡铅焊料凸点,被IBM及其他公司 持续使用了几十年,并一直保持高可靠性记录。倒装 焊料凸点和铜柱凸点的结构如图1所示。由于铅及其 化合物均有很大毒性,对人体健康和环境有不良影 响,我国出台了《电子信息产品污染控制管理办法》以 限制铅及含铅物质的使用。由于成本以及良率、节距 的问题,8英寸晶圆是蒸发沉积技术的终点。
丝网印刷技术由印制电路板产业引进到晶圆级 封装技术中,采用丝网印刷法制备凸点的优点是工 艺简单、操作方便、成本低,缺点是用此种方法制备的 凸点节距较大,无法制备较小节距凸点是因为回流前 后焊膏的体积变化很大,需要足够大的空间。
采用电镀法制备凸点,具有工艺简单、易于量产、 一致性好、线宽/线距小等优点,其被广泛应用于半导体封装领域。该方法的缺点是工序相对复杂,改变 焊料合金的成分相对较难,需要通过对电镀液中各组 成成分的含量进行控制,且在凸点存在状态下进行种子层刻蚀。
焊料喷射是连续的无掩模焊料沉积技术,用喷头 将液态焊料喷射至晶圆上。此技术可以实现较高的喷 射频率,但对整个工艺的控制较为困难。
由于不需要采用光刻和溅射等工序,化镀工艺的 成本较低,可以直接对露出铝焊盘的晶圆进行湿法处 理,从而吸引了研究者的关注。德国的IZM工艺是先 对晶圆背面掩模,然后进行正面钝化层的清洗,通过 铝焊盘的活化、浸锌、化镍、浸金、清洗等制备出磷镍凸 点,其厚度为5μm,表面防氧化层金的厚度为50~ 80 nm。不同凸点制备方法如表1所示。
中国电子科技集团公司第二十四研究所采用德国电镀技术有限公司的MOT机台和某进口电镀 液 , 电 镀 制 备 出 以Cu为 凸 块 下 金 属 (UBM)的Sn3.5Ag二元合金焊料凸点,如图2所示。通过对阳极 板位置的调节、药液中Sn离子和Ag离子浓度比值的 调节、电镀液的定期监控等措施将凸点的成分控制在Sn、Ag的质量比为96.5∶3.5。
YU等的研究将 Sn/Ag/Cu 三元无铅焊料作为含 铅焊料的潜在替代品,并对 Sn/2.5Ag/0.7Cu、Sn/3.5Ag/ 0.7Cu、Sn/3.5Ag/0.7Cu/0.1RE 和 Sn/3.5Ag/0.7Cu/0.25RE 的微观结构和力学性能进行了研究。当 Sn/2.5Ag/ 0.7Cu 和 Sn/3.5Ag/0.7Cu 中形成粗大的 β-Sn 晶粒时, Sn/3.5Ag/0.7Cu 合金中出现块状的 Ag、Sn。通过掺杂 微量稀土元素 Ce 使得粗大的 Cu6Sn5 和 Ag3Sn 晶粒得 以细化,这主要是由于稀土元素 Ce 起到了钉扎作用, 抑制了晶粒的生长。由于显微组织精细均匀,提高了 拉伸强度和伸长率,稀土元素的加入可以作为开发新 型无铅焊料的有效途径。
WEI等介绍了铜柱凸点技术的进展,对比了铜 柱焊料凸点(CPB)和C4凸点的性能,列举了各大厂 的代表铜柱凸点,介绍了铜柱凸点的制造工艺、应用 场景、可靠性、倒装问题和可以生产的封装厂,以及未 来的发展趋势。微互连的铜柱凸点如图3所示。CPB工艺以其更小的凸点节距(<50μm),更优良的电学 性能、热学性能和机械性能,能够满足未来高I/O密 度、优良电热性能的封装需求。
吕镖等研究了阴极移动对在不同电流密度下制 备的镍层表面形貌、粗糙度、孔隙率、组织结构以及纤 维硬度等性能的影响。研究发现,当电流密度较大时, 阴极移动可以改善浓度极化导致的镀层质量劣化,降 低孔隙率和残余应力,但对晶向没有影响。
相较于其他凸点制备方法,电镀法具有易于批量 生产、一致性好,以及可以制备绝大部分凸点等优点, 因此被广泛应用于集成电路的封装领域。研究者们也 会针对凸点材料将常用凸点分为含铅凸点及无铅凸 点。由于铅的毒性,无铅电子组装已成为不可扭转的 趋势。目前已经明确用来取代Sn/Pb合金的无铅焊料 是以Sn为基体的二元、三元甚至更多元的合金焊料。
3微观组织与力学性能
凸点的成分、结构及其形成的微观组织决定了其 力学性能,国内外学者进行了大量的相关研究,以期 构建凸点的微观组织与力学性能之间的联系,从而获 得符合使用要求的凸点结构,并取得了大量的成果。
李福泉等采用熔融法熔滴SnPb焊料,其在CuNiAu焊盘上所形成的组织为Au/Sn IMC,Au/Sn凸 点的整体形貌如图4所示。随后的再回流过程中,Au/Sn IMC迁移至焊料基体内部,裸露出的Ni层与Sn生成Ni3Sn4。随着老化过程的进行,AuSn4重新沉积 于界面,并形成(AuxNi1-x)Sn4,在该层之上有富铅相产 生。Au/Sn IMC的反应及其分布对焊料与焊盘间的力 学性能影响很大。
通过熔融共晶SnPb和热退火Ni的反应润湿,在Ni上形成Ni3Sn4晶粒,并使用同步X射线衍射分析发现Ni3Sn4和Ni之间存在2种择优取向关系。
凸点的成分也会对界面反应的动力学过程造成影 响。LAURILA等研究了SnPbAg、SnAg和SnAgCu凸点焊料与印制板上Ni/Au表面进行光刻的界面反 应,特别是AuSn IMC的再沉积,发现SnPbAg/Ni/Au和SnAg/Ni/Au体系在焊接过程中形成的第一相为Ni3Sn4。在随后的固相退火过程中,2个体系都出现了AuSn4、(Au, Ni)Sn4相的再沉淀,可用局部平衡的概念 和相应的三元相图解释这一现象。结果表明,Ni可以 驱动(Au, Ni)Sn4发生再沉淀。当焊料中含有一定的Cu时,首先形成的IMC为(Cu, Ni, Au)6Sn5,未发现AuSn4的再沉积,在富Sn焊料体系中加入少量Cu就 完全改变了互连系统的行为。
LABIE等研究报道了倒装芯片尺寸凸点的Cu/Sn和Ni/Sn固态扩散,在直径为40μm的键合垫 倒装凸点上测量了Cu/Sn和Ni/Sn的IMC互扩散系 数和活化能,描述了金属反应的形貌。在Ni/Sn体系 中,少量的Cu对Ni的消耗有一定影响,而大量的Cu则会导致金属间界面的极端扇贝化。
回流焊的条件会改变凸点的微观形貌,从而影响 其可靠性。林小芹等用电镀法制备了以Cu为UBM的尺寸小于100μm的Sn3Ag凸点,图5为Sn3Ag凸 点的SEM照片。芯片内凸点高度的一致性为1.4%,4英寸片间的凸点高度一致性约为3.57%;研究了Cu焊 盘与焊料SnAg在不同回流次数下界面反应及孔洞形 成的机理,预测了对凸点连接可靠性的影响。研究结 果表明,焊料与Cu6Sn5界面中孔洞的产生主要是相变 体积收缩所致。凸点的剪切强度随着回流次数的增多 而增大,Cu6Sn5/Cu界面随服役而不断产生的孔洞对凸 点的长期可靠性会产生不利影响。
GORLICH等研究了固态Ni和液态Sn之间的 焊接。研究发现,只有在工艺的早期阶段,IMC晶粒的 生长随时间呈线性变化。之后,IMC晶粒的生长速度 逐渐下降。值得注意的是出现了速率常数不同的2个体系。用最新的助焊剂驱动理论讨论了所观察到 的生长速度变化,但是这个理论仅针对4 min内的 短回流过程有效。使用透射电镜观察到扇贝状微结 构,在Ni/Ni3Sn4界面新晶粒永久成核,海绵状等轴 晶粒随后形成。晶界润湿只出现在反应区的一定范围内。
凸点的微观形貌也会影响其剪切强度。TIAN等对含有限晶粒数的回流失效凸点进行了动态剪切测 试,研究了SAC305/Cu凸点的变形和断裂行为。使用 偏振光显微镜(PLM)和电子束背散射(EBSD)技术分 析了晶粒的形貌和分布,利用SEM观察了凸点组织 和IMC对凸点断裂行为的影响,焊锡接点和IMC微 结构如图6所示。实验结果表明,在Sn3.0Ag0.5Cu焊 料中,IMC(Cu6Sn5和Ag3Sn)的形貌和分布是导致焊 料尺寸效应的主要原因。随着凸点尺寸的增大,回流 和失效焊接头的剪切强度降低。分散在小凸点中的纳 米颗粒状Ag3Sn对凸点的力学性能有强化作用。树枝 状和羽毛状的Ag3Sn使大尺寸的凸点变脆。在动态剪 切测试中,小凸点出现了明显的塑性变形,并发生了 动态回复和再结晶。断裂发生在大部分焊料中,而脆 性断裂发生在大凸点中,断裂位置靠近焊料表面。裂 纹以穿晶断裂的方式扩展。老化后,所有的凸点均发 生动态回复和再结晶。大凸点的塑性增强,在动态测 试过程中发生穿晶断裂和沿晶断裂。
CHUANG等对Ni和Sn反应的空洞消除进行 了研究,以揭示空间限制对Ni/Sn和Ni/SnAg反应的 影响。结果表明,空间限制导致Ni/Sn/Ni夹层中心附 近形成了空洞,其根本原因是反应产生的体积收缩不 能通过夹层垂直厚度的减小而完全消散。在Ni3Sn4相 反方向生长的晶粒互相撞击,有效地阻止了夹层垂直厚度的减小。第一次增加质量分数为2.4 %的Ag时有 效地消除了这些空洞,说明加入Ag可以显著地抑制Ni/Sn空洞的产生,有人认为这是Ag原子的析出扩散 造成的。
CHUANG等提出了在三维集成电路封装中由 空间引起界面反应的几个关键问题。包括IMC晶粒的 碰撞产生结构缺陷,焊料浓度消耗导致杂质浓度上 升,焊料尺寸变小导致薄膜层对UBM和表面光洁度 的影响越来越大等,并讨论了这些问题的含义和解决方案。
凸点的尺寸也会改变IMC的生长情况。HUANG等 报道了在Ni/SnAg/Cu焊料微凸点中的新发现,IMC的生长速率在很大程度上取决于焊料厚度。在Ni/SnAg(厚度为40μm)/Cu结构中,化合物在Ni侧 的生长速度比在Cu侧快。由于焊料中Cu和Ni浓度 的梯度变化,当焊料厚度小于20μm时,IMC的生长情况相反。
LIANG等研究了焊料厚度分别为4μm和12μm时,Ni/Sn2.3Ag/Ni微凸点的三明治结构在260℃下经 回流后的微结构演变。当焊料厚度为4μm的微凸点 经过1次4 min的回流处理后,Ni在UBM界面处形 成了IMC,成分为Ni3Sn4,形成的Ag3Sn IMC分散在焊 料基体中。当回流时间接近34 min时,Ni3Sn4 IMC几 乎占据了整个界面,此时在IMC中仍有些孔洞。相比 之下,在焊料厚度为12μm的微凸点中Ni3Sn4 IMC的 生长速率要慢于焊料厚度为4μm的微凸点。
陈雷达等研究发现,由于IMC的热膨胀系数、 弹性模量、断裂伸长率等材料参数与基体金属差异很 大,所以IMC越厚就越容易产生龟裂,导致凸点失效。在使用过程中由于扩散导致的柯肯达尔孔洞也会成 为裂纹的源头。因此,IMC的形貌、厚度和结构都会影 响凸点的可靠性。微型化导致的尺寸效应对可靠性产 生了越来越重要的影响。
YU等研究了高度小于10μm时Ni/SnAg/Ni微 凸点中的Ag含量对减少孔洞的影响,系统地研究了Ag的质量分数低于8%时的最佳值。结果表明,在固 态反应中,当Ag的质量分数低于2.4 %时有孔洞产 生;当Ag的质量分数不低于3.5 %时,几乎没有孔洞 产生,且在键合条件下析出Ag3Sn。当Ag的质量分数 达到8%时,形成了部分连续的Ag3Sn层。
YANG等研究了Cu/Ni/SnAg微凸点中Sn的表 面扩散对IMC生长的影响,发现随着凸点尺寸的降 低,表面扩散变得更加重要。该团队采用透射电镜 (TEM)观察了侧面的Ni3Sn(靠近4 Ni3Sn4/Ni界面)、侧 壁Ni3Sn(在2 Ni阻挡层表面)和侧面Cu3Sn(在铜柱表 面)对Sn原子扩散的影响;计算出了Ni3Sn4横向生长 常数约为0.025 7μm/h1/2。基于以上实验结果和扩散理 论,提出了微凸点中IMC的形成机理,在高密度电子 封装中,表面扩散引起的额外IMC生长可能是引起失 效风险的潜在因素。
CAI等通过Sn层间的厚度优化、界面IMC的 生长演化和凸点尺寸效应这3个重要实验研究Cu/Sn固态键合。通过对电镀Sn表面粗糙度和预制Cu6Sn5晶粒峰的分析,确定Sn中间层的最小厚度为2μm。在 键合前,只有一个不稳定的Cu6Sn5相在室温下形成, 该相的成核是一个不稳定过程。在富Cu的Cu/Sn/Cu三明治结构的键合和退火过程中,Sn中间层经历了还 原、分裂和衰竭,相应的Cu6Sn5相发生了生长、合并和 转变,最终形成了一个稳定的Cu/Cu3Sn/Cu的3层结 构。柯肯达尔孔洞出现在Cu/Cu3Sn界面处,且随着Cu6Sn5相的减少而不断生成。在200℃的低温条件下,Cu/Sn键合中IMC的生长机制仍为晶格扩散。当Sn存在时,Cu6Sn5相的产生抑制了Cu3Sn的生长,且得到了2个略大的互扩散系数D(Cu6Sn5)=3.035×10-17m2/s,D(Cu3Sn)=7.496×10-17m2/s。随着凸点宽度的不断降低, 尤其是降低至60μm以下时,IMC侧向生长引起的凸 点尺寸效应逐渐明显,并对细节距Cu/Sn/Cu互连有利。
田飞飞等在CuNi焊盘上植共晶Sn63Pb37焊 球,用波峰焊焊接至化学镀NiAu的PCB铜焊盘上, 通过SEM观察了界面的微观组织,采用色谱仪(EDS) 分析其微观组织成分。结果表明,芯片侧从Ni层往PCB方向,IMC依次为(Cu, Ni)3Sn、(Cu, Ni)6Sn5;PCB侧从Ni往芯片方向,IMC依次为NiSnP三元化合物 和(Cu,Ni)6Sn5。由于IMC多为脆性相,容易产生微裂 纹并对凸点的力学性能、可靠性有不利影响。
LIN等人首次在高温、高湿存储条件下观察到 在Cu/Ni/SnAg微凸点表面的浅层晶粒上生长出锡晶 须。氧化反应和IMC反应形成的应力差导致了晶须的 形成。均匀取向的相关孪晶减缓了Sn原子的扩散速 率,浅层表面较大体积的Ag3Sn限制了晶须晶界的迁 移,对晶须和小丘表面形貌有着重要影响。在此基础 上,他们提出了Sn晶须和阶地状小丘的形成机理。该 研究结果对孤立Sn基凸点上的Sn晶须和小丘具有 重大意义,对3D电子封装的可靠性具有指导意义。
目前关于力学性能与微结构的研究主要集中在 较大尺寸的凸点中,针对微型凸点的力学性能研究较少。此外,实际生产过程中的工艺条件以及凸点尺寸 的差异均会显著影响界面IMC,从而导致凸点的力学 性能发生变化。因此,在后续研究中有必要进一步聚 焦微型凸点的微观结构及其力学性能。
4微观组织与电性能及可靠性
凸点的微观组织不仅决定了其力学性能,还会对 电路的电性能及可靠性造成影响。随着电路不断朝着 微型化方向发展,封装结构中的凸点尺寸越来越小, 凸点所经受的电流密度大大提高。电迁移对元素扩散 与界面反应的影响变得越来越重要。因此,在电迁移 作用下凸点中的元素扩散及界面反应已经成为微电 子封装的研究热点。
由于实际倒装凸点结构为非对称结构,在凸点的 电流入口处和出口处容易产生严重的电流拥挤效应 与焦耳热效应,进而使得凸点处的电迁移现象变得十 分复杂。陈雷达在“纯化条件下”研究电迁移对Cu/Sn/Cu、Cu/Sn/Ni凸点中元素扩散及界面反应的影 响,并在此基础上更深一步地研究了电迁移对这2种 凸点的界面反应与失效机理的影响。经研究发现,对 于Cu/Sn/Cu对称结构,在电迁移作用下,凸点界面的IMC生长呈现明显的极性效应。阴极界面处的IMC生 长弱于阳极界面处的IMC生长。电流密度越大、温度 越高,界面IMC的生长速率越大。
对于Cu/Sn/Ni非对称结构,在液/固与固/固条 件下,界面IMC在电迁移过程中的生长均呈现极性效 应,液/固条件下阳极界面的生长速率比液/液条件 下高一个数量级。电子风的方向影响凸点中Cu-Ni的 交互作用,在固/固的电迁移条件下,Cu原子只有在 顺电子风扩散时才能够扩散到对面Sn/Ni界面并改变 界面IMC的类型,在逆电子风时无法扩散到对面Sn/Cu界面,对应的IMC为(Cu, Ni)6Sn5;Ni原子无论 在顺/逆电子风下都无法大量扩散到Sn/Cu界面,在150℃、104A/cm2的条件下,当Ni为阴极时会大量溶 解并与Sn原子生成块状Ni3Sn4。在液/固的电迁移条 件下,原子扩散更快,Cu原子在顺/逆电子风条件下 均能扩散到对面的Sn/Ni界面IMC;Ni原子只有在顺 电子风时可以扩散到对面Sn/Cu界面,逆电子风时并 不 能 扩 散 到 对 面Sn/Cu界 面 , 即 对 应 的IMC为Cu6Sn5。
对于Ni/Sn3Ag0.5Cu/Cu凸点而言,在电迁移作用 下凸点只存在一种失效模式,即当电子由基板(Cu)端 流向芯片(Ni)端时,电流拥挤效应导致基板端的Cu原子在电子入口处出现局部的快速溶解,并导致在阴 极界面处形成裂纹。在150℃、104A/cm2条件下电迁 移1 000 h后,阴极Cu基板基本消耗完,裂纹贯穿整 个阴极界面。在180℃、104A/cm2条件下经过143 h电 迁移后,凸点已经发生失效。当电子由芯片端流向基 板端(芯片端Ni UBM为阴极)时,阴极Ni UBM未发 生明显溶解。无论温度如何,电迁移都没有引起凸点 失效。
研究结果表明,IMC界面的生长动力学符合抛物 线规律,而且电流密度越大、温度越高,界面的生长速 率就越大。然而,目前关于凸点的电迁移研究绝大部 分都集中在固/固电迁移方面。随着凸点尺寸的不断 减小,通过凸点的电流密度越来越大,凸点中的电流 拥挤效应和焦耳热效应更加明显。凸点极易在电迁移 过程中发生熔化现象。因此,进一步研究凸点在液/固 条件下的电迁移行为对理解凸点的失效机理起着至 关重要的作用。
5仿真分析在凸点研究中的应用
随着互连密度越来越高,凸点逐渐向着细节距、微尺寸方向发展,热疲劳可靠性问题的影响越发突 出。为了应对这一问题,诸多学者运用有限元分析 方法、试验设计法(DOE)开展了凸点的热疲劳可靠性 研究,对解决实际工程难题有一定的指导意义。
王健等发明了一种以硅为基板的微波芯片倒装 封装结构,该结构可以解决关键的微波芯片背面接地 问题,并建立了三维有限元模型,在此封装结构中进 行了金凸点的热疲劳可靠性研究。结果表明,关键金 凸点的最大等效总应变分布在硅与凸点的界面处。根 据其他学者的研究结果,选取了凸点高度、直径和共 晶焊料片厚度作为影响凸点热疲劳可靠性的重要因 素,通过3因素3水平9组正交试验对结构设计进行 了优化,得出3个因素的影响程度依次为共晶焊料片 厚度>金凸点直径>金凸点高度,对结构设计具有指 导意义。
王健等还基于Ansys Workbench LS-DYNA软 件,建立了包含钝化层及凸点下金属化结构的热超声 倒装结构三维有限元模型。键合形成的3个阶段中凸 点的运动状态和塑性应变变化如图7所示。根据凸点 的运动状态将键合形成过程进一步细分为3个阶段, 分析了仿真得到的凸点、凸点/焊盘界面及凸点下金属化结构的应力、塑性应变分布及其在键合过程中的 变化规律,指出了热超声倒装芯片键合可靠性的风险点。
凸点界面结合的物理机制是研究倒装芯片键合 工艺的关键。而常规的试验技术手段难以直接测量局 部区域内的动态应力、应变瞬态特性。此外,后摩尔时 代采用的新材料、新结构微互连凸点带来了一系列新 的可靠性问题。为了实现其工程化应用,需要通过合 适的仿真方式建立新的失效模型,探索综合可靠性评 价和设计方法等。因此在后续研究中,凸点仿真的模 块化和精细化是凸点结构设计与工艺开发的关键。
6凸点在先进封装中的应用
凸点是先进封装中重要的要素之一,它的主要作 用是电气互连和应力缓冲。从传统的打线工艺发展到 倒装焊接工艺,凸点起到了至关重要的作用。在当前 比较知名的先进封装技术中,凸点技术都是其中的关 键技术,如台积电的2.5D CoWoS(Chip on Wafer on Substrate)技术和集成式扇出型封装(InFO)技术、英特 尔的嵌入式多芯片互连桥(EMIB)和3D逻辑芯片封 装 技 术 (Foveros)、三星电子的扇出面板级封装 (FOPLP)和混合基板封装(H-Cube)技术等,部分先进 封装形式如图8所示[64]。在过去的10年间,先进封装 技术快速发展,涌现出2D、2.5D、3D、3D+2D、3D+2.5D等多种封装方式,应用领域包括5G、AI、可穿戴设备、 高性能服务器、高性能显卡等。总的来说,先进封装的 目的就是提升功能密度,缩短互联长度,提升系统性 能,降低整体功耗,而其中最为重要的环节之一就是 凸点制备以及互联,因此凸点技术的开发与优化影响 着先进封装技术的发展。
由于工艺技术的发展,凸点尺寸也变得越来越 小,单位面积芯片上的I/O引脚数量不断增加,异构集 成微系统以及凸点制备工艺将继续呈现体积不断微 型化、功能密度不断提高的发展趋势。伴随着凸点互 连技术的不断优化,异构集成微系统产品有望获得突 破,并对集成电路行业产生颠覆性影响。
7 结束语
电子封装的小型化、轻薄化要求倒装芯片的凸点尺寸不断减小,更高密度的微凸点技术正在研发并转向量产应用。但是随着凸点尺寸的减小,体积效应导 致物理、化学的影响更加显著,包括化学反应、金属溶 解、化学势梯度驱动的扩散、电迁移、焦耳热、热迁移和 应力迁移,这些因素对凸点长期可靠性影响的研究将 伴随凸点尺寸的减小同步开展。在材料选择方面,尽 管SnPb凸点由于其具有低成本和高可靠性的优点, 被最早应用于封装互连中,但严格的禁铅条例使封装 行业研究者转向了对无铅凸点的开发与应用,未来的 凸点材料既要满足环保要求,也需要具有优异的可靠性。在制备工艺方面,电镀法由于具备工艺简单、成本 低、易于批量生产等优点,被广泛应用于凸点制备。随着凸点尺寸的进一步缩小和密度的进一步增加,需要开发出更加合适的电镀工艺,从而满足不同的产品要求。
审核编辑:汤梓红
-
芯片
+关注
关注
455文章
50714浏览量
423136 -
半导体
+关注
关注
334文章
27286浏览量
218067 -
封装
+关注
关注
126文章
7873浏览量
142893 -
微电子
+关注
关注
18文章
380浏览量
41196 -
先进封装
+关注
关注
2文章
400浏览量
241
原文标题:先进封装中凸点技术的研究进展
文章出处:【微信号:wc_ysj,微信公众号:旺材芯片】欢迎添加关注!文章转载请注明出处。
发布评论请先 登录
相关推荐
先进封装RDL-first工艺研究进展
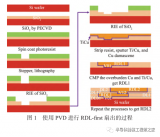
新型铜互连方法—电化学机械抛光技术研究进展
薄膜锂电池的研究进展
传感器EMC的重要性与研究进展
应用声发射评定金属点蚀过程的研究进展
应用声发射评定金属点蚀过程的研究进展
先进封装中铜-铜低温键合技术研究进展
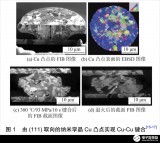
评论