据了解电力部门采用国外传感器产品三年不需检修,采用国内产品每季度检修一次;石化部门,重要生产线几乎全部采用国外传感器,而不敢使用国内产品。 为什么不敢用国产传感器? 下文节选自由我国沈阳仪表院等多家国内传感器权威机构和众多专家编写、审校的《中国传感器发展蓝皮书》,提出了我国传感器产业中存在的9大问题,一针见血地回答了我国传感器产业为什么不行?!推荐! 1、国产传感器品种、规格、系列不全,性能指标差距甚远,稳定性、可靠性差国外竞品1~2个数量级!国内传感器产品往往形不成系列,系列中比较易生产的某些规格尚能生产,且重复生产,恶性竞争,系列两端的产品往往不能生产,多需国外进门,给用户造成很大不便,使传感器应用的显示度大打折扣。 如工业自动化仪表中广为应用的、髙精度、高稳定的低微差压传感器(量程≤1KPa),高差压、高静压传感器(量程≥3MPa、静压≥60MPa),国内尚不能稳定、批量供货,基本靠国外进口。国内高水平的车用传感器,每年需进口50万套以上,不需加装锂电池的胎压传感器尚属空白之列,某些特种用途和特殊量程的传感器,如航天传感器可基本满足,自给自足,部分极端环境下使用的特种传感器,性能指标达到国际先进水平。但航空、航海专用传感器,国内基本不能满足。民营或合资企业的产品占据了中低端市场。
除个别厂家在个别品种方而将国外生产的芯片拿到国内封装组装成相关产品、占据市场较大份额外,其他高端产品均是国外厂商在垄断。 但由于产业档次偏低、技术创新能力较差,国内传感器产业呈现低端过剩、中高端被国外垄断的市场格局。 传感器技术发展滞后,性能指标不高,已掣肘国内战略性新兴产业的顺利推进。国产传感器在测量精度、温度特性、响应时间、稳定性、可靠性等指标与国外也有相当差距。如以压力传感器为例,国产传感器精度通常为0.1%FS,较好能到0.075%FS,国外通常为0.075%FS,甚至0.04%FS。如量程比,国内通常为100:1,国外通常为400:1。
国产硅基传感器的温度误差通常在(0.25%〜0.65%)/55°C之间,与国外产品相比,温度漂移比国外产品的典型值大50%〜100%。传感器的响应时间比国外同类产品要人1倍,甚至数十倍。问题最严重的是国产传感器的稳定性和可靠性,往往比国外传感器同类产品低1〜2个数量级,以至国内用户不敢用、不愿用、不能用。 由于国内不能生产出高性能的传感器产品,严重影响国内新兴产业的顺利推进,如物联网产业、智能制造产业、人工智能产业、数字经济产业等。 2、传感器的产业化问题没有得到长期的足够重视,量产才是最大差距!传感器作为一种基础元器件必须实现产业化,才能体现其经济效益,降底成本,稳定工艺。做十支百支甚至万支传感器不说明任何问题,也不会带来明显的直接的经济效益。国家从“七五”开始就提出传感器的批量生产和产业化问题,但力度不够,未持之以恒,至今尚未形传感器产业的龙头企业和标杆单位。 民用工业传感器的应用与军用传感器的应用有很大不同,军传感器虽然技术指标要求很高,应用环境严苛,技术参数众多,但往往不计成本,一次性应用,可动用全国之力,总能在众多器件中挑选出符合要求的产品。
民用工业传感器则不同,我们和国外传感器的差距往往不是技术指标的差距,而是成本的差距、性/价比的差距、批量生产的差距,而要解决这些问题,传感器产业化是不可逾越的门槛。 传感器产业化是一个系统工程,它涉及国家政策、体制、机制等政府行为;传感器产业化投资机制;市场、用户、产业链和经营模式;传感器本身产业化的条件、规律,即传感器的“产业化技术”、“产业化市场”、“产业化条件”、“产业化人才”等问题没有得到有效解决。而传感器的根本出路也在于传感器能否走出“象牙之塔”进行产业化规模生产。 目前传感器市场鱼目混杂,良莠不齐,存在“虚胖”乏力之势。3、国产传感器大多模仿/抄袭,基础研究不力,核心技术少,创新能力弱!基础研究乏力,新原理、新器件开发凤毛麟角,新材料研发屈指可数,特性研究不深不透。国内对传感器的基础理论研究重视不够,很难得到国家立项,即使得到立项经费也甚少,很难吸引人才;企业忙于效益,无暇顾及;政府看重政绩,很难顾及。 因此对传感器的基础研究缺乏厚实环境,如数学模型建立、芯片设计软件开发,仿真及工艺模拟,工艺装备研发、各种结构材料特性研究、产业化中规模生产技术研究……由于各种原因,投入资金甚少,大大落后国外同行的研究工作。 出于基础研究乏力,近几十年来,国内少有传感器新原理问世,一般是将国外样品(样机),分析测绘,充其量有点集成创新,“克隆”而己。
国内在传感器新材料研究方面也很薄弱,有一些化合物传感材料的研究,但都在实验室里小打小闹,功能传感材料的研究举步维艰,真正应用生产实际,产生规模经济效益的很少。应特别重视非硅基传感器材料的研究,尤其是石墨烯材料的研究。 对传感器的特性研究往往只注意静特性研究,对动特性研究不甚了了,对航天类传感器,动特性尤为关键,忽视传感器动特性的检测及评估,低估测量参数的动态分量,甚至造成传感器无法使用。 4、共性关键技术尚未真正突破:设计软件问题多、量产能力差、标准弱、生产工艺装备落后设计技术:传感器的设计技术涉及多种学科、多种理论、多种材料、多种工艺及现场使用条件;设计软件价格昂贵、设计过程复杂、考虑因子众多;设计人才匮乏,设计人员不仅需了解通用设计程序和方法,还需熟悉器件制备工艺,了解器件现场使用条件。国内虽有一套MEMS传感器设计软件,伹问题较多,离实际普遍应用尚有很长路要走。可以说国内尚无一套有自主知识产权的,真正好用的传感器设计软件。可靠性技术:国产传感器可靠性不高是影响国产传感器大量应用的主要原因之一,据了解电力部门采用国外传感器产品三年不需检修,采用国内产品每季度检修一次,石化部门,重要生产线几乎全部采用国外传感器,而不敢使用国内产品。通常国产传感器可靠性指标比国外同类产品低1〜2个数量级。
国产传感器可靠性指标的提高,不仅有技术问题、材料问题、工艺问题更有管理问题、使用问题。这些问题必须在批量生产过程中才能发现、解决。封装技术:传感器的封装结构和封装材料,影响传感器的迟滞、时间常数、灵敏限,使用寿命等性能。从制造成本看,传感器的封装成本通常为总成本的30%〜70%。国内对传感器的封装技术尚未形成系列、标准,也无统一接口,因而传感器的外型千差万别,很不利于用户选用和产品互换。 传感器的封装有芯片级、芯体级、器件级、系统级等。国内对传感器的封装重视不够,更无这方面的专门研究。 传感器工艺装备:传感器的工艺装备问题,长期以来,一直得不到应有的重视与关注。传感器工艺创新依赖于新工艺装备的问世。 在传感器工艺装备的研发与生产方面,国家无规划,很难立项,也少投入,靠企业自筹资金,零敲碎打进行研发,既不利于传感器工艺研究之创新,且这块市场被国外所垄断和占领,严重制约了我国传感器行业的独立前行。
国内设备制造企业对工艺了解有限,设备应用部门工艺人才培养问题突出,设备维修换代代价高昂,工艺设备状态在线监测及调控手段不足,除非“整线引进”,设备间工艺协调性难以较好解决,柔性化生产组织难度较大。 国有企业发展处于平稳增长状态,总体上跟不上国外最新技术发展的步伐,除少数厂家外,总体差距有扩大的趋势。这是因为传感器技术发展快,工艺和制造设备更新快。绝大多数厂家靠自身积累很难购买新型设备,致使在许多新技术、新工艺方面无法跟上国外传感器飞速发展的步伐。 5、顶层设计和统筹规划执行力度有待提高,近来国家顶层设计对国产传感器认识有很大改观!但整体投资还是很小! 国内传感器分属不同的部门和行业,加之专业面广,国家长期以来难有统一的认识,对传感器发展在思想上没有取得共识,更没有一个部门对传感器的顶层设计进行系统研究和科学规划。但近年来,中国传感器的顶层设计有了很大改观,随着“十三五、十四五”规划的制定和“中国制造2025”的实施,“工业强基”项目的出台,借助物联网、智能制造、人工智能等的兴起,国家出台了一系列的有关振兴传感器产业技术的政策、规划和指导意见。希望由此迎来国内传感器发展的新机遇,迎来传感器产品、产业结构调整的关键期。
▲近十年来国家对传感器产业技术的支持和扶植主要政策
但是,虽然出台了一系列的有利于传感器发展、振兴的政策,但执行力有待提高,特别是应提髙投资强度,加强基础研究,开展先进传感器研究的技术积累,注重传感器产品的产业化研究与建设,改善传感器的产业面貌,提高执行力度。 如“智能传感器三年行动指南”,实施期为2017-2019年,这对传感器的技术进步和缩短国内外差距意义重大,而且该政策撰写也非常到位、精准,专家们也是下了不少功夫,在调研的基础上出台了该政策。 三年过去了,智能传感器变化不大,据说投资很小,“巧妇难煮无米之炊”。当然在上海成了一个“智能传感器创新中心”,据说有启动资金2亿人民币,采用“平台+联盟”形式,筹措资金248亿,但像智能传感器这样的大项目,投资主体应该是国家,国家在这方而是应该投钱的。
又如在“工业强难”项目中“传感器一条龙”计划,列出了示范项目、示范企业等,经了解国家也无资金投入。 再则,在传感器立项时,往往要求地方政府和企业需相应的配套资金,且比例在三分之二左右,地方政府有无相应的配套资金投入,不敢妄加评论,但耍企业配套资金占30%〜40%,对传感器企业是很困难的,传感器一般是中、小、微企业,各种税赋己很重,生存尚且不易,审本无配套资金进行研发,因此应减少企业的配套资金比例。6、资源分散,产业规模小,缺乏带头作用的行业龙头企业产业分散:包括资金分散、技术分散、企业布局分散,产业结构分散、市场分散。 管理分散:包括政府部门管理归口不统一、难于协调、存在多头管理现象。 政策支持分散:政策支持的集中度不高,缺乏专项计划集中扶持,即使支持也过于分散,缺乏力度,缺乏持续性。 产业规模小:传感器企业有2万余家,大都为小、微企业,盈利能力不强,缺乏引领技术的龙头企业。
7、高端人才匮乏,跨国公司高薪挖人屡见不鲜 世间一切事物中,人是第一可宝贵的。人才是创新的根本,影响传感器发展的最大瓶颈是优秀研发人才匮乏。 由于传感器行业经济基础、技术基础、产业基础较为薄弱,加之传感器产业涉及学科多,要求知识面广,新技术层出不穷,长期以来很难吸引国际顶级人才投身到传感器行业工作。 国内由于学科设置不合理,缺少复合型人才培养机制,往往搞设计的不懂工艺、搞工艺的不明应用、会应用的不晓设计,即使我们自己培养的有用之才,由于待遇、职称等问题,加之跨国公司的髙薪挖人,跳槽到外资公司或企业的人才流失现象屡见不鲜。 因此,我们缺乏既懂管埋,又懂技术,还会经营的复合型人才。缺乏工艺人才和技能人才、更缺传感器大国工匠。 8、对传感器的认知在宣传上存在夸大误区,容易造成“虚假繁荣”的误判!国内对传感器产业进行分析时,都是以“泛传感器”这一概念进行,导致大量非工业领域传感器产业数据被采集,传感器数据的真实度严重“失真”、有“虚胖”之感,有误导领导正确决策和企业正确投资之嫌。 另外,国内传感器的市场规模和传感器产品的市场销售额完全是两个不同概念,有市场规模(容量)国内企业并不能一定占据该市场。
对传感器的宣传没有把国内传感器的真实情况和存在问题向大众公布,会引起某些地方政府对传感器的投资过热,往往得不到相应的效益和业绩,传感器产业在短期内是不挣钱的,抱着以赚钱为目标发展传感器往往欲速而不达,有些教训其实很深刻,如20条MEMS生产线开工率严重不足就是例证。 9、中国传感器的国内、外位置,差距在15~20年,产业化差距最大!传感器在国内产业布局中仅位于次重要位置! 中国传感器在国际格局位置:差距15〜20年,属第三梯队。如下图所示。
从设计技术、制造技术、产业化技术、应用技术四个方面与国外进行了比较,差距明显。第一梯队当属美国、日本为首,第二梯队由德国引领之欧洲国家,我们仅属发展中国家之较好。 这些差距,如果不采取有效强力的措施,差距会进一步拉大,这不是危言耸听,而是中国传感器现实的真实写照。 中国传感器在国内位置一一次重要位置。如下图所示。
近70年,中国传感器走过了极不平坦之路,但同时有着不少的技术积累,未来随着物联网、智能制造等强劲兴起,国家有关政策的出台和支持,我们将迎来了传感器产业技术发展春天的脚步。审核编辑 黄宇
-
传感器
+关注
关注
2557文章
51729浏览量
758793
发布评论请先 登录
相关推荐
温湿度传感器:生活中的“小气候专家”
中国传感器产业前景怎样?DeepSeek这样回答
如何校准位移传感器
为什么中国传感器长期依赖进口?7000多家国产传感器企业仅6%产值过亿!专家谈产业的当务之急
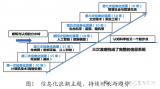
使用LM75BIMX作为温度传感器检测环境温度,得到的数据持续为不符合现实的错误数据,怎么解决?
中国传感器落后10年以上,高端产品96%靠进口,卡脖子现象突出!专家锐评产业现状(最新观点)
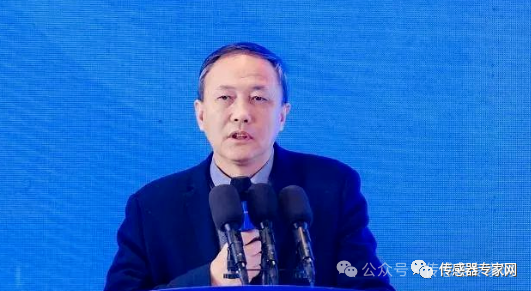
线性传感器和非线性传感器的区别
光纤传感器是光电传感器吗
风速传感器原理及应用
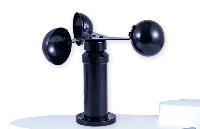
中国压力传感器市场境况如何?
传感器最大赛道,中国压力传感器市场现状及企业未来出路
中国传感器专家当选欧洲自然科学院院士!他推动了国产传感器发展!(深度观察)
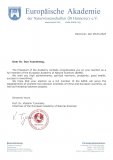
评论