车辆设计必须考虑各种环境应用,从白雪覆盖的冻原到酷热的沙漠。大多数消费类应用的预期使用寿命可能为数月,但汽车电子产品的使用寿命通常要长达15年甚至更久。OEM及其供应商通常会制定一个汽车任务配置文件来说明一个汽车组件,这份文件本质上即为组件在其使用寿命期间将面临的所有预期环境和功能条件的总结。
与此同时,用于汽车组件的集成电路 (IC) 通常需要根据汽车电子委员会的 AEC-Q100 标准进行认证。适用于ADAS 传感器融合和数字驾舱系统的理想组件必须在设计时就将这些规格考虑在内。例如MPS 的 MPQ8875A-AEC1即为一款符合AEC-Q100认证的40W 数字升降压(Buck-Boost)变换器,它以小尺寸4mmx5mm QFN封装提供30W功率。
本文将帮助读者更好地理解任务配置文件与应用于每个汽车级组件的各种电子元器件可靠性认证测试之间的关联。我们将探讨几个常见问题:
谁负责评定 IC 的可靠性能力?
如何应用可靠性“加速模型”来评估IC可靠性测试满足寿命评估需求?
行业通常会根据产品应用的预期寿命来评估其可靠性。换句话说,即看一个应用是否能够承受整个产品寿命周期的应力。为做出合理判断,我们有必要了解应用在其现场使用期间会面临怎样的应力。然后,将这种预期的现场应力与最初认证的应用中所有电子元器件的应力进行比较。这样,就可以确定预期的现场应力是否会使应用中的器件应力过度,从而导致过早失效。对于安全措施非常严格的汽车行业来说,这一点尤为重要。
任务配置文件用于模拟特定类型的现场应力及其相关严重程度。最常参考的应力与温度/电压和热机械应力相关。温度/电压应力通常理解为IC中硅器件的主要老化效应。这种老化效应会影响材料特性,IC的性能也会随时间退化。热机械应力是指器件因温度变化而膨胀和收缩时产生的应力。
我们的目标是了解应用在目标寿命前,特定组件是否可以保证其性能。换句话说,应用的目标寿命是否能达到典型半导体可靠性浴缸曲线的损耗阶段?由于半导体寿命有限,其故障率在损耗阶段会因磨损而迅速增加。随着时间的推移,应力越大,达到固有寿命的时间就越早,磨损失效的可能性就越大(见图 1)。
图1: 浴盆曲线
半导体制造商必须在新产品投入生产和投放市场之前对其进行验证。在验证过程中,IC会进行一系列应力测试,以触发并评估某些失效机制。在测试上述应力时,通常采用两种非常有用的测试。
第一个是高温工作寿命 (HTOL) 测试,它模拟工作条件以在测试室内引发与温度和电压相关的失效机制(见图 2)。第二个是温度循环 (TC) 测试,由于IC 由不同材料制成,而每种材料都具有不同的温度系数,通过TC测试给IC施加应力以引发机械失效机制。
这只是IC在量产之前必须通过的两种验证实验。AEC-Q100 标准定义了汽车 IC 的整套认证测试体系,其中许多测试在JEDEC 标准中也进行了规定。部分应用对电子器件的可靠性要求还要更高,例如卡车和加强型车辆系统,它们必须能够承受双倍的HTOL和TC测试等级应力,才能满足目标任务配置文件要求。MPS的65V 降压变换器MP4572-AEC1即能够在提供 2A 输出的同时满足如此严格的可靠性要求。
图2: MPS HTOL测试室
了解加速因子
HTOL测试由JEDEC标准JESD22-A108 定义。一组231个单元需要在125°C下运行1,000小时。该测试使用 Arrhenius 模型来确定温度加速因子(Af),它提供所需的测试时间 (tt) 以模拟实际使用的等效时间。表1给出了一个任务配置文件的范例,该范例用来模拟平均结温87℃条件下,运行12000小时。Tj是硅器件的结温,对于有较大功耗的功率IC而言,结温需要被特别考虑,因为环境温度Ta往往远低于结温Tj。
表 1:AEC-Q100修订版H; 表 A7.1 – AEC-Q100 应力测试条件和持续时间的基本计算
加载 | 操作 | 热机械 |
任务配置文件输入 |
tU = 12,000hr(15年的平均使用时间) $$A_f = exp left[frac{E_a}{K_B} times left(frac{1}{T_u}-frac{1}{T_t}right)right]$$ TU = 87°C (使用环境中的结温) |
nU = 54,750cls (使用超过 15 年的发动机开/关循环次数) ∆TU = 76°C (使用环境中的平均热循环温度变化) |
应力测试 | 高温工作寿命(HTOL) | 温度循环(TC) |
应力条件 | Tt = 125°C (测试环境中的结温) | ∆Tt = 205°C (测试环境中的热循环温度变化:-55°C至+150°C) |
加速模型(所有温度单位为 K) |
阿伦尼斯(Arrhenius) 也适用于高温存储寿命 (HSL)、NVM 耐久性、数据烘烤和运行寿命 (EDR) |
科芬·曼森(Coffin Manson) $$A_f = left(frac{Delta T_t}{Delta T_u}right)^m$$ 也适用于功率温度循环 (PTC) |
模型参数 |
Ea = 0.7eV (活化能;0.7eV为典型值,实际值取决于失效机制,范围从 -0.2eV 到 1.4eV) kB= 8.61733 x 10-5eV/K (玻尔兹曼常数) |
m = 4 (Coffin Manson 指数;4 表示硬质合金中的裂纹,实际值取决于失效机制,范围从表示韧性材料的1到表示脆性材料的9) |
计算的测试时间 |
tt = 1,393hr(测试时间) $$ t_t = frac{t_u}{A_f} $$ |
nt = 1,034cls(测试循环次数) $$n_t=frac{n_u}{A_f}$$ |
Q100测试时间 | 1 000公里 | 1 000 千克 |
在此示例中,125°C TJ下需要 1,393 小时来对应 87°C TJ 下的12,000 小时。 HTOL认证要求1,000 小时。使用表 1 中的公式,计算出上述场景中的加速因子为 8,615,等同于125°C TJ下的 8,615 小时。可见,任务配置文件将超过认证应力约40%。
任务配置文件计算
表 2 显示了一个任务配置文件,以及它通常是如何定义的。
配置文件 | |||
主动 | 被动 | ||
TJ (°C) | 时间(h) | TJ (°C) | 时间(h) |
-40 | 45 | -40 | 346 |
-20 | 45 | 15 | 21168 21168 21168 21168 |
40 | 855 | 25 | 42336 |
50 | 3150 3150 | 35 | 21168 21168 21168 21168 |
60 | 4950 | 40 | 1382 |
70 | 900 000 | 86400 | |
80 | 11250 11250 | ||
90 | 6750 | ||
100 | 4950 | ||
110 | 2700 2700 | ||
120 | 1170 1170 | ||
125 | 135 | ||
45000 | |||
合计 | 131400 131400 | (15年寿命) |
表2: 典型任务配置文件
此示例定义了主动和被动两种模式,并且所有温度都为结温。主动和被动模式不需要区分。当IC工作时,一定存在与电流密度相关的老化效应,但与温度的老化效应相比,这些效应可忽略不计。
使用表1中的Arrhenius方程,输入表 2 任务配置文件中的第一个数据点 (-40°C)。当测试温度为125°C 时,加速因子 (Af) 可以通过方程 (1) 计算得出:
$$Af=expBiggl[left(frac{Ea}{kb}right)timesleft(frac{1}{273K-40K}-frac{1}{273K+125K}right)Biggl]$$ $$Af=4184927.76$$
使用表1中的第二个方程、加速因子以及表2任务配置文件中的第二个数据点 (45h),使用方程 (2) 计算出所需的测试时间:
$$Af=frac{tu}{tt}$$ $$tt=frac{tu}{Af}$$ $$tt=frac{45h}{4184927.76}$$ $$tt=0.000107h$$
可以得出,在 45 小时内-40°C所代表的实际应力将等于在125°C下进行不到一小时的HTOL测试(见表 2)。 为了计算出总的任务配置文件应力,任务配置文件的所有数据点都必须进行类似的计算,并且相关的等效测试时间总和为大约5888h。这意味着,器件实际上承受的应力将比测试条件下承受的大 6 倍。
通过1000小时的HTOL测试意味着该器件可以承受至少1000 小时的应力。但是,这并不能确定超过1000小时之后器件可以承受多长时间的应力。鉴于等效应力是认证应力的 6 倍,因此很大可能会出现过早失效的问题。
由此可见,汽车电子元器件的可靠性测试至关重要,器件必须能够承受高强度的应力。图 3 显示了正在进行 HTOL 测试的MPS器件。
图 3:在一定负载条件下进行HTOL 测试的MPS器件
如果无法放宽任务配置文件(例如,无法通过散热措施降低结温来减少相关应力),则应调整认证级别。
采用此示例,将结温增加至150°C进行HTOL测试认证。此时,涵盖此任务配置文件应力所需的测试时间被减少到大约1767小时。请注意毋采用更高的结温,因为150°C通常是硅器件可以承受而不会损坏的最高绝对温度。当然,将该示例的测试时间延长到大约2,000小时会更加安全。不过,即使是 1,500 小时的认证测试时间也可以提供相当程度的信任度,对测试成本和时间而言,也是较合理的选择。
任务配置文件定义
最后,这些计算实际上由谁进行,谁来负责?对汽车应用来说,AEC-Q100 标准有明确规定。AEC-Q100修订版H的附录7中有一个流程图,适用于评估现有的合格组件(见图 4)。
图4: AEC-Q100修订版H A7.2中的流程图
首先,电子控制单元 (ECU) 的任务配置文件由一级供应商确定,需要将其转换为组件将执行的任务配置文件。如果组件存在并且已经过认证,则组件制造商已经完成了基本计算。
图1显示了代表本文上述基本任务配置文件的HTOL认证。通过这些数据和 Arrhenius 模型,一级供应商可以确定实际应用的任务配置文件是否与测试条件相当。对于温度和电压应力以外的参数任务配置文件也是如此。
结论
在汽车行业和工业应用需求的主要推动之下,应用设计需要面对不断提高的可靠性要求,以应对多种应力条件。任务配置文件越来越受到关注,并被要求尽可能匹配目标应用的实际应力源。而IC制造商设计的器件必须能够在预期寿命应力下保持其特定的性能,例如MPS的MPQ8875A-AEC1和 MP4572-AEC1。对于一级供应商设计师和IC设计者来说,在流程早期进行合作,评估如何设计应用以最好地满足与 ECU 可靠性相关的实际需求,同时最大限度地提高成本效益,这才是最有效的方法。
审核编辑:彭菁
-
电子元器件
+关注
关注
133文章
3306浏览量
104928 -
电压
+关注
关注
45文章
5559浏览量
115585 -
模型
+关注
关注
1文章
3171浏览量
48711 -
MPS
+关注
关注
26文章
259浏览量
64117
发布评论请先 登录
相关推荐
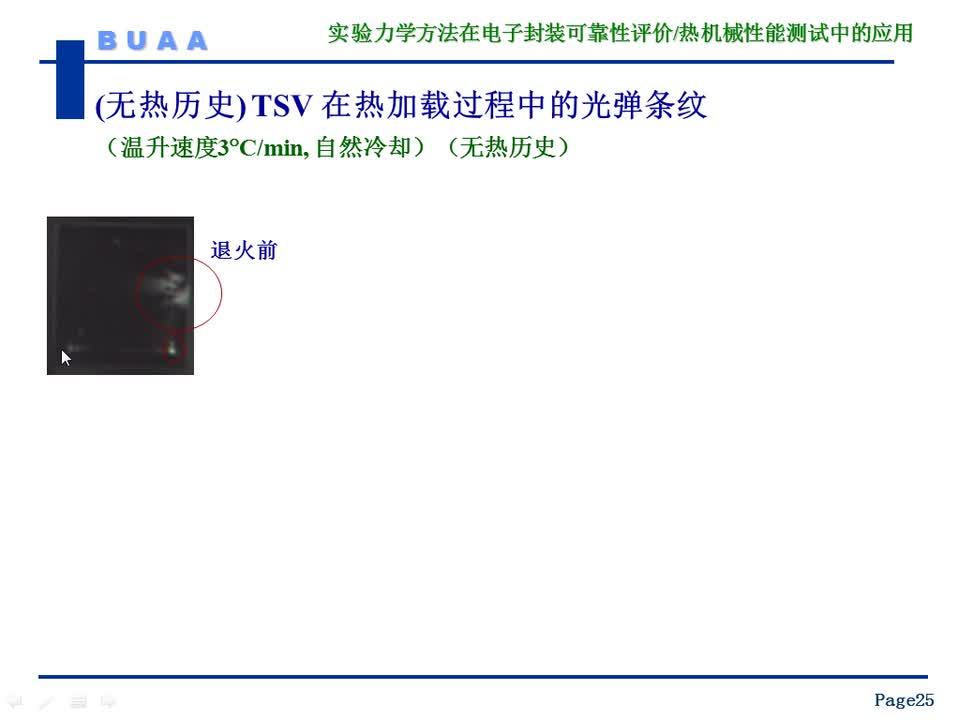
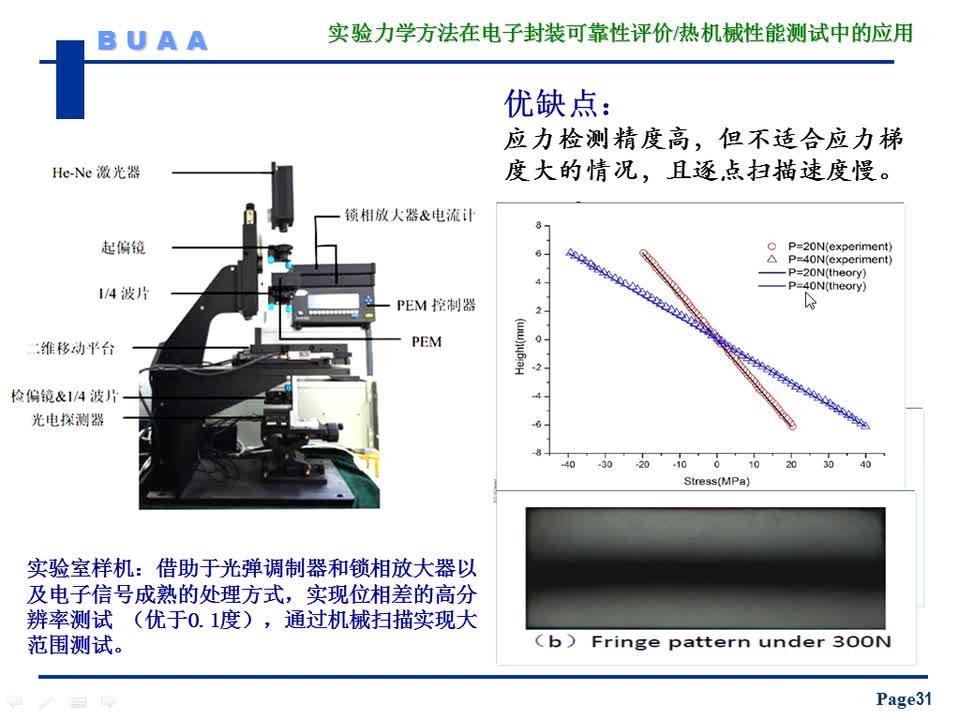
LED加速寿命和可靠性试验
可靠性设计分析系统
企业为何要控制和评估产品的可靠性?
可靠性与失效分析
【PCB】什么是高可靠性?
什么是高可靠性?
可靠性试验(HALT)及可靠性评估技术
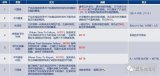
评论