观众朋友们大家好~今天起,我们全新的栏目——仿真101大讲堂正式上线!仿真作为我们半导体器件研发的重要工具之一,通过建模、验证、优化等流程,让我们在研发时能够少走许多“弯路”。作为一家拥有优秀仿真能力的半导体公司,我们希望能够用自身的经验和优势给大家带来一些新的启发和思考。
第一节课,我们从力学出发,讨论下在PCB板非常讨厌的“弯曲挠度”和螺钉布置之间的关系,以快插板为例,探讨下3螺钉和4螺钉两种不同的方案,对底部散热型表贴式功率器件热表现的影响。
话不多说,开讲开讲!
省流
结论先看
对于表贴式功率器件,当采用螺钉锁付结构将器件载板与冷板进行锁付散热时,更多的螺钉数量并不一定带来更贴合的锁付效果
在一定的空间布局下,螺钉的具体选用数量及分布应在充分的DOE分析后进行确定
01什么是表贴式器件?
元器件封装按照安装的方式不同可以分为两大类:直插式器件(Through-hole mounting device, THD)和表贴式器件(Surface mounting device, SMD)
直插式器件的特点
封装的焊盘一般穿过整个PCB,引脚从一侧穿入,并在另一侧进行引脚的焊接。对于功率级(650V及以上)的直插式器件(如TO-247),封装内的散热铜块位于封装底部,器件的主要散热路径为结-底部外壳-绝缘层及热界面材料-冷板,仅有少部分热量通过引脚流向PCB。
TO-247(直插式)的贴合冷板方式
表贴式器件的特点
封装的焊盘只附着在PCB的一侧,在同一侧进行引脚的焊接。对于底部散热型(Bottom side cooling)的表贴式器件(如TO-263),封装内的散热铜块位于封装底部,器件的主要散热路径为结-底部外壳-PCB-绝缘层及热界面材料-冷板。对于顶部散热型(Top side cooling)的表贴式器件(如PSOP),封装内的散热铜块位于封装顶部,器件的主要散热路径为结-顶部外壳-绝缘层及热界面材料-冷板,仅有少部分热量通过引脚流向PCB。
TO-263(底部散热型表贴式)的贴合冷板方式
PSOP(顶部散热型表贴式)的贴合冷板方式
02螺钉锁付的目的是什么?
对于底部散热型表贴式功率器件,由于器件的功率高、发热大,为了确保器件能够长时间的安全平稳运行,往往需要借助热界面材料将器件的热量由PCB传导致冷板。同时,为了确保热界面材料的厚度与接触热阻足够小,则需要对它额外再施加一个稳定的压力。
在电源类产品中,常见的施加稳定压力的手段有弹片预压与螺钉锁付两种。
弹片预压:即在器件的正上方放置一个弹片,弹片的一端接触器件,而另一端则固定在机壳上。在设计时,弹片与器件采用过盈接触。在实际安装时,则会促成弹片在安装过程中产生压缩变形,从而对器件造成一个法向压力。这个法向压力,最终会由PCB传递给热界面材料。
螺钉锁付:即在PCB与冷板上设计有螺钉锁付孔。在螺钉拧紧的过程中,螺钉法兰面推动PCB挤压热界面材料并对其施加一个稳定的压力。
比较两种方法,弹片预压对设计空间要求较高,并且需要在机壳上有对应的安装点,不过当以上两点都满足要求的情形下,弹片预压能够提供比较明确的压力与热界面材料厚度的关系。螺钉锁付对设计空间几乎没有要求,不过由于螺钉锁付时PCB的最大压力不在器件下方,而是在螺钉锁付区域附近,因此器件下方的热界面材料厚度难以简单的通过螺钉预紧力进行估计。
基于以上的特点,弹片预压与螺钉锁紧往往会在不同的情形下进行选用。本文会以EVB快插板为例,介绍螺钉布置对底部散热型表贴式功率器件热表现的影响以及如何布置螺钉孔位。
03什么是EVB快插板?
EVB,即评估板(Evaluation Board)的英文简称。EVB通常是用于向客户展示器件的性能、供客户熟悉器件的功能和作用、且由芯片公司自己开发的非生成类型板。
带独立水道的EVB(主板与功率板)
EVB快插板,即通过快插端子与主板实现功率互联的全桥(或者半桥)功率板。与之相对,在实际电源类产品中,功率板与主板的功率互联主要是通过焊接来实现。
对于EVB而言,易拆卸、更换灵活是它的特点也是它的应用需求。但另一方面,由于没有机壳,如果要实现弹片预压则需要额外定制工装来实现与冷板的连接,显然这样做是本末倒置的。而与预压弹片相比,采用螺钉锁付方式同样能实现稳定的压力,同时在工艺制造上仅需在快插板上增加相应螺钉孔便可,因此它是一种非常契合EVB特点的实现稳定压力的手段。
04螺钉锁付对EVB快插板的影响是什么?
螺钉在锁紧过程中,快插板与螺钉头部接触区域会产生压应变。随着锁紧压力的增大,快插板接触区域的压应变在增大的同时,平面内应变也随之增大。当快插板上下表面的平面内应变差大到一定程度时,则快插板会发生肉眼可见的弯曲。弯曲后的快插板与冷板间的接触面将不再是完全贴合,会产生以最大挠度点为最大值、螺钉锁紧区域为最小值的不均匀的间隙。显然,这种间隙将促使填充在快插板与冷板之间的热界面材料具有不均匀的厚度。而这种不均性,对于高功耗器件热表现的预测与评估是非常不利的。
螺钉锁付时快插板发生弯曲
05有没有办法消除或者减小这种间隙的不均匀性?
要做到完全消除螺钉锁付过程中快插板的弯曲,就必须将螺钉法向锁紧力减小到不足以发生弯曲,或者将快插板弯曲刚度增加到足以克服现有螺钉的法向锁紧力。然而,前者可能造成螺钉锁紧扭矩不足以致热界面材料过厚,而后者则不得不将快插板变得非常厚。显然,这两种手段都是不合适的。
相比起完全消除,减小间隙的不均匀性的手段则要更多。除了螺钉锁紧力、快插板弯曲刚度之外,螺钉的排布方式、螺钉的数量都会对间隙的分布有着显著的影响。同时,考虑到并非整块快插板都会被热界面材料覆盖,因此在设计时,只需要确保有热界面材料的区域具有小且均匀的间隙即可满足应用的要求。
06什么样的螺钉布置方案比较好?
快插板一般面积较小,常见的螺钉锁付方案有4螺钉锁付与3螺钉锁付两种。那么到底哪种螺钉锁付方案更好,螺钉孔又应该以什么样的标准进行布置?本文将借助有限元仿真的手段对这一问题进行对比分析。
简化的快插板螺钉方案示意图
首先将快插板简化为一块88mm * 51.5mm *1.6mm 的长方体,并分别建立4螺钉与3螺钉的仿真模型,每个螺钉的法向锁紧力为3000N。对于4螺钉方案,认为螺钉分别关于长方体的长轴与短轴对称布置,因此螺钉位置信息仅有S1(螺钉孔圆心与长轴间的距离)与S2(螺钉孔圆心与短轴间的距离)。对于3螺钉方案,认为是仅关于短轴对称的三角形布置,因此螺钉位置信息有T1(非短轴上螺钉孔圆心与长轴间的距离)、T2(短轴上螺钉孔圆心与长轴间的距离)以及T3(非短轴上螺钉孔圆心与短轴间的距离)。仿真对比的具体螺钉孔位置信息见表1。其中T1被固定为12.25mm,以缩减仿真数量。
观察4螺钉方案的仿真结果可以发现:
a. 当S2越大时,短轴上的挠度越平均,不过幅值也会变得越大。这表示如果器件沿短轴布置,多个器件下的热界面材料厚度将比较均匀,但是总体厚度偏大;
b. 当S1越大时,短轴上的挠度均匀性将更好,不过这种效应在S2较大时几乎彻底消失。这表示如果器件沿短轴布置时,S1的影响较小;
c. 对于特定的S1,存在一个S2的拐点,当远离拐点时,长轴上的挠度均匀性非常差。并且即使通过减小S2的大小(使螺钉沿长轴布置的更紧凑)来创造出局部的挠度均匀区域,螺钉锁付区域外则会因为翘起过度且无约束而大大增加系统共振风险。这表示器件如果沿长轴布置,需要通过仿真或者DOE实验找到一个较佳的位置,否则将很难保证器件下的热界面材料的厚度均匀性;
d. 本文里的4螺钉较佳方案为S1=17.25mm,S2=29mm。它长轴上的平均挠度为0.0171mm,最大最小挠度差为8.68e-3mm,最大挠度区域为快插板靠近中心处。
4螺钉方案挠度云图
4螺钉方案短轴与长轴挠度结果汇总
4螺钉较优方案,S1=17.25mm,S2=29mm
观察3螺钉方案的仿真结果可以发现:
a. 由于短轴上有螺钉,因此3螺钉方案中只考虑器件沿长轴布置的;
b. 当T3越大时,长轴上的挠度越均匀,并且长轴远端的挠度值越小;
c. 当T2越小时,靠近快插板中心区域的挠度越小,此时远端的挠度几乎无任何改变;
d. 本文里的3螺钉较佳方案为T1=12.25mm,T2=12.25mm,T3=39mm。它长轴上的平均挠度为0.0175mm,最大最小挠度差为5.97e-3mm,最大挠度区域为远离中心处。
3螺钉方案挠度云图
3螺钉方案长轴挠度结果汇总
Conclusion
结论
根据上文的对比,可以发现无论是4螺钉方案还是3螺钉方案,都可以通过DOE手段找到比较理想的排布方式。但是两者相比,依然有以下差异:
a.4螺钉方案挠度最大区域在靠近中心位置,而3螺钉方案则在远离中心位置挠度最大。考虑到高功耗器件需要有足够面积的板内覆铜进行散热,一般不太会放置在快插板边缘区域,因此这一点上3螺钉方案比4螺钉方案更优;
b.4螺钉方案偏离螺钉最佳位置后,整体挠度变化剧烈,而3螺钉方案即使偏离最佳位置,整体挠度变化仍较为缓慢。从这一点上考虑,3螺钉方案同样比4螺钉方案更优;
综上,在布局空间允许的条件下,建议类似文中EVB快插板的表贴式功率器件全桥板优先选用3螺钉方案。
但,如果布局空间受限,4螺钉方案也完全可以接受,但设计时需进行充分的DOE分析以找到较优的螺钉孔位置。
07其他场景下螺钉布置应该如何选择?
EVB快插板由于尺寸较小,因此大多以3螺钉或者4螺钉方案为主。当需要锁付的PCB尺寸较大、PCB形状不规整或者功率器件数量较多时,可能会需要使用6螺钉、8螺钉乃至更多数量的螺钉对PCB进行锁付。此时本文关于EVB快插板的分析结论虽不能简单地直接引用,但是分析流程是相同的。大致的分析流程可以总结为:
1. 确定要对比的螺钉方案(不同螺钉数量);
2. 确定大致的器件布置区域以及器件排列方式(如1*4或者2*2);
3. 以器件布置区域的中心为原点,对PCB进行十字分割;
4. 建立每种方案的DOE螺钉位置矩阵;
5. 按照位置矩阵进行有限元分析;
6. 以PCB十字分割中心点为原点,提取分割边界的挠度数值,并绘制曲线;
7. 寻找在器件布置区域挠度均值与挠度方差均较小的方案;
8. 确认当螺钉位置偏离最佳位置后的挠度均值与挠度方差的变化情况;
9. 根据7与8的结果,并结合PCB的设计空间对螺钉的布置方案进行选择。
审核编辑:汤梓红
-
半导体
+关注
关注
334文章
27290浏览量
218091 -
元器件
+关注
关注
112文章
4709浏览量
92209 -
PCB板
+关注
关注
27文章
1447浏览量
51610 -
仿真
+关注
关注
50文章
4070浏览量
133552 -
功率器件
+关注
关注
41文章
1758浏览量
90416
发布评论请先 登录
相关推荐
20W-50W厚膜无感电阻TO-220封装技术规格&散热说明
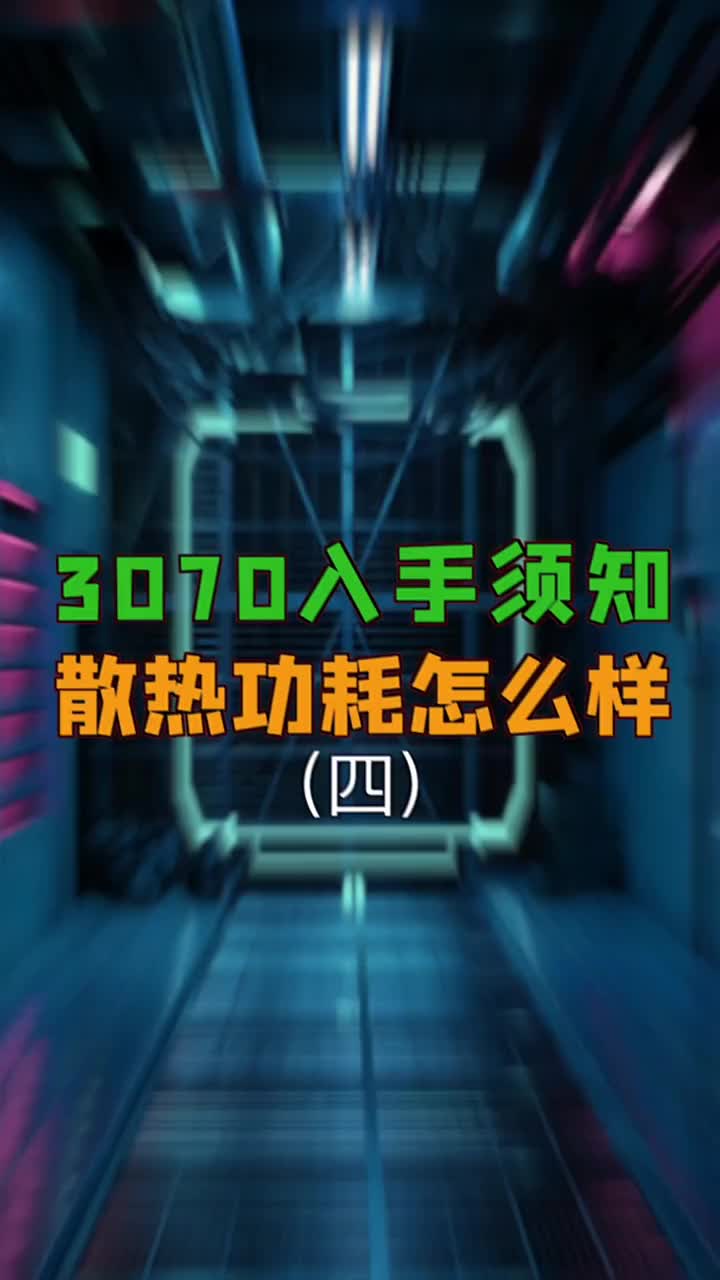
评论