前言:HJT的投资节奏逐步从高赔率走向高胜率,本篇重点更新0BB,我们认为0BB对降本-硅片减薄、降低银浆,提效-降低遮光率,均有较大影响,做如下更新:
核心要点:
1、什么是0BB?
多主栅到0BB的变化实质是电极变化。电池片正背面的金属电极用于导出内部电流,可分为主栅和副栅,其中主栅主要起到汇集副栅的电流、串联的作用,副栅用于收集光生载流子。0BB(无主栅)就是电池片环节取消主栅,组件环节用焊带导出电流,可以降银+降低遮光从而降本增效。
但由于BB方式无主栅后,焊带若直接焊接在TCO膜上,焊接难度更大,可能会造成脱落等问题。为解决上述问题,当前出现SWCT(专利+成本问题,未在国内大规模推广)、点胶(设备简单,稳定性高,但结合力可能略有不足)、焊接点胶(结合力足,但精度要求高、难度大、速度慢)三种工艺方案,各有优劣。
2、为什么要关注0BB(确定性)?
1)降本:可突破硅片减薄的瓶颈,同时HJT降本诉求最为迫切
硅片:HJT硅片减薄面临重要瓶颈之一是电池环节副细栅使用银包铜、主栅使用低温银浆,由于两种浆料的膨胀系数不同,电池串容易有隐裂等问题。在0BB工艺使用后由于只有细栅的银包铜浆料,不存在不同浆料带来的膨胀系数不同的问题。
电池环节:主要是降低银耗,HJT银浆成本最高,降本潜力最大,降银浆诉求最为迫切。目前银浆成本是 HJT(0.117元/W)>Topcon(0.064元/W)>PERC(0.053元/W),如果叠加银包铜浆料,我们预计降本,HJT(-0.052元/W)>PERC(-0.031元/W)>Topcon(-0.016元/W),综合下来看,HJT降本潜力最大,降本诉求最为迫切。
2)增效:减少遮光面+缩短电流传输距离+提高良率
减少遮光面:取消电池片主栅,降低遮光面积,增加光吸收量。
缩短电流传输距离:之前电极在导出电流的过程中,电流需横向穿过覆盖有金属主栅线的电池顶层从而造成功率损耗;0BB直接用焊带导流,免去了主栅路径,大大减少了传输距离。
提高良率:传统焊带使用红外焊接,融化冷却的过程中焊带会发生收缩,会把细栅拉断,而0BB采用低温焊接/点胶,理论上良率可以做到99%。
3、目前0BB瓶颈在哪?
工艺上:主要是设备的稳定性和量产性,但这不是技术障碍,而是时间问题,需要把良率、产量做到现在MBB、SMBB接近的水平。优先导入中试量产的企业具有先发优势。
行业上:由于2023年组件大厂新扩近400GW TOPCon均为SMBB串焊机新产能,如果快速推动0BB会导致组件厂利益受损,而新技术落地最终还是要头部企业来大面积量产来推动;同时0BB更适用于HJT,我们预计HJT产能有望2024-2025年大规模放量。
4、 经济性测算及市场规模?
基于我们对经济性的测算,0BB大规模量产后,叠加银包铜浆料,相较于当前量产的15BB技术成本可降低约5分/W,相较于量产的20BB可降低约2.5分/W,我们认为在2023年下半年主流企业有望批量扩产HJT。
2023-2025年HJT扩产有望达到55、100、200GW,考虑到0BB的渗透率,预计0BB串焊机对应市场空间为3、44、67亿元,0BB焊带对应市场空间2、40、133亿元。
5、标的:
面对0BB从1到N的时间点,我们认为设备及对应辅材是受益的核心环节。
重点推荐奥特维:串焊机龙头,已供货东方日升。400GW的0BB扩产规模对应串焊设备需求95亿元,60%市场份额对应设备价值量57亿元(充分考虑串焊机降价,目前比SMBB的+30%价格),对应260,公司22年收入体量约35亿元。
其次推荐宇邦新材:焊带龙头,已供货东方日升,0BB带来焊带量利齐升。假设26年扩产规模400GW,对应全行业0BB焊带需求275亿元,30%市占率对应82亿元,公司22年收入体量约20亿元。同时,0BB焊带毛利率预计高于传统焊带,可进一步提升盈利水平(参考SMBB焊带毛利率可高于MBB焊带3-8个百分点.)。
建议关注迈为股份:布局0BB串焊机;先导智能:已推出量产型0BB串焊设备。
正文:
1、什么是0BB?
1.1、0BB(无主栅)电池片环节取消主栅,组件环节用焊带导出电流
0BB与此前的栅线方式对比,实质是电极变化,电池片正背面的金属电极用于导出内部电流,可分为主栅(Busbar)和副栅(又称细栅,Finger),其中主栅主要起到汇集副栅的电流、串联的作用,副栅用于收集光生载流子。0BB(无主栅)就是电池片环节取消主栅,组件环节用焊带导出电流。从发展历程看,栅线从4BB、5BB→MBB(Multiple-Busbar,9-15栅)→SMBB(Super-Multiple Busbar,16栅及以上)→0BB(无主栅),主栅逐渐变细,可以起到降银+降低遮光起到降本增效的作用。
图:主栅发展历程
1.2、0BB目前主流方案有梅耶博格SWCT、奥特维的点胶、迈为的焊接+点胶方案
栅线由多主栅到无主栅最大的难点在于:此前焊带是焊接在主栅上,而0BB方式无主栅后,焊带若直接焊接在TCO膜上,焊接难度更大,可能会造成脱落等问题。为解决上述问题,当前出现SWCT(铜丝复合膜层压)、点胶、焊接点胶的三种工艺方案。
表:三种主流0BB工艺方案对比
1)SWCT:专利+成本问题,未在国内大规模推广
最早由 Day4 Energy提出,2012年Day4 Energy 因经营不善退市,并将其技术出售给梅耶博格,后者将 DNA 技术更名为SmartWire 并继续开发,并于2013 年向市场发布。SmartWire专利由梅耶博格独享,加上该方案存在成本较高等问题,故国内并未实现无主栅技术的大规模推广。
与常规的封装工艺相比,SWCT使用新型串焊机将铜丝复合膜铺设在两片电池的正、背面,实现相邻电池的串接,串接后的电池串经过排布、叠层后,在一定的层压温度和压力下将铜丝和电池细栅压合在一起,形成欧姆接触。
工艺流程:生产铜丝复合膜→层压
SmartWire 的关键在于铜丝复合膜:主要包括电绝缘光学透明薄膜、薄膜平面上的胶粘剂层以及嵌入在胶粘剂层中的多条平行带涂层的铜丝(焊带),铜丝由胶粘结层粘贴在薄膜的表面,其表面低熔点的合金涂层从胶粘剂层中突出出来。带有合金涂层的焊带卷在滚筒上,焊带穿过带有开口的边框粘贴在薄膜上;薄膜表面涂有胶粘剂,由滚筒牵引带动,焊带和带有胶粘剂的薄膜交集处由两个滚筒加热,胶粘剂得以软化,焊带浸入粘结剂中,再进行冷却。
图:生产铜丝复合膜
通过层压实现膜与细栅的合金化。铜丝复合膜与电池片连接,将电池片组串,随后与封装胶膜、背板或玻璃重叠,在加热层压过程使焊带与细栅形成稳定电性连接。将铜丝复合膜层压在相邻的电池片表面形成串联。
图:层压后的电池片成串示意图
材料:生产铜丝复合膜需要薄膜材料和胶粘剂。其中薄膜材料需要选取高延展性、良好的绝缘特性、光学透明度、热稳定性、抗收缩性等,并具有良好的粘接能力,可选种类包括EVA、PES、TPU、TPO等。胶粘剂选软化温度在90-110℃之间,对薄膜和电池片具有良好附着力的各种材料都适合作为粘合剂。焊带涂层需要用到铟这一稀有金属元素。
表:铜丝复合膜材料对比
优点:低温工艺、不易脱栅
低温工艺:SmartWire加工条件通常在约140-160℃,对电池产生的热机械应力较小,更适合HJT低温工艺。
图:SmartWire低温工艺
图:SmartWire工艺降银提效
不易脱栅:复合膜抽真空之后,膜有一定的弹性,热和冷的状态下始终产生力量把焊带往电池片方向上压紧,不容易脱栅,结合力更好。
图:SmartWire铜丝复合膜
缺点:工艺复杂、材料成本高、光学遮挡
工艺复杂:虽然取消了串焊步骤,但需要进行膜线复合及热压成串两个步骤作为替代,并且头尾电池片线膜电极复合单元需要经过特殊制作处理,增加了工艺复杂度,也导致了潜在的量产瓶颈。
材料成本较高:虽然节省了用银,但焊带涂层需要用到铟这一稀有金属元素、增加薄膜等耗材。
光学遮挡:铜丝复合膜容易造成较为严重的光学遮挡。
2)点胶:设备简单,稳定性高,但结合力可能略有不足
先施加胶点体(UV胶、热熔胶等粘合剂),将整条焊带利用UV灯点胶固化在电池片上,再通过层压实现焊带与电池片的合金化。
工艺流程:胶粘→层压
点胶:在每个电池片表面上进行点胶形成多个点胶体,通过点胶体将焊带粘结于电池片上,既可以将多个电池片串联形成电池串,又可以保证焊带不在电池片上移动,为下一步电池组件的封装做准备;
布线:沿着垂直于每个电池片表面的细栅线的方向均匀间隔布置多条焊带,与细栅线垂直;
固定:UV灯照射使得焊带均通过对应点胶体粘结于对应电池片上,同时每条焊带均与对应电池片表面的每条细栅线直接接触;
排版: 对多个电池串排版形成电池组件;
层压: 对电池组件进行加热层压 (130-使焊带与170°C)细栅形成合金连接
图:东方日升点胶方案下相邻电池片的串联示意图1
图:东方日升点胶方案下相邻电池片的串联示意图2
优点:设备简单、稳定性高
缺点:EL检测时焊带下有阴影、焊带和电池片结合力不足
材料:点胶体需要增加绝缘胶,焊带为铅锡合金涂层的低温铜焊带,锡的熔点低、比例高,直径约0.1-0.3mm,技术难度不高
3)焊接点胶:结合力足,但精度要求高、难度大、速度慢
先将焊带焊接在电池片上,再点胶将焊带进一步粘贴在电池片上,再层压合金化,这种方案与点胶层压方案不同在于需要进行焊接,焊接实现初步的固定、点胶进一步固定。
工艺流程:焊接→点胶→固化
焊接:通过红外加热使得焊带表面合金或金属熔化并与电池片表面及细栅完成初步连接;
点胶:在焊接好的电池片-焊带的指定位置施加粘附点,粘附点的数量过多会直接导致增加工艺难度以及施加粘附点工艺周期,然而数量过少则达不到加固焊带和电池片的连接强度要求,因此根据遮光面积和机械性能需要,粘附点数量3-8排;
固化:将电池串正面粘附点固化,继续将电池串搬运至下一工站,将电池串保持一定温度条件下进行翻转,并在电池串背部施加粘附点,同时固化,形成电池串;
将多个电池串按照一定的规则进行摆放,摆放在设有封装胶膜的玻璃上,通过焊接将电池串连接成所需要的完整电路,并在后续操作中完成封装-检测-层压等过程。
图:迈为焊接点胶流程示意图
图:迈为焊接点胶连接示意图
优点:焊带和电池片的结合力足,不易脱栅;
缺点:焊接过程中容易导致断栅,对点胶精度要求高,难度大、速度慢。
2、为什么要关注0BB(确定性)?
2.1、降本:去除主栅在硅片环节利于减薄,在电池环节降低银耗
1)硅片环节:制约HJT硅片减薄的关键工艺0BB已即将成熟,后续HJT硅片可继续减薄至100μm。
HJT之前硅片减薄面临几大瓶颈,一是减薄后自动化问题导致碎片率更高;二是减薄后效率下降;三是减薄后再在细栅使用银包铜、主栅使用低温银浆,由于两种浆料的膨胀系数不同,电池串容易有隐裂等问题。
目前问题一已解决,问题二在硅片厚度100μm时影响较小,问题三在0BB突破后也可解决,即只有细栅的银包铜浆料,不存在不同浆料带来的膨胀系数不同的问题。
2)电池环节:主要是降低银耗,HJT银浆成本最高,HJT降本潜力最大,降银浆诉求最为迫切。
PERC:目前量产的PERC单W银耗约11.7mg,对应单W银浆成本为0.053元。
TOPCon:目前量产的TOPCon多为182尺寸16BB,单片银耗为115mg,单W银耗为14.0mg,对应单W银浆成本为0.064元。
HJT:华晟20BB量产,单片银耗为194mg,单W银耗为18mg,对应单W银浆成本为0.12元。
图:PERC、Topcon、HJT银耗(单位:mg/W)
图:PERC、Topcon、HJT银浆成本(单位:元/W)
如果使用0BB技术,PERC可降银0.031元/W,TOPCon降银0.016元/W,HJ(20BB)降银0.052元/W,降银HJT>PERC>Topcon。由于P型电池目前已经接近其效率极限,逐渐退出历史舞台,目前新建产能大多采用N型,而对比Topcon和HJT,HJT明显跟0BB更契合且降本效果较明显,因此HJT企业对于0BB需求更加迫切。
表:PERC、Topcon、HJT降本预期测算
0BB技术叠加银包铜浆料,终极银浆成本约0.032元/W。0BB技术省去了主栅,节省了浆料耗量,而银包铜浆料能够减少银耗量;终极来看,30%银包铜浆料价格约3000元/kg。
表:0BB+银包铜HJT降本测算
2.2、增效:减少遮光、减少电流传输距离、提高良率
1) 减少遮光面:取消电池片主栅,降低遮光面积,增加光吸收量。
2) 缩短电流传输距离:之前电极在导出电流的过程中,电流需横向穿过覆盖有金属主栅线的电池顶层从而造成功率损耗;0BB直接用焊带导流,免去了主栅路径,大大减少了传输距离。
3) 提高良率:传统焊带使用红外焊接,融化冷却的过程中焊带会发生收缩,会把细栅拉断,而0BB采用低温焊接/点胶,理论上良率可以做到99%。
图:无主栅电池和组件
3、目前0BB瓶颈在哪?
1)工艺上:根据迈为口径,目前0BB主要是设备的稳定性和量产性,但这不是技术障碍,而是时间问题,需要把良率、产量做到现在MBB、SMBB接近的水平。优先导入中试量产的企业具有先发优势。
图:光伏绝缘胶示意图
针对点胶方案的绝缘胶EL黑影和贴合度不高问题,东方日升已有解决方案:【可能通过加粗栅块和导电环】,即在水平栅线上间隔排布连接有多个加粗栅块或导电环的布置线,沿布置线上点涂非导电胶并连接焊带;导电环内涂胶水后,能够增大每条布置线上用于粘接焊带的涂胶面积,保证焊带在电池片上的固定效果;同时加粗栅块使点涂胶水不容易遮挡栅线,保证组串形成的组件可靠性,解决了胶水涂布面积不当导致焊带固定不牢或EL不良的问题。
图:东方日升一种0BB电池片结构示意图
针对去除主栅后细焊带拉力是否足够问题,华晟也已经有解决方案:【华晟新能源可能运用软连接和硬连接相互搭配的工艺,防止电池片和焊带脱离】,即在太阳能电池片两面均使用液态粘接胶与粘接胶带搭配的工艺,液态胶与电池片之间属于硬连接,能够减少电池片的弯曲程度;粘接胶带与太阳能电池片之间的连接属于软连接,能够缓冲保护电池片头尾部易碎区域,两者共同作用有利于减少碎片的产生,使焊带和电池片连接更加紧密,同时避免在层压的过程中电池片发生翘曲和焊带脱离,提高电池片的使用寿命。
2)行业上:由于2023年组件大厂新扩近400GW TOPCon均为SMBB串焊机新产能,如果快速推动0BB会导致组件厂利益受损,而新技术落地最终还是要头部企业来大面积量产来推动;同时0BB更适用于HJT,我们预计HJT产能2024-2025年大规模放量。
4、 如何投资?
4.1、经济性测算
0BB大规模量产后,相较于量产的SMBB可降低约4分/W。
0BB点胶环节需要绝缘胶,目前单W成本0.015元,未来规模化后降至0.01元;
丝印设备价值量由4000万/GW下降至2000万/GW(过去SMBB技术需要4台丝印设备,正背面的主副删各需要一台丝印设备,由于0BB不需要印主栅,因此0BB的丝印环节只需要2台设备);
串焊环节需要购置新的0BB串焊机,传统的SMBB串焊机价值量为2000万/GW,0BB串焊机价值量目前为2600万/GW,未来有望下降至2000万/GW。
图:HJT 210电池 0BB经济性测算
4.2、竞争格局/进展
1)量产:东方日升金坛基地0BB 210异质结电池于23年4月底首先首批已经下线,6月满产;
2)中试:正在中试的厂商包括通威、爱康、华晟等。爱康科技5月底表示新开发的异质结组件AKiDower7.0系列(730W)采用0BB技术,可有效降低串联电阻,实现组件CTM提升1%;叠加100um以下硅片薄片化、光转膜、微晶工艺等先进技术,转换效率高达23.5%,当前公司已具备量产能力;
3)技术储备:隆基等组件大厂在接触0BB设备厂商,天合有储备相关技术专利,中来有0BB的Topcon专利储备。
表:行业0BB进展情况
参考SMBB放量仅需一年时间,我们预计0BB放量速度也会很快。从SMBB的切入速度来看,2022年初行业开始试用SMBB, SMBB设备占奥特维2022年新签订单比重约20%,而到2023年初奥特维的串焊机出货均为SMBB类型,占比约95%,我们认为0BB有望复制SMBB的快速放量节奏。
4.3、市场空间测算
核心假设:
1)2023-2025年、峰值点HJT扩产55、100、200、400GW;TOPCon扩产300、300、200、100GW;
2)2023-2025年、峰值点0BB在HJT的渗透率分别为5%、70%、90%、100%;在TOPCon的渗透率分比为3%、40%、70%、100%;
3)0BB串焊机价值量目前为2600万/GW,未来大规模使用有望下降至2000万/GW;
4)0BB焊带价值量目前为3900万/GW,未来大规模使用有望下降至3600万/GW。
由此,预计0BB串焊机对应市场空间为3、44、67亿元,0BB焊带对应市场空间2、40、133亿元。
表:0BB设备市场空间测算
5、标的:
面对0BB从1到N的时间点,我们认为设备及对应辅材是收益的核心环节。重点推荐奥特维(串焊机龙头,已供货东方日升,0BB带来串焊机量利齐升),其次宇邦新材(焊带龙头,已供货东方日升,0BB带来焊带量利齐升),建议关注迈为股份(布局0BB串焊机)、先导智能(已推出量产型0BB串焊设备)。
1)奥特维:传统串焊机龙头,0BB串焊机技术布局领先,多种技术路线均有储备。除了目前的点胶方案外,奥特维也储备了类似SmartWire方案的铜丝复合膜路线。2022年初行业开始试用SMBB,到2023年初奥特维的串焊机出货均为SMBB类型,我们认为0BB有望复制SMBB的放量节奏,奥特维新签订单有望维持高增速。
峰值假设下,400GW0BB扩产规模对应串焊设备需求95亿元,假设公司市场份额60%,对应金额57亿元,公司22年收入体量约35亿元。
2)宇邦新材:焊带龙头,0BB焊带已批量供货东方日升。未来受益于0bb焊带需求量增加+单位盈利进一步提升。
假设26年扩产规模达到400GW,按0BB焊带10万/吨假设,对应全行业0BB焊带需求275亿元,假设公司市占率30%。对应金额82亿元,公司22年收入体量约20亿元。同时,0BB焊带毛利率预计高于传统焊带,可进一步提升盈利水平。(参考SMBB焊带毛利率可高于MBB焊带3-8个百分点.)
表:HJT年扩产达200GW时0BB相关企业弹性测算表(25年)
表:HJT年扩产达400GW时0BB相关企业弹性测算表
建议关注:
1)迈为股份:HJT电池片整线设备龙头,也布局了0BB串焊机,2023年3月将于华晟处验证,采用先焊接再点胶的方式。迈为在HJT设备上走的比较快,其整线设备围绕HJT技术展开。具备渠道优势,中标了全球光伏龙头的量产HJT整线订单,HJT双面微晶经过量产验证、在无铟化、电镀铜等HJT新技术方面均有布局,确定性强。
2)先导智能:锂电整线设备龙头,积极布局光伏领域设备。2022 年 11 月 24 日根据公司微信公众号,先导智能推出量产型无主栅串焊设备,量产效率超过 6800 片/小时,可实现 100μm 厚度电池片串焊。
-
电极
+关注
关注
5文章
813浏览量
27210 -
焊机
+关注
关注
17文章
191浏览量
26742 -
金属电极
+关注
关注
0文章
7浏览量
6517
原文标题:HJT- 0BB:积势待发可期
文章出处:【微信号:AIOT大数据,微信公众号:AIOT大数据】欢迎添加关注!文章转载请注明出处。
发布评论请先 登录
相关推荐
ASMT-YTD2-0BB02 高亮度三色PLCC-6白色表面LED
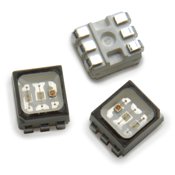
ASMT-YTB2-0BB02 高亮度三色PLCC-6黑色表面LED
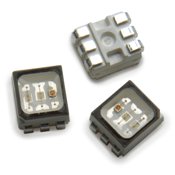
CGAEA3X7T0G104M030BB TDK CGAE系列MLCC
PESD5V0V1BB 双向TVS管 120W 5V SOD-523
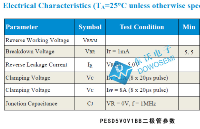
再突破!通威HJT组件功率达到755.03W,转换效率突破24.31%
0BB无主栅技术在IBC电池中的应用及封装测试
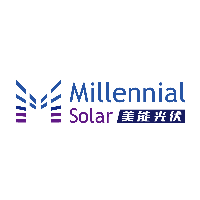
评论