随着芯片成本的上升,“前馈”和反馈变得至关重要,但这一切都需要时间。
半导体工程与微软安全云环境产品管理总经理 Mujtaba Hamid 坐下来讨论智能制造以及工具和人工智能如何为半导体实现智能制造;Vijaykishan Narayanan, proteanTecs印度工程与运营副总裁兼总经理;KT Moore, Cadence企业营销副总裁;以及Alphawave Semi高级副总裁兼总经理Mohit Gupta 。
我们多年来一直在谈论工业 4.0,也称为智能制造。我们今天走到了哪一步?芯片行业的发展又如何呢?
很长一段时间以来,它一直是一个流行词,但现在我们看到了真正的解决方案所带来的成果。这将使公司能够采用改进的 PERCS——生产力、效率、可靠性、成本和可扩展性。
在过去的几年里,尤其是在新冠疫情之后,世界开始意识到半导体的重要性。汽车或冰箱上丢失的微小芯片都无法让你无法正常使用。随着数据增长的出现,我们如何确保有良好的系统可以始终帮我们达成目标?
整个工业 4.0 运动很大程度上是通过向我们的流程注入智能来推动的。过去几十年来,我们一直专注于自动化和可扩展性能。通过在流程中纳入人工智能或机器学习来扩展这一点,无论是设计还是制造——它就在这里。我们不断学习和发展,并与客户合作,做得更好。
长期以来,我们一直希望在供应链中进行更高保真度的设计和更高质量的制造。各种有利因素汇聚在一起。借助云和大数据建模工具,你可以在将设计发送到制造之前对其进行更高保真度的模拟。拥有诸如边缘云之类的东西,它可以实现预测性维护和自动化,以及更好的数据共享以提高供应链的弹性。数字孪生也正在使用中。因此,许多支持技术即将出现。尽管工业 Metaverse 正在经历类似 Gartner 低谷的情况,但它终将挺过来并实现更丰富的可视化。现在人工智能浪潮正在到来。
每当我们谈论智能制造时,人们常常会提到半导体作为最前沿的行业。但这样的说法准确吗?
人们在孤岛中工作。有一个测试团队、一个生产团队和一个现场设计团队。但没有用于数据前馈或反馈的通用平台可以在其中提高效率或生产力。从错误中吸取教训,并将这些教训反馈到你的设计中,从而提高设计的质量。这是自动化的重要组成部分,也是根据从芯片中获得的一些知识做出决策的重要组成部分。打破孤岛是第一步。
你能定义一下通用平台的含义吗?
我们将这些代理添加到芯片内,以获得对该芯片的可见性。一旦硅片出来,我们就能从中得到读数。我们有一个平台,可以在系统级阶段、生产阶段和现场加载数据。因此,现在任何访问该平台的人都可以了解这些领域。如果存在问题,他们会提出警告,并且可以向后或向前反馈数据以解决这些问题或采取其他措施。
从软件行业的角度来看,是持续的开发和运营循环。该循环依赖于通用数据。我们称之为数据底层软件。这可能是一个负载性的术语,但我们需要这种类型的数据基底能够进行前瞻性和回顾性,并具有连续的设计和制造循环。
还有另一个向量。随着这些系统变得越来越复杂,重新设计和犯错误的成本变得非常高。前馈和后馈都类似于整个流程的持续改进。RTL 工程师需要知道芯片中发生了什么。当你在公司里开发一些东西时,你需要在那里直到看到芯片。否则,循环不闭合。如果采用任何具有复杂异构芯片或小芯片的领先工艺节点,构建这些系统的成本要高得多。
这些孤岛产生了两个向量。我们的客户一直在使用顺序流程设计这些复杂的芯片、系统或电路板。但随着这些事情变得越来越复杂、越来越集成,我们必须能够在设计过程中消除这些人为的边界条件。其次,我们的一些客户不再只是设计芯片。我们有设计芯片来构建系统的客户。我们现在有系统公司正在制造芯片。因此,整个集成层正在呈指数级扩展。
这种连续循环不再仅仅存在于制造中或回到设计中。现在它也必须前进到战场并返回。但如何达到所有这些要求呢?有多种产品很快问世,其中一些产品的使用寿命更长。这些数据实际上是如何反馈的?
设计流程也必须不断发展。在过去的几十年里,设计流程没有发生根本性的变化。新的工具和复杂性已经出现。但是,如果真正考虑能够前馈/后馈,如果人工智能到来,如果你改变核心芯片设计与片外加速器设计之间的界限,以及获得什么在系统、主板或软件中完成——边界不断变化。如何在传统设计流程中保持敏捷?这就是这个数据平台如此重要的地方。数据平台既需要在设计中实现反馈和前馈,也需要在制造和现场中实现反馈和前馈。如果数据平台更加一致,并且能够实时获取遥测数据,那么设计人员可以更快地做出反应。整个事情需要成型。
同意。我们还没有达到那个目标,但我们已经走在正确的轨道上了。我们已经采取了一些措施,但仍有更多工作要做。
这些数据平台是什么样的?
从产品创作的角度来看,数据平台需要扩展到设计的各个环节。当我大学毕业时,作为一名芯片设计师,我的主要职责是确保芯片满足性能指标,仅此而已。我们不太关心功率或面积。但是,当你将这些其他维度添加到设计中时,你需要一个可以从 RTL 创建一直延伸到签收的平台,并且能够访问所有这些不同的数据点。现在我们谈论的不仅仅是设计芯片,而是在具体环境中进行设计。这不仅仅是电气行为。它还包括物理行为、物理相互作用——热力等等。
我将给你举一个例子,说明如何从宏观层面看待某些事情。我们公司从事连接领域,世界各地都有这些大型数据中心。如果看看他们的资本支出,就会发现主要是用于冷却的电力。硬件是一个较小的组件。因此,设计芯片或解决方案的人可以拍摄数据中心消耗的电力的图片,深入到机架,从机架到服务器再到芯片,等等。也许我们还没有完全做到这一点,但是有更多的反馈发生,就像它在系统级别的含义一样。除了电池供电的设备之外,其中一些参数(例如功率)过去从未成为关键问题。但现在,如果不能满足功率预算,许多系统将无法启动。
当我们走向芯片上数万亿个晶体管、小芯片和 3D 堆叠时,设计人员必须考虑所有这些排列和组合。然后,在流程中发生变化是可能的。因此,你不能抱着这样的心态:“这是芯片边界,我正在努力实现可预测的结果。”
解决芯片问题的方法有很多,但并非所有方法都必须在芯片级别完成。你可以将某些问题作为芯片的一部分来解决,但你也可以通过软件来修复它。如今,通过硬件/软件协同设计方法可以提供足够的调查功能,你可以从系统角度优化事物。
审核编辑:刘清
-
加速器
+关注
关注
2文章
800浏览量
37905 -
晶体管
+关注
关注
77文章
9698浏览量
138319 -
芯片制造
+关注
关注
10文章
624浏览量
28832 -
人工智能
+关注
关注
1791文章
47350浏览量
238738 -
RTL
+关注
关注
1文章
385浏览量
59829
原文标题:在芯片制造中更有效地使用数据
文章出处:【微信号:ICViews,微信公众号:半导体产业纵横】欢迎添加关注!文章转载请注明出处。
发布评论请先 登录
相关推荐
【「大话芯片制造」阅读体验】+ 芯片制造过程和生产工艺
《大话芯片制造》阅读体会分享_1
【「大话芯片制造」阅读体验】+内容概述,适读人群
大话芯片制造之读后感超纯水制造
铝在芯片制造中的作用
GDS文件在芯片制造流程中的应用
保证信号有效传输的储能隔离芯片
SOLIDWORKS 2025:更有效的协作和数据管理
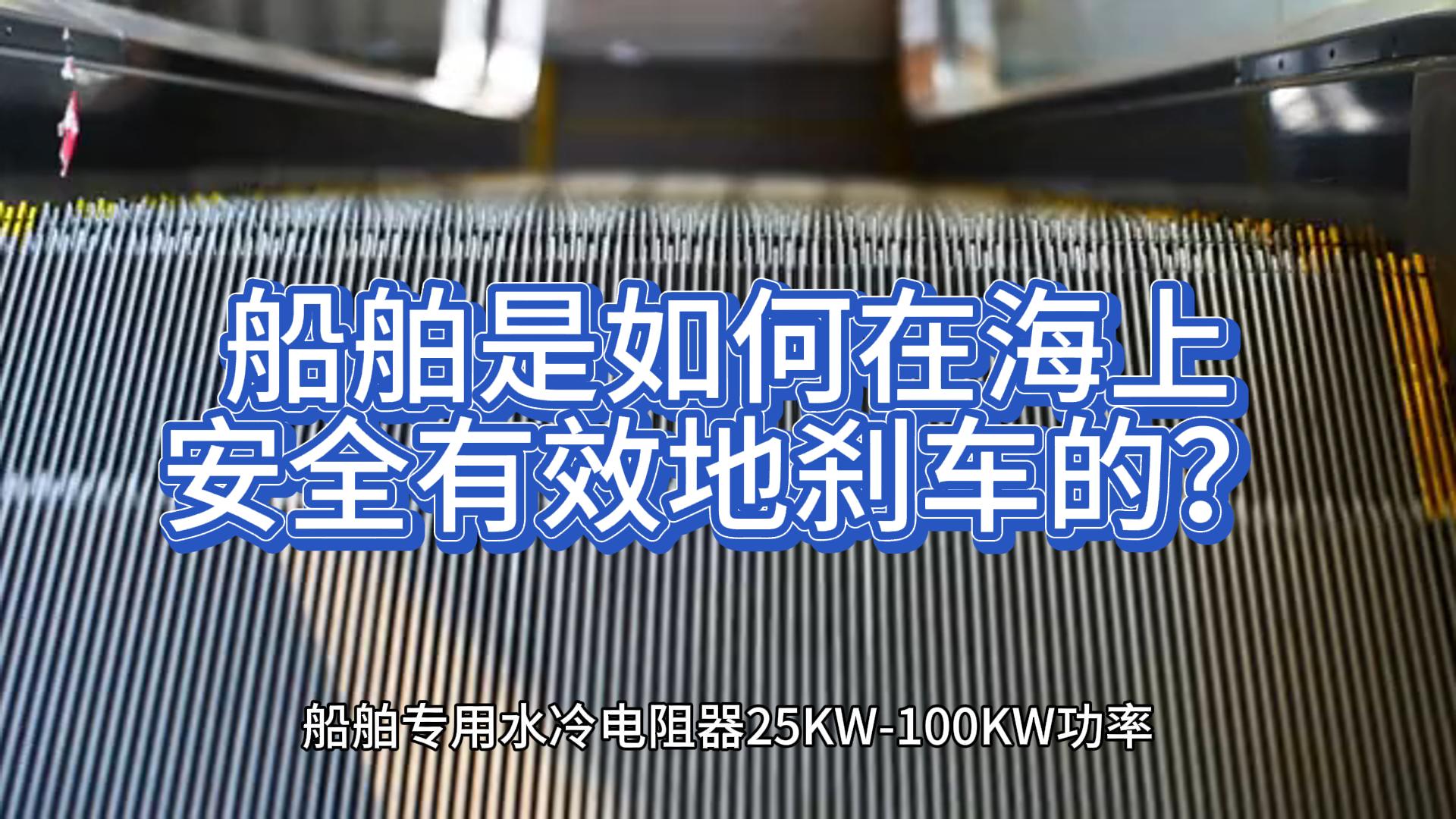
如何在Draftsman中创建PCB制造图纸
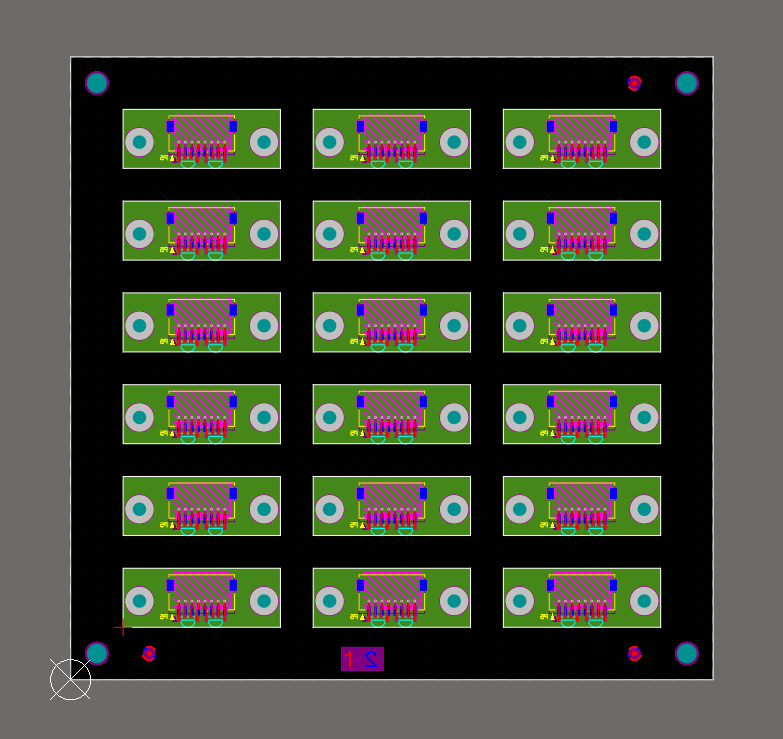
封装、光子引擎等,尖端芯片制造也需要非接触精密除尘
铌酸锂芯片与精密划片机:科技突破引领半导体制造新潮流
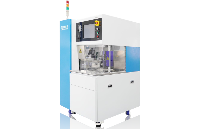
评论