随着数字化技术不断发展与应用,企业数字化转型步伐越走越快,我单位聚焦核心业务的关键痛点难点,在原有数字化建设基础上,以现有厂所数字化协同平台为依托,联合主要外协生产制造厂开展跨地域航天产品多维度一体化控制技术改进与应用实践。选取典型产品为试点产品,以产品研制为主线,打造产品设计制造一体化全流程双向数据贯通,形成产品协同研制多维度数据包,实现设计,以及产品数据的分析、利用和优化,强化研制过程高效监控、预测预警管理,解决厂所数据标准不统一、制造数据在线反馈链路不通、生产及质量数据追溯困难三大问题,从根本上提升产品设计制造过程协同效率,助力企业数字化转型。
引言
高性能运载火箭和航天器具有涉及专业面广、设计更改频繁、对重量要求苛刻、空间十分紧凑、零部件数量巨大、系统布置密集、外形要求严格和内部结构复杂等特点。迫切需要应用数字化研制技术从根本上改变传统的产品研制模式、方法和过程,大幅度提高航天型号产品的研制质量、缩短研制周期和降低成本。近十年来, 航天制造业的数字化发展在跨地域协同创新研发模式、基于模型定义的制造技术、建立基于三维的全过程数字化制造系统、提升制造知识的积累和质量追溯等方向上不断深入,技术应用取得飞速发展。
随着企业业务的快速增长,数字化转型步伐加快,基于MBD 的三维数字化研制模式的逐步推广,当前的系统平台及网络现状已经不能满足型号产品多维度设计制造一体化的控制需求,尤其是生产进度数据及制造过程质量数据一直以来未实现在研究所与制造单位间的贯通与传递。作为典型的跨地域、跨组织型号协同研制单位, 单一维度的设计数据集已不能满足产品在设计制造协同、数据分析等全维度控制要求,亟需通过开展基于产品研制过程数据互联互通和多BOM 集成的产品协同研制过程多维度控制技术研究。在已有厂所协同研制平台的基础上,通过多BOM 管理,将产品设计数据、科研生产管理信息和产品研制过程质量信息三者相关联,形成产品协同研制全维度数据包,打通产品设计制造一体化双向、在线数据链路,实现数据标准统一化、数据交互高效化、生产进度透明化与质量追溯自动化,逐步达到设计所对设计、工艺、生产和质量等产品研制过程的多维度控制, 提升设计单位对产品研制过程数字化的管控能力。
建设目标
以产品研制为主线,打造产品设计制造一体化全流程双向数据贯通,形成产品协同研制多维度数据包,实现设计,以及产品数据的分析、利用和优化,强化研制过程高效监控、预测预警管理,以外协产品生产计划与产品质量管控为主线,通过扩展现有厂所数字化协同平台功能,聚焦厂所数据标准不统一、制造数据在线反馈链路不通、生产及质量数据追溯困难3大难题,打造外协产品设计制造一体化双向数据贯通,形成产品协同研制多维度数据包并实现以下目标:①实现产品外协计划基于系统的结构化制定与管理;②支持编制外协生产任务的序时要求,能够进行序时进度监控与预警;③实现对外协生产过程的进度监测与外协产品数据的可视化图表展示;④基于系统管理外协产品验收数据包相关的产品文档及产品实物数据;⑤实现标准、统一的协同数据包方式进行数据填报与自动解析;⑥形成异地厂所间外协数据双向传输,构建基于相应机制传输的交互机制。总体方案如图1所示。
图1 总体方案
技术路径
按照“网络化、虚拟化、集成化、智能化”的数字化发展方向,以统一的数据标准规范为基础,以开放的、面向服务的厂所协同研制平台为体系架构,在已有厂所协同平台项目管理、图文档管理、BOM 管理、变更管理和数据发放管理的基础上,利用平台的可扩展性、丰富的可配置性,通过跨地域、跨组织及多专业设计、工艺、制造协同技术,基于BOM 的全流程双向数据贯通与应用技术,基于BOM 的质量数据包关联技术,基于BOM 的产品生产进度监测分析技术,产品实测数据与设计数据的关联分析与优化技术等关键技术,开展功能开发,构建跨地域航天产品多维度一体化协同研制系统,实现基于BOM 的设计与制造数据双向精确交互、质量数据及生产进度数据的在线管理与分析应用。
对现有外协生产关键典型业务流程进行调研、梳理, 形成产品外协生产的典型流程,基于典型流程明确建设及功能需求,通过综合分析后,形成相应的业务范围及业务蓝图,并明确涉及所有相关系统的集成与数据流向关系,以支撑系统建设与项目目标实现。系统间数据流向及关系如图2所示。
图2 系统间数据流向及关系
建设内容
形成的产品生产协同业务流程,设计制造与项目管理融合,对涉及的设计部门、项目管理部门、质量管理部门及外协生产厂商在产品外协、外协生产、产品验收及产品交付等过程中的具体业务流程进行了明确与优化, 并形成项目整体架构设计,如图3所示。
图3 系统整体架构设计图
根据业务分析及系统建设功能架构,项目建设实现了以下内容,支撑业务流程运转,实现厂所异地协同研制。
1)形成设计制造协同业务标准规范。通过对设计与制造单位的产品设计、制造数据进行规范化与标准化, 包括统一产品数据编码、统一数据组织形式和统一数据交互标准等,开展系统集成接口开发,实现协同数据标准规范在应用中实施落地,为跨域及多专业协同产品研制提供数据交互基础,保障产品数据在设计与制造单位交互时的唯一性与精确性。
2)产品数据跨地域的协同传递。构建基于独立数据包的跨域协同机制,通过数据包传递设计数据、BOM 结构、产品设计文档、生产计划信息和生产过程数据等。在同构环境和异构环境下,采用推式和拉式的数据传递方式,建立数据同步机制,系统对需传递的数据进行传递及导入、导出操作,数据传递过程中使用原始传递格式, 不对数据进行编辑修改,使原始数据由发送端到接收端后进行无差异的存储与展现。协同数据包在系统外传递时加密处理,仅能够在指定的单位站点进行导入、导出操作,不能在未授权的情况下脱机对内容进行浏览。
3)基于BOM 的产品数据管理。车间按照生产订单进行排产,生产时依据制造BOM 的工艺内容进行指导,当每次生产完成后将生产过程信息、检验信息、人员信息与所装的物料实物信息等进行收集打包,完整的传递到协同系统中,系统收到车间实做信息后构建实做BOM,并将其与工艺BOM 进行关联。工艺BOM 与实做BOM 也可通过打包、数据协同回传到设计单位,设计单位管理人员通过设计BOM 节点查询相关的工艺BOM 结构与实做BOM 信息,系统基于产品图代号/ 物料编码等主要信息进行链接,通过列表的形式展示产品的制造过程数据,用于技术状态跟踪与问题追溯,并对数据进行 分析。
4)结构化工艺管理。支持构建产品工艺设计参数库, 在工艺设计过程中调用参数信息到工艺内容,将编制完成的结构化工艺内容输出后用于车间产品制造。
5)产品生产计划及生产进度管理。管理产品生产任务及其序时计划,生成相应的科研生产任务通知单, 并将其传递到制造端作为生产任务输入。产品制造端按照接收到的产品生成计划任务,在日期范围内进行排产,并将每天的生产进度完工情况反馈给设计所,将进度信息与生产计划信息结合体现,能够清晰得知产品当前生产进度情况,对即将出现的问题及时预警并 调整。
6)产品验收过程数据管理。通过在设计所内针对产品进行验收数据包规划,定义产品验收所需的交付物, 将验收数据包模板传递到制造端,制造单位在产品生产过程中及生产完成后上传提交交付物;与所一起按照验收标准进行逐项验收,最终将验收结果统一到产品验收数据包中,回传到设计所内进行查阅与归档。
7)产品实物数据管理。通过与制造端ERP 系统及手工录入的方式获得产品实物信息,包含产品的批次、序列号及现场多媒体照片等。将产品实物在验收后与产品验收数据包进行关联管理。产品实物验收合格后形成的产品实物对象将传递到设计所内,形成产品实做BOM, 通过实做BOM 能够对相关实物及产品设计信息进行追溯关联查询。
成果价值
5.1 项目技术创新点
本项目主要技术创新点如图4 所示。
图4 项目技术创新点
1)形成统一化、规范化的数字化跨域协同标准规范体系,助力产品研制数据源在厂所间的高效传递与精准一致。
2)开拓基于数字孪生的产品质量数据管理与关联应用技术,实现质量数据包的自动生成与关联应用。
3)实践基于实做BOM 的产品生产进度监测技术, 支撑产品生产管控智能化。
4)开展基于实做信息的质量数据追溯与分析技术, 强化质量过程监控,提升质量管控能力。
5.2 项目实施成效
1)外协计划由基于人工的分散管理模式转变为基于数据的统一线上平台协同模式。通过系统在线创建及管理型号外协计划,全部型号计划数据由系统数据库集中管理;对每份计划详细属性、交付数量和交付时间等进行结构化管理;基于结构化数据能够方便的进行全库查询与统计,计算各单位、各节点按时完成率等;基于结构化的管理方式能够进行典型型号计划的总结与克隆重用;基于数据统一管理、统计分析和数据重用等使外协计划综合管理效率预计提升15%。
2)外协质量管控由线下沟通、传真和出差的模式转变为基于数据的流程驱动模式。通过协同数据包实现厂所间的计划和质量交互、生产进度交互和验收数据交互;交互数据内容、交互记录系统可查,数据有关联;同时通过协同数据包作为数据驱动,系统按照预定规则及时通知质量、设计部门进行处理;整体使沟通内容表达、联系通知等导致的工作量预计减少10%。对任务信息进行预警设置,临近任务交付时间时进行报警通知,促进及时进行进度协调,将人工主动跟进度的工作量预计减少15%。
3)产品外协数据由人工收集再汇总模式转变为以交付产品为核心的标准化组织模式。通过在生产单位部署数据包管理工具,实现基于交付产品的文档与实物在线验收;实现基于实做BOM 的质量数据管理与分析,较手工追溯节省时间达60% 以上;对产品文档清单能够按照验收标准批量初始化,验收时进行完整性自动审查;对产品实物能够按照验收检查表批量初始化,能够调取历史数据进行包络分析;使产品交付与验收过程批量化、标准化。通过交付的结构化产品数据,实时形成可视化图表展示,为管理层及时决策提供数据支撑。
4)构建了厂所异地背景下数字化的设计制造协同模式保障型号任务按时交付。以产品生产计划任务为驱动、以交付关联产品数据进行任务闭环,实现双方基于计划、基于产品的在线协同,加强了所研产一体化目标建设;基于在统一模式下兼容网络互通在线传递与网络不通离线传递两种方式,在后期可将该模式复制到其他所有外协单位;通过整体项目实施为型号研制促进了产品数据规范化、保障了产品交付及时性、增强了供应链韧性。
5.3 推广价值
通过两个试点型号的应用,为我单位面向典型外协生产单位的数字化协同研制和质量管控奠定了坚实基础, 具备面向多个型号、多个外协生产单位推广的条件,具有重要的示范意义和推广价值。此外,项目研究成果可作为成熟模式在其他设计单位及外协生产单位开展复制应用,有助于实时掌握产品生产进度,提高产品研制质量,缩短型号研制周期,具有良好的市场前景和巨大的经济效益。
-
控制技术
+关注
关注
3文章
348浏览量
33265 -
数字化
+关注
关注
8文章
8911浏览量
62347 -
一体化
+关注
关注
0文章
259浏览量
14501 -
数据分析
+关注
关注
2文章
1462浏览量
34230
原文标题:航天产品跨地域多维度一体化控制技术改进研究与应用
文章出处:【微信号:CADCAM_beijing,微信公众号:智能制造IMS】欢迎添加关注!文章转载请注明出处。
发布评论请先 登录
相关推荐
华为入选中国云网安一体化能力领导者
光储充一体化电站建设解决方案

探究光储充一体化电站建设关键技术研究
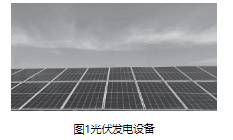
浅谈园区级光储充一体化关键技术研究方案

一体化导航技术的应用和优点
基于OpenRTI的空天一体化平台系统
《嵌入式机电一体化系统设计与实现》读后感
安消一体化平台建设方案
什么是机电一体化?它有哪些应用?
触想工业一体机助力智慧农业水肥一体化高效应用
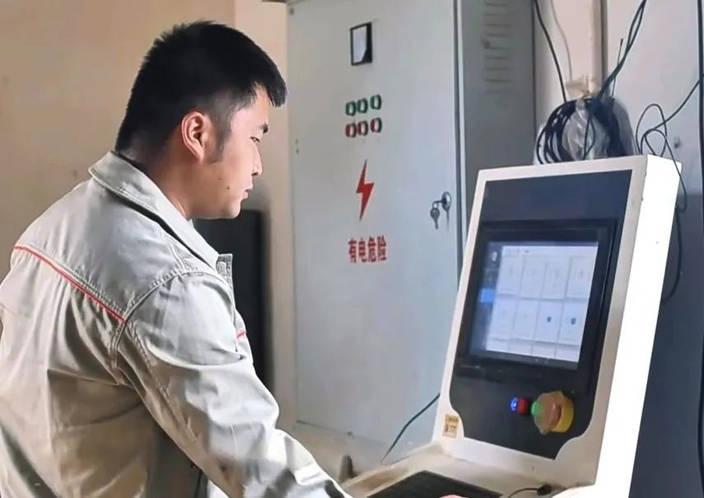
评论